Afriana Tanri Sudarno
Bachelor of Engineering (Chemical), Monash University
Summary
The aim of this project is to investigate the effect of both paper and printing press parameters toward linting of newsprint in the offset lithographic process.
IGT pick test found not to be a suitable method of predicting lint. This is because IGT pick test imposes a lot higher pressure and ink tack to a piece of sample in order for it to be able to collect enough lint to be measured either by weight or by image analysis. However, the lint collected by IGT is not relevant to those from the commercial press trials.
Three different papers were investigated in this thesis, The paper labeled Golbey was Nornews produced by Norkse Skog France. The other two papers were Norstar and Nornews produced by Norkse Skog Boyer. Golbey produced the most lint, followed in order by Norstar and Nornews. Fines, fillers and recycled fibres are the paper components that can lint. Fines are desirable if they bond well with the fibres. However this may not be the case if fines are poorly bonded. From the configuration of the Boyer paper machine, with the horizontal twinwire former and a twinver press, it is believed that the top side of the paper ends up with more fines compared with the bottom side of the paper. However the work here showed that the Norstar top side of the paper produced more lint than the bottom side. This suggested that the fines are not bonded too well in Norstar.
The printing press variables were discussed into four main major parts, paper variables, ink and fountain solution balance, printing press blanket/plate variables, and printing press operating conditions. Various printing parameters were tested to investigate their effect towards offset lithographic printing. Heidelberg GTO-52 and Man-Roland Uniset were used to do most of the printing trials. ANOVA Systat was done and showed that printing take-off angle, tack, print coverage (printing tone), two sidedness of the paper and speed were among the significant print parameters affecting linting in offset lithographic printing in Man-Roland Uniset trials. Screen ruling and printing pressure were not significant according to the ANOVA results.
Lint accumulation on blanket follows a linear relationship with the number of copies for both Heidelberg GTO-52 and Man-Roland Uniset trials before it reaches its plateau, i.e. when the rate of lint accumulation in the blanket is zero because the rate of lint transferred to and from the blanket equal to each other.
The small effect of ink tack was explained as arising from the nature of the measurement of ink tack. Ink is shear thinning, and the Inkometer used to determine ink tack measures tack at much lower shear rates compared to the shear rate in the printing nip of a commercial printing press. Ink tack increases with the increase of ink film weight or ink film thickness as shown by inkometer and Deltack. It was also shown that the higher the speed, the higher the ink tack is for both the inkometer and the Deltack.
Ink tack change with the addition of fountain solution and with the change of speed, ink film thickness and printing nip pressure needs to be correlated better with the commercial offset lithographic press. Thermal Gravimetric Analysis is considered to be the most suitable equipment to measure fountain solution content in process ink.
Analysis of variance showed that pressure was not a significant variable towards linting in the Man-Roland Uniset trial. Swapping the existing blanket with a new blanket, which increased the pressure from 5.5 MPa to 9.5MPa, only increased the average lint of several take off angles, printing tones, and two sides of the paper by 4%. The Heidelberg GTO- 52 trials also showed that pressure did not strongly affect lint results. This is also consistent with the Deltack effect of pressure to linting results.
25% printing screen always yields the highest lint regardless of the test. The 75% scren and solid (100%) gave the lowest lint for results from both the Man-Roland and Heidelberg GTO-52.
Lint increased greatly with take-off angle. The side with higher take-off angle has higher rate of ink film splitting, since the side with the higher take-off separates faster from the blanket at the exit of the nip. The higher rate of ink-film splitting increases the stress that is applied to the surface of the paper, which increases the amount of lint and the size of the lint particles.
Among those variables investigated, take-off angle, paper side and the combination of take-off angle and paper side are the most significant parameters affecting linting.
Lint migration from paper to blanket to plate is dynamic and need to be investigated in the future. Lint in the ink and fountain solution rollers is harder to measure. Some sort of dynamic lint measurement needs to be developed. Dynamic image analysis consists of high speed and high resolution camera with image analysis. Ideally the image analysis should also be done in real time Some early work has already been done by Knut Wiik.
More paper variables, printing plate and printing blanket type, different ink and fountain solution chemistry composition, paper batch variability and ink colours need to be investigated. The main components affecting ink tack and therefore affecting lint mainly are to be identified. Inks with same tack number, both coldset and sheet-fed inks, which often give different result in linting, needs to be investigated.
The relationship between image quality and the amount of lint should also be investigated, as linting is ultimately an issue to printers because of its effect to image quality.
1.0 Introduction
Linting is defined as the tendency of paper to shed-loosely bonded particles, i.e. fines, ray cells, fibres and fillers, from its surface during offset lithographic printing [1]. These materials can then be transferred from paper to printing blanket, plate, ink and water trains causing deterioration in print quality. If there is too much lint then this can cause runnability problems since the operator has to stop and wash the machine, either washing the printing blanket or even the whole ink and water systems [1].
The total material removed from paper surface as lint is only around 0.002-0.004 % of the total area [2]. However, since offset lithography process demands keep increasing and normally offset lithography printing runs are long especially for newspapers, where over 100,000 copies in total can be printed, it can be seen why linting is one of the serious offset-lithography printing problems today. It is worth noticing that offset lithography is the only newspaper printing process used in Australia.
Linting is a complex phenomena associated with the interaction between ink, water, paper [3] and also press parameters. It has been reported that paper and printing press parameters intera
ct and this affects lint results. Even though factors affecting lint have been studied for the last 30 years, some of the reports still give contradictory results and explanations. The effects of printing press parameters on linting still need to be studied in more depth.
The mechanism of linting is generally described as a combined effect on the ink film splitting forces (sometimes called ink tack) [1] and the inter fibre bonding energy of the paper surface. Linting is also related to the flow of ink in the press nip under pressure. There are two types of ink flows[1], a porous ink flow penetrating the paper surface pores and a free ink flow at the surface of the ink-saturated pores. Theoretical analysis by Mangin and Silvy [1] shows that the ink flows induce sufficient drag on the fibre to cause lint by disturbing the bonding of weakly bound fibres on the surface.
Researchers suggest that different levels of force [4] applied to the surface of paper generate different types of linting. At low forces, unbonded material, often referred to as dust, is removed. At medium forces, weak or loosely bound material, often referred to as lint is removed. At higher forces, well bonded surface fibres are removed, a process that is often referred to as picking.
The lint removed from an offset blanket ranges in size from very fine fibre fragments [5] filler particles, ray cells [6], whole fibres [5] to mini shives and other debris. Lint composition has changed over the years from mostly fibres to fines, ray cells and fillers. This can be explained by improvements in the paper making process such as more energy is used now in pulping producing a better developed fibre. Some studies have suggested that the printing press variables have a greater effect on the linting propensity of paper than the paper itself [1, 7]. Therefore the effects of printing press parameters on lint are worth to be investigated.
The aim of this project is to investigate some parameters affecting lint in offsetlithography printing of newspaper. Most of the relevant parameters have been examined including ink rheology, fountain solution, ink degree of emulsion, paper, printing speed, printing plate, nip pressure, blanket materials, press layout and geometry and the relation affecting lint. Some of these parameters had been studied before by other researchers. However, there were some contradictory results and explanations that need to be clarified and examined further.
This project, investigating the affects of offset lithography printing parameters on linting, was carried out as a Masters of Engineering Science by research with project funding by the Smartprint CRC in collaboration with the industrial partner, Norske-Skog Australasia Research and Development. This project is a part of Norske-Skog global lint research project that is carried out in Norske-Skog Europe, Australia and New-Zealand.
Norske Skog Boyer Mill employs 450 people and manufactures a range of newsprint and publishing related grades. The 290,000 tonnes of paper produced represents 40 % of the Australian market. Raw materials for the mill are plantation radiata pine, regrowth eucalypt and recycled fibre, which is produced at Norske Skog, Albury Mill, NSW. There are two paper machines on Boyer site, PM2 and PM3 with production capacities of 125,000 tpa and 165,000 tpa respectively. PM2 produces both newsprint (Nornews) and improved newsprint (Norstar and others) while PM3 only produces newsprint.
The three different grades of paper were used in this thesis were supplied by Norske- Skog. The main one was called Norstar 52 gsm. This is an improved newsprint with an ISO brightness of 74. The furnish typically consists of 67 % TMP radiata pine, 28 % chemi-mechanical eucalypt (cold caustic soda) and a filler component of 5 % calcined clay (supplied by Imerys as Alphatex). This paper is produced by PM 2 in Boyer. PM2 in Boyer has a horizontal twin wire former and a twinver press. Since TMP [5] and filler [8] have been reported to result in higher tendency of linting, and this paper gave the most problems to Norske Skog, therefore this paper was chosen for most of the testing. The second grade of paper used was Nornews, 45 gsm produced by PM3 Boyer. It consists of 25% cold caustic soda pulp, 20% recycled fibre and 5% kraft pulp and the rest is TMP, with no added filler component in it. The Third grade was 45 gsm Nornews produced by Norkse Skog France, i.e. Golbey. It has 60-75% of recycled fibre and the rest of its component is TMP. Both Nornews and Golbey have lower brightness compared than Norstar. The inks used in the experiments were all coldset offset lithography printing ink with different colours, tacks, brands. These are discussed in more details in the experimental method and results and discussions chapters.
Various printing parameters were tested to investigate their effect towards offset lithographic printing. Heidelberg GTO-52 and Man-Roland Uniset were used to do the printing trials. ANOVA Systat was done and showed that printing take-off angle, tack, print coverage (printing tone), two sidedness of the paper, speed were the most significant print parameters affecting linting in offset lithographic printing in Man- Roland Uniset trials. Screen ruling and printing pressure had no statistically significant effect on linting.
2.0 Literature Review
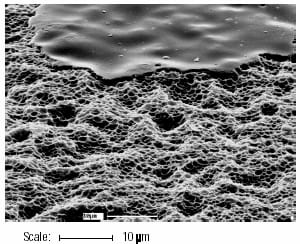
Figure 2. 1. Diazo Plate, the image area is the smooth part and the rest is the non-image area[9]
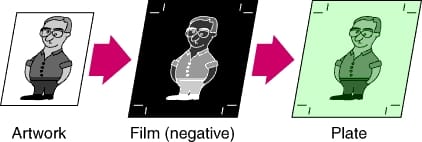
Figure 2. 2. Negative Plate Production. [10]
A lithographic plate is normally bimetal, i.e. it consists of the base plate component and the component building the image area of the plate. The base material in lithographic plates can be aluminium, polymer or paper [11]. The image area materials that lie on top of the base material can be diazo (R2C=N2), photopolymers or silver halide. Both polymer and paper are normally used in small format printing for short runs. For the aluminium plates, a coating is applied on the base to behave as the ink receiving surface with the aluminium, normally in oxidised form, behaving as the water receiving surface[11]. This is shown in Figure 2.1.
While there are several types of offset plates, they are generally are classified as either positive or negative working plates. Negative plates are generally coated with photopolymer and are known as negative working presensitised plates. To expose the plate, a negative film is placed over the light sensitive coating and exposed to the UV light. Light that passes through the clear areas of the negative causes a reaction with the monomers of the photopolymer which chemically cross-link with each other to form polymers . These polymers can be thought of as complex chains of monomers, which are linked so strongly, that they behave a single, hard, wear-resistant molecule. The unexposed non-hardened polymer will be removed during the process. The process of producing a plate using negative film is shown in Figure 2. 2.
A more recent method of producing plate is called computer-to-plate (CTP). Digital data from the computer directs the infrared laser exposure of the plate. This thermal energy will then start the acid-catalysed crosslinking reaction [12]. The second step is then preheating the plate to complete the crosslinking reaction [12]. The last step is to remove the unexposed coating with wet processing [12]. CTP plate processing method is preferable to the older method because CTP results in quicker production cycle, lower production cost, easier revisions, sharper print quality and better registration [13].
CTP also eliminates steps from the production cycle [13]. Even in a Computer to Film (CTF) workflow it can take five steps from having the copy in digital form to having it imaged on a plate:
film imaging, film processing, stripping, contacting, and finally plate processing [13].
In a CTP process four of these steps are fully removed [13]. Each step eliminated from the process reduces the overall time required to get plates to press. Not only were these steps time consuming they were also very labour intensive. Labor is not only costly but by virtue of the human element, performance of these tasks may lead to quality and consistency problems.
CTP allows printing presses to print cleaner and crisper images by way of eliminating dot gain in the prepress process [13]. In a conventional prepress workflow, dot gain from photomechanical processes of imaging plates from film can increase overall dot gain by as much as 6% on press [13]. In a CTP workflow, first generation dots are directly imaged to the plate eliminating dot gain in prepress. This also gives the press more latitude for printing higher ink densities without “plugging up.” The benefits are richer, fuller, better saturated color printing.
Film is comprised of a polyester substrate that is subject to changes in humidity and temperature that can cause it to stretch or shrink and this can be a problem for registration [13]. CTP excludes the use of film negatives or positives. CTP plates are imaged on highly accurate plate-setting equipment on aluminum substrates that are very resistant to changes in temperature and humidity.
Before CTP, revisions were cumbersome and time consuming and even more sensitive to the registration issues mentioned earlier[13]. With an all-digital workflow it is simply a matter of making the needed changes to the pages, deleting the old pages, and placing the new pages in place through the use of automated electronic imposition techniques.
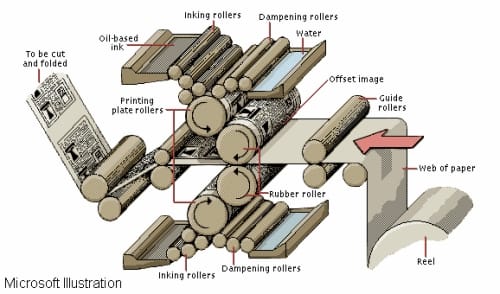
Figure 2. 3. Offset Lithographic Printing Illustration. [14]
Offset lithographic printing is a method of mechanical printing whereby ink is distributed and transferred by the inking rollers and the fountain solution is also distributed by the fountain solution rollers, which are labeled as dampening rollers in Figure 2. 3. Ink and fountain solution are then transferred to the printing plate, printed to the printing blanket and then printed to the paper substrate. Ink is transferred on the printing plate only if the adhesion force between the ink and the plate is greater than the opposing force, i.e. the ink cohesion [11]. Ink is transferred to the image area because the image area is hydrophobic. Ink does not transfer to the non-image area because the non-image area is hydrophilic and the film splits in the layer of fountain solution that is applied before the ink. 95% of concentrated fountain solution is water with small fraction of surfactants and other wetting agents. 2-5 % of the concentrated fountain solution is then diluted with water used for printing.
Linting is considered to be one of the more serious paper related problem in the offset printing of newsprint [15]. It is defined as the tendency of fibres and fines to be removed from the surface of the paper and accumulate on the blanket and possibly also on the plate. Lint migrates from the surface of the paper to printing blanket. It also can be then transferred to the printing plate, ink and fountain solution rollers. Image degradation starts to appear when a considerable amount of lint accumulated in the blanket or plate. This is more likely to occur as the lint particle size increases [17]. Accumulation on the plate is a bigger problem than the initial movement onto the blankets as it interferes directly with ink transfer.
Figure 2. 4 is a printing result of a 50% screen tone and a solid test pattern printed with a Heidelberg GTO-52 at Norske Skog Boyer. It shows a print quality comparison between the beginning of the run and after 7000 copies. Image degradation can be easily seen in the solid as white specks. These are probably lint particles which have transferred to the printing plate.
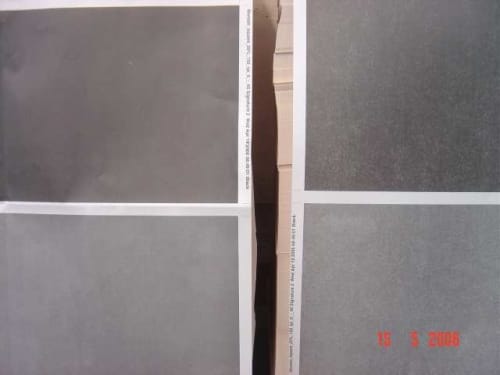
Figure 2. 4. Image Degradation from the beginning of the run (LHS) to the 7000th copy (RHS) caused by linting.
A low level of lint can also cause a problem in subjective human quality judgement as human eyes are more sensitive to a small increase of lint at low level [18]. For high lint level, almost all samples were ranked equally poorly [17-19]. Linting reduces image quality when the build-up of lint deposits on the blanket is non-uniform [17].
Lint primarily consists of three different classes [4, 7], which can be picked up from the surface of the paper during printing. Firstly, lint consists of particles, which are not bonded to the surface at all. Their origin is mainly in the slitting of the web into reels. These particles are referred to as ‘dust’ [7]. Thereafter there are particles that are weakly bound. The stronger the anchorage in the surface the later in the printing process they are removed [2]. These are classified as ‘lint’ [7]. Finally there are fibres, which are bound in the surface but which because of moistening lose their binding ability. This phenomenon is described as water-induced linting or ‘wet-pick’ [7]. Forces required to pick the lint from the surface of the paper gradually increase from dusting to linting and picking [20].
A close examination of the composition of lint reveals four different types of particles – fines and ray cells [21], fibre fragments [21], shives [21] and filler particles [16]. Improvements in equipment [22] and processes [22-24] have led to a decrease in the amount of fibres and shives, whereas the amount of ray cells has relatively remained constant [4, 25]. Thus the size of lint has decreased over the years [21, 26].
The composition of lint has changed over the years from stiff, unfibrillated fibres [5] to deposits dominated by ray cells [16, 21, 26] and fines [6, 27]. Recently, filler [8] and fines have become more significant components of lint, although it was also reported that the surface strength of paper could increase with an increase of fines content [27], because fines could increase the bonding between fibres. If they are not bonded well with the fibre, they will be readily picked up from the surface of the paper. Therefore, the effect of fines on linting is somewhat dependent on the overall surface strength of the paper. However, irrespective of the size, the common characteristic of particles that are linting is their low bonding potential [26].
Offset processes are especially prone to linting problems because of the tackiness of inks [21] and the use of multicolour printing places greater stress on the surface of sheets. Studies have shown that the application of high surface forces in printing is generally associated with the removal of larger particles as lint.
The role of fountain solution has been extensively debated. Fountain solution weakens the fibre bonding and therefore an increase in fountain solution should increase lint[21, 28]. On the other hand, fountain solution lowers the ink tack force [29], which should decrease lint. Reducing fountain solution has been reported to improve ink penetration and dimensional stability but increasing the rate and size of lint accumulation [6]. For this reason, the role of fountain solution at different printing screen tone will be different. Unfortunately most of the literature did not mention the details of the experiments [6, 28] making it impossible to evaluate the results. Hoc specified that decreasing fountain solution tend to increase lint in the blanket of the image printed area [7].
Many linting theories have been proposed but none was found to properly describe the effect of press parameters [28]. Attempts to modify existing theories require a fundamental evaluation and understanding of the linting mechanisms. Based on the examination of the fibre removal curve, it
was concluded that at least three forces were required to fully describe the effect of press parameters on linting [1].
Stefan’s Law predicts the stress required to split ink layer for a Newtonian liquid, under laminar flow conditions, and very high film thicknesses compared to actual printing conditions [1, 28, 30]. It is given by:
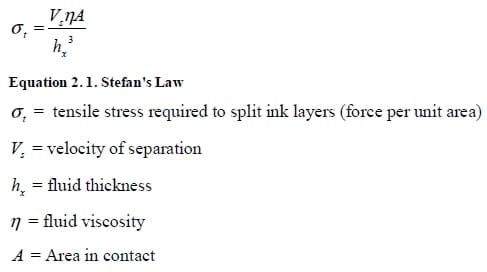
Despite the conditions of which Stefan’s law was derived, it is still used [31] to explain the decrease in the force applied to the paper surface when ink film thickness is increased or ink viscosity is changed.
It was proposed that fibre removal in the printing nip is due to two different types of ink flows, a porous ink flow that penetrates into paper surface pores and a free ink flow at the surface of the ink saturated surface pores. These two forces are shown in Figure 2. 5. It was shown that the ink flows induce sufficient drag on the lint particle to overcome the bonding potential of the weakly bonded surface particles and that the main fibre debonding force is related to the free ink film force, which is an inverse function of the ink transfer function.
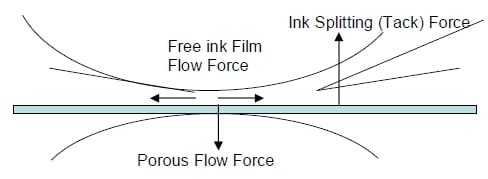
Figure 2. 5. Porous ink flow force, Free ink flow force and ink splitting force. The three of them works at different points. Therefore they can not be added together.
As shown by Figure 2. 5 above, the three forces contribute to lint can’t be added since they are acting at different directions.
The porous ink force can be expressed as
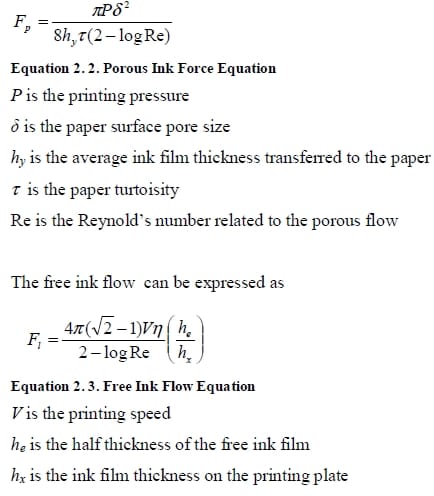
Re is the Reynold’s number of the flow fluid around the fibre. It is to be noted that Reynold’s number is a function of fibre diameter and flow velocity around the fibre.
Linting can be affected by both printing and papermaking variables [1]. By comparison, the paper roughness and the pulp furnish have less effect on linting than the press parameters [1, 7].
The main focus of this thesis is the effect of printing variables on linting and these are discussed in more detail later in this literature review, together with the method for measuring and characterizing lint. However, before this is done, the effect of papermaking variables will briefly be discussed.
2.1 Papermaking Variables [7]
The whole process of papermaking will be discussed in relation to lint, from furnish to stock preparation and paper machine.
2.1.1 Stock Preparation
Screening, cleaning and reject refining are important factors to produce high quality mechanical pulps and reduce linting propensity of the sheet by improving the surface properties [7, 21]. Fibres that are rejected at the screens and processed by the reject refiners tend to be stiff and to make poorly bonded sheet prone to linting and picking. The reject refining process thins the wall thickness of these fibres, creating fines. The combination of thinner, more flexible fibres and fines for bonding creates a better consolidated and stronger sheet surface. Nowadays, systems are operating with double screening, two-stage reject refining or separate refining of screen and cleaner rejects.
2.1.1.1 Refining, Screening and Cleaning
Screening is generally not effective in removing lint candidate fibres [7, 33]. This is because screens separate fibres according to their length rather than according to the specific surface.
Hydrocyclones are more efficient than screens in removing fibres with low specific surface because they separate fibres on the basis of specific surface. The efficiency in removing lint-candidate fibres increases with increasing reject rate [7]. A centricleaner reject requires a substantially higher specific refining energy than a screen reject to reduce the amount of lint candidates in the reject to the same level. Increasing refining energy has been found to reduce linting [34]. At the same applied energy, a grinding process produce less lint candidate fibres than the refining process [34].
Fractionating the pulp with a hydrocyclone, to remove the material of low specific surface so that energy can be selectively applied in a rejects refiner in order to raise its specific surface, is found to be effective [34].
2.1.2 Furnish
2.1.2.1 Mechanical Pulp
Lint deposit from press blanket nowadays consists mainly of ray cells [16, 21, 26] and pulp fines [6, 27]. Ray cells are wood elements that transport nutrients in the radial direction in the tree. They have a diameter approaching that of the normal fibres, i.e. around 20 micrometres, but are not physically entangled in the web to the same extent as normal fibres are, nor are they very conformable. This is because the aspect ratio of ray cells is quite low, i.e. they are short, and therefore they are not entangled in the web. Their contact area to fibres after sheet consolidation in the press section is not high [7].
Ray cells have a relatively high resin content that leads to a very low hydrogen bonding therefore its bonding ability to fibres is weak [7, 34]. Ray cells are readily dislodged from the paper surface, especially when exposed to moisture or when the sheet is not well consolidated.
Ray cells can deposit on blanket as layers that are thick enough to reduce the print quality [7]. They can also travel back to fountain solution and or ink trains and subsequently reappear in the printing nip [7].
A poor mechanical pulp is susceptible to linting [21]. Common causes include insufficient specific energy, non uniform wood supply, unstable pulp mill operation such as lack of control for freeness, coarseness, average fibre length, and inadequate screening, cleaning and reject refining [21].
2.1.2.2 De-Inked Furnish
The traditional ideas says that recycled chemically produced fibres are weakened by recycling and this leads to more linting [21]. However, it was also suggested that for mechanical fibres, linting may actually be reduced since the mechanical and chemical action of the deinking plant may improve sheet strength [35].
The ray cell content of waste paper is much lower compared to papers which contain fresh fibre. This may also contribute to the lower lint result paper made from deinked fibres compared with paper made of virgin stock [7]. It was found that the buildup of filler left over from the deinking process was actually more of a problem than the recycled fibre itself [6]. Mineral fillers in the surface of the deinked-pulp-based newsprint are more easily deposited as lint than the fibrous component [6, 7].
A relationship between fillers and lint can be explained as the fillers settle between fibres, preventing hydrogen bonding between cellulose fibres [7]. As filler content increases, the number of bonds is consequently reduced [7].
2.1.3 Paper Machine
Several papers have discussed the effect of paper machine variables [7, 21, 28, 36, 37] and the effect of printing press variables [2, 6, 7, 17, 38-40] on linting. Some reported that there is little quantitative evidence of the effect of paper machine variables compared with the effect of printing press variables [1, 7]. The difficulties are due to three factors. First, lint measurement is not easy and only good reproducible methods should be used [7, 20]. Secondly, paper machine factors probably interact among with pulp factors themselves [7]. Thirdly, pulp quality [21, 34] has a significant effect on linting propensity and sometimes they can mask the effect of paper-machine factors [7].
2.1.3.1 Sheet Forming
In a Fourdrinier former, lint propensity of the wire side of a sheet is less than that of the top side. The wire side of fourdrinier newsprint has a higher s
urface strength than the top side. Lint propensity on the top side of the paper decreases going from Fourdrinier to Hybrid and to gap former [22]. In order to produce sheet with low linting on both sides, adequate removal of water in both sides of the paper is important in the forming process. The reason for this is when fines are well bonded to the fibres, it increases paper strength. Fourdrainier drainage occurs from the bottom side of the former. Therefore it tends to pull fines away from the top side of the paper. A horizontal twinwire former will still have the effect of two-sidedness, although the drainage occurs from both side of the former, as drainage will still occur preferentially to the bottom side of the paper and drive the fines to the bottom side of former due to the effect of gravity. At the Boyer Mill, the bottom side of the former actually is the top side of the paper once the paper is in rolls. Norstar and Boyer Nornews are produced with a horizontal twinwire former and therefore there will be difference in the distribution of fines on top and bottom side of the papers.
2.1.3.2 Pressing
Lint tendency is decreasing going from straight through presses that drain through the bottom side, to top draining twinvers, or tri-nips [34]. Norstar and Boyer Nornews are produced with a twinver press [41].
In a single-felted press nip, the paper is compressed between a felt and a smooth press roll. Fibres and fines are flattened by the roll and are in intimate contact with its surface [7]. When the web emerges from the press nip, it normally adheres to the press roll rather than to the felt [7]. In an open draw, the sheet is abruptly peeled away from the roll. Depending on the strength of the adhesion to the press roll and the cohesion with the rest of the sheet, the individual fibres and fines located on the paper surface may either become separated from the roll and remain part of the web surface or be picked and remain on the roll surface until they are cleaned off by the doctor blade [7].
Material collected on the press roll doctor blades is composed largely of ray cells. These wood components are known to have a low specific surface, high lignin content and a low ability to absorb water to form papermaking bonds [7, 21]. The material collected on the doctor blades of press rolls or drying cylinders resembles the lint which accumulates on printing blankets and plates [7, 38].Thus corrective measure that reduce picking in the press section of the paper machine might also reduce linting in the pressroom [7, 36].
Linting on the felt side of the newsprint decreased when the load in both presses was increased [42]. However, the lint measurements were done on uncalendered paper and neither the press nor felting arrangements were described. It was recommended that to reduce ray cell linting in the press section, nip loads should be increased or the sheet temperature going to the press section raised. Higher fibre fragments and shives are primarily located on the side that is in contact with the felt [42].
2.1.3.3 Drying System
Picking can occur in the dryer cylinder. If the temperature is too high, the adhesion of individual fibres to the cylinder surface can exceed their cohesion to the wet web [7]. It was suggested that paper damage by picking in the dryer section leads to an increased linting tendency [7].
2.1.3.4 Calendering
At low temperatures, hard nip calendering of newspaper may increase linting [23]. High temperature calendering [23] and soft nip calendering even at a moderate temperature of 110ºC can significantly reduce linting. The lint measurement in this studies were done by removing lint with transparent tape, followed by measurement of lint area by image analysis [23].
Reducing the bulk of a 100% thermo-mechanical pulp newsprint sheet with different combination, of soft nip pre-calendering and hard nip calendering at low temperature increases the offset linting propensity [23].
2.1.3.5 Slitting and Cutting
Blunt slitters can cause linting since a lot of dust is generated during the cutting process. Therefore sharp slitters should be use to minimize dust generation [7]. Mechanical brushing of the moving web suction is also an effective means of removing dust [7].
2.2 Printing Variables
The second part of this chapter will discuss the effect of printing variables on linting. Both the effects of paper making variables [4, 16, 19, 23, 37, 43] and printing variables on linting have been investigated. Some studies have suggested that the printing press variables have a greater effect on the linting propensity of paper than the paper itself [1, 7]. All of the most important printing variables will be discussed in this chapter.
2.2.1 Nip
2.2.1.1 Take off Geometry
The angle separation affects the web-to-surface adhesion characteristics at the point where the sheet begins to leave the nip [7]. The effect can be explained by the fact that one side of the paper has a larger separation rate from the blanket [7]. This is because both sides of the paper travel at the same speed but the two sides of the ink films do not split at the same rate, i.e. the side for which the take off angle is higher will separate from the blanket at a faster rate compared with a side with a lower take off angle, This has been reported in several studies [7, 17, 44], resulting in a higher force imposed to the surface of the paper and causing more lint.
The take-off angle of the paper web from the inked blanket surface is a function of the press geometry and of operating variables such as ink tack, ink transfer, inking level, ink/water emulsification, printing speed and other printing parameters [7]. The blanket cylinder diameters and the press web orientation are the two most important of these determining printing nip geometry [21].
Waech [42] reported that there was no large effect of take-off angle unless the paper wrapped the blanket cylinder rather than the impression cylinder. This meant that the effect was obvious at a high take off angle, i.e. paper wrapped partially around the blanket cylinder. In laboratory testing, paper sample is fixed on the printing cylinder and the take-off angle therefore is constant. However, varying web lead in a large commercial printing press would make it possible to do trials with different take-off angle [7].
There has not been much work to investigate the effect of take off angle compared with the effort put into investigating the effect of the other press variables nor have quantitative results been produced. Therefore further study is required to quantify and measure the importance effect of take off angle to linting.
2.2.1.2 Blanket
As the blanket cylinders of a web offset press are geared in a one-to-one ratio, both cylinders must be packed evenly and should have similar kind of blankets to obtain identical speed of the elements in the printing nip. When packing mismatch between the blanket cylinders occur, the lint accumulation increases slightly [7, 21]. A mismatch of peripheral speed between blankets has greater influence on the lint migration on the blanket surface rather than lint pick-up [7].
2.2.1.3 Plate to Blanket
Plate-blanket pressure is believed to affect lint even though the plate does not touch paper due to three particular situations of plate-to-blanket velocities that occur [7]. The first arises when the blanket is over-packed. The peripheral speed of the blanket in the nip is greater than the plate speed. Lint particles which accumulate on the blanket will move in a direction opposite to that of the moving web. The second case [7] is when the blanket is under-packed, and the speed of the blanket is less than that of the plate cylinder and the lint particles will be pushed forward in the direction of the moving web. This normally occurs when using old blankets that have lost its flexibility.
The third case [7] is when plat
e and blanket are correctly packed. The peripheral speed of both are similar to each other therefore very little to no migration of lint occurs.
Plate-blanket study is important since lint movement results in migration and build up of the lint. Once the lint is built up on the plate and in the ink trains, runnability and image quality will become a serious issue.
In plates containing only solid (100%) and non-printing area (0%), blanket lint was observed to decrease with decreasing solid area compared with the lint in the ink plate and ink trains [38]. This suggest that the lint picked up from image area is more likely to contribute to blanket lint, while the lint picked up from the non-image area is more likely to be released to the plate and then transferred to the ink train [38].
It was reported that it seemed that the lint particles on the plate were larger than those on the blanket [38], although the author only visually measured it, without any quantification [38].
It was also reported that there was migration of lint on the plate, i.e. from the image area to the non image area [20]. If this has been validated, it would then need to be questioned whether increasing fountain solution feed to the plate affected the non image area lint by increasing the amount of lint picked up from the non image area or by increasing the lint collected from the non-image area as a result of the migration of lint from the image area. This would be able to be confirmed by using image analysis and judging whether the lint collected are coloured. Coloured lints would have migrated from the image area while non-coloured lints would have originated from the non image area.
2.2.1.4 Pressure
The effect of pressure on linting is not fully understood. This is due to the lack of comprehensive models of ink-paper-press interactions. Most results showed that lint increased both in non-image areas and in image areas when the printing pressure is increased [7, 28]. However, the opposite result has also been reported [7, 45]. It has been shown that due to the non-linearity and the synergy between linting and the various parameters, with the right combination, a low printing pressure can produce more lint than a high printing pressure [1]. Overpressure in the nip was reported to reduce blanket lint deposits by way of a frictional cleaning effect although the authors stated that overpressure actually caused the paper to lint more [6]. These contradictory reports do not explain the details of the experimental conditions, such as printing speed, the type of printing machine, the type of blanket or the number of copies done. This may be the reason why the reported results vary so much. It was also observed that there was generally less lint in a blanket to blanket nip than in blanket to steel nip [6].
Pressure plays important role to all three forces described by Mangin [32]. The ink porous flow force (Equation 2. 2) is directly proportional to pressure. On the other hand, the free ink film flow force (Equation 2. 3) is directly proportional to (he/hx)2, where he is half of the thickness of the free ink film and hx is the ink film thickness on the blanket. This is likely to fall as printing pressure increases, as more ink will be forced into the pores of the paper.
The ink tack also depends on the ink film thickness although there is dispute about how tack will change with the ink film thickness. Tack force, as it is measured by the parallel plate tack-meter decreases with increasing of the oil or ink film thickness but not as a function of the cube of the ink film thickness [28, 46]. However, these measurements were done in a parallel tack meter with ink that was vertically elongated to do the measurements. The tests also used a with high ink film thickness, i.e. 5-35 µm. The lower plane was attached to a force sensitive piezoelectric transducer that measures the forcetime curve during splitting. These conditions are nowhere near the printing condition where the thickness of the ink is in the order of a micrometer and it definitely has different geometry to the blanket printing rollers. Therefore the results from this experiment may not be directly comparable to the printing press condition. In addition the material used was oil [28], not ink.
Recent studies showed that ink tack increases with the ink film thickness [17, 30, 47-49]. The equipment used in some of these experiments measured the ink film splitting force using printing rollers with only ink printing on the cylinders [30] while other equipment was later used that could simulate offset printing with a cylinders on paper substrate [17, 47, 48]. Zang [30] reported five different sets of measurements of the effect of ink weight to ink tack. All five of them showed ink tack increases as a function of ink weight in the range that is very high of interest of offset printing. Only one data set showed a decrease in ink tack for ink weighs above 5 g/m2. This was attributed to the Stefan’s law type behaviour. Mangin and Silvy [1] also stated that the lint reduction at a high ink weights also might be due to a Stefan’s type law, but only when the surface is fully saturated with ink.
Thus, the three forces will increase and decrease at the same time as pressure changes and how lint is affected will probably depend on which force is most important under the condition they are tested. We can not work this out since most of the experimental details are lacking.
2.2.2 Lint Accumulation Characteristics
2.2.2.1 Lint Accumulation Rate with the number of Copies Printed
Lint accumulation is highest in the beginning of the run and diminishes significantly as the run progresses. In the beginning of the run, lint accumulation curve behaves linearly until it reaches a point where the curve starts to flatten out [19, 50, 51]. It was explained that this behaviour was due to two competing processes of lint transfer to the blanket from the paper and lint transfer off the blanket. At the start of the run there is no lint on the blanket and so lint transfer onto the blanket dominates. As lint build-up on the blanket increases the rate of lint transfer away from the blanket also increases until the lint migration from paper to blanket is equal to the rate of migration of lint from the blanket to the plate [51]. At this point the lint on the blanket will reach a constant level. This was mathematically expressed as
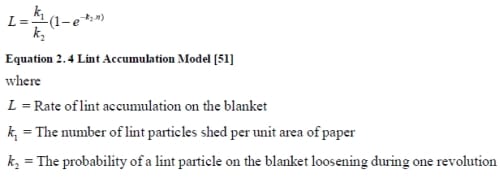
A high speed, high resolution camera combined with image analysis was developed to monitor the lint on the blanket dynamically and to determine the rate constants from Equation 2. 4 [51].
2.2.2.2 Lint Accumulation of First and Subsequent Printing Unit
Lint accumulation in offset blanket is not uniform between printing units and the mechanism of ink transfer and setting, particularly in multi-colour printing, is poorly understood [52].
In the first printing unit, lint consist of smaller particles compared with the subsequent units [2], if all of the conditions are constant between the printing stages. It was suggested that the lint particles on the first printing unit are normally the weakly bonded particles that loosen up from the surface of the paper [7] and their origin is mainly in the slitting of the web into reels [7]. The type and size of lint particles can vary due to differences in other printing variables. Therefore the lint in the first printing station is not only dust originated from slitting, although it will include some of this. It has been shown before that a single printing unit of a smaller printing press produced lint particles similar to the fourth printing unit of a larger commercial press [2]. This may be due to the difference printing parameters applied and also the difference of the press geometry [2].
The stronger that particles are bond
ed to the surface, the later in the printing process they are removed [2, 7]. Well bonded fibres can lose their bonding ability because of moistening. This is sometimes called water-induced linting [7] that occurs in the third or fourth printing units.
2.2.3 Speed
Effect of printing speed is not fully understood. However, it is usually believed that linting increases with increasing speed [28]. It has also been reported that the increase of lint accumulation with speed is two or three times more in the image area than in the nonimage area [7]. This is probably because an increase in speed increases tack force and also increase in speed increases the free ink film force (Equation 2. 2). Tack force between paper and ink film would be higher compared with the tack force between paper and water film.
The percent transfer of ink from the blanket to the paper is an inverse function of the length of the time the ink contacts the blanket [53]. As speed increases, the nip dwell time, i.e. the contact time between the ink and paper surface decreases. This results in less ink flow into the porous surface of the paper .
Ink transfer was modeled in three steps [54]: contact and adhesion between the ink film and the paper surface, immobilization of a portion of the ink into the paper pores, and splitting of the remaining portion of the free ink film. This was mathematically expressed as:
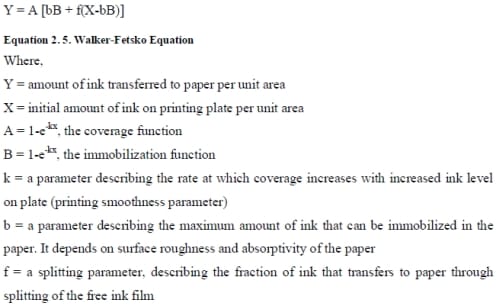
When the contact between the ink and paper is complete at high ink levels, Equation 2. 5 can be approximated by the following linear relationship Y = b(1-f) + fX
Ink film splitting is approximately in the middle through the free ink film. Although there are variations such as the percent transfer of ink from the blanket to the paper is less than percent transfer from the plate to the blanket [52, 55] because once the ink is on the blanket, selected ink components are absorbed and the ink begins to set [53].
The larger the porosity of the paper, the more ink flows into the pore of the paper therefore the pore flow force increases and the ink film thickness decreases resulting in the lower free ink film force.
Referring back to the force equations proposed by Mangin (Equation 2. 1, Equation 2. 2, Equation 2. 3), this means that speed will not have a linear or straight forward relationship with linting. Lower speed will have the same effect as higher pressure (refer to 2.2.1.4). Speed plays an important role in all three forces described by Mangin [32] as the ink porous flow force and ink film flow force (Equation 2. 2, Equation 2. 3) are inversely proportional to speed. On the other hand, the free ink film flow force (Equation 2. 3) is directly proportional to (he/hx)2, where he is half of the thickness of the free ink film and hx is the ink film thickness on the blanket. This is likely to rise as printing speed increases as less ink will be forced into the pores of the paper. How speed affects lint will be dependent on which of the three forces is dominant at the condition at which the printing is done.
In a printing press, the effect of speed on lint is less dramatic for a larger diameter blanket cylinder since the tack force is related to the ink filament acceleration at the exit of the printing nip [7]. Cavitation in the ink film results in filaments which are accelerated normal to the paper surface, with the acceleration, a, given by [7, 28].
a = V2/R – Where, V is the velocity and R is the radius of the printing cylinder
Acceleration is inversely proportional to the cylinder radius [7]. Therefore, for the same linear speed, presses with larger cylinder diameter produces less acceleration compared with that of smaller cylinder. Press with bigger cylinder diameters produce less lint than presses with smaller cylinder diameters at the same printing speed [28].
2.2.4 Temperature
Temperature of the printing press varies across the width of the press and varies from run to run and there is also variation during a run as the press warms up [39]. Two main parameters that influence heat production are the rheological properties of the ink and the rubber of the inking rollers [39]. It was identified by MacPhee, as reported in Dalphond [39] that three of the five sources of heat generation in an inking system were related to ink rheological properties and to the printing speed: ink film splitting, vibration inking roller action and inking roller slippage. The other two sources are constant for each press running under fixed condition, i.e. cyclical straining (compression-decompression cycle) of the roller cover and roller bearings. MacPhee as reported in Dalphond [39] stated that for a sheet-fed press running at 2.8 m/s, 79% of the total heat generated comes from the ink film splitting, the vibrating roller action and the circumferential roller slippage[39]. It was found that for a web offset press that blanket and plate temperatures range between 29º-39º C while the ink form roller and the oscillating roller temperature ranged from 24º-40º C [39].
As the temperature in the press increases, the tack and viscosity of the ink decreases [7, 21, 39]. The lower the tack and the viscosity, the smoother the ink transfer is, therefore the lower the lint accumulation is [7]. On the other hand, the lower the viscosity, the greater the chance of the liquid components of the ink that are more volatile penetrating into the paper, increasing risk of tack rise on the blanket [7].
Control over the temperature of the ink is mandatory to decrease the variation in dot gain and density over the printing run [39]. Dot gain has been reported to increase as the temperature increased. Print density was reported to decrease at lower printing tone while it increased at a higher printing tone with the increase of the temperature [39].
Temperature also affects fountain solution properties. Fountain solution should be maintained at a constant temperature in order to control its evaporation and its viscosity [39]. It has been reported that fountain solution helps to cool the press therefore its absence in waterless offset has a major impact [39].
2.2.5 Relative Humidity
Relative humidity has been reported to be of negligible importance compared with other printing parameters [7, 28]. However, linting has been reported to be more serious in summer months when the relative humidity is higher than that of winter months, although no real data has been provided to justify this claim [7]. It was suggested that relative humidity may affect paper surface wettability and capability to absorb offset fountain solution [7, 28].
In contradiction to [7], another review reported that lint could be reduced by increasing humidity and increasing temperature [21]. They argued that increasing humidity improves the fracture resistance of fibre-fibre bonds [21]. This is a very grey area whereby both of the effects can apply to paper in relation to linting. However, if both of the theories were right, there must be an optimum humidity level which results in minimum linting. Relative humidity is something that is hard to investigate. A further complication is that none of the reports gave experimental details of the press trials. These reports were only from observations and no further investigations were carried on.
2.2.6 Fountain Solution
2.2.6.1 Fountain Solution Composition
There are two types of fountain solution-acid and alkaline [56]. Only 5% of the fountain solution components are active ingredients, the rest is water. The main ingredients of acid fountain solution are water, a desensitizing gum and an acid (phosphoric acid, an acid phosphate compound, or citric or lactic acid) [56]. The acid converts the desensitizing gum to its free acid form in which the molecules contain carboxyl groups, -COOH [56]. These groups h
elp the gum adsorb to the metal plate [56]. Gum is used to prevent plate corrosion. The acidity of the dampening solution is measured by determining its pH. Modern acid fountain solution should have a pH in the range of 3.5-4.5 [38]. Excess acid in the dampening solution is not only useless but may be a disadvantage. If such a solution is emulsified into inks containing varnishes with drying oils, the inks will take longer time to dry [38]. Furthermore, acidity promotes corrosion and can actually cause a sharpening of image area dots due to corrosion on a lithographic plate [38].
The alkaline fountain solution ingredients are mixture of water, sodium dihydrogen phosphate(NaH2PO4) and disodium hydrogen phosphate(Na2HPO4) at a pH around 10 or 11 [56]. At this pH, the phosphate ion reacts rapidly with the aluminium surface and functions as the desensitizing material. When alkaline fountain solutions are made the concentration of the active ingredients are controlled through measurements of conductivity and not pH since the solution is highly buffered [56].
Several advantages of the use of alkaline dampening solutions on newspaper offset presses have been claimed [56], these include that linting will be reduced because it usually requires a little more dampening solution to keep the plate clean. In addition, ink rollers usually do not strip and blankets do not become glazed since the solution contains no gum and fungus does not grow in the fountain pan [56].
Few studies had been done on the effect of acid or alkaline fountain solution on linting. Most of the papers in the linting literature did not even specify the type of fountain solution they used. However, it has been reported that more lint was deposited with alkaline fountain solution than with the acid one when the plate has a preponderance of image area and the reverse is true when the plate mainly consisted of non-image area [38]. The advantage of alkaline fountain solution with the largely non-image area plate for reducing lint was particularly apparent in longer press runs [38].
2.2.6.2 Effect of Amount of Fountain Solution Used
The role of fountain solution has been debated. Fountain solution weakens the fibre bonding and therefore more fountain solution effect should increase lint. It was reported that printing the same paper with both letterset (without water) and relief lithography (raising the image area and not having the non image area on the plate but printing it lithographically) resulted in higher linting results with the lithographic method (with the water) [38]. The authors argued that water could not have lowered the fibre bonding since the contact time is in the order of milliseconds only but somehow the role of water is to make fibres more flexible and more conformable so that it decreased the migration rate of fibres from blanket back to the paper but it was not further explained.
Fountain solution lowers the ink tack force [7, 28, 29] therefore increasing fountain solution flow should decrease lint. Increasing fountain solution flow to the plate reduces lint build-up on the blanket in both the non-image and image areas. In the image area, it was reported that 50% reduction in dampening led to a threefold increase in the lint weight accumulated on the offset blanket [28]. In the non-image areas in the first printing unit, lint accumulation in the press blanket decreases when dampening increases [28]. It has been reported that an increase of solution flow from the minimum to maximum extreme limits of tolerable fountain solution consumption led to a 50% drop in linting in the screened area while a reduction to less than half the solution flow from the normal setting led to a three-fold increase in lint deposit in the non-image areas [7]. Waterless printing with letterset resulted in more coarse and greater quantity of lint compared with that of offset lithographic printing [38].
Fountain solution weakens the fibre bonding but decreases the ink tack, therefore the role of fountain solution in different printing screen tone might be different. Most of the literatures did not mention the details of the experiments, nor the effect of fountain solution in all of printing tones that were investigated.
In order to reliably test the effect of fountain solution on linting, it is necessary to determine how much fountain solution is emulsified in ink. This is quite difficult and will be discussed later (Chapter 3.31). It is not possible to estimate the amount of fountain solution emulsified in ink just from the ink and fountain solution duct openings or even from ink and fountain solution consumption as the fountain solution can do three thingsemulsify, spread in the non image area, or evaporate. There have been some on-line sensors that have been developed to try and measure fountain solution emulsification [6, 39, 57, 58]. Only Near-Infrared Moisture meter [57] was used in our experiments but no quantitative information could be obtained due to the limitation of time.
2.2.6.3 Effect of Fountain Solution Composition Change on Linting
Alcohol is sometimes added to the fountain solution. It is known to improve the wettability of the offset plate and it is also used to reduce scumming, an undesirable effect showing ink spots on originally white areas of the image. This happens if the printing plate is not able to separate the ink effectively from non-printing areas of the plate. It also reduces lint accumulation by up to 25% [7]. However most of today’s newsprint is printed without alcohol.
Hydrophilic correctors are necessary to prevent corrosion of printing plates. They function by filling in capillaries formed in the protective oxide layer on the plate surface, thereby preventing corrosive ions from reaching the aluminium surface. Therefore corrosion is prevented.
Hydrophilic correctors also improves print quality, especially at the beginning of the run, where they facilitate cleaning and they stabilise the ink/water balance [6]. Some reports showed that lowering the content of hydrophilic corrector in the fountain solution increase the blanket deposits by a factor of 2.5 [6]. However the exact amount of the reduction of hydrophilic corrector was not mentioned.
2.2.7 Printing Form: Screen Ruling and Printing Tone
The effect of printing form on linting relates both to screen ruling and tone value, as well as the physicochemical properties of the plate surface [28].
The screen area produces more lint than that of solid. However this can not be related directly to either the percentage of inked area, or to the total perimeter length of the inked/non-inked interface, although the percentage of inked surface and total ink/ uninked interface is larger for screened areas than that for solid [28]. The relationship between solid and non-image area linting is also not well understood. Some results showed that non-image area gave a higher lint result while others found no difference between solid and non image area linting [59].
It was reported that a screen ruling between 65 and 133 line per inch (lpi) had no significant effect on lint [28]. However, lint also has been reported to increase linearly with screen ruling between 65 to 100 lpi independent of tone value [28]. Larsson and Jansen, as reported in John, et al [38] found that the finer the plate screening, the higher the lint result was. Larsson and Jansen suggested that the boundary length between the image/non-image areas was the critical factor in determining lint. This was then investigated by John, et al [38] who found that increasing the boundary between the image and non-image area by a factor of thirty had no effect on lint. The only difference observed between the two plates was that the longer boundary length plate produced a slightly higher amount of lint in the ink train compared with the plate with the shorter image/non image area boundary [38]. The reasoning and the mechanism of it was never explained.
Researc
hers who have investigated the effect of printing tone on lint generally find a maximum in lint at some intermediate value of printing tone. However different studies have come to different conclusions about where the maximum is.
In one study, the average size of lint particles was at a maximum at 50% tone value and decreased linearly as a function of tone value on either side of this maximum [28]. The number of particles removed also increase as a function of the size of the particle removed [28]. In another study [59], it was reported that between 30 and 70% tone value, the number of lint particles was constant for particles with surface area between 2000 to 30,000 µm2. However for particle sizes greater than 30,000 µm2, the number of particles increased as a function of the tone value. Heintze showed that linting on a small Apollo web offset press was independent of tone value between 30 and 70% dot area for a screen ruling of 85 lpi (line per inch) [60]. In the solid area, linting increased with print density [60]. It was speculated [60] that the increase in tone value, up to the point of maximum lint, increases the number of possible ink-to-fibre contacts, i.e. ink anchor points and therefore the probability that particles may be debonded by ink-related forces.
Some important results from the Apollo Press trials were that large lint particles, i.e. lint particles that could be retained by the 150 mesh screens, of the non-printed area (0% printing screen) in the blanket did not change with the number of copies printed [60]. Large lint content of the 30% and 70% screen tone of the blanket increased strongly as the number of copies printed increased [60]. For a shorter press run of either 2,000 or 20,000 copies, the lint from the area of 70% screen tone has a significantly higher fraction of large particles than that of the 30% ink coverage area [60]. However after 40,000 copies, the large lint content was found to be about the same in both 30% and 70% coverage areas [60].
It was reported by Mangin [28] that Parker and Morton found a maximum lint accumulation between 33% and 67% tone value at 3,000 impressions, but at 33% tone value at 12,000 impressions and when the ink level was increased, the maximum in the lint accumulation curve was shifted towards a higher tone value.
It can be seen from the above discussion that the results on the effect of screen tone of lint are not consistent, although there is general agreement that the maximum lint is obtained at a screen tone somewhere within the screen tone range of 30-70%. This is probably because a range of printing machines were used including an Apollo printing press [38, 60], Hamada printing press and Heidelberg GTO-52 . In addition, details about the fountain solution and ink level of emulsification, the dot shape and dot orientation, the ink and also the take off angle are not generally given. All of these variables could have affected the results of the trials. For example, different types of ink (sheet-fed/web-fed, heatset/coldset, ink tack, what the ink vehicle is, i.e. mineral oil/vegetable oil, etc) will produce different lint results.
Most of the experiments also did not state what the print density was or how it was controlled. The thickness of the ink on the plate will determine the gain of a printed screen dot and so therefore the actual screen tone on the paper surface. Furthermore, each and every individual printing tone is a combination of image and non image areas, each of which has their own lint accumulation rate characteristic.
2.2.8 Printing Plate
Plate surface physical properties, especially the graininess of the plates and its wettability were reported to affect lint accumulation on offset blanket. However, these effects are not well understood yet [59].
The grain on the non image area plate acts as a reservoir for water. It facilitates wetting and therefore the ability to hold a thin film over the entire surface. A smooth ungrained plate has a tendency to collect water in drops and not cover the plate with a complete film [7]. The effect of blanket-plate nip to linting is discussed in chapter 2.2.1.3.
2.2.9 Blanket
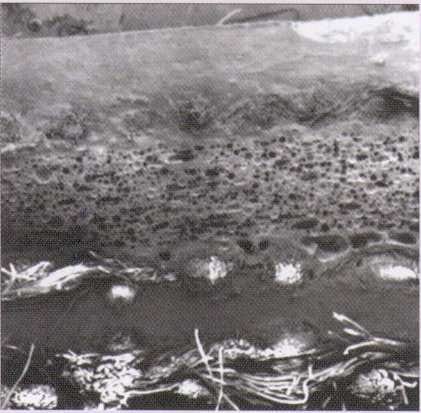
Figure 2. 6. Compressible Blanket [61]
Although the blanket are known to be the most important part of the offset process because ink is transferred from the blanket to the paper, relatively little is known about blanket properties and their influence on lint accumulation and print quality [39].
Several blanket properties influence lint accumulation, i.e. adhesive properties, hardness and compressibility. When the blanket is compressed, the blanket flow properties may also affect fibre removal during printing. Blanket materials are complex, layered structures whose behaviour in the printing nip (please refer to chapter 2.2.1) and in the presence of ink, water and lint is not well understood [6, 7].
2.2.9.1 Durability
The surface characteristics of the blanket are important to lint performance in offset lithographic newsprinting. New blankets showed a rough textured surface under electron microscopy while old blanket appeared to have developed an additional layer of deposited material over the surface texture of the blanket [7].
Old blankets pick up significantly more lint than that new ones. Blanket age also has a strong influence on the migration of lint [7]. Old blanket has lost its adhesive and compressibility properties therefore, at the same applied shear rate when compared with a newer blanket, an old blanket would result in higher lint migration. Old blanket normally has a glazed and smoother surface than the new one. It was shown that a smooth surface exhibited worse picking [6]. However the degree of compressibility did not appear to affect lint results [6].
An aged blanket, with a glazed surface that has lost its surface roughness and its adhesion, reduces the ability of the fibres to adhere to the blanket [7]. The fibres are then more susceptible to migration since the printing nip is conducive to slippage. Since there is more rapid lint migration, the rate of lint accumulation does not decrease [7]. Blanket adhesive properties are limited by the presence of water, both free and emulsified in ink. It was believed that increasing the water will decrease linting by reducing the blanket adhesion [7]. An increase in blanket adhesive properties resulted in an increase in fibre removal [7]. This phenomenon is similar to the ‘ink release property’, i.e. the more ink adheres to the blanket, the harder it is for ink to be released [7]
2.2.9.2 Hardness
The effect of blanket hardness is controversial. A lot of studies have shown that lint increases with blanket hardness [7]. On the other hand, there has been a report that said that linting decreases as a function of blanket hardness [7] and that blanket hardness is important to provide ability of the blanket to conform to the paper surface and ensure a transfer of a thin uniform ink layer [39]. Increasing blanket hardness will decrease print quality due to blanket ink hold out and ghosting.
2.2.9.3 Compressibility
Lack of compressibility normally results in a reduction of ink transferred to the blanket from the plate. The print density in some areas become light and the solid area appears to be grainy and blotched [7]. Due to this, the printer normally corrects the printing by feeding more ink which in turn necessitates an increase in fountain solution feed to the plate. Once the ink level is increased, it is difficult to adjust the water so that the water/ink balances properly. Therefore lint will be then governed more by the effect of the operator trying to adjust the ink/water balance than by a change of blanket compressibility [7].
A compressible blanket consists of three layers, a rubber layer, a compressible layer and a fabric layer in th
e bottom [61]. In quality control laboratories of blanket manufacturers, the compressibility is measured without tension. The blanket thickness reduction under a given pressure is used as an indication of compressibility [39]. Both the age of the blanket (even if it has not been used) and how much the blanket has been used to print affect blanket compressibility.
Some studies have shown that compressible blankets create more lint than incompressible blankets [7].
The discrepancies between the reports on the effect of blanket hardness on linting could be explained by the opposite effects the blanket could have on ink film flow force and ink porous force. For a given load applied at the printing nip, a harder blanket will have a higher peak pressure. This will result in a higher porous flow force but a lower ink film flow force, since the harder blanket will force more ink into the paper pores (refer to chapter 2.2.1.4). Thus a change in blanket compressibility could either increase or decrease lint depending on the relative importance of the two forces.
2.2.10 Ink
Coldset offset lithographic ink normally consists of 20% carbon black, 5% alkyd resin, 5% vegetable oil, 10% hydrocarbon resin and 60% of mineral oil [62].
The rheological properties of ink, i.e. viscosity and tack, are functions of temperature and the ink chemical composition as well as the degree of emulsification of the fountain solution in the ink [30]. Tack is defined as torque force required to split the ink film on the roller of the inkometer at one metre distance away from the centre of the cylinder. It is also related to the viscosity for inks manufactured from the same chemical components. Tack determines how easily the blanket releases ink [7]. At a slow printing speed, ink tack is mainly affected by filament elongation while at high printing speed, ink tack is affected by the maximum force transferred to the paper surface before the ink film splits [7].
Ink drying and setting can be a problem in newspaper printing. Newspaper coldset inks are not sufficiently dry immediately after printing since they dry only by setting at room temperature condition [63]. Therefore ink tends to be partly transferred onto other paper surfaces pressed against the printed surface by trolleys or by folding jaws, a condition called set-off [63]. Ink transfer also occurs onto press parts if the freshly printed web contacts them during its travel and rubs off [63]. Rub-off is also a problem in the finished product [63].
“Drying” or, to be exact, setting in newspaper printing just means that the low molecular weight ink vehicle is absorbed into the pores of the paper while the pigment and binder stays on the surface of the paper [64]. Multi-channel confocal microscope can measure liquid penetration into porous webs at a press nip to determine quantitatively the rate and degree of penetration of inks into paper pores [65-67]. It was found in these studies that the bigger the pores the quicker ink sets [64]. However, since the amount of sample used is relatively small, it has to be assured that the sample is uniform and representative, therefore sampling technique is critical.
2.2.10.1 Ink Tack and Ink Viscosity
Viscosity and tack are functions of ink temperature [5, 31] and chemical composition. Offset inks are non-Newtonian and pseudo-plastic, i.e. the viscosity decreases with the increasing shear rate [39]. They are also thixotropic meaning that the ink viscosity decreases with time at constant shear rate [39].
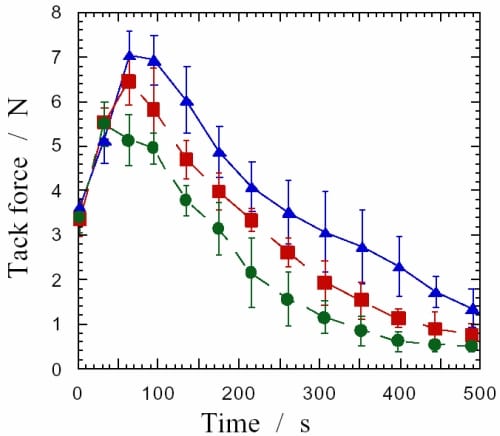
Figure 2. 7. Ink tack development with the addition of fountain solution. 0%(triangles), 15% (squares) and 30% (circles) [29]
Ink tack is also affected by the amount of fountain solution that has been emulsified. Figure 2. 7 showed that the higher the level of fountain solution emulsified in ink, the lower the tack is [29]. The ink emulsions in this figure were prepared using a Ultra Turrax colloidal mill ( Janke & Kunkel GmbH, Germany) [29]. The measurement of the ink tack after the ink emulsion was transferred to the paper was performed with ISIT (Ink Surface Interaction Tester) [29]. The tack measured by ISIT was the force required to separate the disk covered with the ink film from the paper. [29]
The Hydroscope is an instrument that can be used to measure ink tack as a function of fountain solution addition as well as determining the point at which the emulsion becomes saturated and the time required to release the fountain solution after it reaches it saturation point [48].
It has been reported that no agreement has been found between the results obtained from the Duke Tester and a Mixmaster, when both of these mixers were used to produce ink emulsions saturated with fountain solution, with the emulsification on the press [39]. As reported in Dalphond [39], Chou and Cher argued that this may be because emulsification tests provide a mean of determining the emulsification rate and the emulsification capacity of the ink but they do not measure changes in physical properties of the ink caused by emulsified fountain solution. Another laboratory experimental method that had been used to measure the amount of water emulsified in ink is gravimetry. This was used to measure the gain in weight at the end of 30 minutes of mixing of ink with water [39]. As reported in Dalphond [39], Fetsko mentioned that Karl Fischer titration was also used to measure water emulsification in ink. However, this method is very time consuming and complex. It also cannot detect any isopropanol that might have been used in the fountain solution.
Although emulsification rate and capacity are useful to measure, the characteristic of the emulsion in the printing press is not solely dependent on the ink itself. The printing press physical properties such as the ink roller speed, fountain solution feed rate and fountain solution roller speed also contribute to the degree of emulsification of the process ink. Therefore sampling the ‘process ink” either from the printing plate or from the inking roller once it has reached stability also needs to be done in order to measure the level of emulsification on the press.
Tack is defined as the maximum in the force exerted on the paper surface by the ink, from the onset of cavitation in the ink film to the rupture of the ink film filament [28] which is an extension of the definition implied by Kehla, et.al. [46].
Most researchers reported that an increase in either ink tack as measured by inkometer, or ink viscosity leads to an increase in lint [1, 7]. Ink tack varies with the amount of fountain solution added [29, 49, 68], the speed of printing roller [47-49], also the ink film thickness [47-49, 69, 70]. Another study showed that linting increased with increasing ink tack only at low printing speed [7]. In addition, lint usually increased more in the screened area than that in solid area [7], when tack was increased.
Due to variations in rheological properties with temperature and printing nip shear rates, as well as complex interactions with other printing parameters, the mechanisms related to the effect of ink viscosity and tack on linting are not well understood [7, 30].
2.2.10.2 Inking Level
Contradictory effects of the level of ink film thickness on the blanket towards lint have been reported [7]. Some studies from trials on commercial press have reported an increase of lint on the blanket with increasing ink film thickness, others have reported that there was no effect of ink film thickness [7]. However, these results do not agree with acoustic results which have found that printing with higher ink film thickness resulted in higher acoustic power from the splitting of the ink film, which is related to the ink tack [49, 69]. Printing with higher ink film thickness also resulted in higher tack force measured by Prüfbau Deltack [17, 47, 48].
The amount of ink
transferred to the paper is quite low and typically the amount of ink on the paper required for a solid print is around 1 g/m2 which correspond to a thickness of roughly 1µm [64]. A difficulty in adjusting ink/water balance is probably the cause of the disagreement in the reports [7]. Operator factors may mask the effect of inking level since the operators adjust the ink/water balance and print density manually [7]. In addition, a lot of the reports did not really report how they measured the thickness of the ink printed on the paper. Sometimes it has been stated that printing press ink settings have been increased but the physical meaning of increasing press setting was not really clearly explained.
2.3 Lint Measurement and Characterisation Method
2.3.1 Laboratory Experiments
The IGT-AIC-2 is a piece of laboratory printing equipment that has been used to test for dust, lint and picking. For dust test, deionised water was used. After printing a paper strip with water, fibres from the printing forme are collected on a micropore filter. The rubber dampening disc is cleaned of fibres between each printing. The fibrous material originating from the printing with water of 10 paper strips is collected in a clean glass bottle. Two sets of ten strips are prepared. The fibre suspension from each bottle is run through a fibre analyzer. The test result is then reported as the number of fibres removed from the known surface area of the printing disc. The whole solution has to pass through the fibre analyser. The differences between a dust and a lint/pick test is that a lint/pick test uses oil and the viscosity of the oil can be varied by changing the resin content [15], also the use of speed acceleration for pick test and steady speed for dust test. Pick test observes the distance at which fibres visibly start to pick from the surface.
The advantage of using laboratory experiments are the minimum amount of sample required and the time required to do the experiments are relatively short. However, the standard pressure and ink tack that are used in IGT are much higher than those in a commercial press. Therefore a lot of laboratory experiments do not produce lint that is representative of the sort of lint picked up from the printing press [2]. The reason that much higher pressure and ink tack was chosen for the IGT experiment was because the amount of lint picked up from the surface of the paper in a printing press represents only around 0.002% – 0.004% of the surface of the paper. Therefore, running several strips of paper through an IGT under comparable conditions to a commercial press, will not produce enough lint to be accurately analysed.
2.3.1.2 Fibre Length Analyser [21, 40]
Fibre length analysers, such as the Kajaani FS200, have been used to analyse fibrous materials removed from the paper surface during various printing experiments [40]. The instrument analyses all fibrous material present in a volume of water according to its projected length. Most authors agree that about 90% of the lint debris is shorter than 1mm. the average length of lint material which is well within the range of the fibre analyser [15].
Kajaani and the newer version of Kajaani (called Fibrelab) are good for measuring fibre fragments in lint. The experiment time is also very short, around 15 minutes per sample. However the Kajaani is optically blind to most fines, as well as ray cells and fillers, therefore it does not detect the most common lint particles.
2.3.2 Small Scale Printing Trials
2.3.2.1 Hamada 612 CD [45]
A Hamada 612 CD was used to test lint tendency of newsprint. The test used a dry blanket without ink or fountain solution. A hand held reflectance meter was used to measure the change in surface reflectance of the black offset blanket [45]. Hamada press method is easy to operate since there is no ink and fountain solution applied. It is also a simple test and time efficient. However, it is not representative of what really is occurring in offset lithographic printing as it does not include the effect of ink-water interaction with paper.
2.3.2.2 Heidelberg GTO-52 [45]
Heidelberg GTO-52 trials were done by printing 2,000 A4 sheets with a test pattern that included a large solid area. Relative humidity and room temperature were controlled and all press settings were held constant [45]. The quantity of lint was assessed by weighing adhesive tape strips taken from the solid image area of the blanket and expressing the weight change of the tape in grams of lint per square metre. A Gretag E186 densitometer was used to measure the print density across the width of the sheet. A print density of 0.7 was targeted by changing the ink keys [45]. Increases in linting have been detected due to decrease in room temperature, due to ageing of blanket and dampener and due to a decrease in nip pressure [45].
2.3.3 Web-fed Commercial Press Trials
2.3.3.1 Apollo Press [38, 72]
The Apollo press is a web-fed printing with a maximum speed of 28,000 copies per hour. The Apollo press has been used to measure the linting tendencies of mechanical printing paper for over 30 years [72]. For most of this period, the press has been run according to a test method using 500 copies that was developed in 1970 [59]. Heintze then developed a newer test method [72] with the same standard inks, blankets and other press condition as in [59], but the printing plate was changed to one that had large bars of 0%, 30% and 70% screen tone at a screen ruling of 85 lines per inch. Press runs were made with total copies of 2000, 20,000 and 40,000 copies [72].
2.3.3.2 The Dagbladet [43]
Dagbladet press is a web-fed, 4-colour offset press with a maximum speed of 60,000 copies per hour. The aim of the experiment was to compare the lint results from 27 different newsprints and to identify laboratory methods that could successfully predict the linting tendency of newsprints [19]. However, the specification of the printing press was not described, including the web configuration, and the ink and fountain solution used therefore it is quite hard to compare it with other full scale printing press trials that had been done before, e.g. Apollo, Hamada, Heidelberg GTO-52 printing presses.
The advantages of using a printing trial is to get a lint sample that is representative of that which the customers really get [2]. However, it is time consuming and the analysis of the samples require a great deal of care and attention [2, 17, 20].
2.3.4 Lint Measurement and Characterisation
There are a number of different approaches in the literature have been used to quantify lint accumulation. Lint has been removed from the press blanket with adhesive tape- “tape pulls” method and the fibres were then counted by image analysis [21, 42, 60]. However, for heavier deposits, image analysis was not used. Caliper or weight measurement [2, 17, 40, 45] were used instead.
The press blanket has been covered with molten wax to remove the lint. The lint particles were then separated from the wax using a suitable solvent [21, 60]. The lint was then analysed by Kajaani fibre length analyser [21, 60].
Another way of measuring lint was by cleaning the press blanket with a 5% isopropanol solution and a small brush. The lint collector is a tray which is held firmly against the stationary offset blanket area to be sampled. This tray is called Domtar lint collector [21, 60]. Once the samples were collected, lint was separated according to size by screening using a two-stage screening device [40]. It is constructed of commercial PVC pipe and fittings with spaces for one removable 150-mesh stainless steel in the upper position and one removable 400-mesh stainless steel in the lower position.
This device was filled with distilled water through the valve at the bottom to a level about two centimeters above the 150-mesh screen. The lint mixture to be analysed was poured int
o a blender and dispersed thoroughly before being poured into the top of the lint screening device. The larger lint material tended to be retained on the 150-mesh screen (about 110µm on a side), while some smaller materials are mechanically trapped in the weave of the 400-mesh screen. The large and small lint weights were determined by weighing the screens before and after the filtering process. Not all material that passes through the 150-mesh is retained by the 400-mesh screen. The ink pigment and smaller paper derived material that passed through the 400-mesh are ignored.
For a given press and paper, it was found that there was a linear relationship between the quantities of large lint and fine lint collected on the two screens [60]. However, the large lint content of lint from commercial presses was found to vary significantly, ranging from less than 10% to over 70% of the total lint mass. This was due to differences in papers and presses being used by the printers. Total lint mass and large lint mass percentage are two criteria that were used to characterize lint from both commercial and laboratory press trials [60]. A linear relationship was also found between lint determined by weighing tape pulls and the Domtar screening method [40]. It was also found that the Domtar screening method is very difficult because the two screens are quite heavy, therefore it is difficult to accurately measure the change in weight from lint accumulation on the screen [40].
Printing trials combined with the image analysis and lint weight measurement are the method that is considered to be the best option for lint measurement at the moment [2, 17, 20, 45].
3.0 Experimental Method
In this chapter, all of the equipment used in this thesis will be discussed, together with the materials tested, and the methods and the procedures used. This chapter will be divided into three different sections, laboratory scale experiments, press trials, and ink rheology. The materials, equipment and method used will be explained in details for each.
3.0.1. Paper Tested
There are eight different batches, i.e. batch A, B, C, D, E, F, G, H that were used for all experiments mentioned and discussed in this thesis. Batches A, B, and C were the ones used in the Heidelberg GTO-52 experiments. Batch A was used for a preliminary experiment in year 2004 and therefore no results are reported on this. Batches B and C were the ones that were used to do the test of variability within and among batches. Batches B and C were also the ones used to do the testing of any other printing variable effects on linting. Batches D, E and F were the ones used for the first, second and third Man-Roland Uniset Trial (Appendix E, F, G). Batch G was used for Man-Roland Geoman trial (Chapter 5.2.8). The Deltack experiments used Norstar batch H (Chapter 5.2.4).
There were three different types of paper used in the Man-Roland Uniset trial. The first grade used for the study is named Norstar and is a 52 gsm improved newsprint grade manufactured on PM2 (Paper Machine 2) at Boyer. The furnish is 67 % TMP radiata pine, 28 % chemi-mechanical eucalypt (cold caustic soda) and a filler component of 5 % calcined clay (supplied by Imerys as Alphatex). The second type was 45 gsm Nornews, which consists of 25% cold caustic soda pulp, 20% recycled fibre and 5% kraft pulp and the rest is radiate pine TMP, with no added filler component. Nornews is made by Norkse-Skog Boyer on PM 3. This paper has a brightness of 74. The third type of paper was 45 gsm Nornews made in Golbey, France, which has 60-75% of recycled fibre and the rest is TMP. To differentiate this from the Nornews made in Boyer, this will be called Golbey for the rest of the thesis.
3.0.2 Inks and Fountain Solutions Used
Black and cyan inks with different tacks were used. More information on the inks is presented in Table 3. 1. The tacks listed here are those supplied by the manufacturer of the ink. For some of these inks, the tack values were also measured with an inkometer at APPI, for details of the method used see 3.4.1. The only web-fed ink used in this thesis is the black, tack 13.5 which is manufactured by Colortron. The others are sheet-fed inks. Coldset web-fed ink has different composition than sheet-fed ink. Sheet-fed ink has a higher composition of alkyd resin as well as higher composition in rosin esters while the coldset web-fed ink has a higher mineral oils component. Sheet-fed ink costs up to three times as much as the coldset web-fed news-ink.
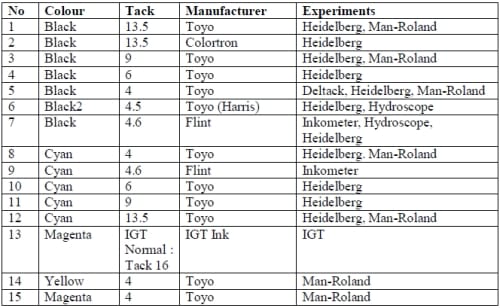
Table 3. 1. Inks used for all of the experiments
Fountain solutions that were used in this thesis were Eurofount H and Alcofix manufactured by DS Chemport. These are acid fountain solutions. Eurofount H is designed for web-fed applications, while Alcofix is for sheet-fed applications.
3.0.3 Plates Used
A number of different printing plates were used with different plate materials and patterns. These are listed in Table 3. 2.
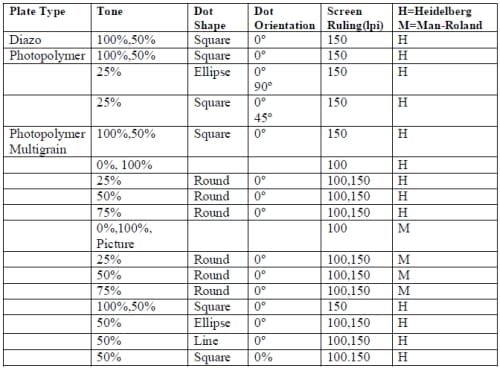
Table 3. 2. Plates used for all of the Man Roland Uniset and Heidelberg GTO-52 Trials
The images of the dot orientation and dot shape used are given in Table 5. 22. A screen ruling of 100 lines per inch means that there are 100 image area dots per inch in the direction of printing. Therefore a 150 lpi plate has a smaller image dot size compared with a 100 lpi plate.
3.1 Laboratory Scale Experiments
There were two laboratory scale experiments done to simulate commercial offset printing press. These were done on the Prüfbau Deltack and the IGT printability tester. The IGT printability tester was used to simulate offset printing with a given amount of ink, pressure, speed and then the print was examined to measure the area of fibres that had been picked from the surface. The Prüfbau Deltack also provides a laboratory scale simulation of the offset printing process. It can measure the amount of ink transferred as a function of printing variables, such as speed, nip pressure and ink. The Deltack is also used to measure the printing tack force that develops at the exit of the printing nip.
3.1.1 Prüfbau Deltack
3.1.1.1 Equipment
The Prüfbau Deltack is illustrated in Figure 3. 1. It consists of an inking unit and a printing unit. The inking unit comprises of an ink roller and four inking stations. The printing unit has two measuring units, 1 and 2, and printing cylinders A and B. Attached to the measuring unit are sample carriers and pins that are equipped with force transducers with force ranges of 5 to 6 N for the high force transducer and 0.1 to 1.7 N for the low force transducer. Printing pressure and speed are specified for each of experiment.
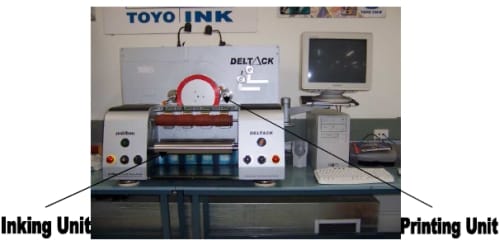
Figure 3. 1. Prüfbau Deltack Equipment
3.1.1.2 Method
Paper was cut into strips of 285mm by 55mm. The ends of the samples were reinforced with adhesive tape before punching it with a hole-puncher. Each strip was then transferred into the sample carrier of the appropriate measuring unit. Ink was applied with a standard ink distributor on the inking unit for 1 minute before inking the printing forme for 30 seconds. The printing forme was then transferred to the printing unit and then samples were printed.
In order to measure the quantity of ink transferred from the printing forme to paper, the ink forme was weighed before and after inking. The weight difference between the ink weight on the printing forme before and after the printing process is the amount of ink transferred to the paper. The forme, printing units, and ink roller were cleaned with heptane at the completion of each set of four runs.
Printing trials were done at different s
peeds, printing forces, ink tacks, and ink volumes. Different types of forme were also used in order to see the effect of different materials, i.e. metal, poly-urethane and rubber. 45 gsm Nornews, 52 gsm Norstar and sheet-fed ink coldset Toyo black tack 4 were used. All experiments were done in a controlled temperature at 23 ± 0.1 °C and relative humidity of 50 ± 0.1%.
3.1.2 IGT Printability Tester
The IGT measurements were performed by Sonya Rand as part of her Master thesis work [8]. The method developed is given here for the readers convenience as her picking results are used later in this thesis for comparison with lint produced during full scale printing.
3.1.2.1 Materials
Six separate batches of Norstar were used for the IGT pick test experiments. The ink used for the experiments is given in Table 3. 1.
3.1.2.2 Equipment
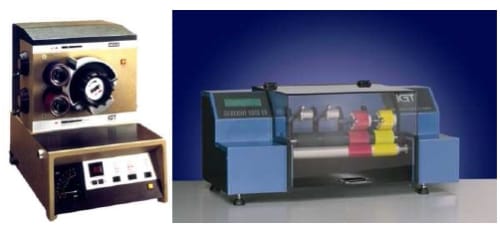
Figure 3. 2. IGT printability tester AIC2-5 printing unit [82] and IGT printability tester AIC2-5 inking unit. [73].
3.1.2.2 Method
The IGT Printability Tester AIC2-5 Series 414.Z was used to do laboratory printing experiments, as it can be used as a preliminary indicator of linting. The IGT consists of separate printing and inking units which are shown in Figure 3. 2. A Pick test [8] was performed on each of the samples as described in the literature review.
The printing parameters were chosen so that the unit produced excess force when run on the surface of the paper so that enough lint was removed from a piece of paper to be readily analysed. The conditions chosen by Sonya Rand were:
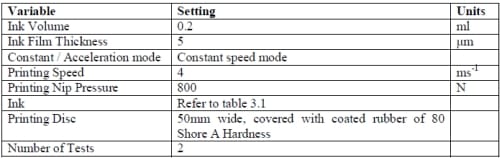
Table 3. 3. Variables for setup of IGT Printability Tester
Printing nip pressure was measured using pressure sensitive tape Fuji Prescale Pressure. The method is discussed in more detail in chapter 3.2.3.4. All experiments were conducted in the constant printing speed mode [8]. It was noticed in the printed IGT paper samples that there was a degree of acceleration, even in this mode of operation, as the amount of lint removed on the sample increased from start to end of printing. This was apparent in all samples and can clearly be seen in Figure 3. 3
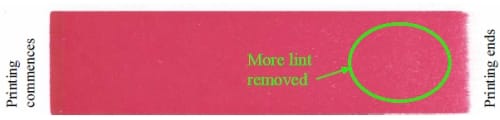
Figure 3. 3 More lint removed in latter part of IGT Printed samples, despite constant printing speed [8].
The printed sheets were fully dried before further analysis was performed. A Hewlett Packard Scanjet 6300C Flatbed scanner was used to capture the images. The glass surface of the scanner was thoroughly cleaned with a dust free wipe to ensure that the images were free from contamination. A 1: 1 image was captured (sized 4.8 x 10 cm) at the bottom of the printed image as this represented the area of most lint removal. This is shown in Figure 3. 4.
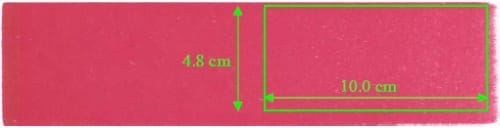
Figure 3. 4. Image captured of printed IGT sample [8]
The images were then analysed by image analysis software, Image Pro Plus 4.5, to determine the size distribution of non- printed areas.
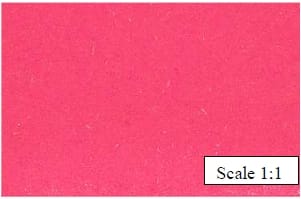
Figure 3. 5. IGT Test Print
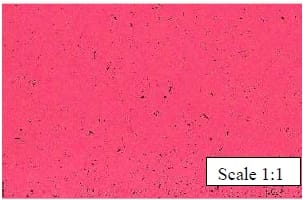
Figure 3. 6. Image analysis quantification
Figure 3. 5 shows the original image. Figure 3.6 shows the areas that have been darkened and then counted as lint by the image analysis software.
The settings used in Image Pro were Hue : maximum (255), Saturation (94), Intensity : maximum (255) [8]. The particle classes used to classify the lint particle are shown in Table 4. 11.
3.2 Printing Press Trials
Printing press trials were considered to be more appropriate to measure linting tendency. A smaller sheet-fed print press, Heidelberg GTO-52 and a larger scale web-fed Man- Roland Uniset printing press were run to investigate the effect of printing parameters on linting.
One Man-Roland Geoman trial was also done to compare the lint from the IGT laboratory pick test with that of a commercial printing press. There was no control over the printing screen or conditions since the sampling was done after the printing press finished its daily newspaper printing. The Man-Roland Geoman printing tower at which the samples were from was similar to the third printing unit of Man-Roland Uniset (Figure 3. 14). The order of printing in the four colour printing unit of the Man-Roland Geoman is cyan, magenta, yellow and black. Chapter 5.2.8 can be referred to for more details regarding the effect of four-colour printing in the Man-Roland Geoman on linting and how the lint removed on this press compared with that removed by the IGT laboratory pick test.
3.2.1 Heidelberg GTO-52
3.2.1.1 Equipment
The Heidelberg GTO-52 located in Norske-Skog Research and Development, Boyer is a sheet-fed single-colour cold-set printing press with a maximum speed of 8000 copies per hour, with a maximum paper size of A3. Several other print parameters can also be adjusted in this machine, i.e. speed, impression pressure setting, and water and ink swipe rate. Ink ducts opening can also be adjusted to obtain the required print density. The takeoff angle of the machine was found to be 70º. The machine can only print one side at a time. A picture of the machine and a schematic diagram of the machine are shown in Figure 3. 7.
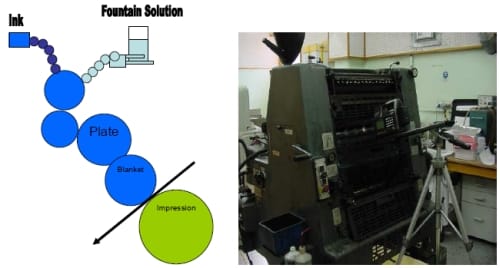
Figure 3. 7. Heidelberg GTO-52 Sheet-fed Printing Press
3.2.1.2 Materials
The paper used for all of these experiments was Norstar. For each paper type and batch, the top or bottom side of the paper was printed separately. The inks used in these experiments are listed in Table 3. 1. The plates used were manufactured by Tadpac Print in Hobart. Several printing plates, i.e. a standard test plate consist of solid and 50% tone, 25%, 50% and 75% tones with different screen rulings of 100 lpi and 150lpi were used. Several plate materials were also tested. The details are given in Table 3. 2.
3.2.1.3 Method
The number of copies printed ranged from 1000 to 7000. The impression (nip) pressure ranged from 0.05 to 2 on the press. These settings are equivalent to a pressure in the range of 3 to 12 MPa depending on the blanket that is used (Please refer to Figure 5. 36). Ink and fountain solution swipe speeds were set at dial settings of 7 and 9, respectively to get print density of 1, except for one set of experiments where the ink and fountain solution swipe speeds were set to 7 and 7, respectively. The fountain solutions used were either 2% Alcofix or 5% Eurofount H manufactured by DS Chemport. The standard conditions used for Heidelberg GTO-52 are shown in Table 3. 4. For each group of experiments which were meant to test a specific parameter, only that parameter was changed and the other parameters were kept at standard conditions.
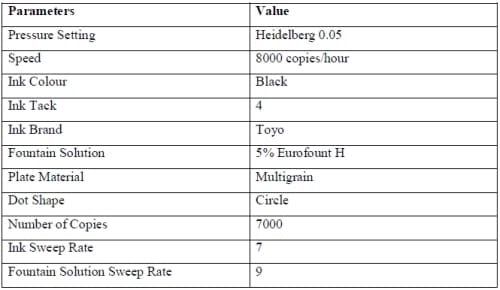
Table 3. 4. Standard Conditions of Heidelberg Trial
Before starting a trial, speed, nip pressure, ink and water swipe speeds, and the paper size setting were adjusted. A four digit balance was then calibrated and prepared. The balance was used to weigh blank paper, wet printed copies and also dry printed copies. Each printing trial was started with a target of print density of 1.
Fountain solution consumption volume and paper weight were noted every 500 copies. The
blank paper weight was calculated from the paper grammage and sheet size. 500 copies of printed paper were also weighed. The weight difference between 500 copies of printed paper and the blank paper was the weight of the process printing ink, i.e. ink and fountain solution emulsified in it that has been printed on each batch. During the printing trial, the solid print density was always targeted to be 1.0. This was done by measuring the solid print density (see section 3.2.3.3) across the width of the sheet and adjusting the ink duct opening if the print density deviated from 1.0. This was done every 500 copies.
At the end of each run, 20 sheets of paper were run without ink and fountain solution to remove excess ink before lint was collected. After printing the desired number of copies, lint was collected using tape pulls and Domtar lint collector, followed by lint analysis. The lint collection and analysis/measurement methods are discussed in section 3.3.
The fountain solution was fed to the machine from a graduated measuring cylinder. Fountain solution usage was measured after every 500 copies by noting the level in the cylinder. However the exact percentage of fountain solution emulsified in the ink on the plate or on the paper could not be measured. This was because while the amount of fountain solution flows to the fountain solutions rollers could be measured from the cylinder, the ink flow to the ink rollers, from the ink reservoir can not be measured. The weight of ink added to the machine at the beginning of the experiment can be measured but not the weight at the end of the experiment as the ink must be partly removed with cloth and solvent. Therefore another way of measuring the degree of ink emulsification is required. Chapter 3.4 will explain the methods that were developed in more detail.
3.2.2 Man-Roland Uniset
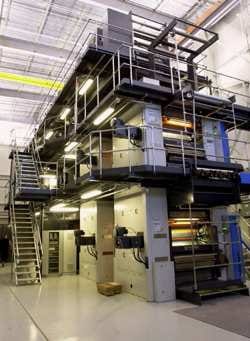
Figure 3. 8. Man-Roland Uniset Web-Fed Press
The Man-Roland Uniset press that was used for experiments in this thesis is located in Harris Print in Burnie, Tasmania. It is a 4-colour web-fed coldest offset lithography printing press. Its maximum speed is 30,000 copies per hour. The inks that were used in the trials are listed in table 3.1. They are all coldset offset lithography inks. The print trial parameters that were varied including printing speed, number of copies, as well as different plate parameters, such as printing tone, and screen ruling.
At the end of the run, i.e. when the desired number of copies had been printed, lint was collected from the printing blanket for lint measurement and analysis using the Domtar and Tape pull methods (see section 3.2.3.1).
There are three web-fed full commercial press trials that have been done on this Man- Roland Uniset press. Each of the trial will be explained in this chapter and the full details can be referred to in appendices E, F and G.
The Man-Roland Uniset at Harris Print has 5 printing units. Each unit has two pairs of printing couples. The press has six reel-stands so that different web arrangements can be achieved, such as arranging top and bottom side of the paper, and varying the printing nip take off angle. On the press, the reel stands are labelled 3, 4, 5, 6, 7, and 8. All odd numbered reel stands, i.e. reel stands 3, 5, and 7 run in the clockwise direction while even numbered reel stand, i.e. reel stand 4, 6, 8 runs in anticlockwise direction. This resulted in different paper side orientation, depending on whether the even or odd numbered reel stand was used.
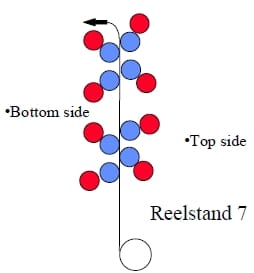
Figure 3. 9. Paper web runs clockwise for reel stand 4, 6 and 8, Bottom side of the paper is on the LHS of the printing machine
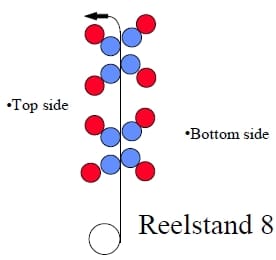
Figure 3. 10. Paper web runs anticlockwise for reel stand 3, 5 and 7. The bottom side of the paper is on the RHS of the printing machine
In odd numbered reel stands, the bottom side of the paper is located on the left hand side while in even numbered reel stands, the bottom side of the paper are located on the right hand side, as observed from the control room. Top/bottom side of the paper means the top/bottom side of the paper as it was produced on the paper machine.
The take-off angle is the angle between the paper web and the printing nip. The right hand printing cylinders are slightly higher than the left hand printing cylinder (see Figure 3. 10). This resulted in the right hand sides having a higher take-off angle compared with the ones in the left hand sides.
There are three printing units that were used in these trials. These were the first, second and third printing units. The first printing unit consists of two printing couples, i.e. top printing couple (blue) and bottom printing couple (red). A schematic diagram of the two print couples is shown in Figure 3. 11. Due to the web configuration, the top printing unit has 102º take off angle for its top side of the paper while the bottom side of the paper has 78º take off angle. The bottom printing couple bottom side of the paper has 153º take off angle while the top side of the paper has 27º take off angle (see Figure 3. 12). This unit was used to in all three trials.
This printing unit is normally be used to print two colours with the web running through both units. However for our experiments, the take off angles produced were due to the web leads that were selected and these were not the normal web leads used in standard printing on the press.
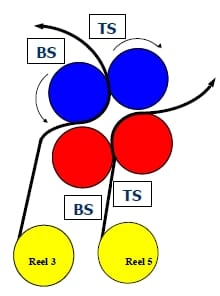
Figure 3. 11. First printing unit of Man Roland Press consist of Top (blue) and Bottom (red) Print Couple
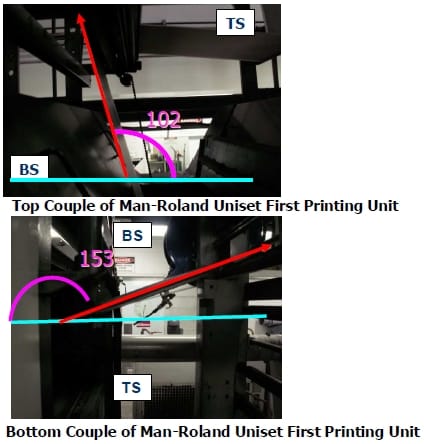
Figure 3. 12. – Top and bottom unit of Man-Roland Uniset with the take off angle accordingly. The red line shows the paper web and the blue line shows 0º take off angle.
The second printing unit consists of two printing couples as well. However, only one paper web ran through it, meaning that the paper was printed twice or four times (RHS of Figure 3. 13). This unit was used to investigate the effect of printing multiple colours (four-colour printing) and also the effect of fountain solution on linting (LHS of Figure 3. 13). The right hand side printing cylinders were positioned a little bit higher compared with those of the left hand side, therefore paper on the right hand side had a higher take off angle compared with the paper side on the left hand side. This unit was used to do experiment in the first (RHS of Figure 3. 13) and second printing trial (LHS of Figure 3. 13). This unit could be run from either the fourth or the fifth reel stand and so the paper side could be swapped as needed.
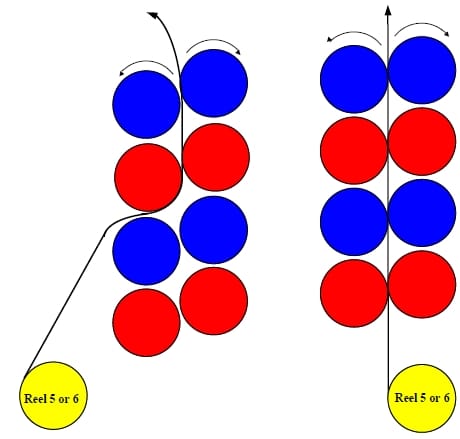
Figure 3. 13. Second Printing Unit of Man-Roland Press
The third printing unit consists of four printing couples. This unit was used to do 4-colour printing in the first printing trial. The order of printing was Magenta (M), cyan (C), yellow (Y) and black (K). Again, the printing cylinders on the right hand side had a slightly higher position compared with those on the left hand side. Therefore the take off angle of the right hand side of the paper side had a higher take off angle compared with the left hand side of the paper.
For both of the second and third printing units (see Figure 3. 13 and Figure 3. 14), when the odd-numbered reel stands were used, the T/S has higher take off angle (~105º) since T/S is on the right hand side compared with the B/S (~75º). The
situation was reversed when an even-numbered reel stand was used.
Figure 3. 14. Third Man-Roland Printing Unit.
3.2.2.1 First Man-Roland Printing Trial
3.2.2.1.1 Aim
To investigate the effect of paper type, paper orientation, paper side and the effect of first and subsequent printing units.
3.2.2.1.2 Web Configuration
There were two runs in the first printing trial, both with the first (Figure 3. 11) and third printing units (Figure 3. 14). The two printing units were used in order for us to investigate the difference between three types of papers. The only difference between web leads used for the runs was that the first run used reel stand 7 and the second run used reel stand 8 for the third printing unit. Therefore the take off angle and paper side orientation of the two runs were different on the third printing unit.
The second printing unit was used to print Nornews and Golbey, while the third printing unit printed Norstar. For details of these papers see section 3.0.
3.2.2.1.2.1 First Run First Trial Man-Roland Uniset
There were two paper webs run on the first run. Nornews from reel stand 5 ran through the second printing unit while Norstar from reel stand 7 ran through the third printing unit. However, both of them had the same take off angle since all the odd numbered reel stand ran in a clockwise direction.
4 colour printing was done on both printing units. The order was magenta (M), cyan (C), yellow (Y) and black (K). This is unusual, as normally the order of colours in the press is cyan, magenta, yellow and black. All of the inks used were Toyo inks with tack of around 4, regardless of the colour.
3.2.2.1.2.2 Second Run First Trial Man-Roland Uniset
The inks used were the same as the first run first trial Man-Roland Uniset. From Reel stand 5 Golbey ran through the second printing unit, while Norstar from reel stand 8 ran through the third printing unit. For the Golbey the T/S has higher take off angle (~105º) since T/S is on the right hand side compared with the B/S (~75º). This was identical to what was used in the first run and was done to compare the lint performance between three different type of the paper, i.e. Norstar and Nornews that had been done in the first run first trial (3.2.2.1.2.1). Therefore Golbey was run with reel stand 5 (odd reel stand), the same as the first run.
Reel stand 8 (even numbered reel stand) was running Norstar through the third printing unit. This was done to investigate the effect of take off angle. In the first run, reel stand 7 was used with the third printing unit. However, to examine the effect of take off angle, this time reel stand 8 was used, so that the bottom side of the paper has a higher take off angle (~105º) than that of the top side (~75º).
The printing plates image area patterns were 0%, 25%, 50%, 75%, solid and picture for all runs in the first trial. Each trial was run for 40,000 before stopping and measuring the lint accumulation using the Domtar and tape pulls.
3.2.2.2 Second Man-Roland Uniset Printing Trial (Refer to Appendix F for details)
3.2.2.2.1 Aim
To investigate the effect of two sidedness of the paper, the effect of ink tack, ink colour, take-off angle, screen ruling, printing speed and the number of copies on linting.
3.2.2.2.2 Web configuration
The first and second printing units were used for this trial. The first printing unit was used to look at the effect of ink tack, ink colour, the number of copies, and take off angle on linting. The second printing unit was used to look at the effect of water consumption on linting during printing.
3.2.2.2.2.1 First Printing unit-Second Man-Roland Trial
The paper web came from reel stand 3 and reel stand 5. Reel stand 3 fed the top couple of the first printing unit and reel stand 5 fed the bottom couple of the first printing unit. The paper web which came from either reel stands 3 or 5 had the bottom side of the paper at the left hand side, and the top side of the paper at the right hand side.
In The first printing run, the top printing couple was run with black ink of tack 13.5 while the bottom printing couple was run with black ink of tack 9. On the second run to the fifth runs, black ink of tack 6 was run on the top printing couple while the black tack 4 ink was run on the bottom printing couple. Please note the difference of the take off angle for the top and bottom printing couple, as was discussed in Figure 3. 12.
There are 6 runs were done in the first printing unit. The first and second runs were done to investigate the effect of black ink tack, i.e. tack 4, 6, 9, and 13.5. The second, third, and fourth printed different number of copies to be able to investigate the effect of the number of copies to linting. In the fifth run, the speed was half the ‘usual’ speed (25,000 copies an hour), i.e. it was run at 12,500 copies per hour to investigate the effect of speed on linting. Lastly the sixth run used cyan ink tack 4 and 6 for comparison with the second run which printed in black tack 4 and 6. The first, second, third, fourth and sixth runs were all run at 25,000 copies per hour, while the fifth run was run at a speed of 12,500 copies per hour. The first run used black tack 9 and 13.5 inks, the second, third, fourth, fifth runs used black tack 4 and 6 inks, while the sixth run used cyan tack 4 and 13.5. The first, second, and sixth runs printed 23,000 copies in total. The third run printed 7000 copies, while the fourth and fifth run printed 14,000 copies in total. For details please refer to Appendix F.
3.2.2.2.2.2 Second Printing Unit Second Man-Roland Trial
In the second printing unit, only one paper web ran through both of the bottom and top printing couple (LHS of Figure 3. 13) from reel stand 7. The effect of water consumption to linting was investigated. A full paper web was run through the Man-Roland Uniset (810 mm). Two different water settings were applied across the paper web. A higher water setting was applied in the LHS of the web and a lower water setting was applied in the LHS of the web. Both the LHS and the RHS of the web printed the same pattern from the printing plate which had 150 lines per inch at 0%, 25%, 50%, and 100% printing tone across the web. More details of the experiments can be referred to Appendix F.
3.2.2.2.3 Third Man-Roland Uniset Trial
3.2.2.2.3.1 Aims
The third trial was run to further investigate on the effect of ink tack, printing tone and take off angle. This trial also investigated the effect of printing nip pressure and blanket age to linting. All of the runs were done with the first printing unit.
3.2.2.2.3.2 Web Configuration
In this trial, only the first printing unit, consisting of the top and bottom printing couple, were used. In this trial, black inks of tack 4, 9, and 13.5 were used. Both top and bottom couples were run with the same ink.
These three runs ( Run 1, 2, 3) were done to investigate the effect of different ink tack, take off angle and printing tone with the same paper orientation, i.e. bottom side of the paper on the left hand side for both paper web at the top and bottom printing couple.
In Run 4, a pair of new printing blankets was used in the bottom print couple. This was done to investigate the effect of printing nip pressure and blanket age to linting. This run was done with Toyo black ink tack 4 in the bottom print couple only while there was no paper run through the top print couple.
In the third Man-Roland Uniset Trial, all runs were done with 25,000 copies per hour speed and 25,000 copies printed for each run. The plate consisted of different screen tones starting from 0%, 25%, 50%, 75%, solid and picture.
3.2.3 Linting Press Collections and Measurements</p >
3.2.3.1 Lint Collections
There are two lint collection methods that were used in the work in this thesis. These are the tape pull and Domtar lint collection method.
3.2.1.3.1 Tape Pull Method
At the end of printing trials, Scotch tape with an area of 68 cm2 was used to collect lint by sticking it onto the blanket with a roller (Figure 3. 15, Figure 3. 16). The weight of the tape before and after lint collection was noted so that the lint weight per unit area of blanket could be calculated. Previous studies by Banham [74] and Mey [40] have shown that the measurements were repeatable within 5-10%. The repeatability of the measurements was also examined in chapter 4.3. Lint weight is calculated from the following formula,
Lint weight on 68 cm2 area of tape = (Final-Initial) weight of the tape
Lint weight (gsm) = Lint weight on 68 cm2 area of tape x 147
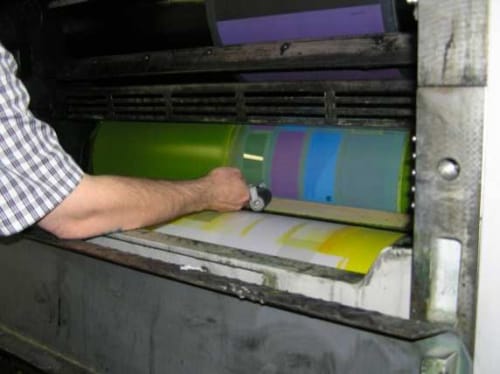
Figure 3. 15. Application of Tape to the Blanket
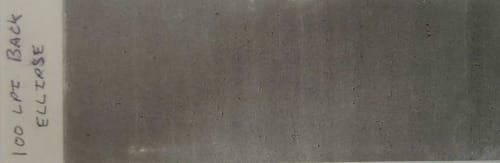
Figure 3. 16. Tape Pulls with Attached Ink and Lint
3.2.3.1.2 Domtar Lint Collector
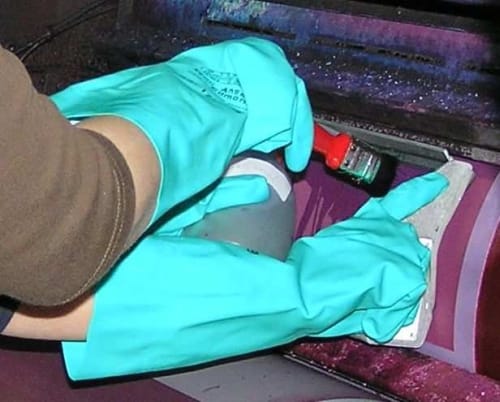
Figure 3. 17. Image of Domtar Frame and Lint Collection Method
Another way to collect lint from the printing blanket is by removing lint from the printing blanket or printing plate with a brush and 5% isopropanol solution. The sampling method involved wetting the blanket by using a squeeze bottle with the isopropanol solution and then brushing vigorously. The isopropanol solution and lint was then captured in a Domtar frame. The frame removed lint from an area of 30 x 10 cm. Different frames were fabricated to match the radius of curvature of each of the Heidelberg and Man- Roland blanket cylinders.
The samples volume collected was adjusted first to either 100 or 200 mL. 50% by volume (50 or 100mL) of the sample was filtered through previously weighed glass filter paper under vacuum to collect the lint for weighing. The set up used is shown in Figure 3. 18. The glass filter was put in the oven for 30 minutes to evaporate the water in it and then weighed. Several images of filter papers after drying are shown in Figure 3. 20. The difference between the glass filter paper before and after the filtering process is the lint weight. This was converted to ling grams/m2 on the blanket using the following formula.
Lint weight in 0.3 m2 area of blanket = Lint weight of 50% volume of the sample x 2
Lint weight (gsm) = Lint weight of the sample * 3.33
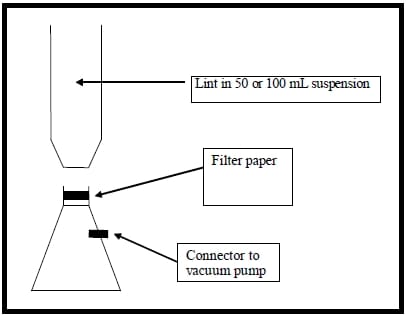
Figure 3. 18. Lint filtering system for Weight analysis.
Glass filter paper was proven not to loose weight when it was heated up to 105°C for 30 minutes. Glass filter paper supplied by DFS has a pore size of 0.7µm. Originally filtering was done with a mixed cellulose-esther filter – 0.45 µm pore size. This was unsuccessful as it gave inconsistent results. The reason for this was because mixed-cellulose ester lost weight when it was heated in the oven even though the specification sheet stated that the glass transition temperature was 140°C. The reason for this weight loss is not known and is still under investigation. More details of the results of the weight stability tests of the glass filter and the mixed cellulose ester will be discussed in chapter 4.4. The lint weight results from the Domtar method is always lower compared with those of tape pulls method and this will be discussed in more details in chapter 4.5.
A previous study by Kevin Mey [40] showed that the Domtar method repeatability was within 15%.
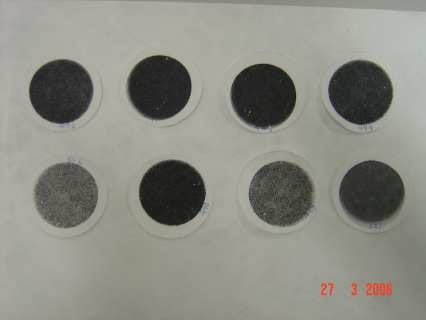
Figure 3. 19. Lint After Being Filtered for Weight Analysis
3.2.3.2 Image Analysis
In addition to the 50% that was filtered for weight analysis, 1% by volume was also filtered with mixed-cellulose ester filter to be analysed by image analysis (see Figure 3. 20). The reason why mixed-cellulose ester was picked for the image analysis was because it gave better contrast so that it was easier to automatically set the threshold of image analysis.
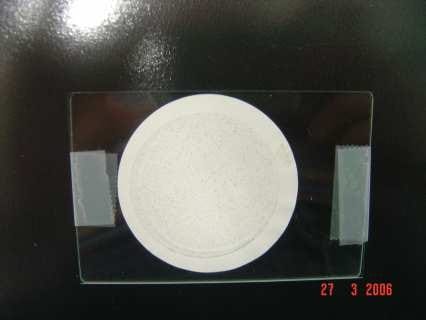
Figure 3. 20. Lint Slides for Image Analysis
20 images were taken using a BTX-60 light microscope from the mixed cellulose filter slide, which has filtered 1% by volume of the Domtar sample. This is shown in Figure 3. 21. 20 samples were found to be statistically adequate compared with 40 or 80 images. That is the accuracy of the measurement was not greatly improved by measuring 40 or 80 images in comparison to 20 images. This will be discussed in chapter 4.5
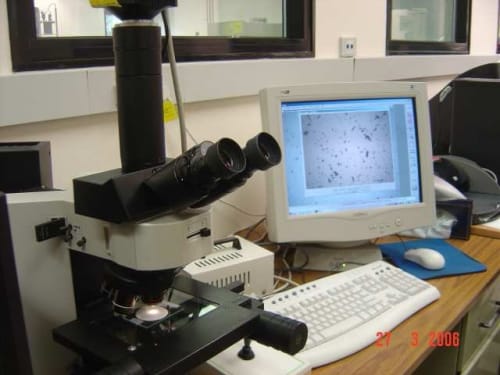
Figure 3. 21. BTX-60 Light Microscope
Image Pro 4.5 image analysis software was used to sort lint particles according to either area or length. The software has the limitation that it can only sort particles into a maximum of 16 classes. A macro was written to enable the operator to process multiple images tied together as well as setting an automatic threshold.
Each of the individual lint particle measurements was exported to an Excel spreadsheet. The average results were also calculated by the macro and exported to an Excel spreadsheet.
The details of the method, including the accuracy and reproducibility of method, are discussed in chapter 4.6. There is a relationship between lint area and lint weight and this will be presented in chapter 4.5
3.2.3.3 Gretag D-186 Densitometer
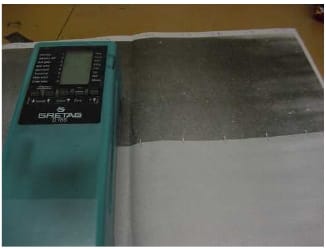
Figure 3. 22. Image of Densitometer Gretag D-186
In order to measure the print density, a Gretag densitometer was used, shown in Figure 3. 22. All of the print trials were run to attain a target print density of 1.0 in the solid area of the print. The Gretag Densitometer was calibrated each time before being used by putting it on top of the unprinted paper and setting it to zero. Before doing this it was also necessary to set the printing colour, i.e. cyan, magenta, yellow or black.
3.2.3.4 Nip Pressure Measurement
3.2.3.4.1 Material
The blanket-blanket nip pressure was measured using pressure sensitive tape-Fuji Prescale film. It was stuck in between blanket to blanket nip. It has two layers of film with bubbles containing chemical in between those two film layers. Pressure in printing nip squeezed the bubble in between the films. The higher the colour intensity is, the higher the nip pressure since more bubbles have been broken by the printing nip.
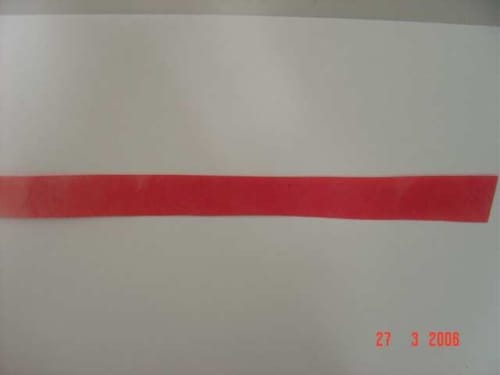
Figure 3. 23. Image of the Fuji sensitive tape
3.2.3.4.2 Equipment
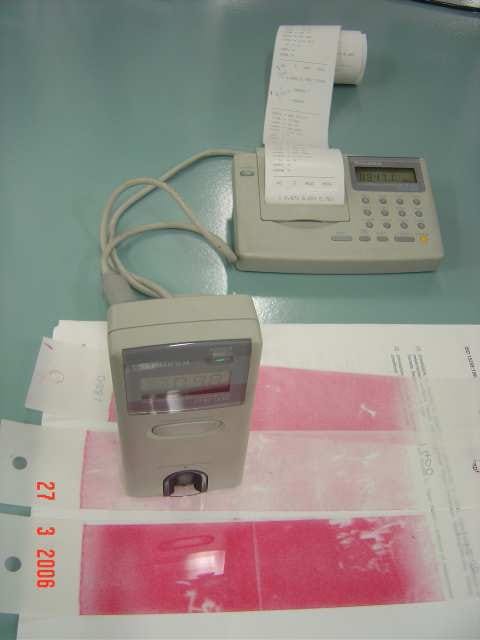
Figure 3. 24. Image of pressure reader
A pressure reader is used to read the colour intensity and it is automated to convert the colour intensity level into nip pressure. This equipment used the calibration curve between colour intensity and nip pressure supplied by the manufacturer.
3.2.3.4.3 Method
Printing nip pressure was measured using pressure sensitive tape Fuji Prescale F
ilm Two- Sheet Type for Low Pressure (2.5 – 10 MPa). This was done by sticking the pressure sensitive tape to the blanket and then running the press for a minute. A minute was chosen to give adequate time for the pressure sensitive bubbles to react to the pressure in the nip. However the time required to do the measurement is not fixed. It is dependent on the roller geometry and the roller speed. The optimum time is found by running tape in the nip until the pressure reading does not change when the time increased. This is unique for each individual piece of equipment. While the Heidelberg GTO-52 and Man-Roland Uniset require 1 minute for each measurement, Deltack (Chapter 3.1.1) requires 5 minutes to reach a constant pressure reading. The manufacturer gives about 20% reading accuracy of this method in the manual.
3.2.3.4 Temperature Measurements
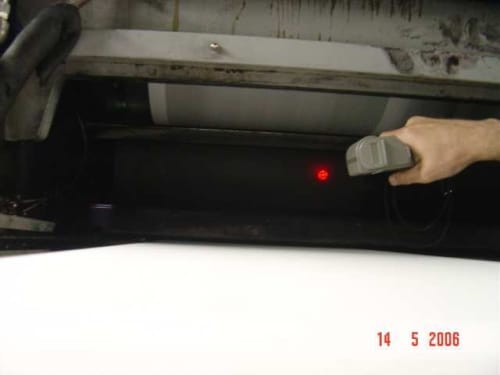
Figure 3. 25. Handheld Laser Thermometer
Non-contact temperature measurement was done using an infrared thermometer-“Minolta Land Cyclops Mini Laser”. This infrared thermometer works within -10°C to 300°C and is based on an emissivity setting of 0.95. Sampling time is approximately 1 second. It can record the maximum and minimum temperature during sampling time.
Infrared radiation is emitted from the laser thermometer onto the surface of the object, which is called a spot. The surface will emit infrared radiation back to the thermocouple, from which the temperature can be read. Another thing that needs to be satisfied is that measurement area has to be bigger than the spot size. It is recommended by the manufacturer that the measurement area should be around 1.5 times of the spot size. The ratio of the spot size to the distance between the instrument and the measurement surface should be 1:7.
3.3 Rheology Measurements
The offset lithography printing process involves ink, fountain solution, plate and paper. Ink tack, viscosity and the level of emulsification of fountain solution in ink are very important factors to be investigated. During the printing process, ‘process ink’ can have different tack or viscosity due to the effect of printing speed, the level of emulsification of fountain solution as well as shear rate in printing nip. Therefore, all of these parameters are required to be better understood in order to understand the wider picture of what really occurs during offset-lithography printing.
3.3.1 Thwing Albert Inkometer
Tack is defined in this instrument as the torque, expressed as Newton-metre required to split an ink film in a specified nip configuration. The inkometer consists of a bath system with a thermostat (1) that circulates water to control the temperature of the machine and a measuring unit with three rollers (2), a fixed brass roller, a larger rubber roller and a smaller rubber roller. The standard test mass of ink was 1.67 grams, which was supplied from a specially designed pipette.
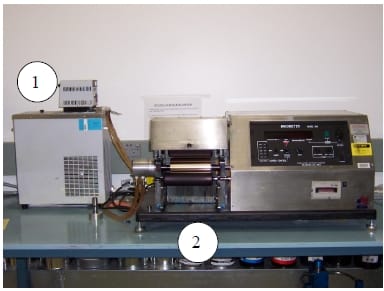
Figure 3. 26. Thwing Albert Inkometer
To operate the instrument, it was first warmed up for 10 minutes before the test allowing the temperature of the rollers to reach 32.2°C, after which the temperature was controlled by the cooling unit. The unit was then calibrated by setting the speed to the desired value and then re-setting the tack value to be zero and the inkometer. The unit was then stopped and ink in the pipette was then transferred to the bottom rubber roller. Roller speed was then set to be 800 rpm, which was the standard speed used for all the tests presented here. Ink tack reading was then taken after 1 minute.
The amount of ink and the test speed were chosen according to the standard test method supplied by the manufacture. However, speeds ranging from 150 to 2000 rpm are available. Ink weight can also be varied from approximately 0.5 gram to 3.2 grams. The maximum ink weight must be chosen to make sure that ink does not splash at the speed selected. If ink starts to splash, it will loose, changing the measured tack value.
After each test, the rollers must be thoroughly cleaned. This was done by checking if the tack was back to zero after cleaning had been done.
Tack is dependent on roller speed, ink weight/ ink thickness on rollers. Therefore, speed, temperature and ink weight need to be specified together with the tack value. More explanation and discussion on the effect of ink film thickness on ink tack can be found in chapter 5.2.4.1, 5.2.4.8.
3.3.2 Hydroscope
The offset lithographic printing involves ink and fountain solution emulsifying on the plate during the printing process. A plate consists of image and non-image areas. Fountain solution is transferred to the non-image area while ‘process ink’ is transferred to the image area. Process ink in this case is ink emulsified with water. The degree of emulsification has been shown to affect tack of the inks. The Hydroscope is an instrument that measure comparative ink tack in relation to the amount of water emulsified in an ink. Each ink has different tack behaviour with degree of emulsification. This is something that will be discussed more in Chapter 5.
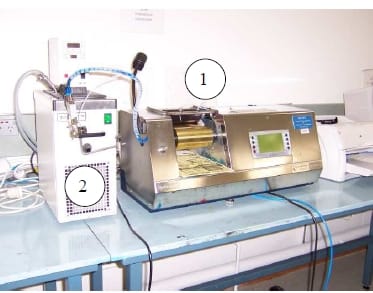
Figure 3. 27. Hydroscope
The Hydroscope is manufactured by Testprint BV. The ink distribution system consists of two brass rollers and one smaller rubber roller. The unit marked 2 is a temperature controlled water bath used to keep the temperature of the brass rollers constant. The unit measures relative ink tack from the displacement of the rubber covered roller that is produced by the splitting ink film. A fountain-solution ink emulsion is produced by dripping fountain solution into the nip between the two brass rollers indicated by (1) in Figure 3. 27. Roller speed (m/min), fountain solution addition rate (mL/min) and ink weight can be varied. The standard test was done at 40m/min and a solution of 5% fountain concentrate was delivered at a rate of 1.3mL/min with 10 grams of ink spread on the rollers. The fountain solution tested was Eurofount H. While the ink was run in the roller at the specific speed, fountain solution was titrated until the ink became saturated. Saturated ink can be noticed when there was a free water flow in the nip between the brass rollers. To make sure that the ink was saturated, titration was only stopped 60 seconds after the visually observed saturation point.
Tack decreased when fountain solution was added, reaching at the minimum at saturation point. Once the titration was stopped, tack recovery was observed. Finally, the measured tack reached the original tack level observed before fountain solution addition was commenced. Once the original tack level was reached, the test was then stopped.
3.3.3 Porepoise P-9 Capillary Rheometer
3.3.3.1 Equipment
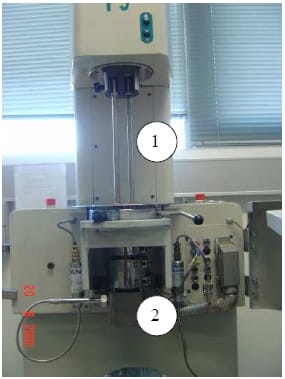
Figure 3. 28. Porepoise Capillary Rheometer
Ink tack is also affected by the shear rate in the printing nip. The Porepoise Capillary Rheometer in Figure 3. 28 is an instrument that is able to apply high shear rate to inks to find the shear viscosity. This instrument consists of pistons (1), a barrel (2) and a computer to control the instrument. There are two pistons in this equipment. The right piston is used for the error discrepancy calculation.
Each piston fits in the ram housing enclosed behind metal panels, and is driven by a ram, driven by a screw attached to the top of the ram, which is powered by an electric stepper motor. Up and down buttons are provided to drive the piston during loading and cleaning.
The barrel has a nitride-hardened bore equipped with
a pressure transducer port and a die location and retention system. Pressure developed during the test is measured by the pressure transducer.
This equipment can measure apparent viscosity at apparent shear rates up to approximately 2×10-5 s-1. The exact maximum shear rate attainable depends on the sample tested.
3.3.3.2 Method
Upon starting, computer and the Porepoise were switched on. A 0.05 mm die and 10,000 psi pressure transducer were fitted. The rams were sent to the top-stop and transducers were zeroed. All the parameters were then specified in the software, i.e. choosing the transducer, die, temperature, shear rate sequence and stages that will be tested on the samples. An ink sample was then loaded into both of the bores and the pistons were then run down to make contact with the sample.
A pre-compression stage was set to compact the sample and to remove any air trapped in the sample during loading. The test was then run under shear rate sequence and stages that were chosen and set in the software previously. This equipment is a form of capillary viscometer. For each shear rate, apparent shear viscosity was calculated, using the model that can be chosen in the built-in software, from the capillary diameter and the measured pressure.
3.3.4 Ink Emulsification Measurement
3.3.4.1 FTIR
It is important to know the exact level of emulsification of ‘process ink’ applied to the paper during offset lithography printing. Norske-Skog had previously used an FTIR (Fourier Transform Infra-Red) Bruker Equinox IFS5 with mercury-cadmium-telluride detector system. The sampling accessory used was a ‘Specac Golden Gate’ diamond. This set up was used to quantify how much water was emulsified in the ink during several printing runs in 2003 [75]. Samples from the printing plate were carefully collected during each run. FTIR method allows degree of water emulsification in ink to be determined. This method was also employed in several samples from the work on this thesis. This instrument is shown in Figure 3. 29.
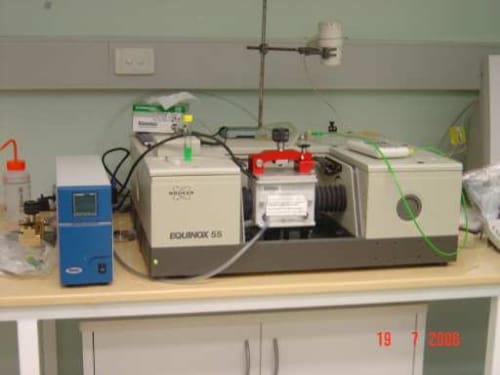
Figure 3. 29.Bruker Equinox
To use the instrument, it is necessary to construct calibration standards. These were blank ink, i.e. ink from the can and not emulsified at all, and several ink samples emulsified to 5%, 10%, 20% fountain solution using the Hydroscope. All of these samples were run through the FTIR to obtain a calibration curve of water concentration in ink versus water peak height in the FTIR spectra. Water has absorption bands mainly centred at 1640 and 3400 cm-1.
Once the sample run through FTIR, the area under the peak is then interpolated to find the corresponding level of water emulsion. However, this method is yet to be proven for quantitative measurement, although it is good enough for qualitative measurement. Therefore as a trial, some quantitative measurements were attempted.
3.3.4.2 Waterproof Paper Printing
Another attempt to measure water in ink concentration, other than using FTIR, was made. Heidelberg GTO-52 was used to run this experiment (please refer to 3.2.1). An A4 plate with 100% solid was used. The reason for using 100% solid on the plate is to minimize the free-water film on the non-image area. The idea was to print on to a waterproof paper and to measure the weight of the paper before and after drying. Tyvek 54 gsm waterless paper, supplied by Paperpoint in South Melbourne, was used for this purpose. This is an extremely high tear strength, waterproof material made from synthetic spun-bonded polyolefin fibers. Tyvek was chosen because after 105 °C and 30 minutes in the oven, it only loses 0.001 % of its weight. Images of unprinted and printed Tyvek paper are shown in Figure 3. 30.
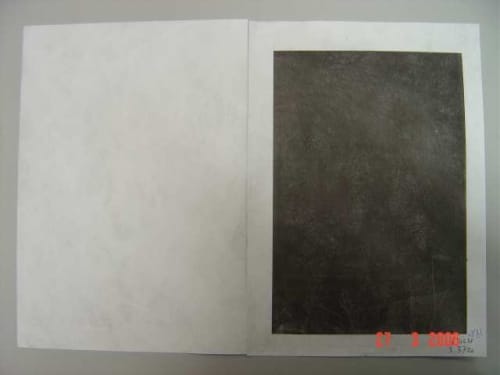
Figure 3. 30. Image of blank and printed Tyvek
To perform these measurements, first a thousand normal prints were done to adjust the press to get the print density close to one. Then ten sheets of Tyvek paper were weighed individually before printing. One sheet was then put in every batch of 100 sheets of 52 gsm Norstar. Each Tyvek sheet was then weighed directly after it had been printed. The difference between the weight before and after printing was equal to the weight of ink and water on the Tyvek paper.
The printed Tyvek papers were then put in the oven for 30 minutes to evaporate the water. Each sheet of the paper was then weighed again after 30 minutes. The weight difference of the dried printed paper and blank paper is the weight of ink (Wi). The weight difference of the printed paper and blank paper is the weight of the emulsified ink, i.e. the weight of the ink, volatile component and fountain solution (We). The fraction of the volatile component in the ink was averaged from the TGA experiment (Equation 2. 10) and is called fv.

3.3.4.3 Thermo Gravimetric Analysis (TGA)
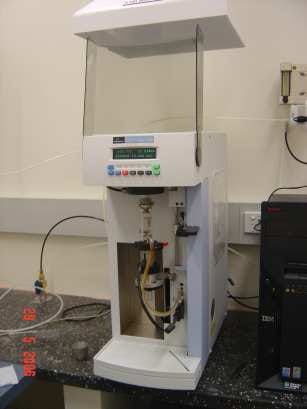
Figure 3. 31. TGA
It was realised that another method was required to find the fountain solution content in the process ink particularly for work on the web-fed Man Roland press where printing a single sheet was not possible. Thermo Gravimetric Analysis (TGA) was examined as a potential method. The Thermo Gravimetric Analyser that was used was a Pyris 1 from Perkin-Elmer. The principle behind TGA is very simple. A sample is put on the sensitive balance and the change in weight measured as the sample dries. The furnace temperature and nitrogen gas flow can be varied. It was chosen to increase the temperature from 25°C to 105°C with a temperature increase rate of 10°C/minute and then hold the temperature at 105°C for 30 minutes. The reduction in weight of the sample is then measured as the temperature is increased. This reduction in weight comes from the evaporation of both the water as well as volatiles in the ink. A minimum weight of 20 µg is advisable. It is good to have the same starting weight for all samples so that the results are comparable.
Pure ink was also processed in exactly the same way as the process ink to provide a blank sample. The decrease of process ink weight subtracted by the amount of evaporation found from the pure ink experiment gave the fountain solution content in process ink. To do this first the fraction of volatiles was calculated from the experiment on pure ink by
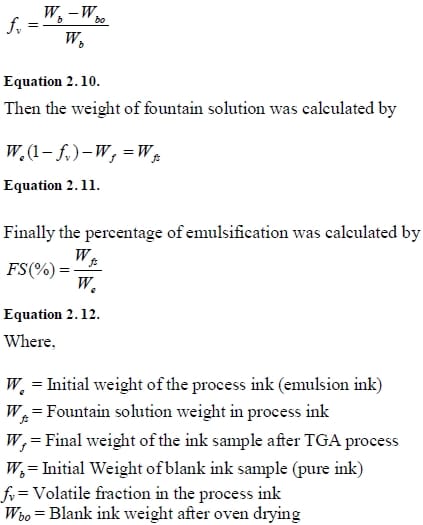
4.0 Establishment of Experimental Technique
This chapter will discuss the development of the experimental methods and some reasoning behind the choice of several parameters that have been used in the experiments.
4.1 Fountain Solution
Fountain solution is used on an offset press to keep the ink from adhering to the nonimage areas of the offset plate. Fountain solution is used to keep ink off the background with a film of water, to maintain the hydrophilic nature of the background, to quickly clean ink off the background during press starts, to promote fast spreading of water over the plate surface, to help the water flow evenly through the dampening rollers, to lubricate the plate and blanket as well as to control emulsification of ink and water.
Two important keys that need to be considered in fountain solution application are pH and conductivity. pH is a measurement of the degree of alkalinity of substances. Conductivity is the ability to transmit or conduct an electrical charge. In water of any solution the degree of conductivity is d
etermined by the number of ions present as a result of minerals or other compounds in the water. The higher the concentration of ions, the higher the degree of conductivity is.
To measure conductivity, an electronic conductivity meter is used. Many are combined with pH meters so pH and conductivity can be measured at the same time.
In the past, up to 20% isopropyl alcohol was used in fountain solution. It was used to help the fountain solution flow across the dampening rollers. Isopropyl alcohol is a very good wetting agent. This feature allows fountain solution to wet the plate well. However isopropyl alcohol is high in volatile organic compounds and it is not widely used in the pressroom now. Alcohol substitutes have been developed to replace isopropyl alcohol. Alcohol substitutes are a mixture of solvents which are strong ink solvents but which are non-volatile.
The Man-Roland press had been using fountain solution with a conductivity of 1500 µS. Therefore it was decided to replicate this conductivity for the Heidelberg measurements. Two measurements were done using tap water and deionised water. These are shown in Figure 4. 1. Based on these results (Figure 4. 1), 5% by volume of fountain solution in deionised water was used for the Heidelberg measurements.
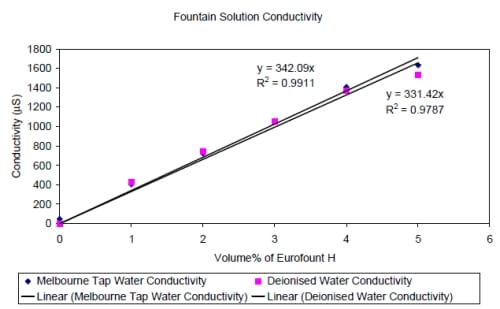
Figure 4. 1. Fountain Solution in Tap Water (y=342.09x) and Deionised Water (y=331.42x) Conductivity.
4.2 Reproducibility of Tape Pulls [74] and Paper Batch Variability
The tape pulls method has been used for years by Norske-Skog Research and Development as a lint weight measurement. They have been printing solid, 50% screen and also a standard picture for 7000 copies and then running the last 20 copies without ink to clean the ink from the blanket. Therefore the sample weight will be mostly contributed by lint particles on the blanket. Once the weight is found, the area of the tape is known therefore the lint weight per unit area can be calculated. The reproducibility of the lint value measured in this way has been checked for water settings of 6.5 and 7 on the Heidelberg press. The same batch of Norstar was used for all experiments. The results are shown in Table 4. 1 and Table 4. 2.
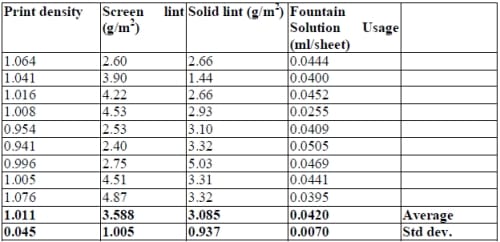
Table 4. 1. 50% Screen and Solid Lint at water setting 6.5 [74].
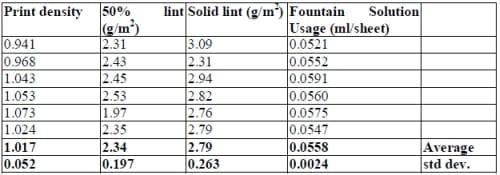
Table 4. 2. 50% Screen and Solid Lint at water setting 7 [74].
The standard deviations of the print density, water usage and the lint results when the water setting was 7 were around 10% for both the solid and 50% screen lint. While when the water setting was 6.5, the standard deviations were around 30%. Water usage is an important factor since too low a water setting will result in piling. Piling is a condition where lint is not deposited evenly along the printing blanket. This is illustrated in Figure 4. 2 and Figure 4. 3 which show the blanket deposit and tape pull for a printing trial on the Heidelberg GTO-52 with a 6.5 water setting. The same batch of Norstar was used for these series of experiments. The standard deviation of a measurement is around 10% of the measurement value.
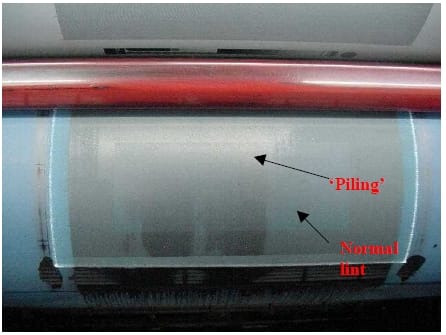
Figure 4. 2. Piling on the printing blanket [74].

Figure 4. 3. Piling results in lint weight measurement tape-pulls result [74].
Having done the experiments in it was decided that a water setting of 7 would then used [74] for the rest experiments. This is then the standard water setting for the Heidelberg experiments that is listed in Table 3. 4.
Eight batches of Norstar were used in the Man-Roland and Heidelberg experiments. These were described in section 3.0.1. Batches B and C were selected for examination of the variability within and between the batches.
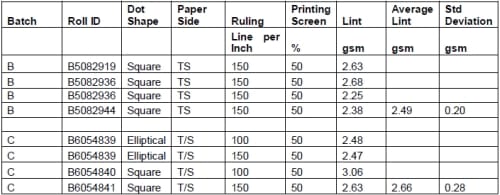
Table 4. 3. Variability between Norstar batch B and C.
These Heidelberg experiments were done according to the standard conditions in Table 3. 4, but with both ellipse and square dot shape plates. Table 4. 3 shows variability experiments within batches B and C, as well as the variability between batch B and C of Norstar. The effect of dot shape on linting is considered to be a lot smaller compared with the effect of paper batch variability and therefore both of ellipse and square dot shape plates were used to investigate the variability of the paper. Standard deviations of lint values of batch B and C are around the 10% of the average lint values, which agrees with the experiments that had been done in Table 4. 2. Both batch B and batch C shows that batch B and batch C averages lie within the upper and lower standard deviations of each other. Thus, Norstar batch B and batch C are no different to each other within the variability limit. These results suggest that the Norstar batch A to H results are comparable to each other.
4.3 Domtar Lint Collector Weight Measurement
Domtar lint collector has been used since the late 1970s to collect lint from the printing press blanket. 5% isopropanol has the standard solvent used to clean the blanket and collect lint on the printing blanket. 100 mL of solvent was used in collecting lint on the Heidelberg GTO-52 printing blanket and 200 mL of solvent was used to clean lint on the Man-Roland Uniset press blanket. The reason behind this was that up to 40,000 copies were printed in the Man-Roland trials, compared with only 7000 copies for Heidelberg GTO-52 trials.
After collecting 100mL or 200mL of the samples from the printing blanket, 1% of the sample was then filtered using mixed cellulose ester (MCE) filter to create surfaces for image analysis. 50% volume of the sample was filtered with glass filter to obtain a lint weight measurement.
The process of producing both samples is shown in Figure 3. 18, Figure 3. 19, Figure 3. 20 and discussed in section 3.2.3.1.2. After filtering and drying, each MCE filter was then sandwiched between a microscope slide and a cover slide and was ready for microscopic image analysis.
4.3.1 Weight stability of Glass Filter
Originally, the MCE filter was used for both image and weight analysis. However, it was found that the weight of the MCE filter was not stable under oven drying. In order for us to get a reliable lint weight measurement, the MCE filter has to be stable in weight. Results showed that after filtering the sample, where lint could be seen on the MCE filter, and drying at 105ºC for 30 minutes, the weight was found to decrease compared with the original weight of the MCE filter, determined after oven drying.
It was believed that the reason for this discrepancy is that the isopropanol reacts with the cellulose ester and carries away some of the MCE filter mass with it. Due to this, MCE filters were only used for filtering part of the sample for microscopic image analysis. MCE filters were used for image analysis since it provides 0.45µm pore size and the colour contrast provided by the filter surface facilitates particle detection. The lint weight analysis was done with glass filter paper with pore size of 0.7µm, which has much better weight stability through the filtering process.
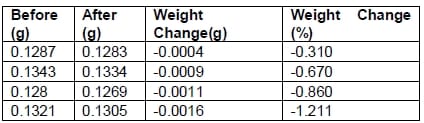
Table 4. 4. Blank glass filter paper weight change before and after filtering process
Table 4. 4 shows four glass filters that were dried at 105ºC for 30 minutes before the filtering process and weighed (before). Then, 5% i
sopropanol (blank, no lint inside) was filtered and each glass filter was dried in the oven at 105ºC for 30 minutes and weighed (after). Glass filter weight losses were in between 0 to 1.2% during the filtering and drying process. The common lint weight in the glass filter papers are in the range of 0.01 to 0.1 gram. Therefore the weight losses of the glass filters are 1% to 10% of the lint weight.
4.4 Weight Measurement Comparison between Domtar and Tape Pulls Method
There are discrepancies in weight measurements between the Domtar filtering method (4.3) and the tape pulls method (4.2). The Domtar filtering method always gives a lower weight than the tape pulls method.
The reasons for this may be that filtering is more complex method compared with tape pulls, whereby the samples are transferred from the Domtar tray to the sample container and then are filtered through the filtering system ( Figure 3. 18). Part of the samples can be lost during the process. Secondly, not all of the lint particles are removed during the Domtar brushing process. Several tape pulls test were done after Domtar sampling to investigate why there is 5 to 30% weight discrepancy between Domtar and Tape pulls. These tape pulls measurements were taken on other parts of the blanket which were not washed with the Domtar. The exact result seemed to depend on how thick the ink layer on the blanket was. Some of the ink components may be dissolved in the 5% isopropanol for the Domtar method while ink would have been retained by the tape pulls method.
The relationship between Domtar and Tape Pulls lint weight is as shown in Figure 4. 4 and Figure 4. 5. The relationship is better with the y-axis intersection of 1.035 (Figure 4. 4) instead being forced through 0 g/m2 (Figure 4. 5). This indicates that there is probably a layer of ink that cannot be cleaned with the Domtar method. This is actually somewhat positive since we are not interested in measuring the ink weight remaining on the blanket. Instead, we are more interested in measuring particles lost from paper. However, the tape pull lint weight measurement is still useful and it has the advantage of simplicity and because no lint particles are lost during the collection process. Therefore the tape pulls method has been mainly used to measure the lint weight results in this thesis. While the tape pulls method was used for lint weight measurement, Domtar samples were used for the measurement of the area and length distributions of lint particles using image analysis.
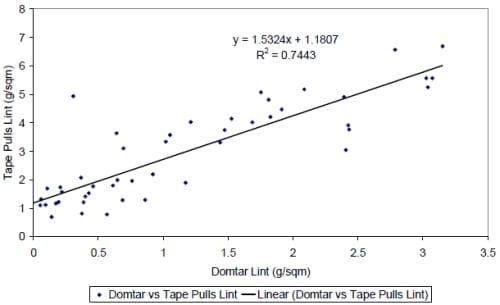
Figure 4. 4. Relationship between Domtar and Tape Pulls Lint using a general linear fit
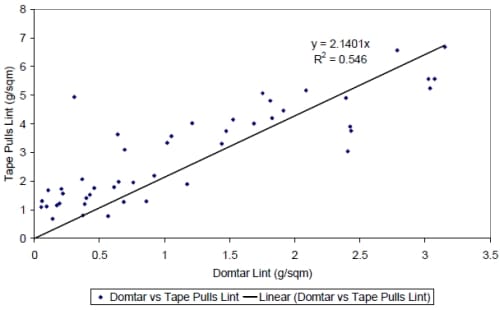
Figure 4. 5. Relationship between Domtar and Tape Pulls Lint through 0, 0
4.5. Relationship between Lint Total Area and Lint Weight on the Blanket
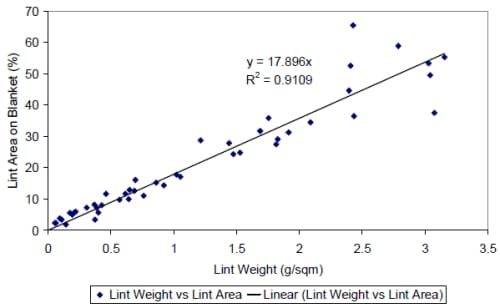
Figure 4. 6. Relationship between Lint Weight and Lint Area of Lint collected from Black Ink Tack 4 and 9 with 5 different printing screen tone (0%, 25%, 50%, 75%, 100%, picture) from Man- Roland Uniset Trials.
Figure 4. 6 shows a very good correlation between lint weight and lint area of lint produced by different ink tack and six different printing tones using the Domtar lint collection method. The relationship between lint area and lint weight is linear.
4.6 Microscopic Image Analysis
Image Pro 4.5 was used to analyse sample filtered by the MCE. 20 images each of size 7.3 mm2, out of the total area of 1134mm2 are taken for each sample. An Image pro macro was written to analyse the images. The reason behind taking only 20 images per sample and not more will be explained later in section 4.6.1. The development of the macro and what it does will be explained in section 4.6.2.
4.6.1 Accuracy of the Number of Images Captured
The accuracy of the counts of lint particles captured through image analysis was also verified by checking the statistical data of 20, 40, and 80 captured images from two different printing trials. Images were taken at a magnification of 50 times using a BTX 60 light microscope. The measurement method was discussed in section 3.2.3.2.
The method chosen for the analysis was to measure 80 images of two separate samples. Each set of 80 images were then divided into two groups of 40 images each and four groups of 20 images. When the mean area of lint particles of each group of 20 images and 40 images were compared with the original 80 images, it was found that the average lint area per image, in &um;m2 varies between 0.8 to 12 percent, and on average, it differs by 4.8 percent from the average for 80 images, as shown on Table 4. 5 and Table 4. 6.
This value is still acceptable, therefore, 20 images was considered to give adequate statistics, and taking 80 images for each printing trials was unnecessary because of the amount of time needed to process all the data. Sample A in Table 4. 5 was lint sample of black tack 4 ink – 6000 copies printed. Sample B in Table 4. 6 was lint sample of black tack 4 ink – 4000 copies printed.
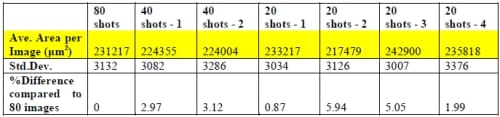
Table 4. 5. Statistical data of different number of images captured for sample A
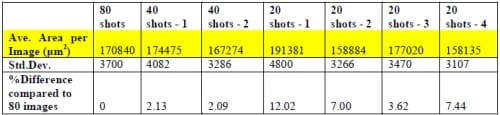
Table 4. 6. Statistical data of different number of images captured for sample B
4.6.2 Image Pro Macro
The complete Macro written in image pro 4.5 is attached in Appendix D. In this subchapter, what the Image Pro Macro does will be explained in more detail. This macro was written for the purpose of picking up contrast between the lint particles and filter paper and classifying the lint particles by size and area. Since the MCE filter paper is used, the contrast will be good between the white MCE filter vs. the coloured lint particles. Before using Image Pro 4.5, it needs to be calibrated, i.e. specifying the width and length of each pixel.
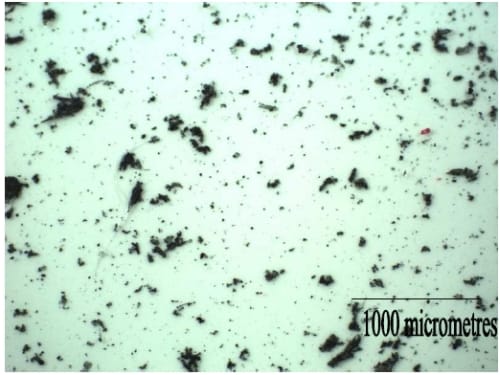
Figure 4. 7. Example of image taken under BX-60 Light Microscope under 50x Magnification
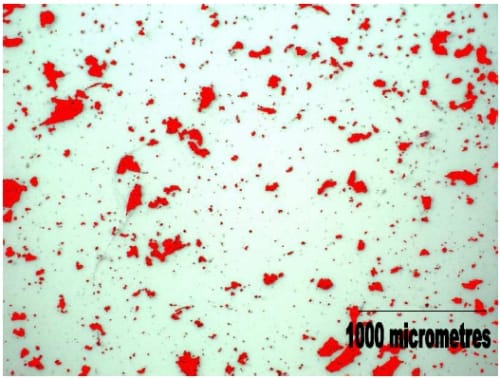
Figure 4. 8. Example of image taken under BX-60 Light Microscope under 50x Magnification After Automatic Threshold was applied
Image Pro 4.5 has an automatic threshold. This is an inbuilt command that is capable of setting the threshold between bright and dark objects. In this case, it can be used to spot the lint particles on the MCE filter. When the contrast is not so good, automatic threshold cannot be reliably implemented. An image of a lint sample is shown in Figure 4. 7. Figure 4. 8 shows the image after the implementation of the automatic threshold, with the lint particles identified in red. There are several inbuilt functions to measure the area, length and width, roundness, width-length aspect ratio, box area as well as many more. However, the main functions used were here the area and length. The dimensions of each lint particle were analysed to determine the maximum and minimum as well as the average length. When the macro is run through each image, a table is exported to Excel file. The way the particles are categorised is they are categorised into 16 different classes. One of the limitations of the program is that only a maximum of 16 classes can be used. These classes can be divided based on area or length. Most of the work in this thesis was done by classifying the
particles based on the average area of the particles. The area classes used for most of the work are given in Table 4. 7.
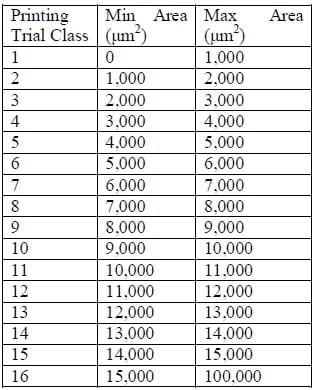
Table 4. 7. Particle classes for image analysis of Heidelberg GTO-52, Man-Roland Geoman and Uniset Samples
To speed up the analysis all 20 images from a given sample were place in one folder. The macro was written so that all the images in a folder would be analysed automatically. The complete Image Pro Macros is given in Appendix D.
A typical table of results exported to Excel is given in Table 4. 8. This gives the particle area statistics for the image in Figure 4. 9 and Figure 4. 10. The parameters to be investigated can be changed according to the information required. Those 20 tables are then averaged into one table as shown in Table 4. 9. This program also gave statistics results on the image analysis, which is shown in Table 4. 10.
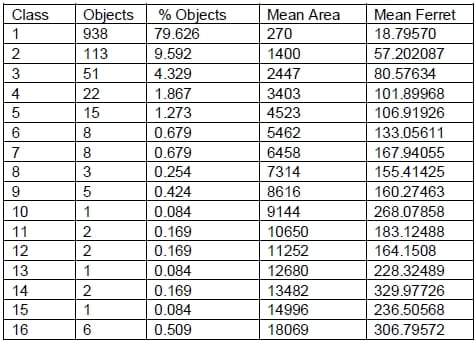
Table 4. 8. Table of Results exported to Excel by Image Pro
Figure 4. 9 and Figure 4. 10 shows area and length distribution comparisons between 20, 40, and 80 images processed using the Image Pro macro. Both figures show that using 20 images gives the same area and length distribution as 80 images.
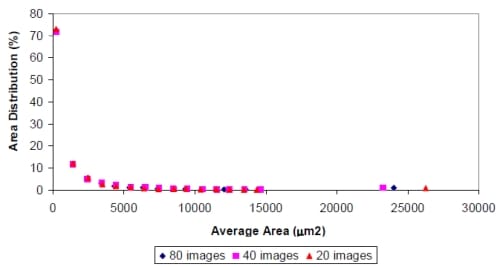
Figure 4. 9. Lint Area Distribution of Lint Comparison of 20, 40 and 80 Image Shots of 6000 Copies Sheet-Feed Black Colortron Tack 13.5.
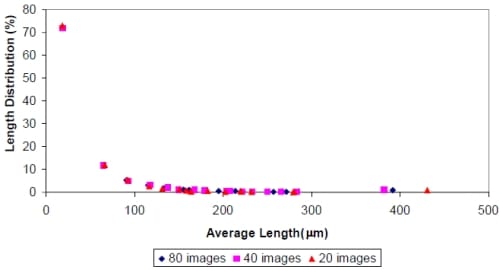
Figure 4. 10. Lint Length Distribution of Lint Comparison of 20, 40 and 80 Image Shots of 6000 Copies Sheet-Fed Black Colortron Tack 13.5
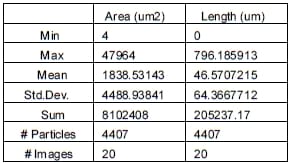
Table 4. 10. Statistics on the analysis of 20 images of each sample
4.7 Comparison between IGT Pick Test and Printing Trial Experiments
There have been several laboratory scale measurement done in order to investigate linting [8, 21, 71]. For the work in this thesis, an offset IGT pick test was used in the initial stages of the work to check the applicability of the method to linting. Details of the test method are in chapter 3.1.2. The pick test chosen used a high speed and a tack 16. It was immediately apparent that the size of the lint removed in the IGT Pick experiments was much larger than that removed in the printing press.
Accordingly, new larger size classes were selected for the sorting of the lint identified from image analysis of the picking experiments. The first two of the new classes, numbers 17 and 18, covers the whole range of lint particle sizes used in the analysis of the lint from the Heidelberg and commercial printing presses. Figure 4. 11 – Figure 4. 14 [2] compares area and length of lint particles from IGT pick test to those of the printing trials, both on the Heidelberg press and the Man-Roland Geoman. Chapter 5.2.8 explained the experiment in more details.
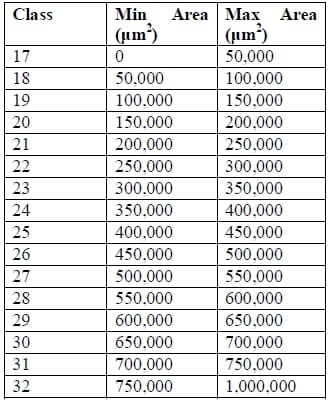
Table 4. 11. Particle Area Classes for IGT Lint [2]
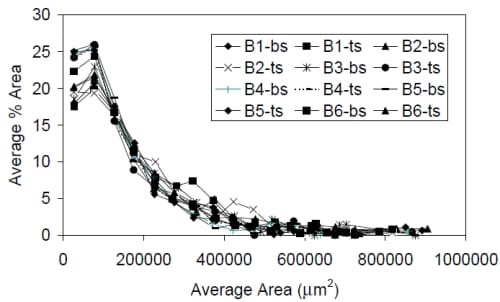
Figure 4. 11. Area distribution of lint particles measured from IGT pick experiments on the top and bottom sides of six samples of Norstar.
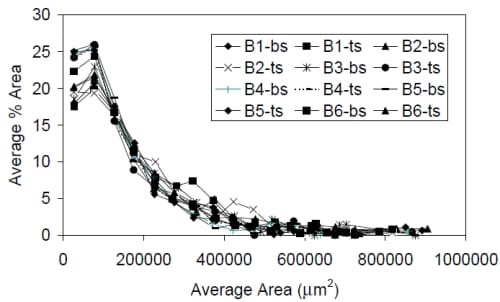
Figure 4. 12. Length distributions of lint particles shown in Figure 4. 11
Results from small and larger commercial printing trials showed a reasonable degree of agreement between the lint distributions resulting from both of them when comparing lint area and length distributions. This comparison is shown in Figure 4. 13 and Figure 4. 14. In these figures, tack 4.5, 6, 9, and 13.5 were run in the Heidelberg GTO-52, while Comm. black 7 and Comm. Black 8 were run with Man-Roland Geoman. The detail of the Man-Roland Geoman experiment is discussed in Chapter 5.2.8.
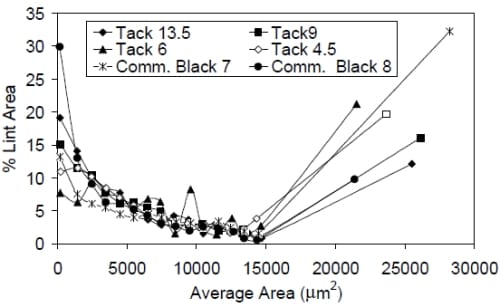
Figure 4. 13. Area distribution of lint particles produced in two printing operations using black ink.
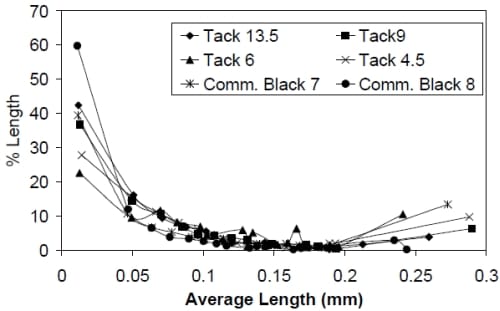
Figure 4. 14. Length distributions of lint particles shown in Figure 4. 13
When the total area of the lint in all classes is summed, then it is possible to estimate the total fraction of the surface, which was removed as lint. For the IGT experiments, this was on average 2.4%. That is, on average fibres had been pulled from 2.4% of the total surface area in the single printing run of the IGT experiment. The equivalent areas for the Heidelberg trials were only 0.001 to 0.003%, provided it is assumed that all lint particles removed from the paper surface had remained on the blanket. For the commercial newsprint measurements the lint removed was an order of magnitude smaller than the Heidelberg measurements, since similar amounts of lint were pulled out after 7,000 copies on the Heidelberg press as were removed after 137,000 copies on the commercial press.
Thus both the area of the particles removed as lint, as well as the size of the individual particles, is much larger in the IGT test than is produced on the presses tested here. This suggests that the IGT test is likely to be of limited usefulness in predicting linting on full scale commercial presses and this technique was not further employed in the work in this thesis.
5.0 Results and Discussions
The results and discussion chapter is divided into four different areas, i.e. paper variables, ink and fountain solution balance, printing press blanket/plate variables, and printing press operating conditions.
5.1 Paper Variables
There were three different types of paper that were used in the Man-Roland Uniset trials. They are Norstar, i.e. a 52 gsm improved newsprint with ISO brightness of 74 manufactured on PM2 at Norske Skog Boyer Mill. Its furnish is 67 % TMP radiata pine, 28 % chemi-mechanical eucalypt (cold caustic soda) and also has a filler component of 5% calcined clay (supplied by Imerys as Alphatex). The second grade of paper used in the trial was 45 gsm Nornews made by Norske Skog Boyer. It consists of 25% cold caustic soda pulp, 20% recycled fibre and 5% kraft pulp. The rest is TMP, with no added filler component in it. The third grade of paper is 42 gsm Nornews produced by Norkse Skog France, i.e. Golbey. It has 60-75% of recycled fibre and the rest of it’s furnish is TMP. This paper was labeled Golbey in this thesis to distinguish it from the Nornews produced at Boyer. Both Nornews and Golbey have lower lint than Norstar.
In order for us to eliminate the effect of take-off angle, both of the paper grades were run exactly with the same take-off angle. The first trial which investigated the effect of paper furnish composition, was run from reel stands 6 and 8 (even numbered reel stands), therefore the right hand side is the bottom side of the paper. Since the right hand side printing couple position is higher compared with those of the left hand side, the bottom side of the paper has a slightly higher take off angle (~105°) compared with the top side (~75°).
Based on the 95% confidence interval [76], ANOVA Systat showed that the paper grade, take off angle, screen, paper side and ink colour all had statistically significant effects on lint. There were two ways interaction that were statistically significant. Howe
ver, these will not be discussed here. The analysis of variance were done with the three different papers: Golbey, Nornews and Norstar, 5 different printing screen : 0%, 25%, 50%, 75%, and solid, both top and bottom of the paper lint, the two different web take-off angle, i.e. 75º and 105º, and each of the four colours that were printed.
5.1.1 Comparison between Norstar, Nornews and Golbey Paper for Both Top and Bottom Side of the paper (First Man-Roland Uniset Trial)
From Table 5. 1 and Table 5. 2, it can be seen that most results showed Golbey (GB) produced most lint, followed by Norstar (NS) while Nornews (NN) produced the least. Fines, fillers and recycled fibres are the components that cause lint. Recycled fibres can be smaller in size compared with both TMP and CCS fibres therefore it is easier for them to be picked up as lint. Fines are desirable if they bond well with the fibres. The printing plate that was used in this experiment is shown in Figure 5. 27.
Table 5. 1. 4-Colour Printing Lint of Top Side of the Paper (take off angle of 105º)
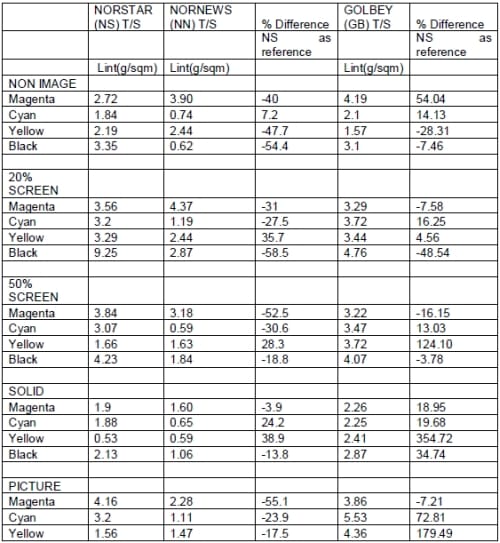
Table 5. 2. 4-Colour Printing Lint of Bottom Side of the Paper (Take off angle of 75º)

Table 5. 3. Summary of Average Lint of Different Screens, Colours and Take-off Angles
Table 5. 3 shows that Golbey, followed by Norstar and Nornews gave the highest linting results
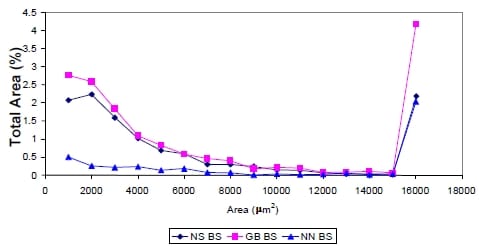
Figure 5. 1. 50% Printing Screen Tone Lint Total Area in Blanket Comparison between NN (Nornews), Norstar (NS) and GB (Golbey) of B/S of the respective paper, Toyo Black Tack 4 Ink.
Figure 5. 1 shows the total lint area on blanket, expressed in percentage area of lint on the blanket area. In general, Golbey, followed by Norstar and then Nornews has the highest percentage area of lint on the blanket.
As can be seen in Figure 5. 2, Figure 5. 3, the relationship between weight and area were relatively high for Norstar, followed by Nornews. However, Golbey lint has no relationship between its weight and its area, as the R2 of the straight line fit to the data is very poor.
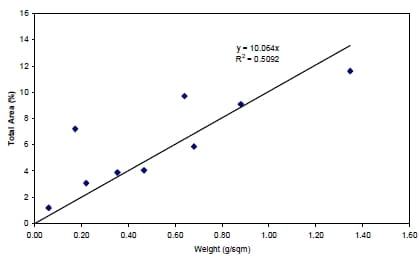
Figure 5. 2. Relationship between Weight and Area of Lint of Nornews
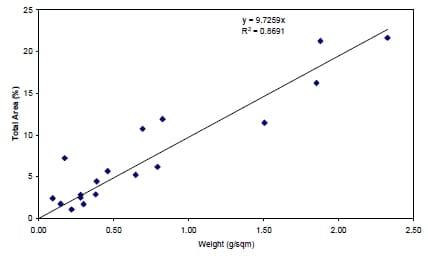
Figure 5. 3. Relationship between Weight and Area of Lint of Norstar
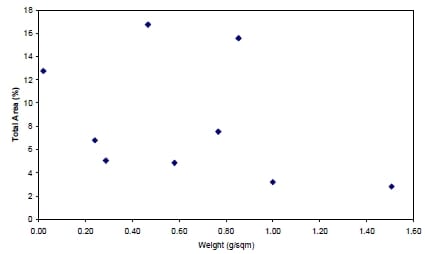
Figure 5. 4. Relationship between Weight and Area of Lint of Golbey
5.1.2 Comparison between Top and Bottom Side of the Paper
In the first Man-Roland Uniset trial, two web reel stand were used in order for us to compare the two-sidedness of the Norstar paper. Reel stand 7 was used for the first run therefore the bottom side of the paper is on the LHS, while on the second run, reel stand 8 was used for the second run and the top side of the paper is on the LHS. The right hand rollers position are slightly higher than those of the LHS (Refer to Figure 3. 11 – Figure 3. 14), therefore the RHS paper take off angle is higher (105º) than that of the LHS (75º). Take-off angle is the angle at which paper web exits from the printing nip. If the paper web goes out straight vertically, the take-off angle is defined to be 90º. The results of the two runs are shown in Table 5. 4.
In Run 1 of the first Man-Roland Uniset Trial, the right hand side take off angle is higher than the left hand side, therefore the top side of the paper has higher take off angle compared with the bottom side of the paper. Therefore if the T/S and B/S of the paper are compared for the first run, there will be accumulated effect of the two-sidedness of the paper as well as the difference in take off angle. In run1, top side of the paper has on average 44.22 % lint as high as compared with the bottom side of the paper.
In Run 2 of the first Man-Roland Uniset Trial, reel stand 8 was used, therefore now the T/S of the paper is in the LHS of the print couple and this means that T/S of the paper has lower take off angle. The T/S of the paper has 39.37 % lower lint than the B/S of the paper. However this is the accumulated effect of the two-sidedness of the paper and the effect of the take-off angle.
In order for us to be able to exclude the effect of take-off angle, only the top/bottom side of the paper with the same take-off angle was compared to each other. This is done in Table 5. 4.
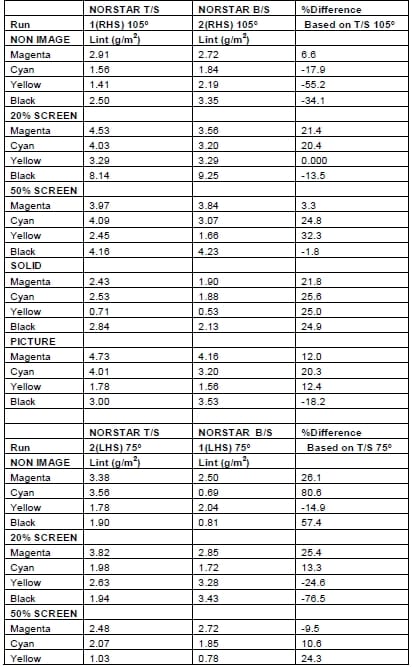
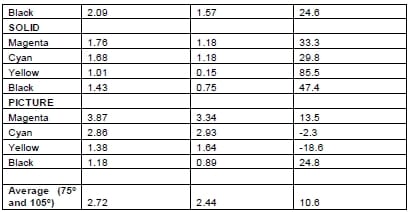
Table 5. 4. Comparison of Norstar Top Side and Bottom Side of the Paper for both take off angles 75º and 105º (First Man-Roland Uniset Trial)
From Table 5. 4, top side of the paper of Norstar that is produced by Paper Machine number 2 at Norske Skog Boyer produced more lint ( around 10.56%) compared with the bottom side of the paper. The average values shown in Table 5. 4 are the average of all T/S or B/S of Norstar. Systat ANOVA of this experiment, which is given in Appendix A, also showed that two sidedness of the paper was one of the significant factors affecting linting and that the top side of the paper had higher lint than the bottom side.
Man-Roland Uniset second and third trial also showed that the top side of Norstar produced more lint compared with the bottom side, please refer to Chapter 5.4.3. Although for these trials the effect of side was not tested independently of take off angle, as it was for the trials reported in this section.
Figure 5. 40 also shows that the top side of the papers produce more lint than the bottom side of the paper, when comparing lint from the solid and 50% screen.
5.2 Ink and Fountain Solution Effects on Linting
The effect of ink and fountain solution on linting will be discussed in 5.2.1, 5.2.2, and 5.2.3. These sections will discuss the effect of ink tack, the effect of four-colour printing, and the effect of ink colour, respectively. Further ink and fountain solution measurements to explain the results in chapters 5.2.1 to 5.2.3 will be discussed in chapter 5.2.4 to chapter 5.2.8. The definition of tack and how it is measured is presented in Chapter 5.2.2, printing parameters that could affect ink tack value are discussed in Chapter 5.2.4 and the effect of shear rate towards shear viscosity is presented in Chapter 5.2.3. The effect of ink colour and 4-colour printing on linting is discussed in Chapter 5.2.5 and 5.2.8, respectively. Chapter 5.2.6 discusses the tack value of emulsified ink and the methods of measuring the degree of emulsification of ink are presented in Chapter 5.2.7.
5.2.1 Effect of Ink Tack
Ink tack is defined as the torque required to split the ink film in the nip of an inkometer. The unit for torque is gram of force metre. The standard speed used in inkometer is 800 rpm with 32.2 ºC temperature and 1.38 grams of ink, which is delivered by a pipette. The effect of ink tack on linting will be discussed here by looking at both the lint weight and lint image analysis results.
Each of Figure 5. 6 -Figure 5. 11 and Figure 5. 15 shows either area or length distributions and the sum of all points equal to 100%. These figures show the relative proportions of small and large lint p
article while Figure 5. 12 – Figure 5. 14 are either total length per area of blanket or the percentage area of lint on the blanket. Figure 5. 12 – Figure 5. 14 will give better comparison with the total amount of lint. When comparing the results between the figures, it should be noted that the number of copies printed in the three different printing machines is quite different, i.e. 7000 copies for Heidelberg GTO- 52, and 25,000 copies for Man-Roland Uniset.
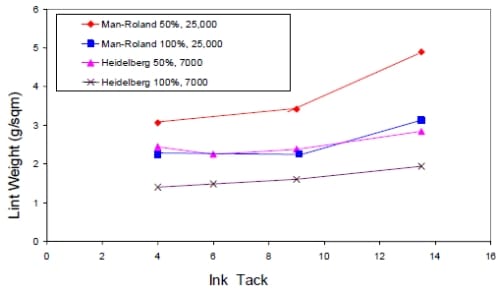
Figure 5. 5. Effect of Ink Tack towards Lint Weight Results.
Figure 5. 5 shows the lint weight measurement results as a function of ink tack for the data from the second Man-Roland Uniset trial (Chapter 3.2.2.2) and the Heidelberg. The Man-Roland data points were the average of both top and bottom side of the paper and four different of take off angle, i.e. 27º, 78º, 102º, 153º. The inks used for both experiments were Toyo Black ink. Only the bottom side of the paper, with take off angle of around 70º, was printed for the Heidelberg tests. Each data point here is the average of three replicates. The Heidelberg experiments used standard conditions stated in Table 3. 4. Norstar batch B was used for the Heidelberg experiments while Norstar batch E was used for the second Man-Roland Uniset trial. Figure 5. 5 includes results both for the 50% screen tone (labelled 50%) and the solid (labelled 100%).
The results in Figure 5. 5 show that the higher the ink tack used in printing, the higher the measured lint accumulated on blanket. However, the lint result on the blanket did not increase too much from tack 4 to tack 9 but there was clear increase from tack 9 to tack 13.5.
However, on the plate, the amount of lint produced by the trials with the tack 9 ink was significantly greater than that produced by printing either the tack 4 or tack 6 inks. It wasalso noticed that the image quality degraded when a higher tack ink was used since there was a higher rate of lint migration from the blanket to the plate. Therefore more lint stay on the plate, resulting in offsetting to the blanket and printing to the paper as non image area.
In order to better understand the effect of ink tack towards lint, the particle area distributions of the lint particles as a function of tack were investigated.
5.2.1.2 Heidelberg Lint Area and Length Distribution Results
The data with various tacks in Figure 5. 6 – Figure 5. 9 were obtained with the indicated tack inks on the Heidelberg GTO52 Press at Norske Skog Boyer. The figures appear to show a parabolic type distribution of the lint either when lint area or particle length are examined. The shape is however, somewhat misleading as it arises from the selection of the size classes for image analysis. For example, due to the limitations of the software to sixteen size classes, the last area class includes all of those lint particles with area of 15,000 – 100,000 µm2. Thus the points for the largest size class are well separated from the rest of the points and show a larger percentage area than for the points in the preceding area classes only because of the larger range of measurement. If the area classes had been uniformly distributed then the data would have shown the same negative exponential type distribution that the rest of the data displays, providing enough lint particles had been measured to obtain reliable results.
Results in Figure 5. 6 – Figure 5. 9 show some very interesting trends. Firstly, there seem to be relatively little differences between the lint produced in the different tack and colour inks used in the Heidelberg press. The similarity between the lint distributions from the cyan and black trials on the Heidelberg is not surprising. The Heidelberg press is a single colour press and therefore simply changing the colour of the ink, everything else being equal, should not change the distribution of the lint particles. The other thing to note from Figure 5. 6 and Figure 5. 8 are that the distributions show no trend with ink tack. For example, in Figure 5. 6 the tack 6 ink has the highest percentage of particles in the largest area class, while the tack 9 ink has the highest percentage of large particles for the cyan ink measurement shown in Figure 5. 8.
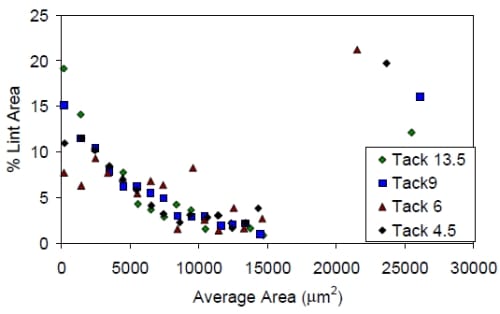
Figure 5. 6. Area distribution of lint particles produced in Heidelberg GTO-52 of 50% printing screen of Black Ink
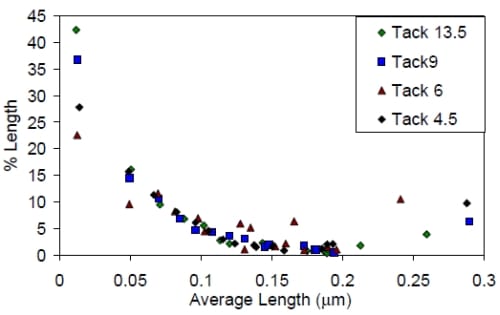
Figure 5. 7. Length distributions of lint particles shown in Figure 5. 6
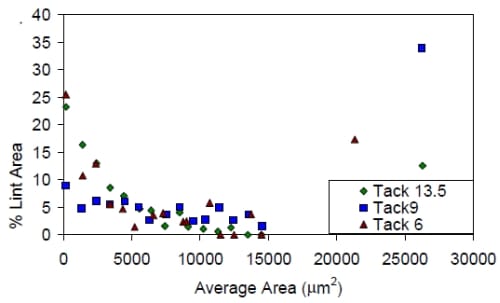
Figure 5. 8. Area distribution of lint particles produced in produced in Heidelberg GTO-52 using cyan ink of 50% printing screen of Cyan Inks
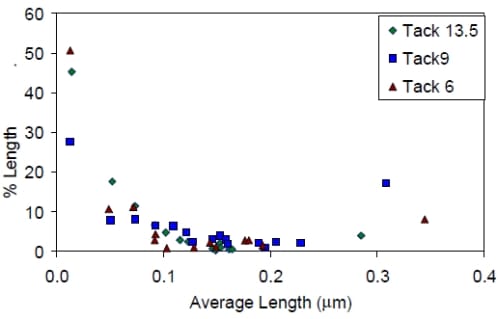
Figure 5. 9. Length distributions of lint particles shown in Figure 5. 8
5.2.1.3 Man-Roland Uniset Second Trial Lint Area Distribution Results
The effect of ink tack on lint particle size distribution is examined in Figure 5. 10 – Figure 5. 14. The lint image analysis method of sample collection and data analysis used to measure the data is described in chapter 3.2.3.1.2, 3.2.3.2, and Chapter 4.4.
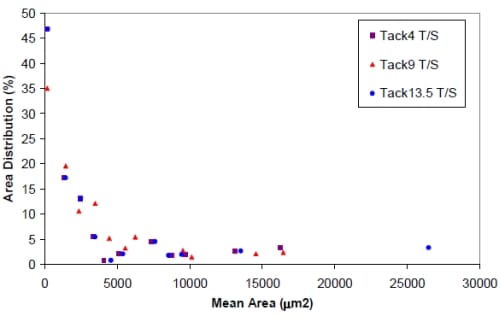
Figure 5. 10. Man-Roland Uniset Third Second Lint Area Distribution as a function of ink tack at 50% Printing Tone at a 27o degree take-off angle printed on the top side of the paper
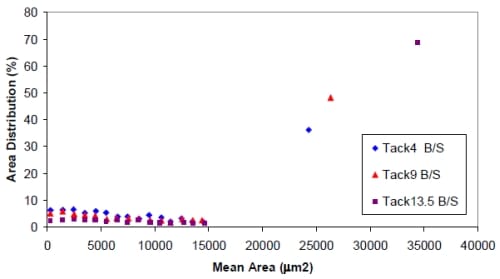
Figure 5. 11. Man-Roland Uniset Second Trial Lint Area Distribution as a function of ink tack at 50% Printing Tone at a 153° degree take-off angle printed on the bottom side of the paper
Figure 5. 10 and Figure 5. 11 plot the lint area distributions for the lowest and highest take-off angle, respectively for 50% tone and the 3 different ink tacks that were used in the Man Roland Uniset trials. The results show relatively little difference in the shape of the area distribution between the measurements with the different tack inks. There is some suggestion for the data with the highest take-off angle of 153o that the increase in the ink tack has increased the percentage and size of the lint particles in the largest size class. However the effects are relatively small in comparison to the differences in the distributions arising from the change in take-off angle. The effect of take-off angle is discussed in chapter 5.4.3.
Thus the results obtained on both the Heidelberg and the Man-Roland Uniset show no apparent effect of tack on particle size except at the highest take-off angle on the Man- Roland press of 153°. To investigate further the effect of tack at this take-off angle, the total lint area distributions for all screen tones and tacks, at a take-off angle of 153°, have been plotted in Figure 5. 12 – Figure 5. 14. For comparison, the total lint area distributions for the 13.5 tack ink and the 27° take-off angle is presented in Figure 5. 15.
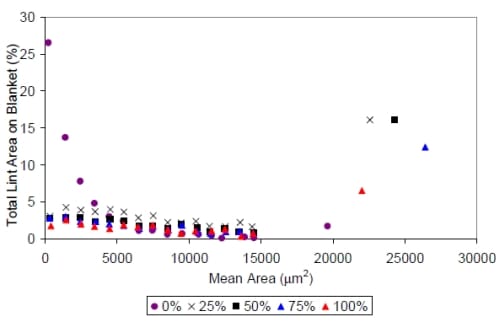
Figure 5. 12. Man-Roland Uniset Second Trial Total Lint Area on Blanket of B/S of the Paper with Tack 4 Black Toyo Ink with 153° Take-Off Angle
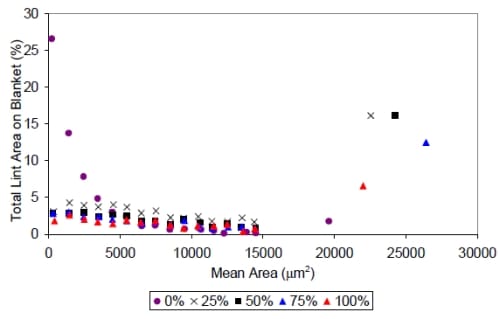
Figure 5. 13. Man-Roland Uniset Second Trial Total Lint Area on Blanket of B/S of
the Paper with Tack 9 Black Toyo Ink with 153° Take-Off
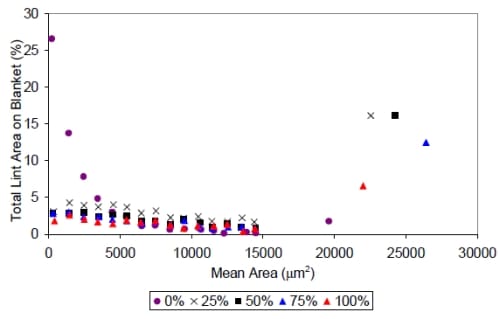
Figure 5. 14. Man-Roland Uniset Second Trial Total Lint Area on Blanket of B/S of the Paper with Tack 13.5 Black Toyo Ink with 153° Take-Off Angle
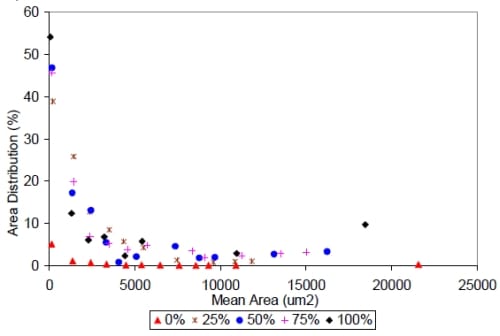
Figure 5. 15. Man-Roland Uniset Second Trial Lint Area Distribution on Blanket of T/S of the Paper with Tack 13.5 Black Toyo Ink with 27° Take-Off Angle
Figure 5. 12 – Figure 5. 14 are the measurements at 153° take-off angle on the bottom side of the paper of Man Roland Uniset second trial (Chapter 3.2.2.2). The figures show the lint distributions at the different screen tones. Each figure contains results for a separate tack of ink. There is not much difference in the small size particles total area lint with the exception of 0% screen tone that has the highest amount of lint of the smallest particle size.
Figure 5. 12 – Figure 5. 14 shows the effect of tack on the total area of lint which expressed in terms of percentage of lint area on blanket. It could be seen that the total percentage area of small particles decreased from tack 4 to tack 9 and tack 13.5. However, the total lint area in the largest particle class increased dramatically from tack 4, tack 9 and was highest for tack 13.5. This means that the lower tack inks at this 153° take off angle, the majority of the lint are smaller particles while the higher tack inks pick up larger lint particles.
It should be noted that this effect seems only to apply at this very high take-off angle. There is not much effect of ink tack on the particle size distribution for the Heidelberg test samples of Domtar lint collection (Figure 5. 6 – Figure 5. 9) and the Man-Roland lint Domtar samples (Figure 5. 10 – Figure 5. 15). Heidelberg and Man Roland tape pulls samples (Figure 5. 5) also show little effect of ink tack to lint weight from ink tack 4 to 9 and then show a small increase from ink tack 9 to 13.5. Man-Roland Uniset third trial samples from the 27° take-off angle (Figure 5. 10, Figure 5. 15) also shows that at a lower take-off angle, there is little effect of ink tack towards lint.
We are then faced with attempting to explain why the effect of ink tack has been relatively small when the take-off angle is small but is quite large when the take-off angle is large. At a lower take-off angle, it is the shear in the nip that could be important. The Porepoise viscometer shows that the apparent viscosity of the different inks converge at different shear rates and so there might only be small differences at the high shear rates in the printing press (Chapter 5.2.3). This compares with the much lower shear rates used in inkometer, which will produce larger differences between the inks. At higher take-off angles it seems that the extensional behaviour of the ink becomes important. The relationship between extensional viscosity to the tack measured in the inkometer should be the subject to further study.
The tack values given here were measured using an Inkometer, which measures the ink tack based on a specific rotational speed and specific temperature of the roller. The ink industry normally uses 800 rpm and 32.2°C for the temperature of the roller. It is generally accepted that at high rates, inks are shear thinning, where the apparent viscosity will fall as the apparent shear rate increases. Thus it is important to perform the measurements at a shear rate that is relevant to the press under investigation. Since the shear rate of inkometer and the commercial presses are very different (Chapter 5.2.2: Table 5. 5 and Figure 5. 19), the Inkometer tack is therefore not likely to be a good predictor of lint as rheological state of the inks are quite different in the lab instrument and in the press. This is discussed further in the next section.
5.2.2 Ink Tack Measurement using Inkometer
Ink tack is defined as the torque required to split the ink film in the nip of an inkometer. The unit for torque is gram of force metre. The standard speed used in inkometer is 800 rpm with 32.2 ºC temperature and 1.38 grams of ink.
However, it is known that the Toyo inks were tested by the manufacturer at 1200 rpm. The maximum speed of the inkometer is 2000 rpm. Tack is dependent on the speed, temperature as well the ink film thickness on the rollers of the equipment
Figure 5. 16 shows tack as a function of measurement speed for the Toyo inks. The tack number of the ink in the legend was given by Toyo who did the measurement at 1200 rpm and these numbers match well with the measurements shown in this figure. It can be seen that the higher the speed, the higher the ink tack is.
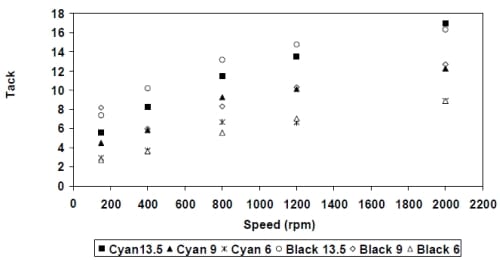
Figure 5. 16. Effect of inkometer speed on Inkometer ink tack with standard ink weight manufactured by Toyo
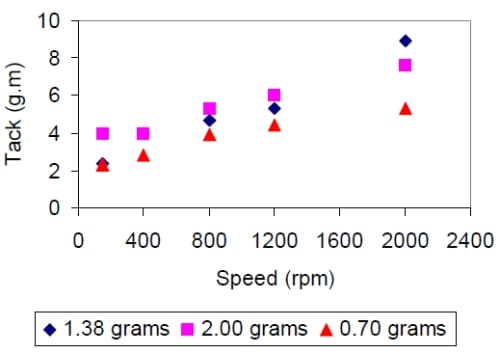
Figure 5. 17. Ink weight and speed effect on tack number of coldset black Flint ink Tack 4.6 [48]
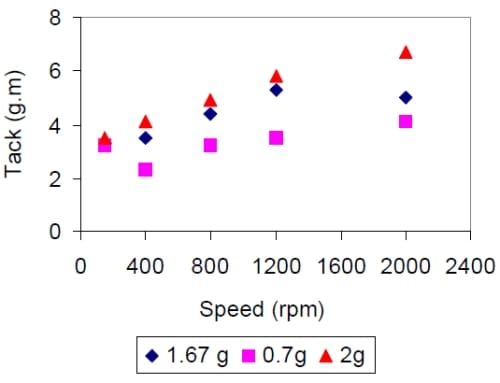
Figure 5. 18. Ink weight and speed effect on tack number of coldset cyan Flint ink Tack 4.6 [48]
Inkometer measurements are a measure of ink tackiness. However, the number is dependent on ink weight and the roller speed. 1200 rpm translates to around 5 m/s peripheral speed which is lower than the speed of a modern web-fed printing press, which is normally around 10 m/s. While the speed is lower than that of larger commercial printing press, the ink film thickness applied on the inkometer is around 14.48 µm compared with a 1-2 µm ink film thickness of newspaper printing. Therefore the tack number resulted from inkometer has only an indirect relationship to the ink film behaviour and properties in the printing nip.
This leads us to another experiment to vary the applied ink weight. The results in Figure 5. 17 and Figure 5. 18 show that the use of a higher ink weight produces a higher tack value. This also agrees with the Deltack experiments which are explained further in section 5.2.4.1.
5.2.3. Shear Viscosity Measurement with Porepoise
The shear rate of an ink film can be found by from ink film thickness when it splits divided by the speed of the ink rollers.
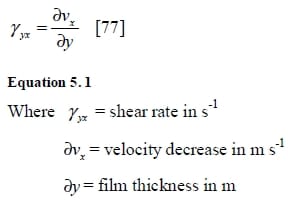
Shear viscosity is applicable in the printing press nip since the force applied is parallel to the ink film direction of travel. Once the ink splits at the exit of the nip, extensional viscosity is more relevant since the splitting force is perpendicular to the direction of ink film flow.
The approximate apparent shear rates in the Inkometer, Hydroscope and the two printing presses are given in Table 5. 5. The ink weights for the Inkometer and Hydroscope were calculated from the ink weights of 1.38 and 10 grams, respectively as well as the respective roller areas of the two instruments. The ink weight in the printing press was assumed to be between 1-2 gsm. The shear rates given in Table 5. 5 were then calculated using Equation 5. 1.
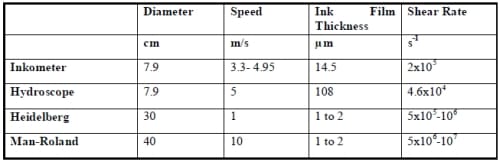
Table 5. 5. Shear rate occurs in the printing roller nip of the three different machines
Porepoise rheometer is a capillary rheometer that is capable of measuring the effect of shear rate towards shear viscosity. The advantage of this instrument is it can perform measurements at high shear rates of up to 200,000 s-1. The results of the tests on the Toyo inks ar
e shown in Figure 5. 19.
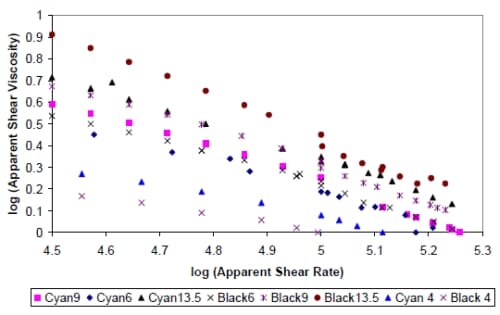
Figure 5. 19. Apparent shear viscosity decreases as the apparent shear rate increases of Toyo Inks
From Figure 5.12, it can be seen that shear viscosity decreases as the apparent shear rate increases. This figure shows a log-log plot of the data. The data for each of the inks can be well fitted by a straight line. The apparent shear rate in the commercial printing press is three to thirty times as much as the maximum apparent shear rate in the inkometer, which is around 200,000 s-1. However with the linear relationship between log of apparent shear viscosity and log of apparent shear rate, the apparent shear viscosity can be predicted from a straight line fit to the data. The apparent shear viscosities converge as the apparent shear rate increases.
5.2.4 Tack Force Measurement with Prüfbau Deltack
A project that was done by 4th year undergraduate student in Monash University was set up to investigate the effect of several print variables on the ink film splitting force. Robert Vukasinovic [47] did this project for one semester in 2005. The ink that was used was Toyo Black tack 13.5.
The Prüfbau Deltack can measure the force of ink film splitting between paper and printing roller. Speed, ink film thickness, type of printing roller, nip pressure and the paper grade can be varied (Refer to 3.1.1 for more details of the method)
All the Deltack results will be presented in this section will be averages of four runs, to condense the data and give a better estimate of the trends produced. Some of the runs only consist of three samples. This was due to the fact that on occasion there was a result that was very different to the others and which was removed to produce more accurate averages. The average ink film splitting force calculated from the point where ink film force starts to stabilise until the end of the run, i.e. distance 24 mm to 75 mm in Figure 5. 20.
As the forme is rolled across the printing surface of the paper the Deltack calculates the tack force required to split the free ink film and then calculates the average for that run. A typical plot of this tack force response is displayed below in Figure 5. 20.
The only real variance for each run under each printing conditions is the value of the plateau that is reached in each occasion.
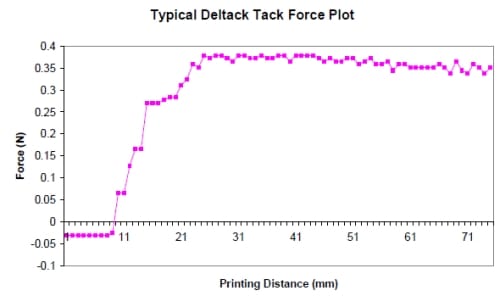
Figure 5. 20. Typical Deltack Tack Force Plot [47]
5.2.4.1 Effect of ink volume on Tack Force
The first parameter of the printing process to be examined is the effect of ink volume on the tack force required to split the free ink film. As mentioned previously this tack force contributes to linting during printing, so it would be of great interest to be able to minimise this property if possible. The results are shown in Figure 5. 21. The range of ink volumes printed on paper was from 0.1mL to 0.3mL. Use of volumes less than 0.1mL prevented the paper from being adequately coated. The use of volumes greater than 0.3mL caused the ink to be splattered from the roller as it was being dispersed. The ink volume tests were carried out on only one batch of 45gsm Boyer Nornews paper due to the limited time frame. The effect of speed and pressure were also investigated.
As can be seen in Figure 5. 21, the tack force increases with ink volume. Clearly the free ink film increases as the ink volume increases and hence requires more force to split it.
This result actually opposed Stefan’s Law (Equation 2. 1) that stated that ink film thickness is inversely proportional to the ink film splitting force.
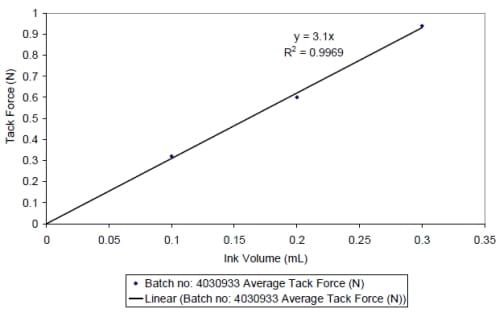
Figure 5. 21. Effect of Ink Volume on Tack Force [47]
5.2.4.2 Effect of Print speed on Tack Force
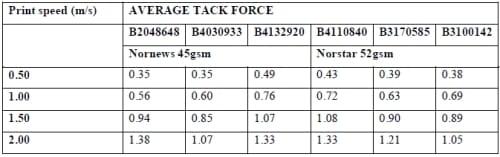
Table 5. 6. Printing speed comparison [47]
The print speeds analysed ranged from 0.5 m/s to 2 m/s and were carried out at a mid range printing pressure of 800N and ink volume of 0.2 mL. The resulting tack forces produced for the six batches (B2048648, B4030933, B4132920, B4110840, B3170585, B3100142) as can be seen in Table 5. 6.
It can be clearly seen that the tack force required to split the free ink film was directly proportional to the printing speed. This is most probably due to the fact that at high speeds the roller has less time in contact with the paper and hence less time to transfer ink, leading to less ink entering the pores. This causes the ink film of the paper/roller interface to be thicker leading to a larger tack force being required in order to split it. In comparison at lower speeds the ink has more time to enter the pores and hence this reduces the film thickness.
Another effect might be due to the ink rheology. The ink film splits as an extensional flow. It may be that the more force is required to split the ink film when it is split at a faster rate.
5.2.4.3 Effect of Print pressure on Tack Force
The printing pressures examined throughout this experiment were in the range of 400 N to 1200 N and were conducted at a speed of 1m/s and ink volume of 0.2 mL. The results, as seen in Table 5.11, were not as conclusive as the speed trials however a trend still existed.
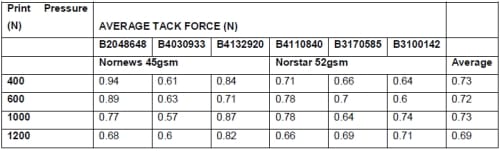
Table 5. 7. Printing pressure comparison [47]
As the printing pressure increased the tack force produced decreased slightly, especially for the batches of 45gsm. This inversely proportional relationship was likely to be related to the free ink film and the amount of ink that was forced to enter the pores as force was increased.
The decrease in tack force was as a result of the smaller pores being filled as the pressure overcame the capillary forces resisting the inks entry. The reason for two of the 52gsm batches not experiencing the same trends was is likely to be due to the fact that for the improved newsprint the average pore diameter is smaller and hence requires more pressure for the ink to be able to penetrate. Therefore the pressures we examined did not have a significant effect on the amount of ink transferred to this paper. This will be explored further in chapter 5.2.4.5.
5.2.4.4 Effect of grammage on Tack Force
The grammage of paper did not exhibit any real trends across the printing properties.
5.2.4.5 Effect of speed on Ink transfer
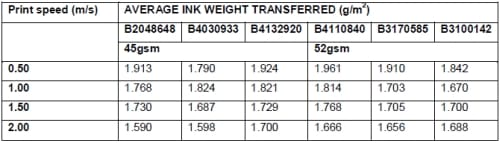
Table 5. 8. Print speed compared to ink transferred [47]
The ink transferred to the paper was calculated simply from the differences in weight of the forme before and after printing, which was then calculated in terms g/m2 using the dimensions of the paper sample to make the number more recognisable. The results seen in Table 5.12 reinforce the fact that the slower the print speed the more the ink was able to enter the pores and hence the larger the overall ink transfer.
5.2.4.6 Effect of Pressure on Ink transfer
The Ink transfer gave a lot clearer picture relating the ink transferred to the printing pressure for all six batches that were examined. As mentioned previously the pressure appears to be forcing the ink into the smaller pores as can be seen in Table 5.13.
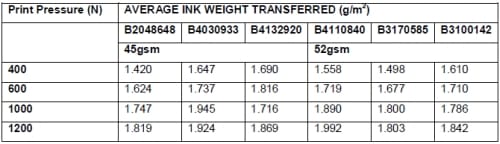
Table 5. 9. Print pressure compared to ink transferred [47]
5.2.4.7 Effect of grammage on Ink transfer
The results obtained were inconclusive and didn’t lean toward
one paper weight over the other.
5.2.4.8 The relationship between Free Ink film weight and Tack Force
The free ink weight of the film that has to be split creating the Tack force can be calculated given that none of the ink is absorbed into the rubber forme. From this, the difference in weights before inking and after printing must equal to the ink remaining on the forme.
Assuming that the free ink film is split in half, the free ink film weight can be calculated by doubling the weight of the remaining ink on the forme. A comparison of free weight versus tack force was conducted for one batch of each grammage, as seen in Figure 5. 22.
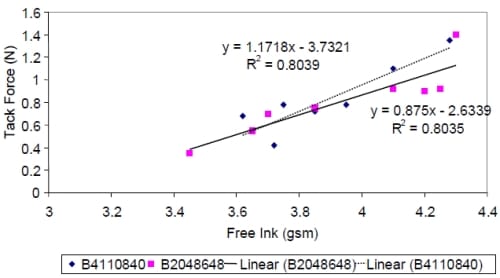
Figure 5. 22. Plot of Free Ink vs. Tack Force [47]
The trend is as expected with both paper samples (B4110840 is 52 gsm Norstar with dotted line and B2048648 is 45 gsm Nornews with solid line) producing a linear increase in tack force as the ink film weight (and hence thickness) is increased.
5.2.5 Effect of Ink Colour
A Man-Roland Uniset second trial (section 3.2.2.2, Appendix F) was done to investigate the effect of ink colour of the same tack ink towards linting. The same take off angle, Norstar batch E and the same ink tacks were applied to the same printing couple during the trials in order to be able to investigate the effect of ink colour. Tack 13.5 was done in the top couple of the Man-Roland Uniset with take off angles of 78º for the top side of the paper and 102º for the bottom side of the paper. Tack 4 was done in the bottom print couple with take off angles of 27º for the top side of the paper and 153º for the bottom side of the paper. 23,000 copies were printed for each runs.
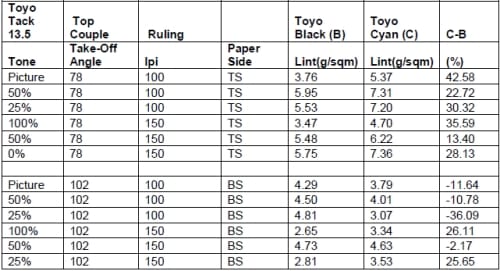
Table 5. 10. Toyo Tack 13.5 was printed on the top print couple with black and cyan ink on two different runs
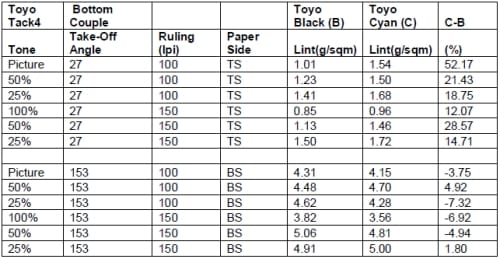
Table 5. 11. Toyo Tack 4 was printed on the top print couple with black and cyan ink on two different runs
There are clear trends for the lower take off angles (27º and 78º) that cyan ink resulted in higher lint for the same nominal tack number. However with the higher take off angle, black ink seemed to result in higher lint than the cyan
The side with the higher take-off angle has a higher rate at which the blanket surface and the paper will separate coming out of the printing nip, provided all other press variables are constant. The higher the printing speed, the higher the torque required split the ink film in the inkometer (Figure 5. 17 and Figure 5. 18).
Figure 5. 17 and Figure 5. 18 show the effect of ink weight and ink speed on tack for black and cyan tack 4.6 inks from Flint. Figure 5. 16 shows the effect of inkometer speed on the tack measured for the Toyo inks. From Figure 5. 17 and Figure 5. 18, it can be seen at a lower speed (standard inkometer speed of 800 rpm), both of the inks shows tack number at around 4. However at a higher speed, both of them behave differently. Black ink tack increases more than the cyan, in other words the linear slope of tack increase versus speed is higher for black ink than that of the cyan. The Toyo tack 9 and 13.5 inks in Figure 5. 16 show the reverse effect with the slope of the cyan data being lower than for the corresponding black ink. Thus inks with nominally the same tack display divergent behaviour at different inkometer speeds. For a higher take off angle, the rate at which the ink film splits is higher and therefore the black tack ink could have a higher tack than the cyan ink. Another reason is that the same tack inks with different colour have different rheological properties and behave differently when they are emulsified, which is discussed in 5.2.6. The methods of measuring fountain solution in ink emulsion are discussed in 5.2.7.
5.2.6 Emulsified Ink Tack
While the Inkometer measures the tack of the ink and not the emulsified ink, the Hydroscope is able to measure the development of ink tack only with the addition of fountain solution to the ink in the rollers. The fountain solution feed rate and the roller speed can be varied.
Figure 5. 23 shows the tack development curves that were obtained on the Hydroscope on for the black inks of different tacks and manufacturers. In this Figure the lines marked FS give the amount of fountain solution that has been added. All of the inks show a similar behaviour, with the tack decreasing as fountain solution is added followed by a recovery in tack when fountain solution addition was stopped when the ink became saturated. The fountain solution feed was stopped at saturation point, which was the point where bubbles formed across the whole length of the printing nip. Table 5. 12 summarises the measurements and gives the initial tack before fountain solution addition, the tack at saturation and the volume of fountain solution required to saturate the ink.
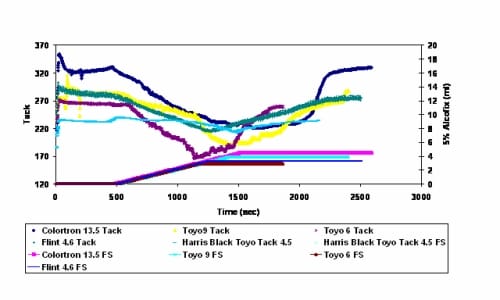
Figure 5. 23. Change of hydroscope tack number with the addition of 5% Alcofix fountain solution of black ink
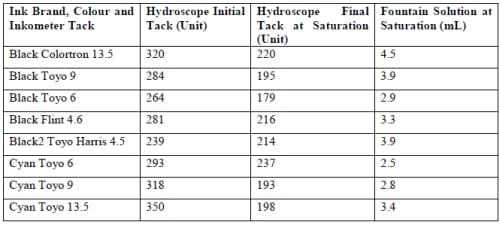
Table 5. 12. Hydroscope Tack and Fountain Solution Saturation Point of 10 grams Inks
Inks from different manufacturers (Flint, Toyo and Colortron, Toyo (Harris) that is specially manufactured for Harris Print) give different trends. Thus Flint tack 4.6 can emulsify more fountain solution than tack 6 ink made by Toyo. The amount of fountain solution which was taken up by ink tack 13.5, tack 9 and tack 6 to reach saturation point decreases with tack for a given manufacturer. Harris Toyo Tack 4.5 is at around 40% of its original value at saturation but its hydroscope relative tack number is the most stable, i.e. its tack number only undergoes a slight change when the fountain solution is added, compared with the others.
From Figure 5. 23, it can be seen that that process ink in the printing press will have different tack compared with the pure ink without fountain solution. The tack of the process ink will depend on the stability of the ink with the addition of the fountain solution. Once fountain solution is added, even inks with tacks 13.5 and tack 4 could behave similarly.
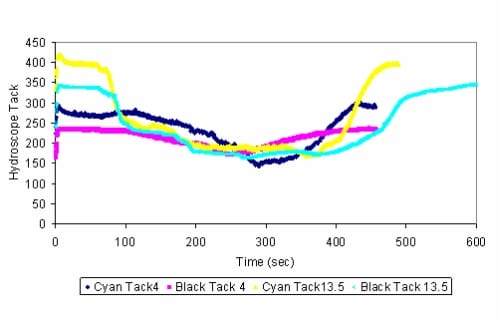
Figure 5. 24. Hydroscope Results with the addition of Eurofount H. Fountain Solution for Inks with different tacks and colours from Toyo
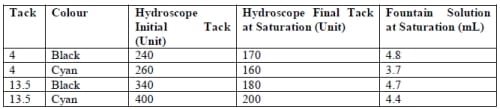
Table 5. 13 Eurofount H. Fountain Solution Total Consumption Emulsification of 10g of inks at saturation point. The inks were all made by Toyo
Figure 5. 24 compares four inks from Toyo with different tacks and colours. From Figure 5. 24, it could be seen that black inks are more stable in relation with fountain solution addition compared with cyan inks. Cyan inks have deeper trough compared with the black inks although they can emulsify more fountain solution before they reach saturation point (Table 5. 13).
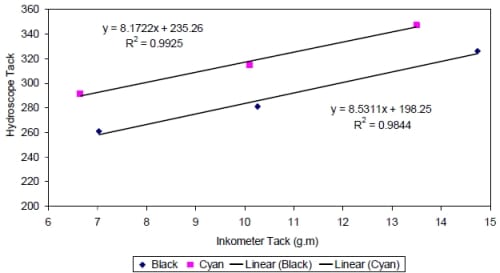
Figure 5. 25. Relationship between Inkometer tack measured at 1200 rpm and Hydroscope Tack
Figure 5. 25 shows that the relationship between the Inkometer and the Hydroscope initial tack before the addition of the fountain solution is linear but the slope and intersection with y axis is unique for each and individual ink colour and brand.
5.2.7 Me
asuring “process ink” fountain solution content
During offset lithographic printing, ink is emulsified with the fountain solution. The property of offset lithographic ink in the can is different from the property of the emulsified ink in the printing nip which we are going to call as ‘process ink’ in this thesis. Coldset offset lithographic ink normally consists of 20% carbon black, 5% alkyd resin, 5% vegetable oil, 10% resin hydrocarbon and 60% of mineral oil. The fountain solutions that were used in the experiments were Alcofix and Eurofount H. Alcofix is designed for a sheet-fed press while Eurofount is designed for web-fed press.
In offset lithographic printing, water is emulsified in ink on the ink rollers and also on the printing plate. It is then transferred to the printing blanket and then to paper. After it is transferred to the blanket and paper, the ink is also partly de-emulsified.
Measuring fountain solution content in the process ink on the Heidelberg press is not that simple since the amount of fountain solution transferred from the fountain solution rollers to the ink rollers can be measured but the amount of ink on the rollers can not be measured easily. It was then decided to measure the amount of water content in the ink on the printing plate. Fountain solution percentage in ink on the printing blanket won’t be exactly the same as the composition on the plate since there will be some deemulsification of the fountain solution from the ink. This can occur rapidly over a millisecond time frame. “Process ink”, which is ink emulsified with fountain solution in the printing process, on the plate was chosen because it is the easiest place to sample. Sampling in the inking roller is harder to do since inking roller is normally inside the system and is unreachable and sampling from the printing blanket may disturb the blanket.
5.2.7.1 Fountain Solution Consumption Measurement on the Heidelberg GTO-52
Fountain solution is fed from a measuring cylinder to the fountain solution rollers before it is transferred to the inking roller where it is emulsified. A typical measurement of fountain solution consumption on the GTO-52 is shown in Figure 5. 26.
The slope of the graph is dependent on ink emulsion characteristic under the same fountain solution roller sweep speed (Table 5. 14). The data in Table 5. 14 show that a lower ink tack is generally associated with a higher rate of fountain solution consumption.
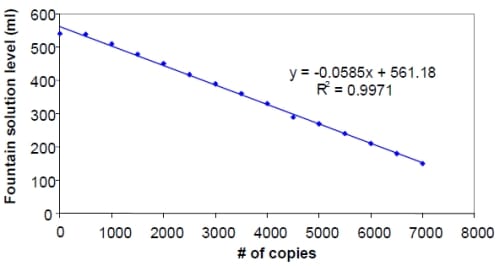
Figure 5. 26. Fountain Solution Usage in Heidelberg GTO-52 during printing of Toyo Black Tack 4
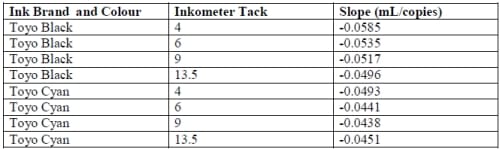
Table 5. 14. Fountain Solution Consumption per sheet of paper printed of different Inks
After a lot of number of runs, it was estimated that the fountain solution rollers consumes around 30 ml per 500 sheets printed for the Black Toyo tack 4 ink, i.e. around 0.060 g of fountain solution used per sheet of paper printed. The ink used to print each 1280 cm2 of printed area was on average 0.14 gram and this is corresponds to 0.14 cm3 of ink. The weight of the ink consumed was found by weighing the paper after it was printed and subtracting it with the weight of the blank paper. The weight of the blank paper was found by multiplying the grammage specification of the paper (gsm) by its area. The printed area consists of half solid and half 50% screen tone. This means only 75% of the total area of 1280 cm2 is inked, i.e. 960 cm2. Therefore, the ink thickness on the paper is around 1.46 µm on average.
Therefore the fountain solution content in ink on the inking roller was around 30%, assuming that none of the fountain solution evaporated in the press (0.06 g of water mixed with 0.14g of ink). This is close to the fountain solution saturation point for Toyo black ink tack 4 (Figure 5. 23).
5.2.7.2 Fountain Solution Measurement Using Tyvek Waterless Paper
The idea of doing weight measurement of the printed paper is to get an approximate estimation on how much weight of ink and fountain solution has added to the paper during printing. The weight of the paper is taken as the average gsm (gram per square meter) of the blank paper. In order for us to find the fountain solution content of printing ink on the paper, a substrate with minimal moisture content needs to be used so that the evaporation rate comes solely from the evaporation of the fountain solution. Tyvek 54 gsm waterless paper, supplied by Paperpoint in South Melbourne, was used for this purpose. At 105 °C, Tyvek only loses 0.001 % of its weight. A 100% solid printing area was then printed on the Tyvek paper. Tyvek is an extremely high tear strength material made from synthetic spun-bonded polyolefin fibers.
For the measurement on the Heidelberg GTO-52 machine, an A4 solid printing area was used in order to eliminate the effect of printing screen tone on fountain solution emulsification. The ink and fountain solution sweep settings were 7 units and 9 units, respectively. The weight of the Tyvek paper before and after printing was then noted and gave the weight of the process ink (fountain solution + ink). After the printing process, Tyvek paper printed was dried in the oven and the weight before and after drying were noted and the difference is the weight of the fountain solution and the weight of volatile component in ink. The weight of the volatile component in ink was found by using TGA experiment (Table 5. 16) and the value was taken as an average of 4.00%. Therefore by doing the printing and drying process, both of the weight of the fountain solution and ink could be found. The method is described in more detail in chapter 3.3.4.2. The results of the measurements are shown in Table 5. 15. Each data point is the average of ten measurements
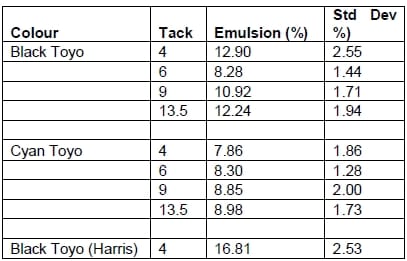
Table 5. 15. Tyvek Water-Proof Paper Fountain Solution Content in Process Ink Results
The weight percentage of fountain solution in the process ink on the Tyvek paper is within 7% to 17%. This value is lower than the emulsion rate of the process ink on the printing roller, i.e. around 30% (Chapter 5.2.4.1). This is because fountain solution evaporates as the fountain solution travels from ink rollers to printing plate and finally on the paper. These values are also much less than the emulsification capacity of the inks as measured on the Hydroscope and listed in Table 5. 12 and Table 5. 13.
As we can see above, in general the black Toyo inks takes up more water than the cyan Toyo inks do. The Harris Print Toyo black ink consumed the most water among the inks in Table 5. 15. Harris Print black Toyo ink has been designed for large web-fed press to use with a web-fed press fountain solution. During the print runs, some observations made.
- The Harris Toyo black ink balanced quicker and gave better print quality visually compared to Toyo black ink of the same tack.
- The Ink/water balance is highly affected by equipment setting, in this case the ink and water sweep, and ink duct opening.
- Higher tack inks required a bigger ink duct opening in order for it to flow with the same ink sweep rate and water sweep rate.
- Harris Print Toyo Black Ink takes up more water compared with the other two.
- The print quality degrades as the tack of the ink increased.
- The equipment setting affects the way the ink emulsifies more than the tack does.
The results above agree with the emulsion experiment done with the Hydroscope which also showed that the Harris Print Toyo black ink has a higher capacity to emulsify fountain solution compared with the other Toyo or Flint inks of the same tack and colour. The Harris Toyo black inks also have higher emulsion
stability as the tack with the addition of fountain solution is also more stable compared with the others. The Hydroscope results (Figure 5. 24) also showed that the black inks have a higher capacity to emulsify fountain solution than the cyan inks, which is consistent with the results presented here.
5.2.7.3 ATR-FTIR
Based on the consulting work done by Chemistry Department Monash University in 2003 [75], process ink sampled from the printing plate was run with ATR-FTIR and then O-H peak at around 1800 cm-1 was detected. Pure ink was also run under the FTIR as a blank sample. The method for doing so was described in 3.3.4.1.
Pure ink also has an O-H peak. The O-H peak from the pure ink was chosen as 0% level of fountain solution. A droplet of water was run under the ATR-FTIR and the O-H peak was chosen to be 100% of fountain solution. The 0% and 100% correlation was assumed to be linear therefore the process ink O-H peak was then found based on the linear plot of % fountain solution versus O-H peak height.
Process ink samples from September 2005 Man-Roland Uniset Second Trial were processed under the FTIR. There were problem with getting consistent results since process ink is far from homogenous. Pressing the ink on the microscope slide gave different results to not pressing the ink. The O-H peak was also dependent on time taken between collection and measurement. This indicated that the fountain solution evaporated over time.
After a lot of effort was put into the technique, it was realised that more accurate method was required. This was the Thermo Gravimetric Analysis described next.
5.2.7.4 Thermo Gravimetric Analysis (TGA)
The principle behind TGA (refer to 3.3.4.3) is quite simple. A sample is put on a sensitive balance capable of measuring up to 4 significant figures of micrograms of weight. This balance sits in a temperature and atmosphere controlled furnace. It was chosen to increase the temperature from 25°C to 105°C at a rate of 10 °C/minute and then hold the temperature at 105°C for 30 minutes. Pure ink was also processed exactly the same way as the process ink provided a blank sample. The decrease of process ink weight subtracted with the amount of evaporation found from the pure ink experiment gave the fountain solution content in process ink. The equations for the calculation are given in 3.3.4.2.
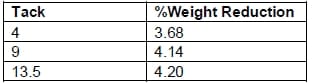
Table 5. 16. TGA weight reduction of volatile component in pure Toyo Black ink
Table 5. 16 shows weight reduction of the volatile components in blank ink samples (fv). These numbers are used to normalise the percentage fountain solution in ink sample as shown in Equation 2. 11.
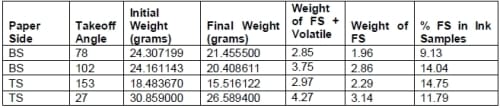
Table 5. 17. TGA Results of Process Toyo Ink Black Tack 4 collected from printing plates.
Table 5. 17 shows TGA application of process ink tack 4 samples collected from printing plates of Harris Print third trial run 2 (refer to 3.2.2.3). The pure ink acted as a blank sample undergoing 3.68% reduction in weight as shown in Table 5. 16. This is the weight of the volatile components in the ink.
Table 5. 18 shows results from samples that were collected in the second Harris trial for analysis by ATR-FTIR. Following the failure of the ATR-FTIR tests, these samples were then analysed months later with the TGA in April 2006. In comparison, the Table 5. 17results were samples from the third Harris trial in April 2006 which were analysed in May 2006. Therefore slightly lower fountain solution contents in Table 5. 18 are expected due to process ink sample evaporation.
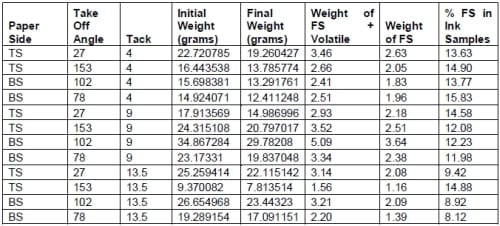
Table 5. 18. TGA results of Process ink with (Toyo) printed on BS/TS at different take-off angles
The results in Chapter 5.2.7.2 and 5.2.7.4, i.e. Tyvek waterless paper printing method with Heidelberg GTO-52 and TGA method in which samples were collected from the second and third Man Roland Uniset trial, were all done with the same inks, i.e. Toyo Black tack 4, 9 and 13.5 for both of the methods. Toyo black tack 9 was also tested on the Heidelberg GTO-52.
The Heidelberg GTO-52 samples analysed with Tyvek paper gave results ranged between 7% – 17% for black Toyo inks with tacks 4, 9 and 13.5. The emulsion rate results of samples from Man-Roland Uniset (Table 5. 17 and Table 5. 18) are in the same range as the emulsion rates of the samples from the Heidelberg GTO-52.
To sum up, the experimental data showed relatively little effect of ink tack on lint. Ink tack is measured in the Inkometer and the tack force is contributions from both shear in the nip as well the filamentation. Inkometer is also dependent on the speed and ink volume. Unfortunately the range that is available in the machine does not match the speed and ink volume in the commercial printing presses. In addition, the shear viscosity of the inks change with shear rate. Unfortunately the rate of change is different with different tack inks.
Ink that is used to print in the press is emulsified with fountain solution. Ink emulsification behaviour changes with tack and color and experimental data show differences in lint when colour changes. Lab based instruments also confirmed this.
Correlation between the lab measurements with the linting performance on the press has not been developed yet and this should be the subject of future work.
5.2.8 Effect of Four-Colour Printing
There were two trials were done to investigate the effect of four-colour printing. One was done in the first Man-Roland Uniset trial (Table 5. 19 – Table 5. 20) and the other was done on the Man-Roland Geoman (Table 5. 21). The first Man-Roland Uniset trial experimental method is given in Chapter 3.2.2.1.
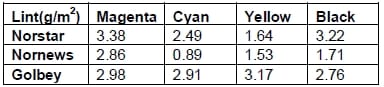
Table 5. 19. First Man Roland Uniset 4-Colour Printing Trial: Averaging 20%, 50%, 75%, 100% and Picture Printing Screen and Both Paper Sides
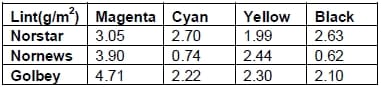
Table 5. 20. First Man-Roland Uniset 4-Colour Printing Trial: Averaging non image area of Both Sides of the Paper

Table 5. 21. Man-Roland Geoman CMYK (Cyan, Magenta, Yellow, Black) Lint Weight
In the Man-Roland Geoman, cyan was printed first, followed by magenta, yellow and black. This is different from Man-Roland Uniset configuration where magenta is printed first, followed by cyan, and the yellow with black last. Since the Man-Roland Geoman trial was printing commercial newspaper, there was no control over the printing screen and there was no balancing of print between the four colours. C1 and C2, B7 and B8, Y6 and Y7, B7 and B8 were sampled from different position of the printing blanket of the different images sampled (Figure 5. 27 and Figure 5. 28).
Except for the Golbey paper in the first Man-Roland Uniset trial, the lint deposited shows the same parabolic trend in both the Uniset and Geoman trials, with the minimum in lint for the second and third colours printed. The maximum lint is generally for the first colour printed and there is an increase in lint between the third and fourth stages (Table 5. 19, Table 5. 21). The Golbey paper is unique in that it produces approximately the same level of lint across all four printing stations. This may in some way be related to the very high level of recycled fibre used in the manufacture of this product. The non-image area (Table 5. 20) also shows that the first printing stage produced the maximum lint but the subsequent printing stages do not seem to produce the sam
e trend among the three different papers.
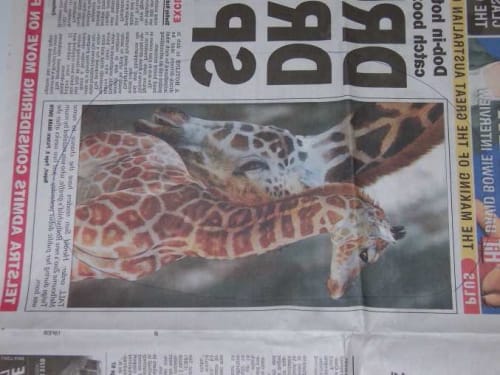
Figure 5. 27. Image of the blanket from where C1 and B7 were sampled from
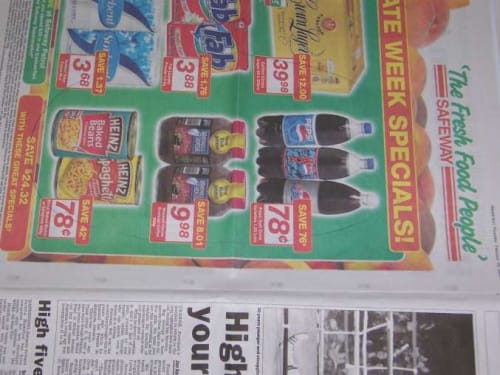
Figure 5. 28. Image of the blanket from where C2 and B8 were sampled from
There are very clear differences seen in the area distributions for the lint from the cyan and the black blankets on the Man-Roland Geoman press (Figure 5. 29), where cyan was the first colour printed and black was the last (the fourth).
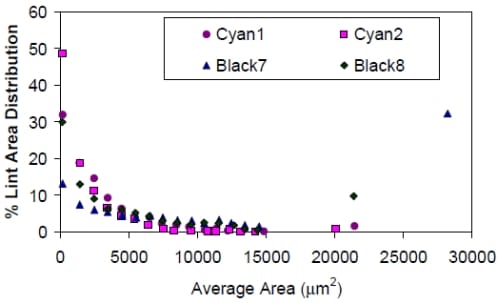
Figure 5. 29. Man-Roland Geoman Trial with Cyan and Black Ink Tack ~4 and 45 gsm Nornews
Cyan produced a lot smaller particles compared with that produced by the black. It can be seen that in comparison to the cyan runs on the Heidelberg (Figure 5. 8), there are very few large particles removed as lint in the second printing couple of the Man-Roland Geoman (Figure 5. 29). This is consistent with the changes in character of the lint as the paper moves through a multi-colour press as the cyan was the first colour printed on this press and the black was the last.
In contrast, the lint from the black blankets has approximately the same area distribution as that produced in the Heidelberg press (Figure 5. 6), whichever ink was used to perform the printing trial. This is possible because Heidelberg and Man-Roland Geoman are two very different machines other than both are offset printing presses. The ink, fountain solution settings as well as the geometry of the printing press are totally different. Heidelberg GTO-52 printing rollers are also smaller than those of Man-Roland, however the speed is a lot lower than that of Man-Roland, therefore two inks of the same tack number of 4 could behave totally different in the nip, depending on all of the factors influencing the ink rheology. In addition the Heidelberg GTO-52 is a sheet fed process while the Man-Roland is web-fed. As a result of all of these factors, the lint resulted from both of the printing processes could be quite different.
As has been previously stated in the literature [2, 7], the lint removed on application of the first colour is likely to be predominantly small fragments, only loosely bound into the surface, such as dust from slitter operations. The application of the fountain solution in the application of each colour then roughens and weakens the surface of the newsprint, increasing the likelihood that larger, better bonded particles will be removed, later in the printing process. There is, as yet, no means of quantitatively predicting how the character of the lint will change as it passes through the printing process. Different paper with different compositions, i.e. Norstar, Nornews and Golbey, different take-off angle (Table 5. 19, Table 5. 20, Table 5. 21) can give different answers about the effect of first and subsequent printing on linting. This is due to the different natures of the size of the lint particle candidates, i.e. dusts and fillers are likely to be picked up by low printing forces while take-off angle (nip geometry) is also one of the factors to define the printing forces.
5.3 Printing Press Blanket and Plate Variables
5.3.1 Screen Ruling, Dot Shape and Dot Orientation
Screen ruling is one of the important variables that need to be investigated. 100 lines per inch screen ruling (lpi) is quite common for commercial web-fed newspaper printing while 150 lines per inch is more common for sheet-fed commercial printing. Therefore 100 and 150 lpi were investigated for their effect on linting.
The experiments were done both with the Heidelberg GTO-52 and Man Roland Uniset second trial (Chapter 3.2.2.2). Norstar batch C was used for the Heidelberg experiments and Norstar batch E was used for the second Man-Roland Uniset trial. The Man-Roland Uniset trial investigated only the effect of line ruling while the Heidelberg trials also investigated the dot shape and dot orientation of the plate. In the Heidelberg experiment, the plate type, dot shape and orientation were changed but the other experimental conditions followed Table 3. 4. The dot shapes and orientations used in the Heidelberg trials are explained in Table 5. 22.

Table 5. 22. Dot orientation on printing plate
The Man Roland Uniset data is given in Table 5. 23. Analysis of variance of the results from the second Man-Roland Uniset trial showed that the screen ruling had no statistically significant effect on linting (please refer to Appendix B and Table 5. 23). Although there are variations in the lint results of the two different screen ruling, statistically, the effect was not significant. There are a lot of other variables that may contribute to these variations. For example, there are three different operators in charge of the water and ink tuning. The thickness of the blanket across the paper web may also vary since sometimes the printing press is run half web and other times it is run full web.
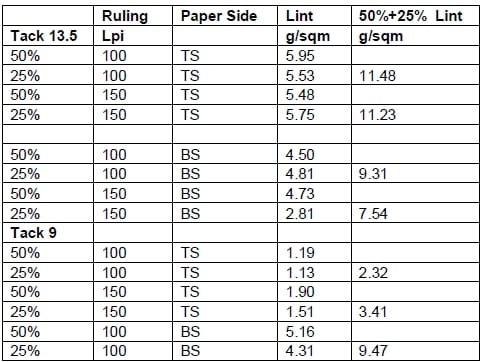
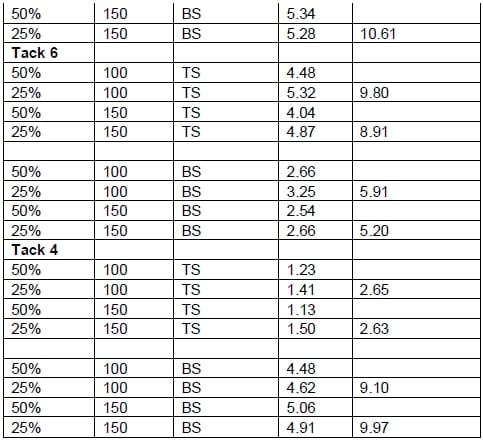
Table 5. 23. Second Man-Roland Uniset Trial
The results from the Heidelberg GTO-52 (Table 5. 24) also shows that both averages of 100 lpi and 150 lpi lint of multigrain plates with wide varieties of printing tone, dot shape are almost identical. From Appendix H, where paper side, dot shape, screen ruling and printing screen tone were investigated using analysis of variance, it was found that paper side and dot shape were the only two significant variables, while line ruling was not significant.
The results also show that the top side of the paper lints more than the bottom side of the paper. Circle resulted in highest lint result, followed by square and ellipse. There are more experiments that need to be done to investigate the effect of dot shape, i.e. line, dot orientation and plate type to linting. From Table 5. 24, a 90° ellipse gives higher lint compared with the 0° ellipse while a 0° square gives higher lint than the 45° square. However, these results need to be confirmed in the future.
The differences observed when changing dot shape and orientation are probably because the force required to split the ink is affected by how the dots are oriented. A shorter length of the boundary between the image/non image area in the direction of printing will probably give a lower ink splitting force between the plate and paper.
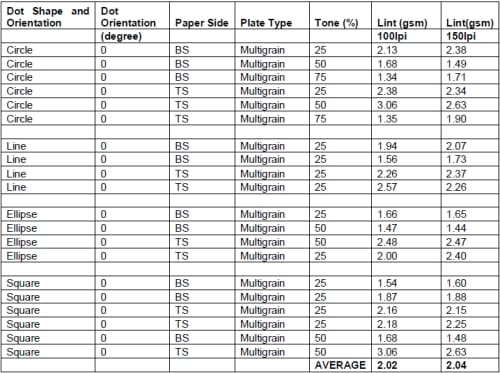
Table 5. 24. Effect of Screen Tone, Dot Shape and Dot Orientation on Linting on the Heidelberg
5.3.2 Plate Type
There are several major types of lithographic plates used in the printing industry today: diazo, photopolymer, silver halide, electrophotographic, bimetal, waterless, and digital waterless.
Negative-working films are used to image the negative working plate. These plates are generally coated with photopolymer and are known as negative working presensitised plates. To expose the plate, a film negative is placed over the light sensitive coating and exposed to UV light [78]. Light that passes through the clear areas of the negative reacts with the monomers of the photopolymer under the non-clear areas of the negative [78]. Processing removes unexposed non-hardened polymer. An application of a gum solution to the non-image areas of the plate can make it water-attracting/ink-repelling. The processing does not wash off the hardened polymer image areas of the plate [78].
Positive working pl
ate are more expensive compared with the negative working plate [78]. Positive films are used to image this plate. The photopolymer used to produce a positive working plate is different from the polymer used in the negative working plate as it is hardened before exposure [78]. The photopolymer used here becomes unstable when exposed to ultraviolet light and remains hard when no light strikes the polymer [78]. Plate processing is similar to negative plate except that the processor removes the exposed photopolymer from the plate and applies a thin layer of gum to protect the non-image areas from ink [78].
The three different types of plate that were investigated were all negative plates, i.e. diazo, photopolymer, and multigrained photopolymer, which was the standard plate used in all the other Heidelberg experiments. Diazo coatings are organic compounds that are used to make the presensitised plate. The unexposed diazo is dissolved by a solution and the gum deposits on the non-printing areas ensure water receptivity. Run lengths are relatively short with this type of plate.
The two other plates that were investigated were photopolymer type plates. The coating that is used to make photopolymer plates is made of organic compounds that are very inert and abrasion resistant. Once the plate is exposed to the UV light, the monomers polymerise to produce polymer. Photopolymer plates have a longer running capacity compared with diazo plates.
These two photopolymers only differ in that one is a Fujifilm patented photopolymer plates with additional micro grains on the aluminum surface to provide a better ink/water balance. The grain consists of a complex structure, consisting of primary grain, honeycomb grain and micropores on an aluminium support [79]. The primary grain helps control tone reproduction and ensure excellent water receptivity, secondary grains (honeycomb grains) contributes to the property of high scum resistance and tertiary grains (micropores) provide desirable printing qualities to the plate, such as optimum ink to water balance and high non-image area wear resistance [80].
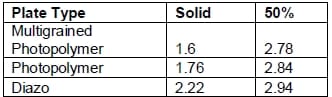
Table 5. 25. Lint in g/m2 of 7000 copies printed.
The effect of the printing plate towards lint was investigated. The printing trials were done under the standard conditions described in Table 3. 4 with black coldset Toyo tack 4 inks with chessboard pattern dots (square) printed on the bottom side of 52 gsm Norstar.
From the results above, it can be seen that multigrain photopolymer plate resulted in lowest lint results, photopolymer came second and diazo resulted in the highest lint. However since these data came from a single measurement, more experiments and analysis of variance are required to confirm this result. It may be that the multigrain plates allow water hold up better than the other two plates therefore a higher level of fountain solution emulsification is possible, which would lower the ink splitting force and the ink tack.
From observation, it was noticed that after 7000 copies had been printed, both the diazo and photopolymer plates were starting to wear out. This is shown in Figure 5. 31 and Figure 5. 32 below and can be seen by a lighter colour area across the plate as in comparison with Figure 5. 30. The Fuji Multigrain plate is the regular plate that is generally used for the other experiments and normally this plate does not start to wear out until it has done more than 100,000 copies. As can be seen in Figure 5. 33 the multigrain plate has not worn out after 42,000 copies were done.
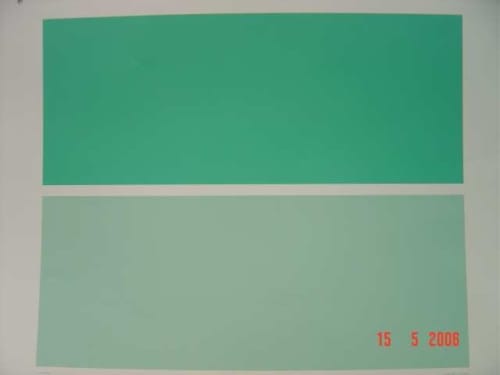
Figure 5. 30. Diazo plate before 7000 copies were printed
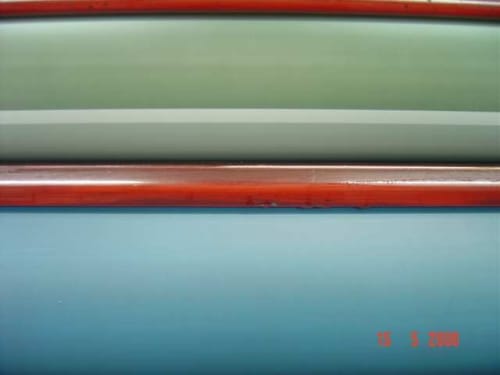
Figure 5. 31. Diazo plate was worn out after 7000 copies were printed
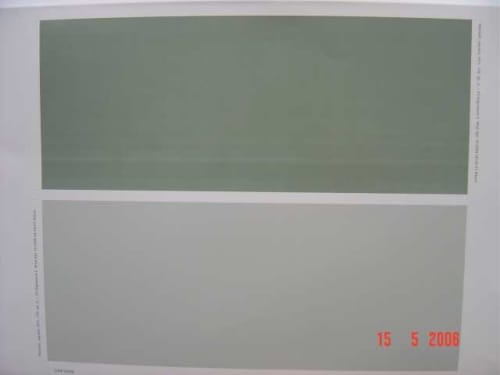
Figure 5. 32. Photopolymer plate started to wear out after 7000 copies were printed
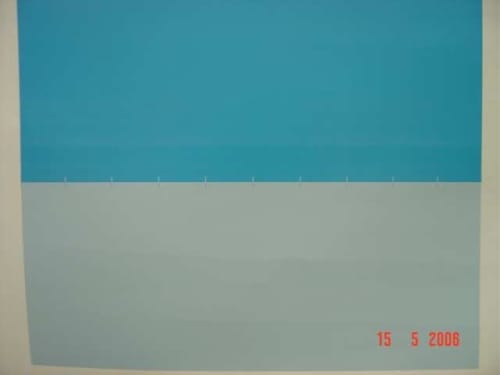
Figure 5. 33. Photopolymer Fuji Multigrain after 42,000 copies were printed
5.3.3 Effect of Ink Coverage (Printing Tone)
Figure 5. 34 shows the effect of printing tone for the Man Roland Uniset third trial averaging results with the Toyo black inks of tacks 4, 9 and 13.5 (section 3.2.2.2.3 and appendix G). The paper printed was Norstar batch F. Each data point is the average of the lint measurements obtained for the combined set of three ink tacks and two print couples. For comparison, results are also shown from a series of measurements with different ink coverage made on the Heidelberg GTO-52 press with the Toyo black tack 4 ink. The press conditions are given in Table 3. 4. These measurements were for printing the bottom side of the Norstar batch C that was tested. Please note that only 7000 copies were printed for Heidelberg compared with 25,000 for the Man-Roland. Each data point of the Heidelberg result is an average of two experiments. All 3 data sets show identical trends, with the 25% tone always yielding the highest.
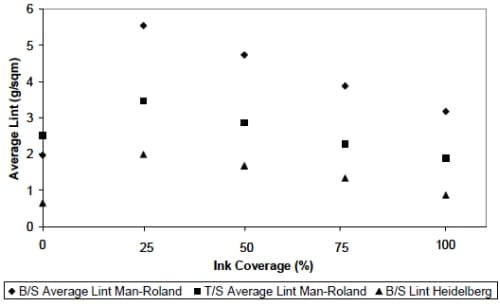
Figure 5. 34. The Effect of Ink Coverage on Linting
Table 5. 26 shows the average lint results for printing trials where printing screen tone was varied. 20-25% printing screen tone gives the highest lint results, followed by the 50%. The results are very clear and consistently show that on average the non-image area lint was then the third highest, followed by the 75% screen tone and the solid. This means that fountain solution is also a quite important contributor to linting. The reason why 25% printing screen tone resulted in the highest lint may be because the ink in the image area has more room to spread to the non image area than the 50% or the 75% printing screen tone. This phenomenon is not desirable as the printing result will not be delivered to the exact printing screen desired, something that is called dot gain. As a result of dot gain, the ink on the plate is thinner and is the ink film transferred to paper. According to Equation 2. 2, the thinner the ink film transferred to the paper, the higher the porous ink force if all other parameters are kept constant although the thinner free ink film produces a lower tack force (Chapter 5.2.4.8). While Equation 2. 3 will behave accordingly to the ink splitting behaviour to respond whether the free ink flow force increase/decrease with the decrease of thickness of the ink film on the plate. Therefore, 25% printing screen tone must have resulted in such a combination of forces so that the resultant effect of the three forces, namely tack force, ink porous force, free ink film force to linting is a maximum.
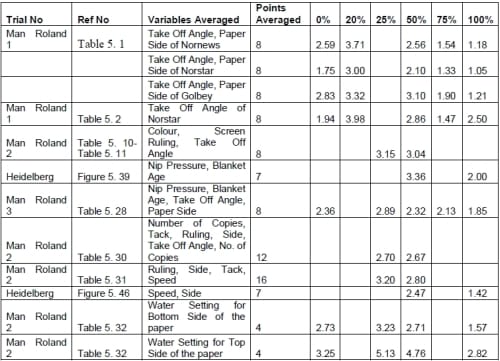
Table 5. 26. Effect of Printing Screen Tone
Figure 5. 35 shows the lint particle size distributions for the Heidelberg lint data shown in Figure 5. 34. Lint particle size distributions with different printing tones were also shown in Figure 5. 12 – Figure 5. 14 (Man-Roland Uniset third trial, with 153º take-off angle, varying printing screen tone). The data show no great differences in the size distributions of the lint particles produced with different screen tones, except that the non-image area lint is always smaller than the image area lint produced at any screen tone.
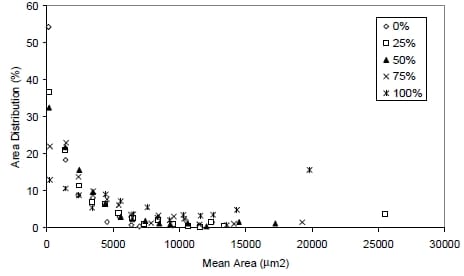
Figure 5. 35. Heidelberg Lint Area Distribution of Different Screen Tone- Norstar 52 gsm, bottom side, tack 4.
</div >5.3.4 Blanket Age and Blanket Nip Pressure
The effect of blanket age and nip pressure experiment was tested with both the Heidelberg GTO-52 and the Man-Roland Uniset. With the Heidelberg GTO-52, an old blanket, a medium-aged and a new blanket were used for this experiment. Both the blanket used for Heidelberg GTO-52 (Brand: Seaga CMD2) and the one that is used for the Man-Roland Uniset (Blanket Maker: MacDermid, Graffity thickness of 1.96±0.01 mm.) are compressible. The blanket experiment in the Man-Roland Uniset was done by swapping the old blanket for a new blanket and investigating the effect on linting. The nip pressure of the old blanket and the new blanket were also measured.
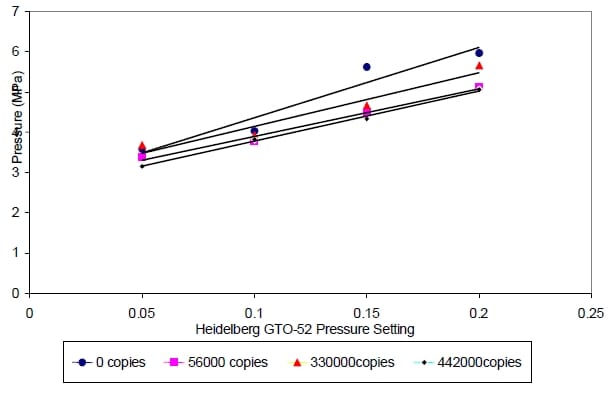
Figure 5. 36. Comparison of blanket age with the blanket pressure of Heidelberg GTO-52
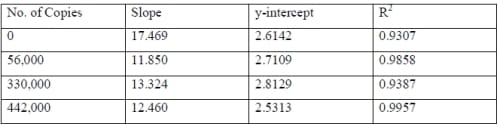
Table 5. 27. Linear Fitting Parameters for the Relationship between Nip Pressure and Impression Dial Setting for Heidelberg GTO-52
The relationship between Heidelberg pressure setting and nip pressure measured using the Fuji Prescale tape is shown in Figure 5. 36. The fitting parameters to each data set are given in Table 5. 27. The pressure setting in the x axis is the pressure setting that can be adjusted in the Heidelberg GTO-52 machine. This is the nip pressure setting between the impression and the blanket cylinder. 0 and 56,000 copies were done with the same blanket. The medium aged had printed 330,000 copies while the old blanket had printed 442,000 copies. The rate of increase of the pressure is shown by the slope of the graph, while the y-intercept shows the nip pressure setting at an impression dial setting of 0.
The measurements on both the old blanket (442,000 copies) and the new blanket (56,000 copies) were done immediately after 7000 copies were done. However the measurement with the medium-aged blanket, that had printed 330,000 copies, was done after the blanket had been allowed to rest for about a month. It is possible that the blanket has recovered some of its thickness during the time it was rested. That may be the reason why this blanket produced so much higher pressure compared with that of the new blanket that had only printed 56,000 copies. This result is surprising and needs further investigation. It is recommended for future work to test whether the 330,000 blanket will produce a more expected result if it is run to reach stability before the pressure measurement is done.
The results in Table 5. 27. shows that there is a rapid decrease in the blanket compressibility from the new blanket (0 copies) to 56,000 copies therefore there is quite a big difference in the pressure between both of them, at a given press setting. After 56,000 copies, the compressibility of the blanket seemed to settle. As can be seen from Figure 5. 36, pressure lines, for the blankets that had printed 56,000 and 42,000 copies, are close to each other.
The reason of the change of pressure with the number of copies the blanket has done is that the pressure setting actually sets a position of impression cylinder relative to the blanket cylinder. This is an absolute position and does not take into account any compression of the blanket and so as the blanket compacts with increasing number of copies printed, the pressure drops as a result.
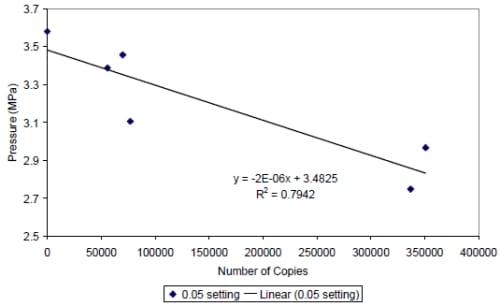
Figure 5. 37. Blanket effect on pressure drop at Heidelberg GTO-52 pressure setting of 0.05
This pressure drop with blanket age is shown in Figure 5. 37. for a pressure setting of 0.05, which was the standard pressure used for the trials in this thesis. There is a linear relationship between the pressure and the number of copies done by the blanket. More pressure measurement experiments during the aging of the blanket need to be done to complete the shape of Figure 5. 37. Due to the limitation of time, this could not be completed in the current study. However this should be done as part of future work.
The effect of blanket age to linting was then investigated by doing printing trials with the standard conditions shown in Table 3. 4. by using the old blanket and the new blanket alternately. The new blanket has done between 0 to 56,000 copies while the old blanket has done around 442,000 copies. For the same nip pressure and 50% printing screen, the old blanket produced slightly more lint compared with the new one. This is the opposite for the solid (100%) printing screen tone, i.e. the old blanket produced lower lint than the new blanket.
The relationship between lint and absolute pressure shows a lot better correlation as shown by Figure 5. 39 compared with the relationship between lint and the pressure dial in GTO-52 as in shown by Figure 5. 38. Thus, it can be concluded that simply using the machine blanket setting to compare lint result is not a good practice since the same pressure setting actually means different nip pressure for both the new and old blanket.
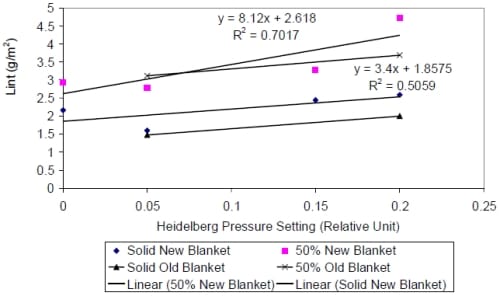
Figure 5. 38. Relationship between Lint and GTO-52 Pressure Setting Relative Dial of B/S of Norstar
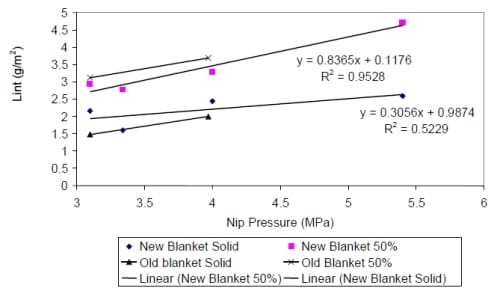
Figure 5. 39. Relationship between Lint and Absolute Pressure of GTO-52 of the New Blanket of B/S of Norstar
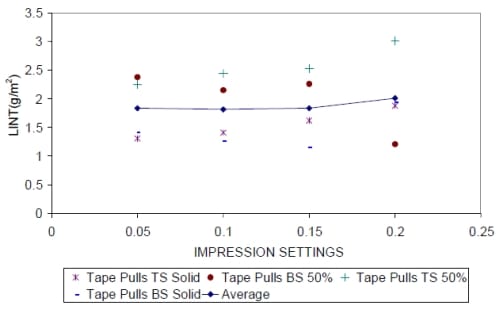
Figure 5. 40. The Effect of Impression Settings (Nip Pressure) towards Lint of Heidelberg GTO-52
The effect of nip pressure setting on lint of the Heidelberg GTO-52 in Figure 5. 40 was not so strong although a small increase of lint was observed with the increase of pressure setting. It was noted that the blanket was a very old one that had done around 700,000 copies when the experiments were done. This may be one of the reasons why there was not a lot of effect of pressure nip change between the impression setting 0.05, 0.1, 0.15 and 0.2. The actual pressure was not measured at the time of experiments. However it could be expected that having run 700,000 copies, the nip pressure variation would not be that much between those four impression settings.
The effect of pressure was also investigated in the third Man Roland trial. A full set of measurements with different take-off angles was completed with old blankets and then repeated after the blankets had been changed for new blankets. The change in blanket increased the nip pressure from 5.5 MPa to 9.5 MPa. The results are shown in Table 5. 28.
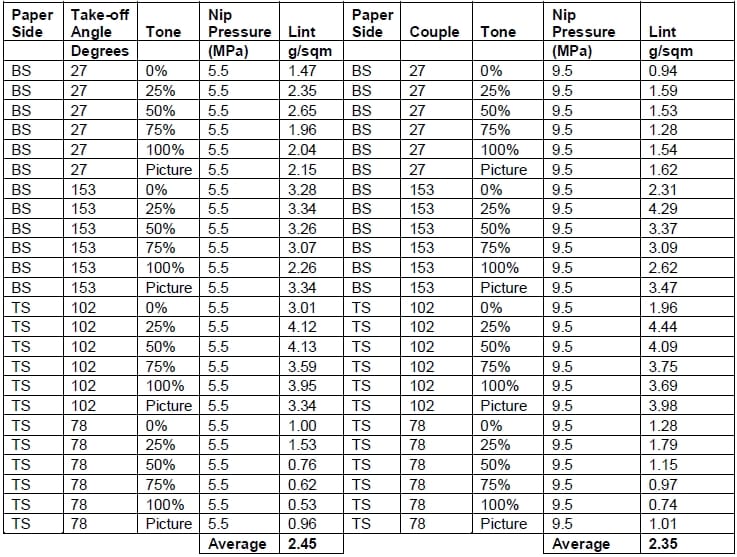
Table 5. 28. The effect of Pressure towards Lint (Third Trial Man-Roland Uniset)
The data in Table 5. 28 show that the effect of printing pressure towards lint was not strong. In fact, the analysis of variance given in appendix C also showed that pressure was not a significant variable towards linting (Table C1). Changing the old blanket for a new blanket which increased the pressure from 5.5 MPa to 9.5MPa actually decreased the lint averaged over four take off angles, printing tone, and two paper sides by 4%.
Another point to note is that the variation of the thickness of the blanket in Man-Roland Uniset trial. The new blanket was manufactured by MacDermid, Graffity and had a stated specification thickness of 1.96 ±0.01 mm. However, after 2 years old age on a press that was sometimes only running a half web, there were variations in the thickness of the old blanket that we measured using caliper.
On the top left blanket the measured thickness were 1.94, 1.90 & 1.91 mm at one
edge and 1.95, 1.93 & 1.98 mm at the other. Middle point of the blanket gave thickness readings of 1.98, 1.98, 2.03, 1.99, 2.00 and 2.05 mm. For the bottom left blanket the measured thickness were .97, 1.94 & 1.95 mm on one side and 2.10, 2.00 and 2.08 mm on the other. There will be variations of pressure across the blanket since the thicknesses of the blanket are not uniform across and this could contribute to the experimental error although it has been statistically proven that pressure was not a significant variable towards linting.
5.3.5 Lint Movement from Blanket to Plate
As discussed in Chapter 5.2.1, the lint weight result showed that the lint did not increase so significantly with the increase of ink tack from 4 to 6 and then to 9 and then increased quite significantly when the tack was increased to tack 13.5. However, from observation the amount of lint on the plate was significantly different between ink tack 4, 6 and 9. It is important to understand how much lint is transferred back to printing plate since it causes the deterioration of image quality as it interferes with ink transfer in the image area. It was observed that the higher the ink tack, the more lint transferred from the blanket to the plate. Therefore, the lint area size distribution on the plate and blanket were investigated with the Man-Roland Uniset third trial. Tape pulls and Domtar samples were taken from both blanket and plate to find the weight and lint area distribution comparison between both of them. The results are shown in Table 5. 29.
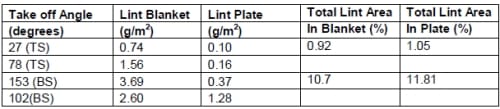
Table 5. 29. Distribution of Lint in Plate and Blanket with the Take Off Angle Effect of Black Coldset Tack 4 Ink of Top and Bottom Side of Norstar and Total Lint Percentage Area in Blanket or Plate
In Table 5. 29, the lint percentage area is higher in plate compared with that on the blanket, although it also shows that the lint weight is lower in plate compared with that on the blanket. This suggests that lint on the plate has a larger area size compared with the lint on the blanket. This hypothesis is confirmed by the lint particle size measurements shown in Figure 5. 41 and Figure 5. 42.
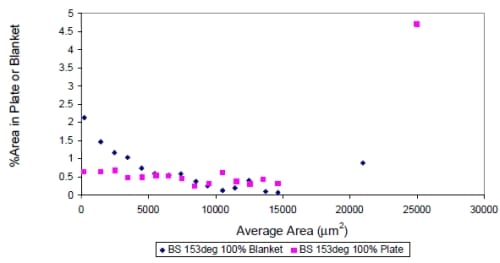
Figure 5. 41. Blanket and Plate Lint at 153 degrees Take-Off Angle
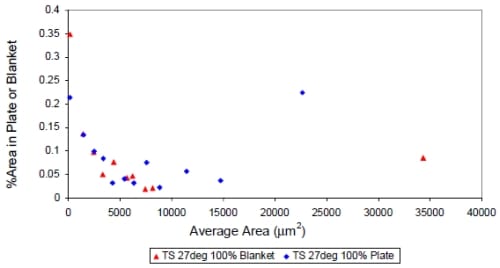
Figure 5. 42. Blanket and Plate Lint at 27 degrees Take-Off Angle
From the area size distributions, it could be seen that the transfer of lint from the blanket to the plate occurs at a higher rate at a larger particle range (larger than 10,000 µm2 for Figure 5. 41 and larger than 7,000 µm2 for Figure 5. 42). For lints that are smaller than this range, the lint tends to stay on the blanket rather than to be transferred to the plate.
Due to limitation of time, only lint of tack 4 experiment from blanket and plate was sampled. In the future, the same experiments with higher ink tack needs to be done to investigate the effect of ink tack to lint transfer behaviour from blanket to plate.
5.4 Press Operating Conditions
Different printing conditions will affect linting results. The printing parameters that will be examined in this sub-chapter are the number of copies, speed, and paper web take off angle.
5.4.1 Number of Copies
Heidelberg GTO-52 experiments were done to investigate the effect of number of copies printed on to linting. The standard conditions used followed Table 3. 4, only the number of copies and ink tack variables were changed. The results for the black web-fed tack 4.6 are shown in Figure 5. 43 while the corresponding results for the sheet-fed tack 13.5 inks are shown in Figure 5. 44.
Solid lint seemed to be following a linear relationship with the number of copies for both of the inks. The rate of lint build up and the lint weight of the solid area printed with the tack 4.6 ink are lower compared with that of the tack 13.5 ink. However, the development of lint for the 50% screen is different for the two inks. The lint with the coldset newspaper ink of tack 4.6 (Flint) is still increasing linearly at 7000 copies while for the sheet-fed tack 13.5 ink (Colortron) the lint has reached a plateau. This means that the rate of accumulation of lint is zero, i.e. the rate of lint transferred to the blanket is equal to the rate of lint transferred from the blanket [51].
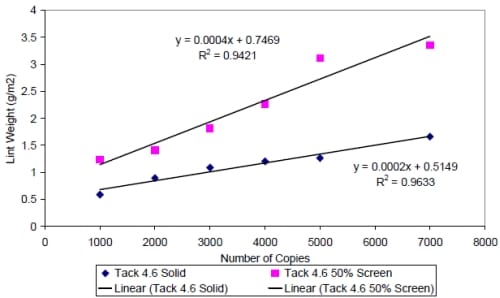
Figure 5. 43. Black Flint Coldset Web-Fed Inks Run in Heidelberg GTO-52
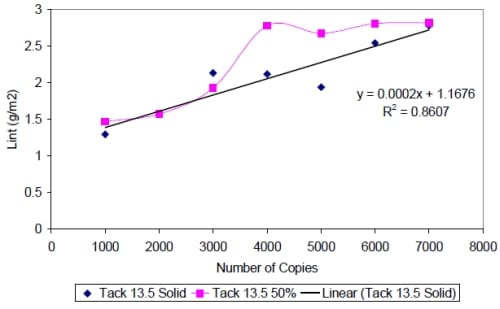
Figure 5. 44. Black Toyo Coldset Sheet-Fed Inks Run in Heidelberg GTO-52
The effect of number of copies was also examined in the Man Roland Uniset second trial. The trial was printing with 25000 copies per hour using black tack 4 and tack 6 Toyo inks. There were three runs, i.e. printing for 7000, 15000, and 23000 copies. The lint was collected at the end of the run and was compared among the three runs. The results are shown in Table 5. 30.
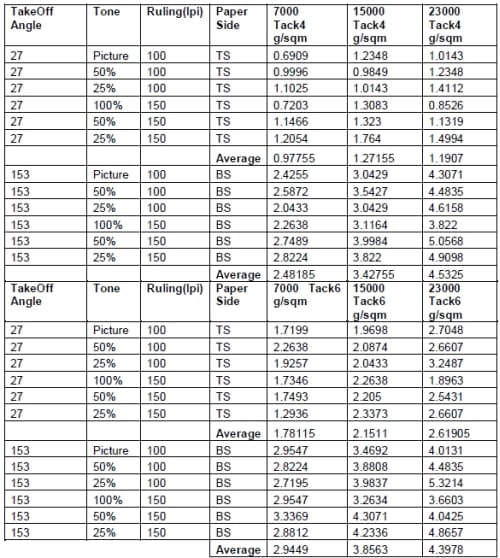
Table 5. 30. Man-Roland Second Trial Number of Copies Effect towards Linting of Man-Roland Uniset Second Trial.
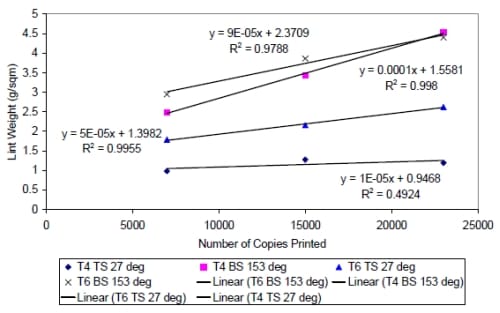
Figure 5. 45. Average Lint of Table 5. 30 of Man-Roland Uniset
The average results of Table 5. 30 are plotted in Figure 5. 45. All the data sets in the figure show a linear increase in lint with the number of copies printed. Both sets of measurements at the lower take-off angle, i.e. 27º with tack 4 and 6 resulted in lower lint compared with the corresponding measurements at 153º. They also have lower slope, i.e. lower lint rate accumulation, compared with those of 153º.
5.4.2 Speed
The effect of speed on lint was tested in the Man Roland Uniset second trial (Chapter 3.2.2.2). Two speeds were done, i.e. 12500 and 25000 copies per hour. The results are shown in Table 5. 31. Analysis of variance showed that speed was a significant variable affecting linting. The ANOVA can be referred to in Appendix B.
From Table 5. 31, it was clearly seen that an increase in speed also increases the lint, especially for the higher ink tack. This may be the result of the higher free ink film thickness due to the higher of the printing speed (chapter 5.2.4.5), which increases the ink tack force (chapter 5.2.4.1, 5.4.2.2). However, there was one set of data that suggested the opposite, i.e. top side of the paper, tack 4 suggested that 12,500 copies per hour speed produced higher lint than the 25,000 copies per hour speed. The reason for this is not currently understood and should be a part of the future work that needs to be done.
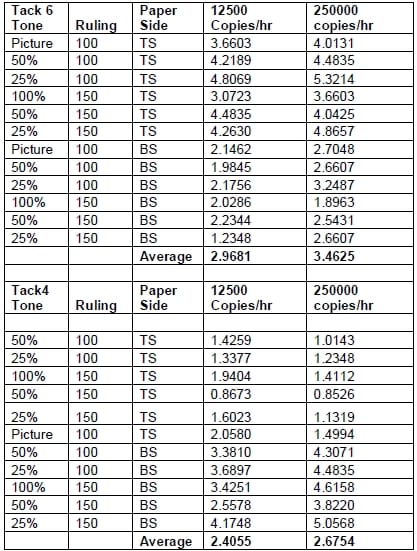
Table 5. 31. Man-Roland Uniset Second Trial Speed Experiment on Linting.
Heidelberg trials were also done to investigate the effect of speed. These measurements were done with the tack 4 ink from Toyo and Norstar batch C. Otherwise, the conditions were as shown in Table 3. 4. The results are shown in Figure 5. 46. The results suggest a slight decrease in lint as the speed is increased, which was the reverse effect to what was generally found in the Man Roland Uniset Trials.
Heidelberg GTO-52 has runnability problems when it is run at a lower speed than 8000 copies per hour. 6000 copies per hour is the minimum speed that could be run without producing severe paper jams. This suggested that the variabil
ity of the results between the four series shown in Figure 5. 46 was probably due to these runnability issues of this particular press rather than any intrinsic effect of speed.
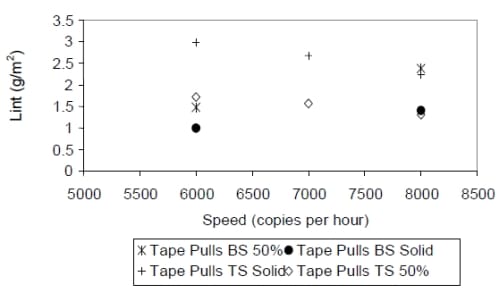
Figure 5. 46 . Effect of Printing Speed Towards Lint of GTO-52
5.4.3 Take Off Angle and Paper Side
The effect of take-off angle and paper side were investigated in the second and third Man-Roland Uniset trials.
Figure 5. 47 shows the effect of side and take-off angle from the second Man-Roland Uniset Trial. These results were generated by averaging all of the data obtained for each take off angle and paper side. Thus each point shown here is the average of fifteen data points as five different screen tones and three different ink tacks were tested for each combination of take-off angle and paper side. The critical importance of these two factors acting together is indicated as the highest average lint result (bottom side with take off angle of 153o) is approximately five times the smallest average lint result (top side with take off angle of 27o). Please refer to table B3 in Appendix B and Table C1 in Appendix C that showed that take-off angle and the combination of take-off angle and side were the most significant variables affecting linting. The data in Figure 5. 47 also shows that the top side of the paper tends to give more lint than the bottom side but the effect cannot be quantified as a different set of measurements, i.e. different take-off angle, were done for each side.
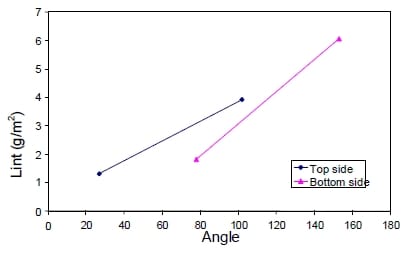
Figure 5. 47. Effect of Paper Side and Take-Off Angle from the Second Man-Roland Uniset Trial
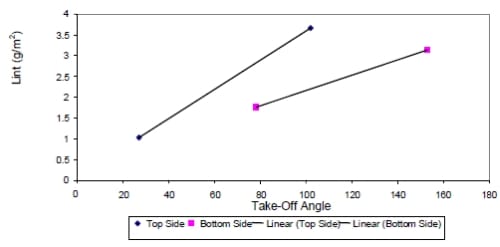
Figure 5. 48. Effect of Take-Off Angle and Paper Side of Man-Roland Uniset Third Trial
Figure 5. 48 is the average lint of Man Roland Uniset third trial using black Toyo ink of tack 4 with two pressure settings, i.e. 5.5 and 9.5 MPa and five printing tones. The data also shows the effect of take-off angle and paper side. The top side of the paper still produced more lint compared with that of the bottom side of the Norstar 52gsm. Again the higher take off angle for both bottom side and top side of the paper resulted in higher lint, i.e. three and a half times for the T/S and twice for the B/S, when comparing the lower take-off angle with the higher.
Figure 5. 47 and Figure 5. 48 shows that lint weight increases with the increase of takeoff angle regardless of paper side. Figure 5. 10 and Figure 5. 11 show the size distributions for the lint distributions obtained at different screen tones with the tack 4 ink of the Man Roland Uniset third trial. The data from the experiments with the 27º take-off angle is shown in Figure 5. 10., while Figure 5. 11 shows the size distributions of the lint from the 153º take-off angle experiments.
Figure 5. 10 and Figure 5. 11 show that the higher take-off angle has produced heavier and larger lint. For the data collected at 27o take-off angle, nearly half of the total area of lint is in the smallest size class, while for the highest take-off angle, the largest area class contains by far the most lint, except for the non-image area (0% print tone) lint.
The side with the higher take-off angle has a higher rate at which the blanket surface and the paper will separate coming out of the printing nip, provided all other press variables are constant. It seems likely that the change in the take-off angle increased the force imposed on the surface, which in turn increased the amount of lint and the size of the lint particles.
This hypothesis was tested using a Prüfbau Deltack with an ultra-low force sensor with a range of 0.2-1.4 N. While the printing nip configuration is fixed in the instrument, it is possible to simulate a change in take off angle by altering the speed at which the tests are conducted (Chapter 3.1.1).
The Deltack experiments (Chapter 5.2.6) showed that the tack force required to split the free ink film was strongly related to the print speed. The increase in tack force with print speed arises both from an increase in the force required to split the ink film, as speed increases, as well as an increase in the thickness of the ink film that is split. The ink film thickness increases at higher speeds as the printing cylinder has less time in contact with the paper and thus less ink will enter the pores, leaving a thicker free ink film requiring more force to split. Measurements made on the Deltack have shown that the tack force increases as more ink is used for printing, but all other conditions are held constant.
On any given press, the ink-film splitting rate will depend on the diameter of the printing rollers, the rotational speed as well as the take-off angle itself.
Figure 5. 35 shows the lint distributions measured for different screen areas for the Heidelberg experiments. These can then be compared with the size distributions produced in the Man Roland Uniset, for the take-off angles of 27o and 153o shown in Figure 5. 10 and Figure 5. 11, respectively. The data in these figures show that the size distributions of lint produced by the Heidelberg sit between those produced at 27o and 153o on the Man-Roland Uniset. The Heidelberg produces lint distributions in which the smallest lint particles still comprise the largest percentage of the total area, but in which there are some lint particles in the largest area class. This is consistent with the estimated take-off angle of the Heidelberg press of 70o.
5.4.4 Fountain Solution Consumption Effect to Linting
It was not fully understood before whether fountain solution would actually increase or decrease lint. Fountain solution decreases process ink tack while weakening paper surface strength at the same time.
The second Man-Roland Uniset trial was used to investigate the effect of fountain solution consumption on linting. The experiment was done by printing a full-web (810mm width) of paper and having exactly the same pattern in the left and right hand side, but applying a higher fountain solution level on the left side and applying a lower level of fountain solution on the right side. The plate consisted of solid area, 25% and 50% printing tone with 150 lines per inch screen lining and non-image area. The rest of the experiment conditions followed Table 3. 4. The terms higher and lower are relative to the printing condition at the time of the trials. At the “higher” level water setting, the ink and water level settings were chosen by the operators so that the print densities were close to the targets. From these settings, the water settings were then decreased to the lowest possible without producing scumming, i.e. where ink starts printing in the nonimage area because of the lack of fountain solution). This fountain solution setting was then called ‘lower’ setting. The numbers were the values set in the Man-Roland Uniset system that controlled the amount of water or ink delivered to the inking/fountain solution rollers.
The results of this experiment are shown in Table 5. 32. Some results in Table 5. 32 were negative values, this means that the amount of lint removed from the blanket to the adhesive tape was less than the amount of the adhesive that was removed from the tape to the blanket. This can occur for tape pulls method where only a small amount of lint exists on the blanket. Therefore for the negative numbers, it was assumed that no lint was removed from the blanket and the value was set to zero.
From Table 5. 32, it can be seen that a decrease of fountain solution setting resulted in a decrease of lint in the non image area but resulted in an increase of lint in the image area. This is expected as fountain solu
tion can decrease process ink tack resulting in lowering the lint in the image area but at the same time it weakens paper surface strength therefore it increases lint in the non-image area. Therefore the decrease of fountain solution usage in offset lithographic printing will increase lint when the printing area is solid or dominated with image area, i.e. 100% and 50% printing tone and will act the opposite way when the printing area is dominated with non-image area or blank, i.e. 0% and 25% printing tone.
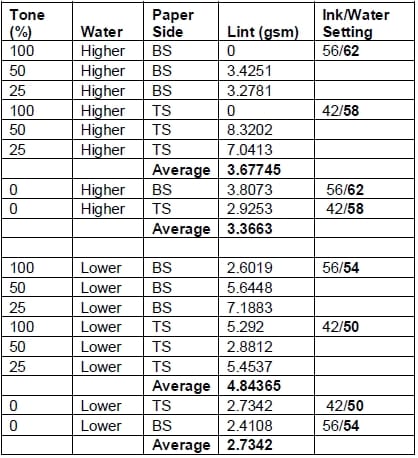
Table 5. 32. Fountain Solution Effect on Linting on Man-Roland Uniset Second Trial (150 lpi ruling)
A set of experiments was done with GTO-52 to investigate whether fountain solution in printing increases or decreases lint. The experiments used Norstar batch C and the Toyo black tack 4 ink. Except as noted below, the conditions of the experiments were as listed in Table 3. 4. In order for us to do that, the GTO-52 plate was divided into 2 exactly the same areas at the top and bottom of the plate each with the same printing screen tone, i.e. 0%, 25%, 50%, 75% and solid area. 1500 copies were printed under lower water levels (water setting of 7, ink setting of 7 GTO-52) and then tape pulls and Domtar lint collection were done in the bottom half of the area. The lint measured under these conditions is referred to as AL. Another 1500 more copies were then printed but running at higher water levels (water setting of 9 and ink setting of 7), and the lint was measured with the tape pulls and Domtar on both top and bottom side of the blanket. The lint collected from the bottom side of the blanket was labeled AH while the lint collected from the top half of the blanket was labeled BL+H. The water setting of 9 was the standard setting used for all the other Heidelberg experiments. AH was sampled in the bottom side of the blanket, which is at the same place where AL had been sampled.
The lint collected in AH would have been the same as the amount of lint accumulated starting from a fresh blanket (0 copies) since the lint would have been totally removed in this area with tape pulls and Domtar blanket washing, when the AL lint was collected. Lint collected in BL+H is positioned at the top blanket area and this would be the accumulation of the lint resulted from 1500 copies with the lower water setting and another 1500 copies with the higher water setting. AH is measured on exactly the same position as AL and so the ratio of AH/AL gives the change in lint deposit rate due to the increase in water. If the experimental conditions are selected correctly then the lint measured with AH should also have been laid down at B, i.e. AL=BL and AH=BH
Control experiments were done by printing 1500 copies with lower water levels (water setting of 7, ink setting of 7 GTO-52) and then tape pulls and Domtar lint collection were done in the bottom half of the area. The lint measured under these conditions is referred to as AL1. Another 1500 more copies were then continued to be printed with the same water setting (water setting of 9 and ink setting of 7), and the lint was measured with the tape pulls and Domtar at different areas on both top and bottom side of the blanket. The lint collected from the bottom side of the blanket was labeled AL2 while the lint collected from the top half of the blanket was labeled BL1+L2. AL2 was sampled in the bottom side of the blanket, which is at the same place where AL1 had been sampled.
In this case, the lint collected in AL2 would have been the same as the amount of lint accumulated starting from a fresh blanket (0 copies) since the lint would have been totally removed in this area with tape pulls and Domtar blanket washing, when the AL1 lint was collected. Lint collected in BL1+L2 is positioned at the top blanket area and this would be the accumulation of the lint resulted from the 3000 copies in total with the water setting 7 throughout the whole experiment. As AL2 is measured on exactly the same position as AL1, therefore, AL1= AL2. If the experimental conditions are selected correctly then the lint measured with AH should also have been laid down at B, i.e. AL1=BL1 and AL2=BL2
It is well-known that lint movement is dynamic. The accumulation of lint on the blanket equals the difference of the deposition of lint from the paper to the blanket and the redeposition of the lint back to the paper from the blanket [51]. Thus some of the lint BL or BL1 would have been removed in the subsequent printing of 1500 copies. If we denote the lint from BL remaining after printing the extra copies as BL*, then we can write BL* = BL+HAL and if we denote the lint from BL1 remaining after printing the extra copies as BL1*, then BL1*= BL1+L2 – AL2.
If the increase in water was associated with re-deposition of lint onto the paper, then BL*/AL < BL1*/AL1. Thus doing this experiment would allow us to probe the role of the fountain solution in detail. Possibly some of the contradictory information as to the importance of fountain solution might be because it may be simultaneously true that AH > AL and BL*/AL < BL1*/AL1, i.e. more fountain solution increases the rate at which lint is removed from the paper but also reduces the time that the material stays on the blanket.
The results of the experiments are shown in Figure 5. 49, Figure 5. 50 and Figure 5. 51 . Each figure shows 10 data points from 5 printing tones and the two sides. Figure 5. 49 shows that the amount of lint accumulated was lower after the water setting increased. The trend line shows that AH was on average only 76% of AL. This means that more fountain solution decreases the rate at which lint is removed from the paper to the blanket.
Figure 5. 50 and Figure 5. 51 compare the lint accumulation of the first 1500 copies with the lint that remains on the blanket after 1500 more copies were done. Both data sets showed that between 40 % and 50% of the lint that had been deposited in the first printing of 1500 copies had been removed during the subsequent printing. The data showed poor correlations and therefore whether more fountain solution reduces the time that the material stays on the blanket was inconclusive.
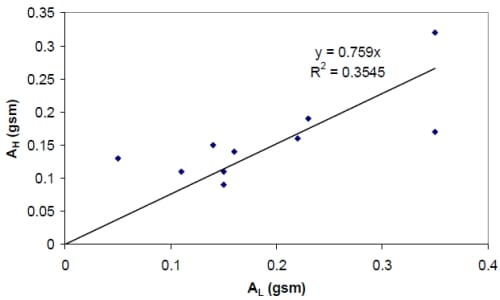
Figure 5. 49. Comparison of the lint accumulation of the first 1500 copies with lower water setting of 7 and the second 1500 copies with higher water setting of 9
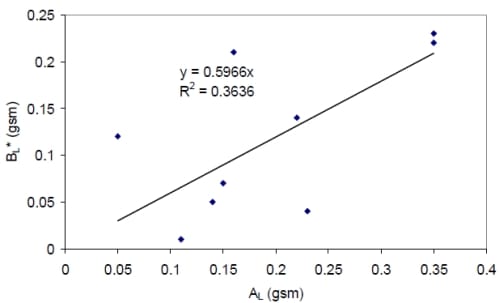
Figure 5. 50. Comparison of the lint accumulation of the first 1500 copies and the lint remains of AL1 after 1500 more copies
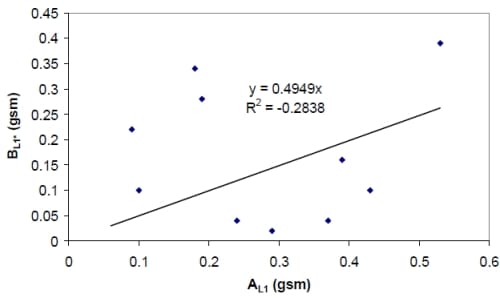
Figure 5. 51. Comparison of the lint accumulation of the first 1500 copies and the lint remains of AL1* after 1500 more copies. A water setting of 7 was used for printing both sets.
Thus it can be concluded from these experiments that the increase in fountain solution usage decreased the rate at which material had been pulled out of the sheet and more work needs to be done to investigate the effect of fountain solution on the time that the lint stays on the blanket.
5.4.5. Temperature Measurements across the Printing Blanket
Man-Roland Uniset blanket temperatures were measured w
ith the handheld laser thermometer for the third Man-Roland Uniset Trial (refer to 3.2.2.2.3). There were variations between the left of right blankets. The left hand side blanket showed 25.8 ºC- 26.3ºC while the right hand blanket showed 24.4ºC- 25.2ºC. It is not known at this stage how the temperature difference affect lint results in details and this is an area of work in the future that needs to be pursued.
6.0 Conclusions
In this thesis, the effect of paper and printing press variables were investigated. Paper variables were not looked into in so much detail compared with the printing press variables. The printing press variables were discussed in three main major parts: ink and fountain solution balance, printing press blanket/plate variables, and printing press operating condition.
The length and size distributions of lint from Man Roland Uniset, Man-Roland Geoman, Heidelberg GTO-52 and the IGT Pick Test were measured. The pick test removed far more lint than any of the commercial presses. The length and area of the lint was also much larger than the material removed as lint on commercial press. This disparity between the size distributions of the lint produced in the commercial printing and laboratory pick test suggests that the results of the pick test cannot be automatically assumed to be relevant to linting in commercial offset printing.
Lint increased greatly with take-off angle. The side with higher take-off angle has a higher rate of ink film splitting, since the side with the higher take-off angle separates further, compared with those of the other side with the same amount of time. The higher rate of ink-film splitting increases the stress that is applied to the surface of the paper, which in turn increased the amount of lint and the size of the lint particles.
Three different papers were investigated in this thesis, the paper labeled Golbey was Nornews produced by Norkse Skog France. The paper labelled Norstar and Nornews were produced by Norske Skog Boyer. Golbey produced the most lint, followed in order by Norstar and Nornews. Fines, fillers and recycled fibres are the paper components that can lint. Fines are desirable if they bond well with the fibres. However this may not be the case if fines are poorly bonded. From the configuration of the Boyer paper machine, with the horizontal twinwire former and a twinver press, it is believed that the top side of the paper ends up with more fines compared with the bottom side of the paper. However the work here showed that the top side of Norstar paper produced more lint than the bottom side. This suggested that the fines are not bonded too well in Norstar.
It was found that 20-25% printing screen tone gives the highest lint results, followed by the 50% screen tone. The results are very clear and consistently show that on average the non-image area lint was then the third highest, followed by the 75% screen tone and the solid.
Various printing parameters were tested to investigate their effect towards offset lithographic printing. Heidelberg GTO-52 and Man-Roland Uniset were used to do the printing trials. ANOVA Systat was done and showed that printing take-off angle, tack, print coverage (printing tone), two sidedness of the paper, paper type, printing speed and dot shape were among the significant print parameters affecting linting in offset lithographic printing. Screen ruling and printing pressure were not significant according to the ANOVA results.
Linting increases with speed, especially for the higher ink tack, in the Man-Roland Uniset. This may be the result of the higher ink film thickness due to the higher printing speed, which increases the ink tack force. This is found to be consistent with the Deltack results. In the Heidelberg GTO-52 trials, it was shown that the effect of speed towards lint was relatively small. Lint decreases as the speed increases. However this was not solely the effect of printing speed but also the effect of runnability issues at low speed.
Lint accumulation on blanket follows a linear relationship with the number of copies for both Heidelberg GTO-52 and Man-Roland Uniset trials. Some trials were also observed to reach a plateau when the rate of lint accumulation in the blanket is zero because the rate of lint transferred to and from the blanket are equal to each other.
Ink tack was found to have a relatively small effect on the amount of lint. There was no large difference in lint weight between ink tack 4, 6, and 9. However tack 13.5 gave a somewhat higher result. The size and area of the lint removed in the commercial presses did not depend on the tack of the ink, except at high take-off angle. Lint increased greatly with take-off angle. The amount of lint on the plate was significantly different between ink tack 4, 6 and 9. The higher the ink tack, the more lint transferred from the blanket to the plate. From the area size distributions, it could be seen that the transfer of lint from the blanket to the plate occurs at a higher rate for a larger particles size (larger than 7,000 – 10,000 µm2). Lint particles that are smaller than this tend to stay on the blanket rather than transfer to the plate.
The small effect of ink tack was explained as arising from the nature of the measurement of ink tack. Ink is shear thinning, i.e. shear viscosity decreases as the shear rate decreases, and the Inkometer used to determine ink tack measures tack at much lower shear rates compared to the shear rate in the printing nip of a commercial printing press. Measurements of apparent viscosity on the different inks showed that the viscosity values tended to converge at very high shear rates. Ink tack increases with the increase of ink film weight or ink film thickness as shown by the Inkometer and the Deltack. It was also shown that the higher the speed, the higher the ink tack is for both the Inkometer and the Deltack Ink tack also changes with the addition of fountain solution. Ink tack depends on the stability of the ink with the addition of the fountain solution. Once fountain solution is added, even tack 13.5 and tack 4 inks can behave similarly. The relationship between the Inkometer and the Hydroscope tack is linear but the slope and intersection with the y-axis are unique for each and individual ink colour and brand.
Tyvek water-proof paper experiment with two different brands of ink, four different ink tacks and with two different colours gave a variety of different fountain solution content in the process inks ranging from 7 – 17% (process ink sample from Heidelberg GTO-52). Higher fountain solution content in the process ink resulted in lower lint and a higher print quality. It was found that the higher the tack is, the higher the amount of fountain solution emulsified in the ink. Black tack inks also took up more fountain solution compared with the cyan ones. This agreed with the Man-Roland Uniset trial which showed that for the same tack number, cyan inks had been shown to result in higher lint weight compared with the black inks.
Thermo Gravimetric Analysis was concluded to be the most suitable method so far for the measurement of the fountain solution content in the process ink. Weight reduction measurement with TGA was quite simple to handle. Pure ink acts as blank sample. As the tack increased, the percentage of volatile component at 105ºC also increased slightly. The fountain solution content of process ink samples ranged from ~7%-12%. An increase in tack reduced the fountain solution content. The tack 4 ink had around 12% fountain solution content, tack 9 had around 10% while tack 13.5 had around 7% fountain solution content. These all are samples from Man-Roland Uniset. The TGA results were also found to be of a similar size with the Tyvek water-proof printing method used to measure the fountain solution content of the process ink in Heidelberg GTO-52.
There is optimum level of fountain solution for printing. Too little fountain solution will result in higher lint, possibly followed by sc
umming. Increasing fountain solution usage was found to increase the lint in the non image area but reduce the lint in the image area. More fountain solution increased the rate at which lint is removed from the paper.
Analysis of variance showed that pressure was not a significant variable towards linting in the Man-Roland Uniset trial. Swapping the existing blanket with a new blanket, which increased the pressure from 5.5 MPa to 9.5MPa, only increased the average lint of several take off angles, printing tones, and two sides of the paper by 4%. The Heidelberg GTO- 52 trials also showed that pressure did not strongly affect lint results. This is also consistent with the Deltack measurements of the effect of pressure on tack force.
For the Heidelberg trials, there was rapid decrease in the blanket compressibility from the new blanket (0 copies) to 56,000 copies. Therefore there is quite a big difference in the pressure, at a given press nip setting between both of them. After 56,000 copies, the compressibility of the blanket seemed to settle since the blanket after printing 56,000 and 442,000 copies produced the same pressure at a given setting.
Simply using the machine blanket setting to compare lint result is not a good practice since the same pressure setting actually means different nip pressure if the blanket age is different. The nip impression setting sets the distance between the impression cylinder and blanket cylinders, which does not take into account the effect of blanket ageing and blanket thickness reduction as the blanket ages.
From ANOVA done in Appendix H, it was found that dot shape was a parameter that has a statistically significant effect on linting. Circles produced more lint than squares and ellipses, respectively. More work needs to be done for line shape and dot orientation to confirm the observations.
The multigrain photopolymer plate resulted in the lowest lint, the photopolymer plate came second and the diazo plate resulted in the highest lint. More work needs to be done to confirm this since there was only one experiment on each plate for comparison. Also, after 7000 copies printed, it was noticed that after 7000 copies had been printed, both of the diazo and photopolymer plates were starting to wear out.
7.0 Future Work and Recommendations
Lint migration from the surface of the paper to the blanket, plate and then to the ink and fountain solution rollers needs to be further investigated. Lint in the ink and fountain solution rollers is harder to measure. However the dynamics of paper-blanket-plate lint migration should be done next. Some sort of dynamic lint measurement needs to be developed. A dynamic image analysis system would consist of a high speed and high resolution camera with image analysis. Ideally the image analysis should also to be done in real time as well. Some early work has already been done by Knut Wiik [51].
Variability within one paper grade needs to be further investigated. The differences between paper grades should also be tested. Paper machine variables, i.e. if there is change in any way the paper was made, needs to be noted carefully. This is important since changing parameters on the paper machine definitely changes the newspaper structure. The link between the sheet structure and lint needs to be examined closely.
The amount of lint is at maximum at 25% screen tone. More work needs to be done in order for us to understand why the curve goes through maximum at the 20-25% printing screen tone, followed by the 50%, non image area, 75% and solid.
More varieties of printing plate and printing blanket type should be investigated further. It would be worth examining the surface chemistry of the printing blanket and printing plate with AFM to get the topography of the plate and the blanket. Physical properties such as the compressibility and the tensile strength of the blanket would also be interesting to measure.
Different ink and fountain solution chemistry composition could be investigated. Other ink colours could also be investigated. The main components affecting ink tack and therefore affecting lint mainly should be identified. Inks with same tack number often behave differently towards linting. This needs to be investigated. The reason why coldset and sheet-fed inks result in different linting should be investigated.
Ink tack change with the addition of fountain solution and with the change of speed, ink film thickness and printing nip pressure needs to be correlated better with the commercial offset lithographic press. Ideally, if the % of the fountain solution in the process ink is known, the ink film thickness, speed and the nip pressure are all known in the commercial printing press, the lint produced will be able to be predicted with a good model or with the lint library results collected from the trials.
Thermal Gravimetric Analysis is considered to be the most suitable equipment to measure fountain solution content in process ink. A method of reproducibly collecting process ink from the plate or the last roller of the inking train needs to be developed. Another possible method of measuring the fountain solution content is by using the NPIRI water content meter [58]. A calibration curve between dielectric constant and the known fountain solution content in ink needs to be developed.
The measurement of fountain solution film thickness and ink degree of emulsification method research should be continued further. Measurement of fountain solution film on the plate can be done with an infrared moisture-meter, “Near Infrared KJT-100 moisturemeter [57] that has been used in Norske Skog, Boyer. However, a calibration graph between the moisture-meter and the fountain solution film thickness still needs to be obtained. This could be done by smearing emulsified process ink with almost the same ink thickness applied in the commercial press (1-2µm). The process ink fountain solution content has to be known beforehand so that the correlation graph between the moisturemeter number and the fountain solution free film thickness can be developed.
The relationship between image quality and the amount of lint should also be investigated, as linting is ultimately an issue to printers because of its effect on image quality.
APPENDIX A. First Trial Man-Roland Uniset ANOVA Systat
Independent Variables:
PAPER$: Norstar, Golbey and Nornews
SCREEN$: 0%, 20%, 50%, picture and 100%
COLOUR$: Black, Cyan, Magenta, Yellow
SIDE$ : Top side and bottom side
ANGLE: 75º, 105º
Dependent Variable
LINT (g/sqm)
N: 80
Analysis of Variance
Table A. 1. ANOVA of Man-Roland First Trial
Based on Fisher, R.A.“ Statistical Tables for Biological, Agricultural, and Medical Research [76], the F ratio was checked at 0.05 significance level according to its degree of freedom and 12 degree of freedom error. The f ratios that are in bold are the factors and interactions between factors that are significant to linting.
Statistically, there are two and three ways interaction that affected lint significantly. However this will need further study to confirm and to explain this further.
APPENDIX B. Second Trial Man-Roland Uniset ANOVA Systat
Independent Variable:
TYPE$ (3 levels)
100%, 25%, 50%
SIDE (2 levels)
1, 2
RULING (2 levels)
100, 150
COPIES (3 levels)
7000, 15000, 23000
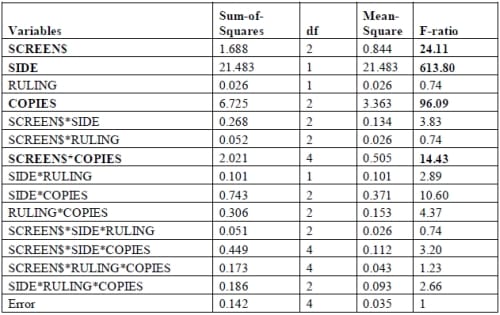
Table B. 1. First ANOVA of Second Man-Roland Uniset Trial
From the table above, it was concluded that screen ruling was not a significant factor towards lint. While printing screen, paper side and the number of copies printed were significant factors
to linting. Two ways interaction between screen$ and the number of copies were also significant.
PRINTCOUPLE (2 levels)
Top print couple, bottom print couple
Screen$ (5 levels)
0%, 100%, 25%, 50%, Picture
SIDE (2 levels)
Top side, Bottom side
WATER (2 levels)
Low , Normal
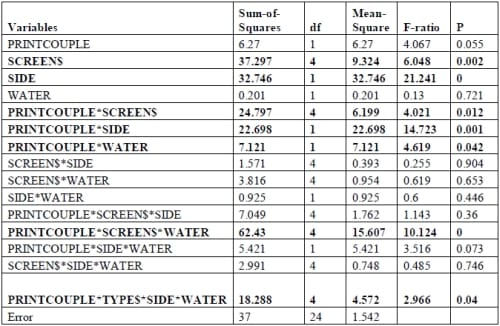
Table B. 2. Second ANOVA of Second Man-Roland Uniset Trial
From the table above, the effect of print couple (top and bottom print couple), water level were not significant. The printing screen, paper side were both significant, which is consistent with the result from table B.1. There were two ways and three ways interactions which were significant statistically to linting.
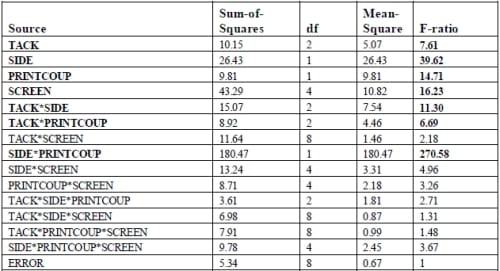
Table B. 3. Third ANOVA of Second Man-Roland Uniset Trial
Tack, side, print couple and printing screen were amongst the significant variables affecting lint. Two way interactions between tack and side, tack and print couple, and side and print couple were significant.
The interaction between side and print couple was also significant. This actually represented the take off angle since the take off angle of each of the side and each of the print couple would result in different take off angle.
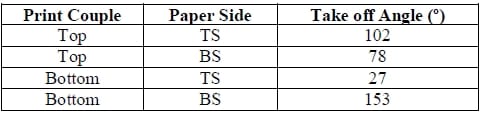
Table B. 4. The two way interactions between paper side and print couple.
APPENDIX C. Third Man Roland Uniset ANOVA Systat
SIDE$ (2 levels)
Bottom side, top side
SCREEN$ (6 levels)
0%, 100%, 25%, 50%, 75%, Picture
BLANKET$ (2 levels)
New (5.5 MPa blanket nip pressure), Old (9.5 MPa blanket nip pressure)
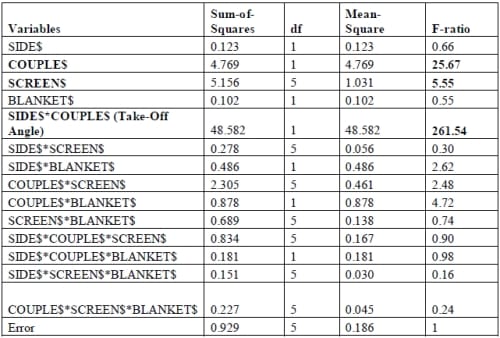
Table C. 1. ANOVA of Third Man-Roland Uniset Trial
Print couple (top and bottom) and printing screen were two significant factors affecting linting. The interaction between side and print couple was also significant. This actually represented the take off angle since the take off angle of each of the side and each of the print couple would result in different take off angle (refer to table B.4.) Blanket$ means blanket age or blanket nip pressure. It shows that blanket nip pressure and blanket age is not statistically significant to linting.
APPENDIX D1. Image Pro Macros for Area Classes
Option Explicit
‘path for the temp AOI file
Const TempAOIName As String=”temp.aoi”
Sub Afri_copy_area()
Dim pic As Single
Dim down As Single
Dim top As Single
Dim count As Integer
Begin Dialog UserDialog 320,135,”Collect data (Area, Perim., Roundness”,.DialogFunc3
‘ %GRID:10,7,1,1
Text 20,5,450,21,”To run particle size analysis push ‘RUN’. “,.Text1
PushButton 65,25,180,21,”Collect Data”,.PushButton1
PushButton 65,50,180,21,”Close All Pictures”,.PushButton2
PushButton 65,75,180,21,”Clear Data Collector”,.PushButton3
CancelButton 85,105,140,21
End Dialog
Dim dlg As UserDialog
ret= Dialog ( dlg ) ‘ display the dialog
If ret = 0 Then Exit Sub ‘ Cancel button pressed
End Sub
Function DialogFunc3%(DlgItem$, Action%, SuppValue%)
Dim tmp As Single
Dim heigh As Single
Dim downn As Single
Dim topp As Single
Dim I As Single
Select Case Action%
Case 2 ‘ Value changing or button pressed
If DlgItem$ = “PushButton1” Then
Call The_best()
DialogFunc3% = True ‘do not exit the dialog
End If
If DlgItem$ = “PushButton2” Then
For I = 1 To 40 Step 1
ret = IpDocClose()
DialogFunc3% = True ‘do not exit the dialog
Next I
End If
If DlgItem$ = “PushButton3” Then
Call clear_data_collector()
DialogFunc3% = True ‘do not exit the dialog
End If
End Select
End Function
Function The_best()
Dim ttt As String * 400
Dim more As Integer
Dim xratio As Single
Dim yratio As Single
Dim szout As String * 255
‘ Scan through and process all files in a directory
Dim IName As String*255
Dim fName As String
Dim workStr As String
Dim docID As Integer
Dim gdirstart As String
‘ Make certain we have a reasonable starting point. This code is
‘ only executed the first run after macro compilation. If you have
‘ a desired standard starting point, initialize the directory
‘ search here.
If gDirStart = “” Then
gDirStart = “C:My Documentsherman”
End If
‘ Get a file name in the desired directory
workStr = GetFilePath(“”, “*”, gDirStart, _
“Select a file in the desired directory”, 0)
‘ Check to make certain the user did not cancel
If workStr = “” Then
End If
‘ Close all open images prior to processing (this can be removed if desired)
ret = IpAppCloseAll()
‘ Extract the directory name from the full file name
gDirStart = Left(workStr, InStrRev(workStr, “”))
‘ Clear the output for work purposes
debugclear
ret = IpOutputClear()
‘ Call a setup routine ***
‘ Insert your setup call here
‘ Look for standard files, no directories or system files.
‘ See the ‘Dir’ command help for details
fName = Dir(gDirStart + “*.*”, 32)
While fName <> “”
‘ Print out the file name and its attributes
Debug.Print GetAttr(gDirStart + fName); ” “; fName
‘ Load the image
docID = IpWsLoad(gDirStart + fName, “”)
‘ Don’t process if there is a failure loading
If docID >= 0 Then
ret = IpWsLoad(gDirStart + fName, “”)
‘*******************
ret = IpCalGet(“sName”, szout) ‘get variable from calibration
If ret < 0 Then
Debug.Print “no spatial calibration”
Exit Function
End If
Debug.Print “spatial calibration:”
Debug.Print “calib name = ” + szout
ret = IpCalGet(“sUnitName”, szout)
Debug.Print “unit name = ” + szout
ret = IpCalGet(“sXUnitPerPix”, szout)
xratio = Val(szout)
Debug.Print “unit/pix (x) = ” + Str$(xratio)
ret = IpCalGet(“sYUnitPerPix”, szout)
yratio = Val(szout)
Debug.Print “unit/pix (y) = ” + Str$(yratio)
Debug.Print “aspect ratio = ” + Str$(yratio / xratio)
ret = IpCalGet(“sAngleOffset”, szout)
Debug.Print “angle offset = ” + Str$(Val(szout))
‘******************
ret = IpWsZoom(50)
ret = IpDocMaximize() ‘resize
ret = IpDocSize(829, 646)
ret = IpFltFlatten(0, 20) ‘2 x filters
ret = IpFltLoPass(3, 7, 1)
ret = IpBlbSetAttr(BLOB_FILTEROBJECTS, 0)
ret = IpBlbSetAttr(BLOB_8CONNECT,1)
‘call macro Blob_analys1()
Call Blob_analys1()
ret = IpTemplateMode(1)
ret = IpBlbShow(0)
ret = IpBlbSetAttr(BLOB_AUTORANGE, 1)
ret = IpBlbSetAttr(BLOB_BRIGHTOBJ, 0)
ret = IpTemplateMode(0)
ret = IpBlbCount()
ret = IpBlbUpdate(0)
ret = IpBlbShow(0)
ret = IpDcShow(1)
ret = IpDcShow(3)
ret = IpDcShow(3)
ret = IpDcSet(DC_AUTO, 2)
ret = IpDcUpdate(DC_FETCH)
ret = IpDcSelect(“Count_Size”, “BLBM_AREA”, 0)
ret = IpDcSelect(“Count_Size”, “BLBM_MEANFERRET”, 0)
ret = IpDcSelect(“Count_Size”, “BLBM_MAXFERRET”, 0)
ret = IpDcSelect(“Count_Size”, “BLBM_MINFERRET”, 0)
ret = IpDcSelect(“Count_Size”, “BLBM_PERIMETER”, 0)
ret = IpDcSelect(“Count_Size”, “BLBM_ROUNDNESS”, 0)
ret = IpDcSelect(“Count_Size”, “BLBM_ASPECT”, 0)
ret = IpDcSelect(“Count_Size”, “BLBM_BOX_AREA”, 0)
ret = IpDcSelect(“Count_Size”, “BLBM_BOXY”, 0)
ret = IpDcSelect(“Count_Size”, “BLBM_BOXX”, 0)
ret = IpDcSelect(“Count_Size”, “BLBM_MAXCALIP”, 0)
ret = IpDcSelect(“Count_Size”, “BLBM_MEANCALIP”, 0)
ret = IpDcSelect(“Count_Size”, “BLBM_MINCALIP”, 0)
ret = IpDcSelect(“Count_Size”, “BLBM_BOX_XY”, 0)
ret = IpDcShow(1)
ret = IpDcSet(DC_AUTO, 2)
ret = IpDcSet(DC_AUTO, 2)
ret = IpDcUpdate(DC_FETCH)
ret = IpDocClose()
‘
Close the initial image
ret = IpAppSelectDoc(docID)
ret = IpDocClose()
Else
Debug.Print “Error loading “; gDirStart + fName
End If
‘ Get the next file name
fName = Dir()
‘x=1
Wend
‘ Call a finish routine ***
‘ Insert your code here.
‘ Let the user know that we’ve finished
ret = IpMacroStop(“All images in directory processed.”, MS_MODAL)
End Function
Function clear_data_collector()
ret = IpDcShow(1)
ret = IpDcShow(3)
ret = IpDcShow(3)
ret = IpDcSelect(“Count_Size”, “BLBM_AREA”, 0)
ret = IpDcSelect(“Count_Size”, “BLBM_MEANFERRET”, 0)
ret = IpDcSelect(“Count_Size”, “BLBM_MAXFERRET”, 0)
ret = IpDcSelect(“Count_Size”, “BLBM_MINFERRET”, 0)
ret = IpDcSelect(“Count_Size”, “BLBM_PERIMETER”, 0)
ret = IpDcSelect(“Count_Size”, “BLBM_ROUNDNESS”, 0)
ret = IpDcSelect(“Count_Size”, “BLBM_ASPECT”, 0)
ret = IpDcSelect(“Count_Size”, “BLBM_BOX_AREA”, 0)
ret = IpDcSelect(“Count_Size”, “BLBM_BOXY”, 0)
ret = IpDcSelect(“Count_Size”, “BLBM_BOXX”, 0)
ret = IpDcSelect(“Count_Size”, “BLBM_MAXCALIP”, 0)
ret = IpDcSelect(“Count_Size”, “BLBM_MEANCALIP”, 0)
ret = IpDcSelect(“Count_Size”, “BLBM_MINCALIP”, 0)
ret = IpDcSelect(“Count_Size”, “BLBM_BOX_XY”, 0)
ret = IpDcShow(1)
ret = IpDcUpdate(DC_RESET)
ret = IpDcSet(DC_AUTO, 2)
ret = IpDcSet(DC_AUTO, 2)
ret = IpDde(DDE_SET, “row”, “1”)
ret = IpDde(DDE_SET, “col”, “1”)
ret = IpDde(DDE_SET, “append”, “0”)
ret = IpDcUpdate(DC_FETCH)
ret = IpDocClose()
End Function
Function Blob_analys1()
Dim x As Integer
Dim ttt As String * 400
Dim more As Integer
Dim xratio As Single
Dim yratio As Single
Dim szout As String * 255
Dim xname As String
Dim yname As String
ret = IpFltFlatten(0, 30) ‘2 x filters
ret = IpFltLoPass(3, 7, 1)
ret = IpBlbSetAttr(BLOB_FILTEROBJECTS, 0)
ret = IpBlbSetAttr(BLOB_8CONNECT,1)
ret = IpDde(DDE_SET, “append”,”1″)
ret = IpDde(DDE_SET, “target”, “c:program filesmicrosoft
officeoffice10excel.exe”)
ret = IpTemplateMode(1)
ret = IpBlbSetAttr(BLOB_AUTORANGE, 1)
ret = IpBlbSetAttr(BLOB_BRIGHTOBJ, 0)
ret = IpTemplateMode(0)
ret = IpBlbCount()
ret = IpBlbUpdate(0)
ipBins(0) = 0
ipBins(1) = 1000
ipBins(2) = 2000
ipBins(3) = 3000
ipBins(4) = 4000
ipBins(5) = 5000
ipBins(6) = 6000
ipBins(7) = 7000
ipBins(8) = 8000
ipBins(9) = 9000
ipBins(10) = 10000
ipBins(11) = 11000
ipBins(12) = 12000
ipBins(13) = 13000
ipBins(14) = 14000
ipBins(15) = 15000
ipBins(16) = 100000
ret = IpBlbShowSingleClass(BLBM_AREA, ipBins(0), 16, 1)
ret = IpDde(DDE_SET, “topic”, “[Book1]Sheet1”)
End Function
APPENDIX D2. Image Pro Macros for Length Classes
Option Explicit
‘path for the temp AOI file
Const TempAOIName As String=”temp.aoi”
Sub Afri_copy_length()
Dim pic As Single
Dim down As Single
Dim top As Single
Dim count As Integer
Begin Dialog UserDialog 320,135,”Collect data (Area, Perim., Roundness”,.DialogFunc3
‘ %GRID:10,7,1,1
Text 20,5,450,21,”To run particle size analysis push ‘RUN’. “,.Text1
PushButton 65,25,180,21,”Collect Data”,.PushButton1
PushButton 65,50,180,21,”Close All Pictures”,.PushButton2
PushButton 65,75,180,21,”Clear Data Collector”,.PushButton3
CancelButton 85,105,140,21
End Dialog
Dim dlg As UserDialog
ret= Dialog ( dlg ) ‘ display the dialog
If ret = 0 Then Exit Sub ‘ Cancel button pressed
End Sub
Function DialogFunc3%(DlgItem$, Action%, SuppValue%)
Dim tmp As Single
Dim heigh As Single
Dim downn As Single
Dim topp As Single
Dim I As Single
Select Case Action%
Case 2 ‘ Value changing or button pressed
If DlgItem$ = “PushButton1” Then
Call The_best()
DialogFunc3% = True ‘do not exit the dialog
End If
If DlgItem$ = “PushButton2” Then
For I = 1 To 40 Step 1
ret = IpDocClose()
DialogFunc3% = True ‘do not exit the dialog
Next I
End If
If DlgItem$ = “PushButton3” Then
Call clear_data_collector()
DialogFunc3% = True ‘do not exit the dialog
End If
End Select
End Function
Function The_best()
Dim ttt As String * 400
Dim more As Integer
Dim xratio As Single
Dim yratio As Single
Dim szout As String * 255
‘ Scan through and process all files in a directory
Dim IName As String*255
Dim fName As String
Dim workStr As String
Dim docID As Integer
Dim gdirstart As String
‘ Make certain we have a reasonable starting point. This code is
‘ only executed the first run after macro compilation. If you have
‘ a desired standard starting point, initialize the directory
‘ search here.
If gDirStart = “” Then
gDirStart = “C:Documents and SettingsuserMy DocumentsHerman”
End If
‘ Get a file name in the desired directory
workStr = GetFilePath(“”, “*”, gDirStart, _
“Select a file in the desired directory”, 0)
‘ Check to make certain the user did not cancel
If workStr = “” Then
End If
‘ Close all open images prior to processing (this can be removed if desired)
ret = IpAppCloseAll()
‘ Extract the directory name from the full file name
gDirStart = Left(workStr, InStrRev(workStr, “”))
‘ Clear the output for work purposes
debugclear
ret = IpOutputClear()
‘ Call a setup routine ***
‘ Insert your setup call here
‘ Look for standard files, no directories or system files.
‘ See the ‘Dir’ command help for details
fName = Dir(gDirStart + “*.*”, 32)
While fName <> “”
‘ Print out the file name and its attributes
Debug.Print GetAttr(gDirStart + fName); ” “; fName
‘ Load the image
docID = IpWsLoad(gDirStart + fName, “”)
‘ Don’t process if there is a failure loading
If docID >= 0 Then
ret = IpWsLoad(gDirStart + fName, “”)
‘*******************
ret = IpCalGet(“sName”, szout) ‘get variable from calibration
If ret < 0 Then
Debug.Print “no spatial calibration”
Exit Function
End If
Debug.Print “spatial calibration:”
Debug.Print “calib name = ” + szout
ret = IpCalGet(“sUnitName”, szout)
Debug.Print “unit name = ” + szout
ret = IpCalGet(“sXUnitPerPix”, szout)
xratio = Val(szout)
Debug.Print “unit/pix (x) = ” + Str$(xratio)
ret = IpCalGet(“sYUnitPerPix”, szout)
yratio = Val(szout)
Debug.Print “unit/pix (y) = ” + Str$(yratio)
Debug.Print “aspect ratio = ” + Str$(yratio / xratio)
ret = IpCalGet(“sAngleOffset”, szout)
Debug.Print “angle offset = ” + Str$(Val(szout))
‘******************
ret = IpWsZoom(50)
ret = IpDocMaximize() ‘resize
ret = IpDocSize(829, 646)
ret = IpFltFlatten(0, 20) ‘2 x filters
ret = IpFltLoPass(3, 7, 1)
ret = IpBlbSetAttr(BLOB_FILTEROBJECTS, 0)
ret = IpBlbSetAttr(BLOB_8CONNECT,1)
‘call macro Blob_analys1()
Call Blob_analys1()
ret = IpTemplateMode(1)
ret = IpBlbShow(0)
ret = IpBlbSetAttr(BLOB_AUTORANGE, 1)
ret = IpBlbSetAttr(BLOB_BRIGHTOBJ, 0)
ret = IpTemplateMode(0)
ret = IpBlbCount()
ret = IpBlbUpdate(0)
ret = IpBlbShow(0)
ret = IpDcShow(1)
ret = IpDcShow(3)
ret = IpDcShow(3)
ret = IpDcSet(DC_AUTO, 2)
ret = IpDcUpdate(DC_FETCH)
ret = IpDcSelect(“Count_Size”, “BLBM_AREA”, 0)
ret = IpDcSelect(“Count_Size”, “BLBM_MEANFERRET”, 0)
ret = IpDcSelect(“Count_Size”, “BLBM_MAXFERRET”, 0)
ret = IpDcSelect(“Count_Size”, “BLBM_MINFERRET”, 0)
ret = IpDcSelect(“Count_Size”, “BLBM_PERIMETER”, 0)
ret = IpDcSelect(“Count_Size”, “BLBM_ROUNDNESS”, 0)
ret = IpDcSelect(“Count_Size”, “BLBM_ASPECT”, 0)
ret = IpDcSelect(“Count_Size”, “BLBM_BOX_AREA”, 0)
ret = IpDcSelect(“Count_Size”, “BLBM_BOXY”, 0)
ret = IpDcSelect(“Count_Size”, “BLBM_BOXX”, 0)
ret = IpDcSelect(“Count_Size”, “BLBM_MAXCALIP”, 0)
ret = IpDcSelect(“Count_Size”, “BLBM_MEANCALIP”, 0)
ret = IpDcSelect(“Count_Size”, “BLBM_MINCALIP”, 0)
ret = IpDcSelect(“Cou
nt_Size”, “BLBM_BOX_XY”, 0)
ret = IpDcShow(1)
ret = IpDcSet(DC_AUTO, 2)
ret = IpDcSet(DC_AUTO, 2)
ret = IpDcUpdate(DC_FETCH)
ret = IpDocClose()
‘ Close the initial image
ret = IpAppSelectDoc(docID)
ret = IpDocClose()
Else
Debug.Print “Error loading “; gDirStart + fName
End If
‘ Get the next file name
fName = Dir()
Wend
‘ Let the user know that we’ve finished
ret = IpMacroStop(“All images in directory processed.”, MS_MODAL)
End Function
Function clear_data_collector()
ret = IpDcShow(1)
ret = IpDcShow(3)
ret = IpDcShow(3)
ret = IpDcSelect(“Count_Size”, “BLBM_AREA”, 0)
ret = IpDcSelect(“Count_Size”, “BLBM_MEANFERRET”, 0)
ret = IpDcSelect(“Count_Size”, “BLBM_MAXFERRET”, 0)
ret = IpDcSelect(“Count_Size”, “BLBM_MINFERRET”, 0)
ret = IpDcSelect(“Count_Size”, “BLBM_PERIMETER”, 0)
ret = IpDcSelect(“Count_Size”, “BLBM_ROUNDNESS”, 0)
ret = IpDcSelect(“Count_Size”, “BLBM_ASPECT”, 0)
ret = IpDcSelect(“Count_Size”, “BLBM_BOX_AREA”, 0)
ret = IpDcSelect(“Count_Size”, “BLBM_BOXY”, 0)
ret = IpDcSelect(“Count_Size”, “BLBM_BOXX”, 0)
ret = IpDcSelect(“Count_Size”, “BLBM_MAXCALIP”, 0)
ret = IpDcSelect(“Count_Size”, “BLBM_MEANCALIP”, 0)
ret = IpDcSelect(“Count_Size”, “BLBM_MINCALIP”, 0)
ret = IpDcSelect(“Count_Size”, “BLBM_BOX_XY”, 0)
ret = IpDcShow(1)
ret = IpDcUpdate(DC_RESET)
ret = IpDcSet(DC_AUTO, 2)
ret = IpDcSet(DC_AUTO, 2)
ret = IpDde(DDE_SET, “row”, “1”)
ret = IpDde(DDE_SET, “col”, “1”)
ret = IpDde(DDE_SET, “append”, “0”)
ret = IpDcUpdate(DC_FETCH)
ret = IpDocClose()
End Function
Function Blob_analys1()
Dim x As Integer
Dim ttt As String * 400
Dim more As Integer
Dim xratio As Single
Dim yratio As Single
Dim szout As String * 255
Dim xname As String
Dim yname As String
ret = IpFltFlatten(0, 30) ‘2 x filters
ret = IpFltLoPass(3, 7, 1)
ret = IpBlbSetAttr(BLOB_FILTEROBJECTS, 0)
ret = IpBlbSetAttr(BLOB_8CONNECT,1)
ret = IpDde(DDE_SET, “append”,”1″)
ret = IpTemplateMode(1)
ret = IpBlbSetAttr(BLOB_AUTORANGE, 1)
ret = IpBlbSetAttr(BLOB_BRIGHTOBJ, 0)
ret = IpTemplateMode(0)
ret = IpBlbCount()
ret = IpBlbUpdate(0)
ipBins(0) = 0
ipBins(1) = 10
ipBins(2) = 20
ipBins(3) = 30
ipBins(4) = 40
ipBins(5) = 50
ipBins(6) = 60
ipBins(7) = 70
ipBins(8) = 80
ipBins(9) = 90
ipBins(10) = 100
ipBins(11) = 110
ipBins(12) = 120
ipBins(13) = 130
ipBins(14) = 140
ipBins(15) = 150
ipBins(16) = 5000
ret = IpBlbShowSingleClass(BLBM_MAXCALIP, ipBins(0), 16, 1)
ret = IpDde(DDE_SET, “topic”, “[Book1]Sheet1”)
ret = IpBlbSaveClasses(“”, S_LEGEND+S_DDE)
ret = IpBlbShowSingleClass(0, ipBins(0), 0, 0)
ret = IpBlbShow(0)
End Function
APPENDIX E. Harris Print Trial September 2004 (First Trial Man Roland Uniset Trial)
There are two main sections in this report. The first one is aimed to investigate the effect of paper orientation and paper side in the press using Norstar produced by Boyer Mill. The second one is aimed to compare the linting of Boyer PM2 45 gsm (Nornews), Norstar improved brightness of 74 ISO brightness and that of Golbey 42gsm newsprint produced by Norske Skog in France, are currently being supplied to Australian pressrooms.
1.0 Effect of Paper Orientation and Paper Side in the Pressroom
Paper Used: Norstar 52 gsm produced by Boyer Mills in Tasmania
There were two runs for this purpose, 52 gsm Norstar was run first from reelstand 7 then from reelstand 8. The paper was still run through the same printing unit. This allowed us to ‘turn-over’ the paper in the press and look at the effects of the two sidedness of the paper and the two sidedness of the press (Figure 1).
2.0 Effect of Paper Type : Comparing Norstar, Nornews and Golbey
Norstar was run in the third printing tower from reelstand 7 and 8 for the first and second trials.
Nornews and Golbey were run in the second printing tower with reelstand 5 for the first and second printing trials.
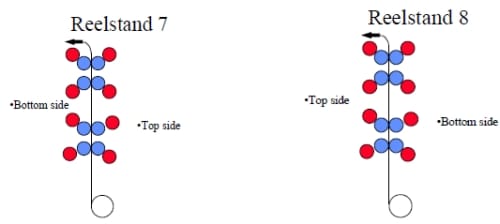
Figure 1:
The RHS rolls are slightly higher (105º) than the LHS ones (75º). This resulted in larger take off angle for the RHS of the paper. According to the literature, the higher the take off angle, the higher the lint result. The results of this experiment will be discussed later in this report. Boyer 45gsm newsprint was run from reelstand 6, then Golbey 42 gsm was run from the same reelstand.
The Harris Print press is a Man Roland Uniset with 3 towers. The tower the newsprints were printed upon uses coldset inks. The tower the Norstar was printed on is fitted with a small oven and runs with inks that are ‘heatset-like’. This enables the pressroom to run coated paper for some customers.
40,000 copies (gross) were run of each paper at a speed of 25,300 impressions per hour. The last 200 to 300 copies were run with the zonals on (with no ink being applied to the plate) to remove ink from the blankets. Blanket pulls were collected from non-image, 20% screens, 50% screens and solids on each colour and from the picture of a balloon using weighed tape pulls which were reported in a separate technical memo.
Domtar Lint Weight
Around 300 cm2 of the blankets were washed with isopropyl alcohol, these samples were then filtered and weighted, then the lint weights per square metre of blanket were calculated
This method is slightly different but has the sampe principle with the one that is normally used by Boyer Research whereby they use tape pulls method and then wash the tape with dichloromethane, filtering the lint deposit and weight it.
Ink used: Toyo Coldset Newsprint
Paper Used: Nornews : 45 gsm Newspaper grade produced by Norske Skog Boyer
Roll number:
- B 4132933
- B 4132921
- B 4132920
Norstar : 52 gsm improved brightness (ISO brightness of 74) produced by Norske Skog Boyer
Roll number: First Run
- B3170608
- B 3162655
- B 3170601
- B 3170585
Second Run
- B 3170609
- B 3162663
- B 3170600
- B 3170584
APPENDIX F. July 4th and 5th 2005 Harris Printing Trial (Second Trial )
Aim: Looking at the effect of printing parameters to newspaper lint:
- Ink tacks
- Colours
- Screen RulingScreen Ruling
- Speed
- No of impressions
Paper: Norstar 52gsm
Roll number
- B 5138329
- B 5138352
- B 5138354
- B 5138362
- B 5138336
- B 5138345
- B 5138387
- B 5138334
- B 5138343
- B 5138353
- B 5138344
- B 5138335
- B 5138379
Ink: Toyo Test Newsprint
Parameters tested:
- Screen Ruling ( 100 and 150 lpi)
- Screen tone (25%,50%,solid)
- Tack( Black 4,6,9,13.5 and Cyan 4,6,9,13.5
- Colour(Black and Cyan)
- Effect of fountain solution level
- Second printing unit lints
RUN 1:
Parameters tested:
- Black Tack 9 and 13.5
- Screen Ruling (100 and 150)
- Screen tone (25%,50% and solid)
- Efect of fountain solution level
- Second printing unit lints
First Tower: Unit 5
Top printing couple:
Ink: Black Toyo Tack 13.5
Paper:Norstar 52gsm 405 mm width 2 rolls, giving us around 23000 copies
Bottom printing couple:
Ink: Black Toyo Tack 9
Paper:Norstar 52gsm 405mm width 2 rolls, giving us around 23000 copies
Middle Tower:
Unit 7, two printing couples are used:
Ink:Both top and bottom print couple with Black tack 4</p >
Paper: Norstar 52gsm 810 mm width, 2rolls around 23000 copies
I am looking at the effect of first and second printing process as well as varying water level across the paper width (half width with normal level, the other half with low water level), therefore I need 810 mm width of paper. Screen ruling will also be investigated. In this run, 150 lpi is used.
RUN 2
Parameters tested:
- Black Tack 4 and 6
- Screen Ruling (100 and 150)
- Screen tone (25%,50% and solid)
- Backtrap lint (effect of fountain solution level)
- Dot shape
First Tower (Unit 5):
Top printing couple:
Ink: Black Toyo Tack 6
Paper:Norstar 52gsm 810mm width 2 rolls, giving us around 23000 copies
Bottom printing couple:
Ink: Black Toyo Tack 4
Paper:Norstar 52gsm 810mm width 2 rolls, giving us around 23000 copies
In this first tower I will have a look at lint result effect of tack, screen ruling and dot shape. I will have ellipse, diamond and line as dot shapes in the full plate, therefore I need 810mm paper.
Middle Tower:
Ink:Both top and bottom print couple with Black tack 4
Paper: Norstar 52gsm 405 mm width, 2rolls around 23000 copies
RUN 3
Parameters tested:
- No of impressions
- Tack
- Screen Ruling
- Screen Tone
First Tower:
Top printing couple:
Ink: Black Toyo tack6
Paper:Norstar 52gsm 405mm
No of impressions: 7000
Bottom printing couple:
Ink: Black Toyo Tack 4
Paper:Norstar 52gsm 405mm width 2 rolls.
No of impressions: 7000
Run 4
Parameters tested:
- No of impressions
- Tack
- Screen Ruling
- Screen Tone
First Tower:
Top printing couple:
Ink: Black Toyo tack6
Paper:Norstar 52gsm 405mm
No of impressions: 14000
Bottom printing couple:
Ink: Black Toyo Tack 4
Paper:Norstar 52gsm 405mm width 2 rolls.
No of impressions: 14000
Run 4
First Tower:
- Top printing couple:
- Ink: Black Toyo tack6
- Paper:Norstar 52gsm 405mm
- No of impressions: 14000
Bottom printing couple:
Ink: Black Toyo Tack 4
Paper:Norstar 52gsm 405mm width 2 rolls.
No of impressions: 14000
Run 5
Parameters tested:
- Tack
- Screen Ruling
- Screen Tone
- Speed
First Tower:
Top printing couple:
Ink: Black Toyo tack6
Paper:Norstar 52gsm 405mm
No of impressions: 2 rolls around 23000
Speed: 12500 imp/hour
Bottom printing couple:
Top printing couple:
Ink: Black Toyo Tack 4
Paper:Norstar 52gsm 405mm width 2 rolls.
No of impressions: 2 rolls around 23000
Speed: 12500 imp/hour
Run 6
Parameters tested:
- Screen Ruling ( 100 and 150 lpi)
- Screen tone (25%,50%,solid)
- Tack(Cyan 4, Cyan13.5)
First Tower:
Top printing couple:
Ink: Cyan Toyo tack6
Paper:Norstar 52gsm 405mm width 2 rolls, giving us around 23000 copies
Bottom printing couple:
Ink: Cyan Toyo Tack 4
Paper:Norstar 52gsm 405mm width 2 rolls, giving us around 23000 copies
In this first tower I will have a look at lint result effect of tack, screen ruling and also colour effect since Run 1 and 2 are done with black.
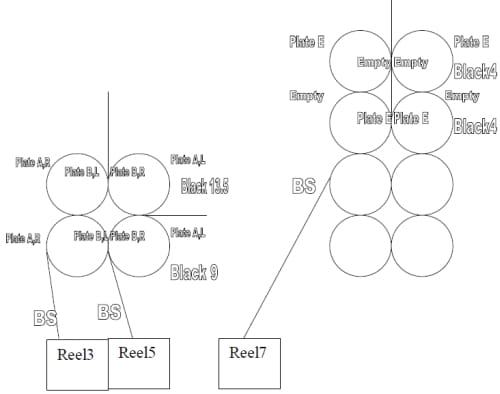
Run 1 – Speed:25000 copies/hr Run:2 rolls of paper from each reelstand (approx. 23000 copies)
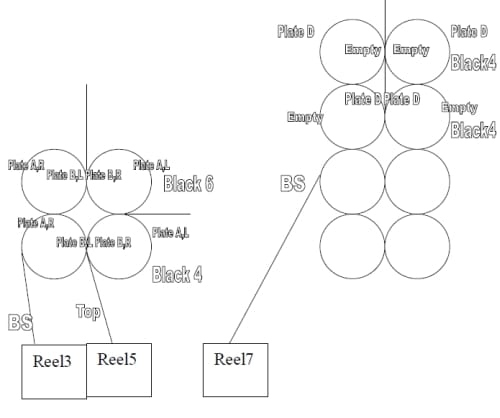
Run 2 – Speed:25000 copies/hr Run:2 rolls of paper from each reelstand (approx. 23000 copies)
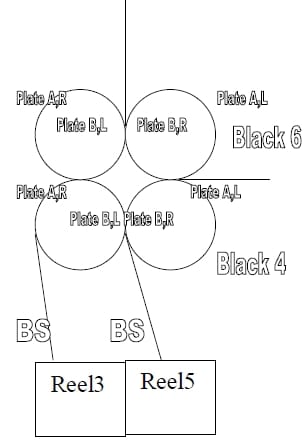
Run 3 – Speed:25000 copies/hr Run: 7000 copies
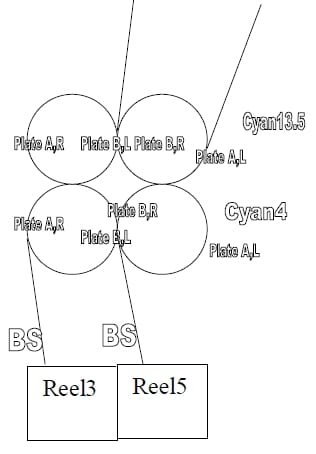
Run 4 – Speed:25000 copies/hr Run: 14000 copies Plate and ink arrangements are the same as RUN3
Plate:
800mm (width) x cut off dimension of the plate which is 578mm
All dots will be circular with screen ruling as specified, i.e. 100 lpi or 150 lpi. The only thing that needs to be designed is the PICTURE in plate A, may be using the picture of the balloons with gray colour
The dimension of each of the image area inside the plate is 370×180 mm.
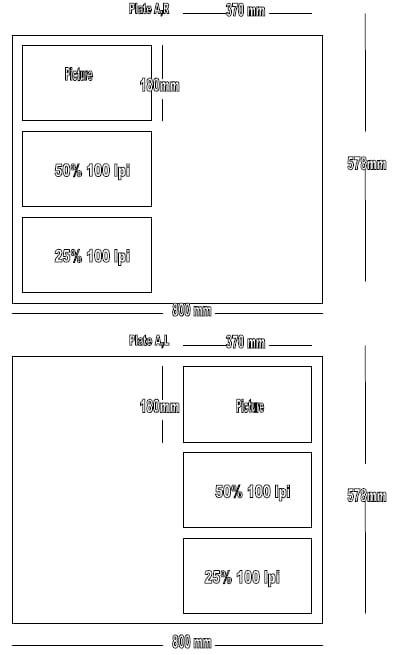
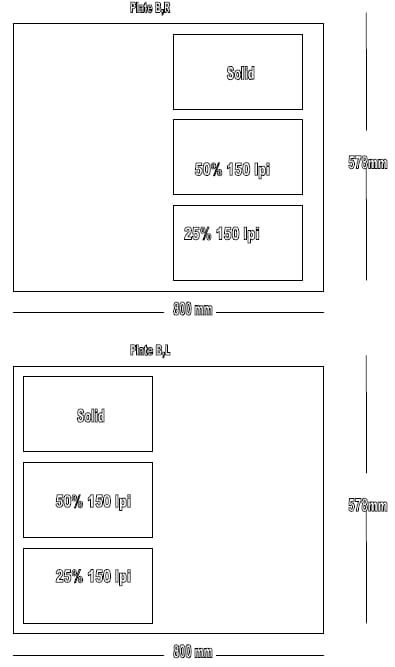
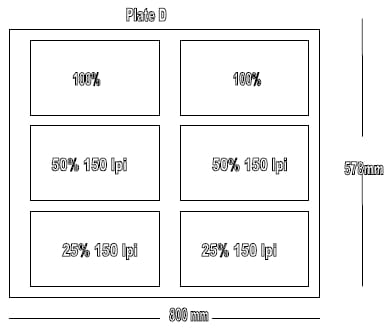
APPENDIX G. Man Roland Uniset Third Trial
13th – 14th May 2006
Speed: 25000
25000 copies printed
Preliminary work:
Checking the nip pressure with pressure sensitive tape.
Nip Pressure of Old blanket AND New Blanket
Check with the manager how many number of copies it had done before for the OLD
BLANKET. The new blanket is put in the BOTTOM COUPLE.
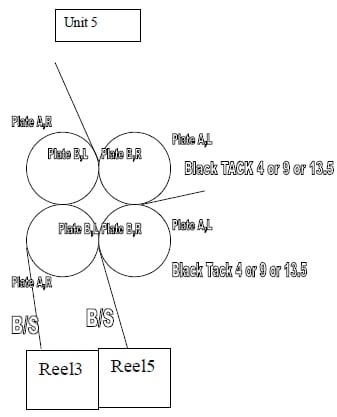
Paper and Printing Web Arrangements
Run 1: Using Old Blanket
Reelstand 3 and 5 are used (or reel stand 5 if only one print couple is changed with new blanket)
Ink: both top and bottom couple with Black toyo tack 9
Run 2: Using Old Blanket
Reelstand 3 and 5 are used (or reel stand 5 if only one print couple is changed with new blanket)
Ink: both top and bottom couple with Black toyo tack 13.5
Run 3: Using Old Blanket
Reelstand 3 and 5 are used (or reel stand 5 if only one print couple is changed with new blanket)
Ink: both top and bottom couple with Black toyo tack 4
Run 4
NEW BLANKET IS USED in the bottom print couple. Only the bottom print couple was used to print, no paper is run through the top printing couple. Pressure sensitive tape needs to be run in the beginning. Reelstand 3 and 5 are used similar to RUN1. Plate and Inks are the same as run 3
PLATE
800mm (width) x cut off dimension of the plate which is 578mm
All dots will be circular with screen ruling as specified, i.e. 100 lpi
The only thing that needs to be designed is the PICTURE in plate A, may be using the picture of the balloons with gray colour. The dimension of each of the image area inside the plate is 370×180
INK
Toyo Black Test Newsprint
PAPER
Norstar
- Reel Stand 5
- B 5154179
- B 6021582
- B 5154195
- B 6021581
- Reel Stand 3
- B 5154186
- B 6021570
- B 5154187
- B 6021569
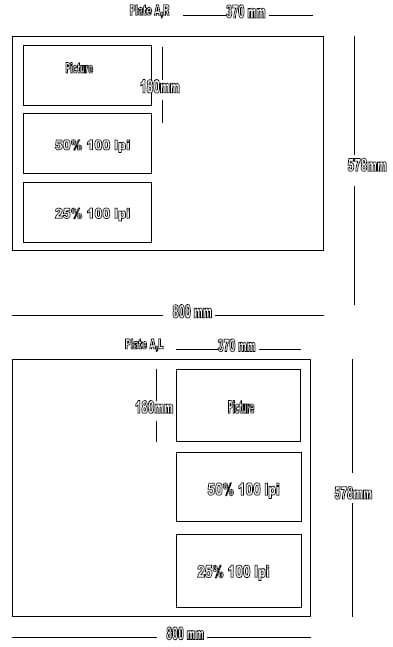
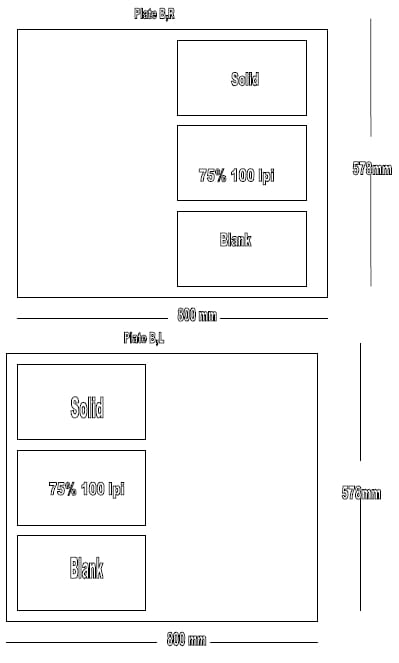
APPENDIX H. Heidelberg GTO-52 Dot Shape, Paper Side, Printing Screen Tone, Printing Ruling Effects to Linting Systat ANOVA.
Categorical values encountered during processing are:
DOT_SHAPE$ (3 levels)
Circle, Ellipse, Square
SIDE$ (2 levels)
BS, TS
SCREEN (2 levels)
25, 50
RULING (2 levels)
100, 150
Dep Var: LINT100 N: 28 Multiple R: 0.991
761 Squared multiple R: 0.983590
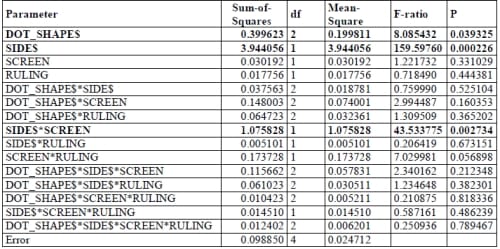
Table D. 1 Analysis of Variance of Heidelberg GTO-52 Printing Press Variables
Parameters which are significant to linting at the 5% level are highlighted in bold. The dot shape, the side of the paper have significant effect to lint and also there is a significant interaction between the paper side and the screen type. Circle, square, ellipse respectively gives higher lint results. Top side of the paper resulted in higher lint than the bottom side.
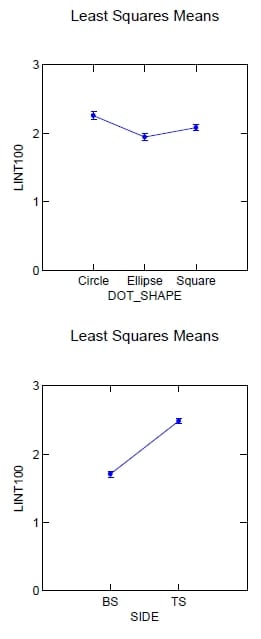
References
- MANGIN, P.J. and SILVY, J., “Fundamental Studies of Linting: Understanding Ink-Press-Paper Interactions Non-Linearity”, TAGA Proceedings, 884-905 (1997).
- SUDARNO, A.T., GUJJARI, C., RAND, S., JANKO, P., BATCHELOR, W., and BANHAM, P., “Comparison of Size Distributions of Lint Particles from Different Printing Operations”, 59th APPITA Annual Conference, 279 (2005).
- GANE, P.A.C., SEYLER, E.N, “Some Novel Aspects of Ink/Paper Interaction in Offset Printing”, International Printing and Graphic Arts Conference, 209-225 (1994).
- BROUILLETTE, F., MORNEAU, D. , CHABOT, B. , DANEAULT, C., “Evaluation of New Lint Reduction Additives in Wood- Containing Paper Manufacturing”, Pulp & Paper Canada, 107(2):47-50 (2006).
- IONIDES, G.N., “The Linting Tendency of Newsprint: A General Review”, Paperi ja Puu, 66(4):298 (1984).
- MOLLER, K., THOMASSEN, B., WEIDEMMULLER, J., MENZEL, P., WALTHER, K., FALTER, K., SPORING, G., MEISSNER, M., and AXELL, O., “Factors Influencing Linting in Offset Printing of Newsprint”, 115-121, APPITA Conference, (1995).
- HOC, M., “The Phenomenon of Linting in Newsprint Printing,” IFRA, Darmstadt, 2000.
- RAND, S.F., “Linting of Filler in the Offset Printing Process”, MEngSc Minor Thesis Monash University, (2004).
- “Handbook of Print Media (Technology and Production Methods)”. Springer- Verlag Berlin Heidelbery, 2001.
- Offset lithography,https://desktoppub.about.com/gi/dynamic/offsite.htm?zi=1/XJ&sdn=de sktoppub&zu=http%3A%2F%2Fwww.bobs.co.uk%2Fprint%2FOffset.html, Bob’s Print, 11th June, 2006
- OITTINEN, P. and SAARELMA, H., “Papermaking Science and Technology,” in Printing, vol. 13: Fapet Oy, 1998.
- GOODMAN, R., NUSSEL, B., “The Technology Generations of Digital Thermal Printing Plates”, TAGA Proceedings, 264-279 (1999).
- “The Benefits of Ctp,https://www.theprintinghouse.com/ArticleBenefitsCTP.cfm, The printing House, 21st June, 2006
- “Encyclopedia Encarta”: Microsoft Illustration, 1996.
- MANGIN, P.J. and DALPHOND, J.E., “A Novel Approach to Evaluate the Linting Propensity of Newsprint: Part 2: Case Studies”, Pulp & Paper Canada, 94(1):T5-10 (1993).
- WOOD, J., ZHANG, X., CHAGAEV, O., STATIONWALA, M., GOEL, K., SHALLHORN, P.M., and BEAULIEU, S., “The Effect of Various Mechanical and Chemical Treatment of Ray Cells on Sheet Properties and Linting”, Pulp & Paper-Canada, 101(10):83-87 (2000).
- SUDARNO, A.T., BATCHELOR, W., BANHAM, P. GUJJARI, C., “Investigation of the Effect of the Press and Paper Variables on Linting During the Offset Printing of Newsprint”, APPITA Conference, 26-32 (2006).
- SHALLHORN, P., HEINTZE, H.U., “Hardwood Vessel Picking in the Offset Printing of Uncoated Fine Papers”, International Printing and Graphic Arts Conference, 147 (1994).
- LINDEM, P.E. and MOLLER, K., “The Dagbladet Full-Scale Printing Trials”, Tappi Journal, 77(7):185-193 (1994).
- HEINTZE, H.U., “Offset Lint Testing : An Overview of Printing Options and Issues”, Pulp & Paper Canada, 107(2):30-33 (2006).
- ASPLER, J.S., “Linting and Surface Contamination : Current Status”, TAGA Proceedings, 375-398 (2003).
- WOOD, J.R., MCDONALD, J.D., FERRY, P., SHORT, C.B., and CRONIN, D.C., “The Effect of Paper Machine Forming and Pressing on Offset Linting”, Pulp & Paper Canada, 99:53-59 (1998).
- WAECH, T.G., “Lint Reduction by High Temperature Calendering”, Pulp & Paper Canada, 93(10):44-47 (1990).
- MIYANISHI, T., “Wet End Optimization for a Neutral Pcc Filled Newsprint Machine”, Tappi Journal, 82(1):220-225 (1999).
- KELLER, S.F. and WAECH, T.G., “The Effects of High-Temperature Soft-Nip Calendering on Newsprint Properties”, Journal of Pulp and Paper Science, 18(3):J103-J107 (1992).
- WOOD, J. and KARNIS, A., “Linting Propensity of Mechanical Pulps”, Pulp & Paper Canada, 77(7):185 (1992).
- MIYANISHI, T. and MIYAGI, M., “The Effects of Fines on Offset Newsprint Linting”, Tappi Journal, 75(5):75-80 (1992).
- MANGIN, P.J., “A Critical Review of the Effect of Printing Parameters on the Linting Propensity of Paper”, Journal of Pulp & Paper Science, 17(5):J156-J-163 (1991).
- FROBERG, J.C., VOLTAIRE. J., SUNDIN, M., TIBERG, F., “Effect of Ink- Fountain Balance on Ink-Tack Development”, International Printing and Graphic Arts Conference,133-138 (2000).
- ZANG, Y.H., ASPLER, J.S., BOLUK, M.Y., and DE GRACE, J.H., “Direct Measurement of Tensile Stress (“Tack”) in Thin Ink Films”, J. Rheol., 35(3):345- 361 (1991).
- MERET, R.G. and SZANYI, L., “The Gfl Surface Strength Test Applied to Newsprint and Its Relationship with Offset Linting”, Tappi, 64(9):177-178 (1981).
- MANGIN, P.J., “Etude De La Destructuration De La Surface Du Papier En Zone D’impression Offset”, Phd Thesis de L’Institute National Polytechnique de Grenoble, (1988).
- WOOD, J.R. and KARNIS, A., “Linting Propensity of Mechanical Pulps”, Pulp & Paper Canada, 93(7):17-24 (1990).
- WOOD, J.R. and KARNIS, A., “Towards a Lint-Free Newsprint Sheet”, Paperi Ja Puu 59, 10:660 (1977).
- HOWARD, R.C., BICHARD, W., “The Basis Effects of Recycling on Pulp Properties”, Journal of Pulp & Paper Science, 18(4):J151-J159 (1993).
- CANTY, R., “Literature Review into Dusting and Linting,” CRC for Functional Communication Surfaces, Melbourne, Report, 2003.
- MCDONALD, J.D., PIKULIK, I, “The Effect of a Fourth Press on Print Quality”, Tappi, 74(9):159-166 (1991).
- JOHN, B., TYLER, R., LEEKLEY, R., “An Investigation of Linting and Fluffing of Offset Newsprint,” Institute of Paper Chemistry, Report, Appleton Wisconsin, 23 August 1974.
- DALPHOND, J.E., “A Critical Review of the Main Variables in Offset Printing : Effects on Printing Quality, Measurement and Control,”STFI, Stockholm, Report June 1997.
- MEY, K., “Linting in Newspaper Offset Printing and Domtar Lint Collector,” CRC for Functional and Communication Surfaces, Melbourne, 2003.
- MOON, K., “Press Section Principles,” Norske Skog, Boyer, Tasmania, 1997.
- WAECH, T.G., “Offset Lint Testing by Image-Analysis”, Pulp & Paper-Canada, 93(9):60-65 (1992).
- HANSEN, A., MOESTUE, P., MOLLER, K., THOMASSEN, B., and NOSTDAL, H., “The Dagbladet Full-Scale Printing Trials .1. Methodology of Trial Runs”, Tappi Journal, 77(1):139-145 (1994).
- WOOD, J.R., IMADA, S.E., BEAULIEU, S., and KERR, R.B., “Reduction of Offset Linting – a Comparison of 6 Mills .1. Pressroom Effects”, Pulp & Paper- Canada, 96(10):33-39 (1995).
- COLLINS, N.J., RASSON, A.J., and JENKINS, S., “Print Quality Studies on a Heidelberg Test Press”, APPITA, 43(6):437-445 (1990).
- KEHLA, V., MANNINEN, M., OITTINEN, P., “Tack Force Measurement and Picking”, TAPPI, 57(4) (1974).
- VUKASINOVIC, R., “Linting – Paper and Printing Properties of Newsprint,” Monash University, 4th Year Research Project, June 2005.
- TURNBULL, J., “Effect of Ink Tack on Linting in Offset Lithographic Newsprint,” Monash University, 4th Year Research Project, June 2005.
- VOLTAIRE, J., BATCHELOR, W., FOGDEN, A., SUDARNO, A., “New Technique for Monitoring Ink-Water Balance on an Offset Press”, submitted to APPITA Journal (2006).
- LI
NDQVIST, U. and MEINANDER, S., “A Pilot Test for Linting Propensity of Papers”, TAPPI, 64(12):61-63 (1980). - WIIK, K., “Dynamics of Linting”, APPITA Conference, 33-35 (2006).
- ASPLER, J.S., LEPOUTRE, J.S., “The Transfer and Setting of Ink on Coated Paper: A Review”, TAPPI/CPPA Symposium of Paper Coating Fundamentals, TAPPI Press, Atlanta, 333-357 (1991).
- LIND, J., “Ink Transfer from the Offset Blanket,” TAGA Proceedings, 328-337 (1985)
- ZANG, Y.-H., “Asymmetric Splitting and Ink Transfer : A New Ink Transfer Model”, International Printing and Graphic Arts Conference, 103-112 (1992).
- DE GRACE, J.H., MANGIN, P.J., “A Mechanistic Approach to Ink Transfer. Part 2 – the Splitting Behaviour of Inks in Printing Nips,” Advances in Printing Science and Technology, 21, 146-141 (1988)
- ELDRED, N.R., “Chemistry for the Graphic Arts”, 3rd ed. Pittsburgh: GATF Press, 2001.
- KJT-100, “Near Infra-Red Ray Reflectance Moisture Meter,” Japan Tobacco Inc, Japan, 1992.
- BASSEMIR, R., HARBIN, N.,DIPIAZZA,J., “Development of the Npiri Water Content Meter,” American Ink Maker, March 1996.
- HEINTZE, H.U., ROMBOUGH, W.C., and GORDON, R.W., “Lint Testing on a Small Web Offset Press”, CPPA Tech. Sect. 62nd Annual Meeting, 3223 (1976).
- HEINTZE, H.U. and RAVARY, R.E., “An Economical Means to Measure and Characterize Lint”, Pulp & Paper Canada, 95(6):47-50 (1993).
- SHEN, W., “Appi Printing Lecture Material”, (2004).
- URQUHART, R., “An Introduction to Ink and Fountain Solution in Offset Lithographic Printing,” Melbourne, Personal Communication, 2005.
- BECKMAN, B., RUDER, R., “Set-Off, Smearing and Rub-Off in Offset Newspaper Printing,” in Advances in Printing Science and Technology, vol. 23: John Wiley & Sons Ltd., 1995, pp. 314.
- STROM, G., “Interaction between Offset Ink and Coated Paper- a Review of the Present Understanding”, Fundamental Research Symposium, (2005).
- LIU, F., MAO, Y., SHEN, W., PARKER. I., “The Penetration of Offset Ink Emulsion in Fine Paper – Confocal Microscopic Evidence Relevant to Vessel Picking and Show Through”, APPITA Conference, 207-214 (2006).
- LYNE, L.M., MADSEN, V., “An Apparatus for the Measurement of Liquid Penetration into Porous Webs at a Press Nip”, Annual Meeting of the Technical Section, Canadian Pulp and Paper Association, 523-528 (1964).
- LIU, F., SHEN, W., PARKER. I., “Ink-Fountain Solution Interaction in Lithography. Part 2: Visualising the Fountain Solution Droplets in Ink Vehicle By 3-D Image Construction”, APPITA Conference, 267-274 (2005).
- VOLTAIRE, J., GUJJARI, C., BATCHELOR, W. FOGDEN, A.,, “Accoustic Emission and Tack of Heat-Set Inks During Setting on Mwc-Papers and Fountain Solution Emulsification”, Submitted to Journal of Pulp and Paper Science (2006).
- VOLTAIRE, J., MATTILA, U., FOGDEN, A., NIEMINEN, S., REINIUS, H., “Accoustic Characterisation of Film Splitting in a Hswo Printing Nip”, International Printing and Graphic Arts Conference, 21-27 (2004).
- VOLTAIRE, J., HOC, M., FOGDEN, A., “Use of an on-Press Acoustic Sensor to Monitor Coldset Offset Printing of Newspaper”, Submitted to Nordic Pulp and Paper Research Journal (2005).
- BLOMBERG, E., HOC, M., “Evaluation of Methods for Determine the Linting Tendency of Newsprint,” Karlstads Universitet, Karlstads, Sweden, 2004.
- HEINTZE, H.U., “The Measurement of Linting Technology in Mechanical Printing Papers”, International Printing & Graphic Arts, 321-327 (1992).
- IGT, “Igt Aic2-5,https://www.igt.nl/igt-site-220105/index-uk/specs/specaic.html, IGT, 11th June, 2006
- BANHAM, P., “Reproducibility of Tape Pulls Method of Heidelberg Gto-52,” Norske Skog, Report, Boyer, Tasmania, 2005.
- SHANKS, F., “Quantification of Water Content in Process Ink with FTIR” Monash University, Report, Melbourne, 4th April 2003.
- FISHER, R.A., YATES, F., “Statistical Tables for Biological, Agricultural, and Medical Research”, 3rd Edition ed: London : Oliver and Boyd, 1957.
- BIRD, R., STEWART, W., LIGHTFOOT, E., “Transport Phenomena”: John Wiley & Sons, 1960.
- “Offset Plate Technology,https://www.internationalpaper.com/PDF/PDFs_for_Papers/Offset%2 0Plate%20Technology.pdf, International Paper Company, 7th June, 2006
- FUJIFILM, “Fujifilm Ps Plate Fns Negative Presensitized Aluminium Offset Plates,https://www.fujifilm.co.uk/gs/rdas/papp.asp?cmd=MCSearch&Industry=0, Fuji Photo FIlm Co., Ltd., 11th June, 2006
- FUJIFILM, “Fuji Film Graphic Arts Handbook”. Japan: Fuji Film.