A variety of composite manufacturing processes involve two mating surfaces in which the pressure distribution needs to be uniform for optimal process performance. Some of these processes include lamination pressing, resin transfer molding, and sheet molding compounding.
Uniform pressure distribution may be ensured by using pressure indicating film in setting-up presses and molding equipment. Once preliminary equipment set-up has been completed, pressure indicating film may be used to trouble-shoot issues that arise as production is ramped up. Additionally, quality control will benefit from the use of pressure indicating film as periodic checks on the pressure distribution will indicate pressure non-uniformities, hopefully before problems have developed in the production of composite materials. If problems are proactively avoided, rather than reacted to, then the manufacturing of out-of-specification composite materials are avoided, with obvious economic benefits. All the time, labor and material costs to make unacceptable parts are avoided.
In lamination pressing, a press is used for curing layers of pre-impregnated fibrous cloth (prepreg) after they have been assembled into a multi-layer structure, placed into a mold, and cured. Prepreg may be produced by dipping a fiber cloth (reinforcement) in a mixture of resin and solvent, and squeezing out excess resin using nip rolls as shown in Figure 1. An oven drives off the solvent and the prepreg is wound up along with a release film (paper or poly interleaf) to enable removal of a single layer of prepreg later. In these manufacturing processes there are two opportunities to use pressure indicating film. Nip roll alignment needs to be precise to provide consistent resin content throughout the prepreg. Putting pressure indicating film through the nip rolls will quickly indicate the pressure distribution applied to the prepreg. The magnitude and location of any needed adjustments to the nip rolls’ alignment will be indicated by the color-map provided by the pressure indicating film. The mold/press assembly must be properly aligned to provide a uniform pressure distribution to the prepreg. Again, pressure indicating film provides direction as to where and how large any needed alignment adjustments are.
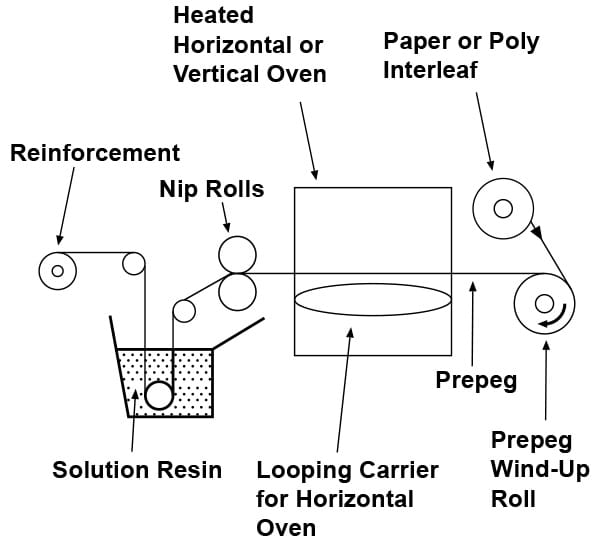
Figure 1. Schematic Diagram of the Solution Prepregging Process
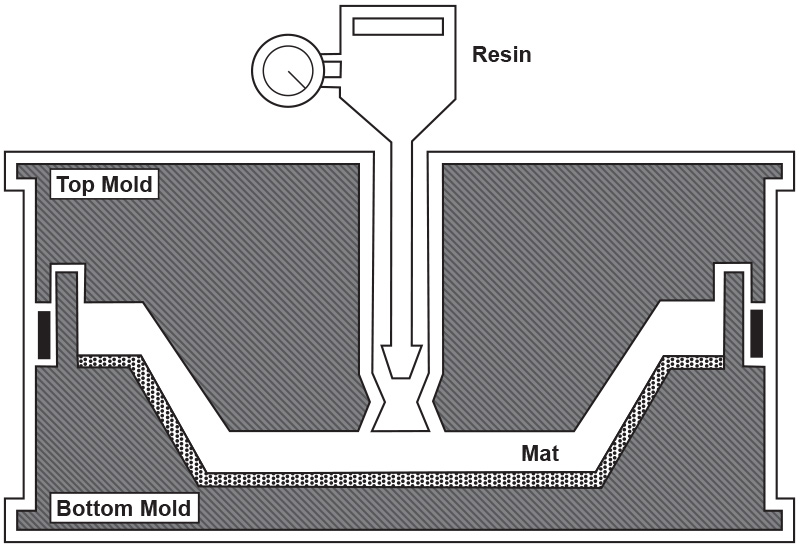
Figure 2. Schematic Diagram of Resin Transfer Molding Process
Pressure indicating film may be used in RTM composites production as well as development. Over time misalignment may creep into the mold assembly resulting in poor quality composite parts. When trouble-shooting the issue, pressure indicating film can provide understanding of the magnitude and location of needed adjustments. With such high-quality information provided for diagnosing the problem, the remedy will be accomplished quickly.
Sheet molding compound (SMC) composite material manufacture involves using a premanufactured combination of fibers and fillers with resin referred to as SMC. When the appropriate charge of this material is placed in a mold the SMC will flow as the mold is closed to fill the mold. Mold/press assembly alignment is critical to successful SMC manufacturing. Pressure indicating film may be used to ensure mating mold surfaces generate a uniform pressure distribution when the mold is closed.
Pressure indicating film provides a quick, easy-to-use, and cost-effective diagnostic tool for challenges of mold assembly misalignment and fibrous preform mobility in composite manufacturing. In process development, trouble-shooting, and quality control applications, pressure indicating film provides insight to both the magnitude and location of necessary adjustments by producing a color-map showing the pressure distribution in mating surfaces.