It is generally accepted that battery manufacturers reject over five percent of cells during manufacturing and testing. Two major causes of these rejects are cell leakage and failure of formation cycling and charge-retention tests. Leakage usually occurs when there are defects in the perimeter seals of cells or in fill tubes. Cycling and charge-retention problems are a result of defects in positive and negative electrodes. For economic reasons, all cell and battery manufacturers strive to eliminate these costly rejects.
Fujifilm Prescale® is a pressure measurement film that has can be useful in reducing or eliminating the defects discussed above. Fujifilm Prescale® is a mylar-based film that contains a layer of microcapsules. The application of force upon the film causes the microcapsules to rupture, producing an instantaneous and permanent high resolution image of pressure variation across the contact area. This image color ranges from light pink to dark magenta. The intensity of the color is proportional to the amount of pressure. The resulting Prescale® image can be compared against a correlation chart to quantify the pressure. Alternatively, the image can be scanned with optical imaging software, quantified, and displayed in several multi-colored formats.
Two specific manufacturing operations that benefit from the use of Prescale® are heat sealing of lithium polymer cells and calendaring of Li-ion electrodes. Prescale® can also be used to quantify the extent and distribution of pressure generated as cells or batteries expand during cycling.
Heat Sealing Lithium Polymer Cells
There are two heat sealing operations performed on lithium polymer cells. The first is the formation of the cell pouch containing the positive and negative electrodes and the separator membrane. The second is the final heat seal after electrolyte is injected into the cell.
After set-up of the manufacturing equipment, Prescale® should be used to verify that pressure is evenly distributed on the pouch laminates during the heat-sealing process. Uneven distribution of pressure can result in cell rejects due to leakage. The use of Prescale® to check the pressure exerted by the bonding equipment is illustrated below.
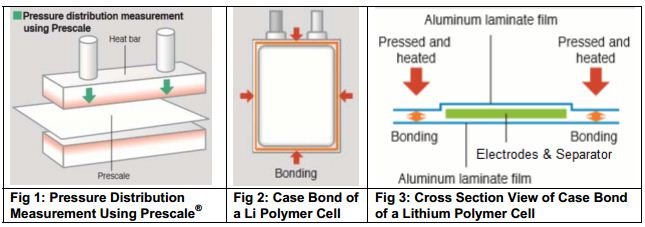
Figure 1 shows how Prescale® is used to check the pressure distribution along the bond line of a lithium polymer cell. The Prescale® is placed between the jaws of the heat-seal equipment and pressure is applied. Figure 2 shows the perimeter bond line, and Figure 3 shows a cross section view of the case bond. After pressing, the Prescale® image should be a consistent color, and the pressure exerted can be determined by the intensity of the color.
Figure 4 shows the results of some defective and acceptable images. The two defective images show that the heat bar is not parallel to the work. As a result, pressure is uneven across the bond line, and the effective area of the bond has been significantly reduced. In contrast, the image of the acceptable set-up shows uniform pressure across the bond. This set-up will result in uniform heat seals. Based on the above discussion, it is obvious that the use of Prescale® during heat-seal set-up operations will improve the quality of heat seals, which will result in fewer cell rejects.
Prescale® is also an effective tool in diagnosing the causes of cell leakage. For example, if cells have been rejected due to leakage along the bond lines, Prescale® can be used, after the fact, to determine whether the heat-sealing equipment is misaligned resulting in the poor bonds. However, it is always cost effective to verify the set-up with Prescale® before production operations commence, to prevent any defective heat seals.
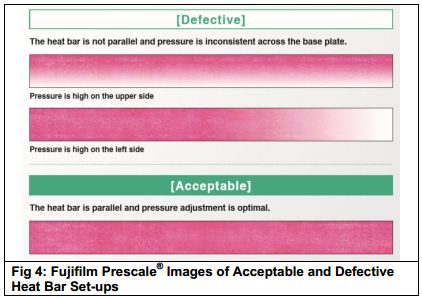
Calendering of Li-ion Electrodes
Formation cycling and charge retention problems in Li-ion cells are frequently a result of defects in the positive and negative electrodes. Three steps in the manufacture of electrodes are coating, drying, and calendering, but the calendering process is critical in establishing the proper condition of the electrodes. Calendering assures that the electrodes are properly densified, that they have consistent thickness, that they are flat, and that they have no surface defects.
A lack of parallelism in the calenders will produce a variation in the thickness of the electrodes, which will create winding problems as well as an increase of cell internal resistance. Calender wheels with surface defects will result in electrodes with surface defects that can lead to internal short circuits within the cell.
Prescale® can be used during the set-up of calendering equipment to check for scratches, dents or deformation and to check for parallelism of rollers after gap adjustment. Figure 5 shows Prescale® being inserted between the calender rolls. Notice that the color has changed indicating pressure exerted by the rollers.
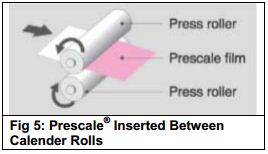
Figures 6 and 7 show the results of some typical images after Prescale® was passed through calender rollers. Prescale® makes it possible to identify damage on rollers such as scratches or dents. Prescale® also highlights lack of roller parallelism.
Using Fujifilm Prescale® is a cost effective tool to help prevent cell performance problems due to defects in positive and negative electrodes. Such defects may not be noticeable when the electrodes are made. They will, however, effect cell performance and may result in rejected cells during formation cycling and charge retention tests. In addition, cells with electrode defects may pass all in-house qualify assurance tests, but may have short cycle lives in the field.
Cycle Testing of Lithium Ion Batteries
Fujifilm Prescale® is also a useful tool that can be used during the development of Li-ion cells. When new cell designs are being developed, design engineers need to characterize the physical changes in cells that occur during charge and discharge. For example, lithium-ion cells swell during cycle testing. Usually, their maximum thickness is reached when fully charged. This occurs because lithium moves into the crystal lattice of the positive material during charge, expanding it.
During charge and discharge, Prescale® can be used to show the pressure distribution between cells and between cells and battery cases. It can also be used to quantify the pressure. Figure 8 shows a prismatic Li-ion polymer battery built for NASA. Figure 9 shows a typical Prescale® image generated during swelling of the battery cells. The highest pressure is in the center, and pressure lessens at the edges of the cell.
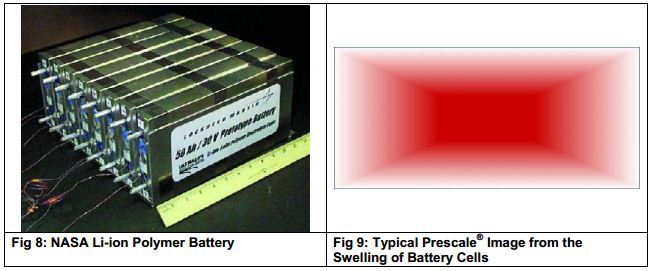