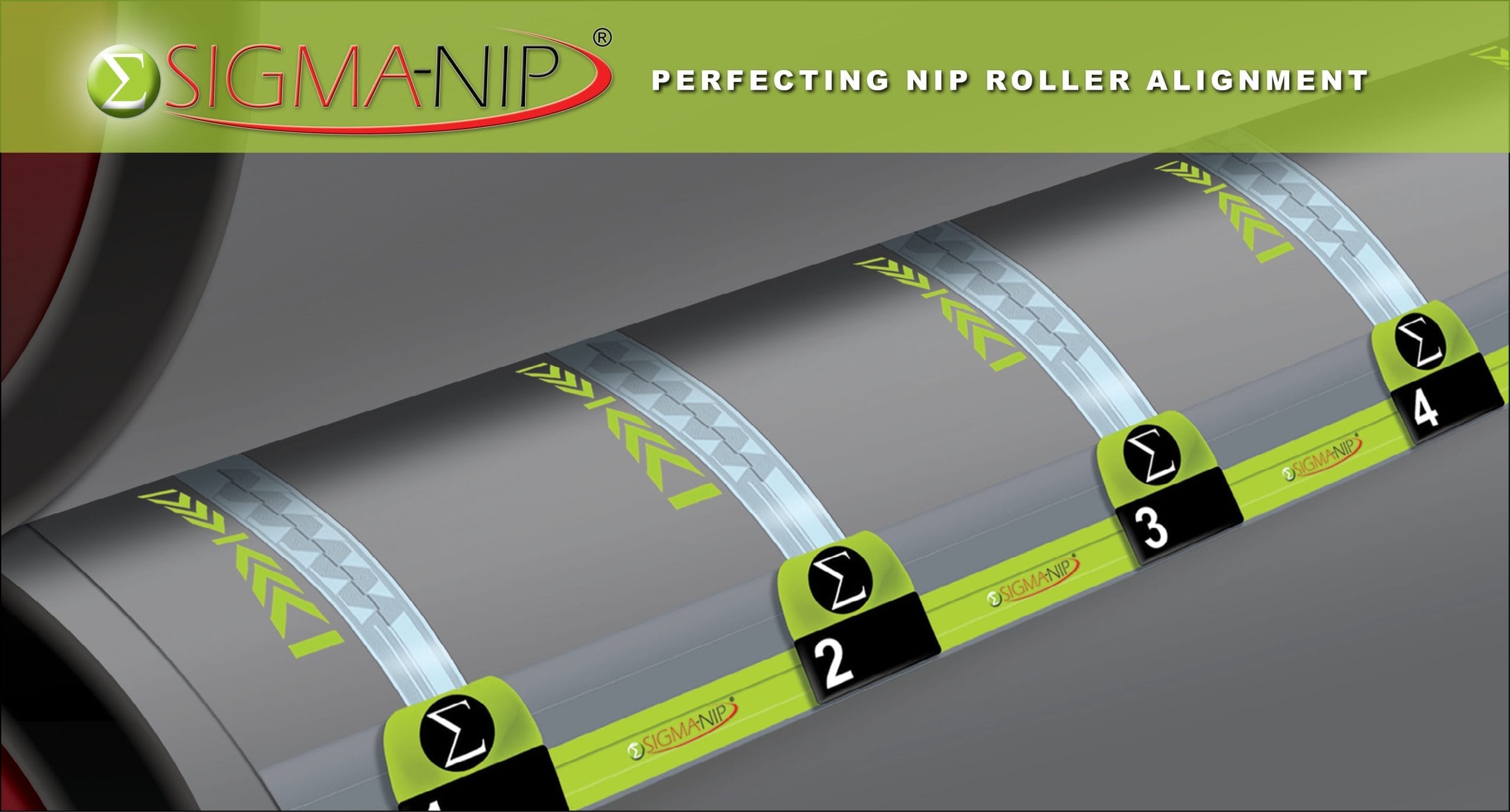
What people are saying about Sigma-Nip® …
“Sigma-Nip® has come a long way from concept to a reliable, easy to use nip profile measuring tool. It has successfully bridged the gap between conventional carbon paper impressions and the first generation of electronic nip devices. Being able to save and review the entire real-time data from nip closing to nip opening is extremely useful, however, the ability to correlate accurate nip width data to roll deflection is an exceptional benefit.” – Mike Stoltz, Metso Paper USA
“Sigma-Nip® is an extremely helpful tool for troubleshooting in printing presses and has saved my colleagues and I significant amounts of time. It allows us to assess what is happening where the actual printing takes place and quickly get to the source of the problem. This is a new tool for us and the industry, but I foresee more and more printers starting to use this system as people begin to see its advantages.” – Don Jordan, Abitibi Consolidated
Sigma-Nip® – an electronic nip analysis system, calculates and records nip width at multiple points across your rollers face length in real-time with unprecedented speed, accuracy and repeatability. The new Sigma-nip® system is not only more accurate, but can handle higher pressures than ever previously attainable.
Sigma-Nip® presents a revolution in quality control. Now, for the first time ever the technician is able to accurately, efficiently and economically measure roller profiles and alignment condition. Sigma-Nip® consists of a series of thin-film resistive ink pressure transducers on a carrier sheet. As this carrier sheet is loaded in between your rollers the Windows based software assimilates the readings into easily interpretable graphical images – all in real-time.
What Is Sigma-Nip®
Sigma-Nip® consists of a series of sensor elements that are placed in between two contacting rollers. Immediately upon closing of rolls, the sensor begins recording precise nip width measurements allowing you to instantaneously determine whether your rollers are aligned properly and are squeezing together sufficiently. Sigma-Nip® is a real-time system. What that means is that your roller adjustments can be made WHILE the sensor is actually in the closed (non-rotating) nip. This allows for unprecedented flexibility and speed.
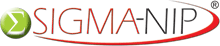
Schedule a Live Product Web Demo
Download
- General Brochure
- General Brochure – Chinese
- The Benefits of Sigma-Nip
- The Benefits of Sigma-Nip – Portuguese
- Paper Industry
- Printing Industry
- Mini Sigma-Nip
- 15 Sensor Chain Illustration
- New Sigma-Nip Sensor for Small Nip Widths
Related Products
Articles
- Iron & Steel Technology
- Iron & Steel Today
- World Tobacco
- Nonwovens Report International
- Industrial Products Finder
- RFP Magazine
- Paper Making & Distribution Magazine
- Opapel (Portuguese)
- Finnish Magazine – Paperi ja Puu
- Artesgraficas.com
- IPW Magazine
- Africa and Middle East Textiles
- Newspapers & Technology
- Paper Industry
- Paper Film & Foil Converter
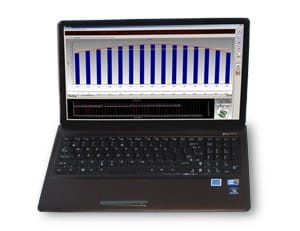
Designed For Productivity
Sigma-Nip® comes complete with everything you need to quickly and accurately take nip impressions. Sigma-Nip® is designed with the intention of being used during routine maintenance or set up and is quickly disposed across the roller surface by just one person. The system is modular and portable and quickly interfaces to the USB port on any standard Windows laptop.
Why Use Sigma-Nip®
Proper roller alignment and pressure level are critical for both print clarity and web control. An evenly loaded roller set is much less likely to cause costly web breaks and sheet “walking”, wrinkles, or fold-overs. Simply by virtue of routine tests, Sigma-Nip allows the user to greatly extend blanket life.
Benefits
- Quickly and accurately take nip impressions
- Intuitive and user friendly Software
- Modular and portable
- Designed with the intention of being used during routine maintenance
- Interfaces with any standard Windows computer through your USB port
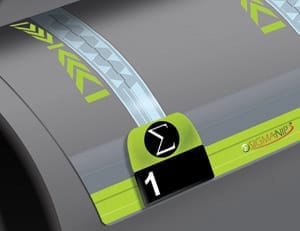
Sigma-Nip® Technology
Through the application of sophisticated mathematical algorithms, Sigma-Nip® is able to discern the contact profile of the machine’s cross direction with a higher degree of accuracy never before attainable. Each sensor is individually calibrated, serialized and carefully assembled to exacting tolerances. The sensor is designed to withstand repeated high pressures, conform to radiused surfaces and routine exposure to grease, liquids and inks.
System Specifications | |
Sensor Technology | Resistive Ink |
Cycle Speed | 1 FPS |
Accuracy | ± 6% |
Repeatability | ± 98% |
Disk Space | 200 MB |
RAM Size | 128 MB RAM |
Connection | USB Port |
Compatibility | Windows® 2000 / XP / Vista / 7 |
Sensor Specifications | ||
Standard Sigma-Nip® | Mini Sigma-Nip® | |
Active Sensor Area | 8.4 in (21.3 cm) | 4.21 in (10.7 cm) |
Sensor Thickness | 15 mils (0.381 mm) | 5 mils (0.381 mm) |
Usable Temp. Range | 0 to 250°F (-17.7 to 121°C) | 0 to 250°F (-17.7 to 121°C) |
Resolution | 0.05 in (0.13 cm) | 0.02 in (0.5 mm) |
Nip Width Range | 0.15 to 8.4 in (0.38 to 21.3 cm) | 0.06 to 4.21 in (0.15 to 10.7 cm) |
Min. Pressure | 40 PSI (2.8 kg/cm2) | 40 PSI (2.8 kg/cm2) |
Max. Pressure | 10,000 PSI (703 kg/cm2) | 10,000 PSI (703 kg/cm2) |
Max. Exposure Time | 300 Sec | 300 Sec |
Sensing Points | 168 | 168 |
Substrate Material | PET | PET |