Valeria Antonelli1, Dieter Decoster2, Roelof Marissen1, Adriaan Beukers1
1Delft University of Technology – Kluyverweg 1, 2629HS Delft, The Netherlands
URL : www.dpcs.lr.tudelft.nl
e-mail: V.Antonelli@tudelft.nl; R.marissen@tudelft.nl; A.Beukers@tudelft.nl 2Sirris – Technologiepark 915, 9052 Zwijnaarde, Belgium Institute yyyyy – Postal address URL: www.sirris.be e-mail: dieter.decoster@sirris.be
ABSTRACT
The present paper presents the results of a study aiming at the reduction of developments costs for the design of an adequate rubber mould during pressure forming of thermoplastic parts. In this paper the problem in the present production technique is presented. An improvement in the production method which has recently been developed and patented at the Delft University of Technology is described as well. The latter allows a more uniform pressure distribution during the forming phase and the production of a wider range of products without the need to design a new rubber mould for each product. Finally test results comparing the pressure distribution during the forming phase of the product with the classical method and the improved one are presented.
Key words: Rubber forming, Fibre Reinforced Thermoplastics
Introduction
Rubber forming of thermoplastic composites is a technique which allows the series production of parts with high mechanical properties [1]. Most of the time the products made with rubber forming are small, simple single curved shapes due to the difficulties in designing the appropriate rubber mould. The design of more complicated parts (i.e. doubly curved products or parts with sharp edges) is difficult, this makes development costs high and outcomes uncertain.
In order to reduce the development costs, a research program has started at the Delft University of Technology, aiming at better understanding both rubber mould behaviour and the thermoplastic composite during the rubber pressure. The difficulties in the design of rubber moulds and the resulting long development time and the consequent costs are due to the high friction between the laminate and the moulds and the high coefficient of thermal expansion of the rubber used. The first causes deformations on the corners and small areas of the rubber, reducing the pressure just in those areas where pressure is needed to form an optimal product. Moreover, this effect is even more evident during production, because the rubber mould heats up, increasing in volume and consequently increasing friction.
THE CLASSICAL RUBBER FORMING PROCESS
A typical rubber forming set-up consists of a rigid mould, a flexible (rubber) mould and a clamping or sliding frame.
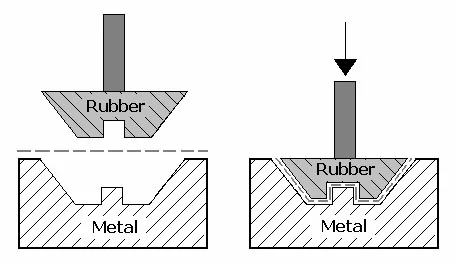
Fig. 1. Principle of rubber forming
When the hot laminate is positioned between the two moulds the press is closed and the product is formed. Forming times of 1-5 seconds are normal in rubber forming. When the shape is formed and final consolidation is assured, the product must be cooled down under pressure. After cooling down, the product can be taken out of the mould.
The rubber used for the press forming of thermoplastic composites is a silicone base rubber with a very high coefficient of thermal expansion, of the order of 10-3 cm/cm/degree. This means that even when the product to be manufactured is small, the increase in volume of the mould is significant, especially when small details are changing the shape of the product.
During series production the thermoplastics are heated up to about 250 °C. The heat exchange from the hot product towards the rubber causes a considerable temperature increase of the rubber. The measured temperature inside the rubber mould during series production showed values up to 160 °C.
The pressure distribution during pressure forming
To be able to acquire data on the pressure distribution during pressing of thermoplastics, a test set up has been built [2] as shown in the figure below. The tests have been carried out on a 25 Tons static Zwick Roell testing machine equipped with an oven, to be able to carry out tests at higher temperature.
One rubber mould has been used in all the experiments presented, it has dimensions determined from the metal mould, but with 1 mm space left at the sides to allow the presence of the laminate. The rubber is Silastic M, from Dow Corning, a silicon rubber of hardness (shore A) 55 which can withstand temperatures up to 250 °C.
The laminate is a substitute of the thermoplastic laminate, where a rubber matrix replaces the thermoplastic one to simulate the same viscosity and friction during the process and allow for static tests.
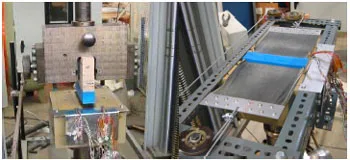
Fig. 2 Test set up.
To verify the influence of the temperature changes, several tests have been carried out with and without laminate at different temperatures, from room temperature up to 75 °C. Unfortunately it was not possible to test at higher temperatures due to the maximum service temperature of the used strain gauges.
To investigate the influence of lubricants, tests have been carried out in the normal test conditions and with some sort of lubricants.
The test set up consists of a steel mould for press forming of U-beams. This shape is very useful because it allows carrying out tests in which the only parameter that has to be taken into account is the rubber mould, as in-plane shearing of the fibres is not present. The mould allows the production of beams of different heights and widths. The results that are presented in this paper though are for beams of 40 mm wide and 40 mm high. The length of the mould is 180 mm.
In the
centre of the mould a series of pressure sensor is placed as shown in Fig. 3. This way the pressure distribution on the three sides of the mould can be obtained, so that it is possible to verify whether the distribution is constant, as desired.
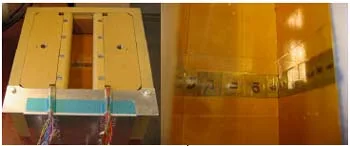
Fig. 3 Metal mould and position of strain gauges
2.1a Results
The effect of friction is analysed in two ways [3, 4]. At first the effect of the coefficient of thermal expansion is analysed without laminate, in order to be able to quantify the pressure distribution due to the shape of the mould during the process. Secondly, the laminate is pressed together with the rubber in the steel mould to verify the effect of friction among the different components due to thermal expansion.
Fig. 4 shows the pressure distribution at different temperatures without a laminate where it is evident that even without laminate there is a decrease of pressure at the corners. The loss of pressure is about similar, independently from the temperature. This is due to the fact that the same rubber mould has been used in both experiments with the same clearance of 1 mm at each side of the mould. Thermal expansion effects are therefore negligible as compared to this large clearance.
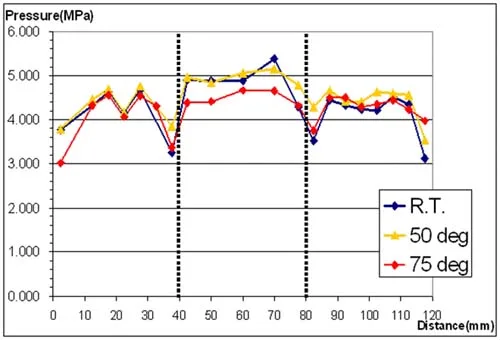
Fig. 4 Pressure distribution without laminate.
In Fig. 5, the reduction of pressure on the corners due to the friction between moulds and laminate is evident even at temperatures lower than the actual processing temperature.
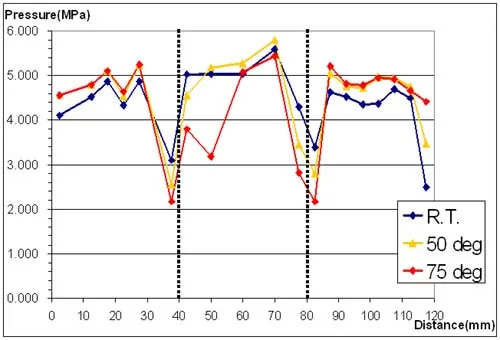
Fig. 5 Pressure distribution with laminate.
The same test set up has been used to investigate the possible improvements in pressure distribution using several lubricants [5] and the results are shown in Fig. 6.
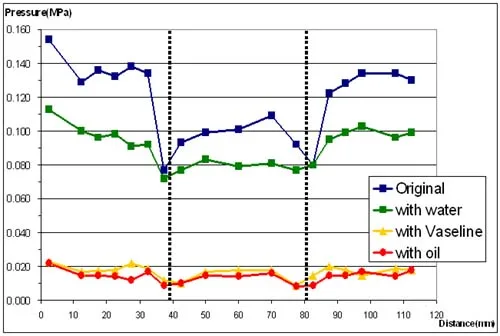
Fig. 6 Effect of lubricants.
Even with water as lubricant there is a reduction of the average pressure of 24%, while for Vaseline and oil the friction is reduced of 86% and 88% respectively. Fig. 7 shows the effect of oil as lubricant during the pressure forming of a laminate at a working temperature of 75 °C. Also in this case the effect of lubrication is evident, being the loss of pressure in the corners decreased of 25%.

Fig. 7 Effect of lubricant at higher temperatures
2.1.b Conclusions
From the work shown in this paper, it is evident how much the friction is influencing the pressure distribution during press forming of thermoplastic composites. Being the rubber mould produced at room temperature using the steel mould as negative mould, the thermal expansion is not considered during the fabrication of the rubber mould. A compensation for the thermal effects is not straight forward. This increases the development time especially when details are included in a product, or when sharp edges are present which, at the processing temperature are shifted from the position they had at room temperature.
One method which is investigated in the present paper is to use lubricant to decrease the friction between the moulds and the thermoplastic. This method looks promising, but it does not eliminate completely the loss of pressure distribution in delicate areas and has the disadvantage of possible performance reduction of the thermoplastic product.
3. THE IMPROVEMENT IN THE RUBBER FORMING PROCESS
In an effort of improving classical rubber forming method and eliminate the classical problems described above, a variation of this production technique has been developed and verified with tests [6].
Instead of using a solid rubber mould, the method uses a collection of rubber particles which, when pressed inside the metal mould, tend to fill it completely creating a uniform pressure distribution. The method is exemplified in Fig. 8. The rubber particles are held in a container connected to the press. When the thermoplastic composite has reached its matrix melting temperature and is placed between the mould and the container, the particles are pressed inside the metal mould, this forming the thermoplastic into the right shape. In this case the rubber particles act as a fluid, creating a more uniform pressure distribution and eliminating the problems related to thermal expansion of the rubber.
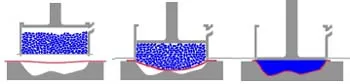
Fig. 8 Graphics of the method.
In order to verify the homogeneity of the pressure distribution during the process and to qualitatively compare it to the pressure distribution of the traditional method, simple tests using a Pressurex® film have been used. Fig. 9 shows the pressure distribution in a stroke of the U-beam metal mould when a solid pressure mould is used. Here it is visible, as in the previously discussed experiments, that the pressure in the corners of the mould is decreased.

Fig. 9 Pressure distribution with a solid rubber mould.
The same test has been carried out using rubber particles and is shown in Fig. 10. Here a much more uniform pressure distribution is shown, together with some small irregularities due to the prints of the particles, as shown in Fig. 11.
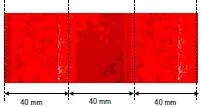
Fig. 10 pressure distribution using rubber particles.
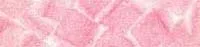
Fig. 11 detail of the pressure distribution
In order to reduce the prints of the particles, ellipsoidal rubber particles have been manufactured. This shape has in fact the potential to achieve a denser packing and therefore reduce the imprinting in the final product. The uniformity of the pressure distribution has also been tested in the case of a hemispherical shape. The pressure distribution of cubical and ellipsoidal particles has is shown in Fig. 12.
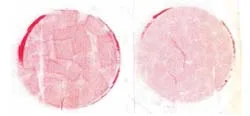
Fig. 12 Effect of different rubber shapes.
Here it is visible how the ellipsoids give a finer imprint with less voids in-between. The imprint is though only an aesthetic problem which is not influencing the mechanical characteristics of the thermoplastics part. Moreover the imprint is visible only on one side of the product, giving the possibility of choosing which side needs to be smooth. This is anyhow a characteristic of many manufacturing techniques for FRP.
4. CONCLUSIONS
The presented improvement in the rubber forming method has the potential to outclass the method as it is used at present. This method in fact would allow the manufacturing of any shape, including shapes with undercuts, eliminating both development and manufacturing of a rubber mould for each product. The following step in this research will be to investigate the pressure distribution in the actual production conditions for both techniques improving the test set-up described earlier in this paper.
REFERENCES
- ROEBROEK L.M.J., The Development of Rubber Forming as a Rapid Thermoforming Technique for Continuous Fibre Reinforced Thermoplastic Composites, PhD Thesis, Delft University Press 1994
- DE BIE R., Tooling Design for Rubber Forming of Thermoplastic Composites, Master Thesis, Delft University of Technology 2004
- DE BRUIJN G., Pressure Distribution During Rubber Forming of TPC’s, Delft University of Technology 2003
- BUIJS E., Mould Pressure Distribution Analysis in the Press Forming of Thermoplastic Composites”, Delft University of Technology 2005
- HUANG C.Y., “A Fundamental Investigation of the Friction Effect Upon Rubber Forming of Thermoplastic Composites”, Delft University of Technology 2005
- DECOSTER. D., Novel, universal pressure moulding process for thermoplastic composites, using a collection of rubber particles as pressure medium, Master Thesis, Delft University of Technology 2007