BSc Clemens Oertela*, DI Heinz Neuburgera,b, FH-Prof. Ing. MMag. Dr. Anton Saboa
Abstract
Abstract In this paper the development of a test bench which can be used to check the behaviour of bicycle brakes (disc brakes and in the next stage of extension rim brakes) during a brake cycle under dry and wet conditions is described. Additional, there is the option to perform endurance tests. For the dimensioning of the test bench, calculations of theoretical possible brake torques, measurements with acceleration sensors, high speed camera and Fuji Prescale measuring Films have been done. A special focus was laid on usability and the reducing of the mechanical changing time during serial tests. The programmed real-time control, based on a LabView RealTime System was created to automate the test procedure as it is defined in the test protocol. The system gives information about brake hysteresis function, a function connecting the lever(hand)- and measured brake force(torque).
Keywords: mountain bike; road bike; bicycle; brake; disc brake; rim brake; test bench; measuring equipment;
1. Introduction
To get objective statements about the behaviour of bicycle brakes under defined conditions, there is the need to find another test option besides the outdoor tests, in which only subjective statements from the rider or measured field data under not reproducible conditions can be found. Therefore, a test bench was built which makes it possible to investigate different brakes under identical conditions (dry and wet) in the laboratory. With the developed equipment, a hysteresis [1] function can be logged, that gives information about the relation of the applied lever force, caused by the rider’s hand/fingers, and the measured brake force which decelerates the rider-bike-system. With this information, several statements can be made, e.g. if the brake is acting strong or powerless or if it is easy to handle in critical situations or not. Additional any changing of the brake, like using other brake-pads, special brake discs or changing the brake’s piston diameters in the development process can be controlled objectively. The whole test bench, in the final development state, should be able to check any rim and disc brakes available on the market for their handling and endurance behaviour.
![Fig. 1- left to right: side-pull caliper brake (rim brake) for road bikes with one centred mounting bolt; V-brake (rim brake) for city-, trekking- and mountain bikes; a disc brake (hub brake) for mountain bikes mounted by IS2000 standard [2] figure 1](https://www.sensorprod.com/wp-content/uploads/2023/08/figure-1-8.jpg)
Fig. 1- left to right: side-pull caliper brake (rim brake) for road bikes with one centred mounting bolt; V-brake (rim brake) for city-, trekking- and mountain bikes; a disc brake (hub brake) for mountain bikes mounted by IS2000 standard [2]
Brakes for bicycles are categorized by their acting position [3]. This means, if the brake force is applied at the hub of the wheel or at the rim. In Fig. 1 the three most popular brake-designs are displayed. The left and the middle ones are rim brakes, the right one is a disc brake of the category hub brakes. The one on the left, a single pivot sidepull caliper brake, is mostly used for road bikes in a modified version. The brake is mounted by just one centre mounting bolt, which is located directly over the wheel. The V-brake, shown in the mid picture, is mounted on two bolts, which are fixed on the seat stays or the fork blades left and right from the wheel. On the right hand side, a disc brake is shown, which is mounted by two hex screws on the left fork blade or on the left seat stay, based on the IS2000 [2] standard for bicycle disc brake mounting. Another common mounting standard is Postmount [2].
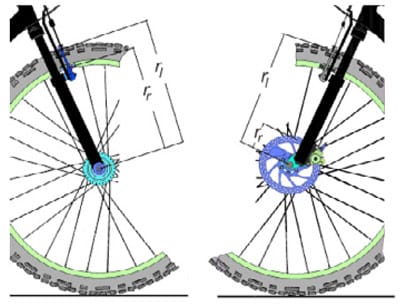
Fig. 2 – comparison of the different acting radius (rr) of rim and hub brakes; on the left, the rim brake radius is shown, on the right the hub brake radius; additional the wheel radius (rl) is shown.
The most important mechanical difference of these two categories (rim and hub brakes) is the acting radius (rr), which is important for the brake torque as shown in Fig. 2. The smaller the acting radius is, the higher the friction force has to be to produce enough brake torque, which decelerates the rider. To get the same brake force, the friction force of a disc brake (rotor diameter 160mm) produced by the friction of the brake pads and the brake disc is about 3.5 times higher, compared to a rim brake between brake pads and rim to equalize the shorter lever arm. A realistic brake force at the front wheel, when a bicycle rider (80kg) in upright position (it depends on the position and the geometry of the bike) does a rollover, is in the region of about 400N. To produce this brake force, a disc brake with a 160mm rotor needs to produce a friction force of about 1666N. Calculating with a friction coefficient of about 0.5, the applied force, which pushes the brake pads against the brake disc must be 3332N. If the rider is heavier and shifts his centre of mass backwards, the possible brake forces can rise up to over 700N (measured). This brake force is produced by possible hand forces of about 100-150N. Basing on 400N rollover force and an applied hand force of about 80N means, the overall transmission ratio of the brake (mechanical and hydraulic ratio) is about 40-45.
2. Measurements and results for the dimensioning
The key factors to construct a well designed test bench are the knowledge of the appearing mechanical values, such as the maximum brake torque, the applied hand force and the velocity of the brake lever. To find out these values several measurements took place.
To find out the reachable brake torque or brake force, two different approaches were chosen. One was to check the maximum reachable value of the deceleration with the help of a three-dimensional acceleration sensor, which was placed on the top tube of the main frame of a mountain bike. The measurement setup was built out of a sensor platform called “Neon” (Spantec GmbH, Gumpendorferstrasse 132/2/5, 1060 Vienna, Austria). This sensor platform does a 10bit a/d conversion and records the data on an SD-card or digitally transmits them via ANT+ wireless communication to a computer. The chosen three-dimensional acceleration sensor type was MMA7260Q (Freescale Halbleiter Deutschland GmbH, Schatzbogen 7, D-81829 Munich, Germany). Its measurement range was set to +/- 1,5g.
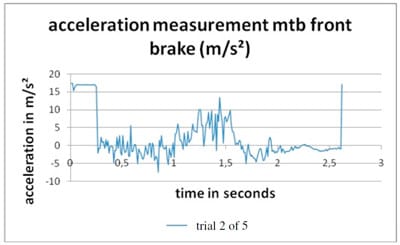
Fig. 3 – Acceleration measurement showing a maximal braking when just using the front disc brake (Avid Juicy seven, 203mm rotor) of a mountain bike. Positive values representing deceleration; start of braking at about 1 second; high values at the beginning and end are from the trigger signal; no filtering was used because the measurement only needs to equal a rough estimate area for the construction in cooperation with the other measurements. Quite exact data weren’t needed.
The rider was familiar to the brake and the bike. He was advised to shift back his centre of mass as far as possible and brake as hard as possible at the border of nearly losing the ground contact of the back wheel. The subjectively best three trials out of five were averaged. To obtain one single acceleration value per trial and to eliminate measurement inaccuracies an average was calculated for a time span of 0.15s before and after the local maximum. For example: the maximum deceleration in Fig. 3 occurs at about 1.45s. The found result was 6.62ms-2. With a system weight of about 120kg the acting brake force is 794N (1).

The second method to find the maximum brake force was to use Fuji Prescale measurement films (Fuji Film Europe GmbH, Heesenstr.31, 40549 Düsseldorf, Germany). These films are indicating applied pressure differences as red colour density variations. These films were positioned between the brake pads and the brake disc while applying a force of FH = 100N at the brake lever. The found pressure was about 12Nmm-2 The measured pressure multiplied by the pad area, which is pressed against the disc (420mm²), equals a contact force of FR = 5040N. With (2) a brake force FB = 775N was calculated (µ=0.5, rdisc=0.102m, rwheel=0.33m).

According to the results of the motion analysis, which was done with Simi Motion (SIMI Reality Motion Systems GmbH, Unterschleißheim, Germany) and the camera VDS Vosskühler HCC-1000 (VDS Vosskühler GmbH, Weisse Breite 7, 49084 Osnabrück, Germany), an average pulling velocity of the brake lever under resisting force of the brake system was found to be 0.18ms-1. Three different subjects were tested with the advice to pull five times as fast and hard as possible. One subject activated the brake with two fingers, two with one. The maximum releasing velocity was between 0.2 and 0.3ms-1.
3. Construction
With the measured values the test bench could be dimensioned. To get an advantage in comparison to the outdoor tests, the whole test process has to be precise, guarantee constant conditions, requires a small number of test personnel as well as having a fast throughput.
The concept was to use a powerful three-phase engine with a worm gear (Fig. 4 , 3 and 4) on whose shaft a hub (Fig. 4, 7) with the brake disc is mounted. The force values are measured with two load cells, one for the hand force and one for the resulting brake force. Controlling is done with a real-time controller system (compactRIO cRIO- 9073, a real time controller including FPGA) and a LabView2009 application (National Instruments, Austin, TX, USA)
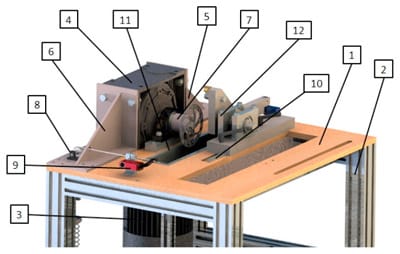
Fig. 4 – overview of the test bench; 1. baseplate, 2. construction profile system, 3. three-phase engine, 4. worm gear, 5.&6. engine mounting construction, 7. hub with mounted brake disc, 8. direction change for the wire rope, 9. brake lever, 10. fitting key, 11. water reservoir to collect splash water, 12. lever arm assembly
The hand force is produced with a Fluidic Muscle (Festo AG & Co. KG, Esslingen–Berkheim, Germany) which works pneumatically. The Fluidic Muscle is in line with the load cell. Via the load cell the cable, which is fixed at the brake lever to apply the hand force, is pulled. To control the process of pulling the lever with a defined force, the pneumatic valve and the load cell are in a controlling cycle, which is programmed on the FPGA (Field- Programmable-Gate-Array). The advantage of the FPGA is that the controlling cycle is “built in hardware” using logical gates and because of that, the system can work autonomous. That means computer hang-ups or timing problems caused by the operating systems do not affect the quality of the measurement or the safety of the device. The controlling frequency is 1000Hz.
The engine drives the brake disc with a constant speed. It is powerful enough to keep the adjusted rotation speed of the disc during the whole brake cycle constant. The brake caliper (Fig. 5, 7) is mounted on two round steel profiles (Fig. 5, 6), which are acting as an adapter for quickly connecting the brake caliper to the so called lever arm assembly (Fig. 4, 12 or extracted Fig. 5).
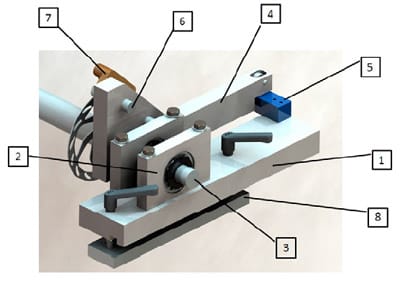
Fig. 5 – lever arm assembly; 1. baseplate, 2. bearing housing with ball joint bearing, 3. main axle, 4. lever arm, 5. beam, 6. adapter for brake caliper fixation, 7. brake caliper, 8. holder-up
The lever arm assembly is the main assembly which allows measuring the brake torque. The brake caliper is placed via adapter on the long lever arm (Fig. 5, 4). The position of the adapter with the caliper is constructed according to the Postmount standard. The lever arm has a main axis (Fig. 5, 3) around which it can turn. This axis is coaxial to the driving shaft on which the brake disc is mounted. If the brake disc rotates and the brake is operated, the whole lever with the brake caliper would turn around its axle. To make a statement about the brake torque, the lever is held by a beam (Fig. 5, 5), which inhibits the rotation of the lever arm. With the help of the beam, a force can be measured, which is proportional to the produced brake torque. The brake force can be calculated by dividing the measured value from the beam by the specified lever arm of the beam (distance between main axle and beam). This calculated brake force, in relation to the applied hand force, results the brake hysteresis [1]. This information can be used to interpret the behaviour of the brake. The brake force is a calculated value, based on the values of the beam. The brake force is the force, which decelerates the bike-rider-system in practice. It acts at the touching point of the wheel and the ground. Its direction is against the riding direction.
To realize a high throughput when doing serial tests, the already mentioned adapter solutions are becoming important. With the help of them and the ability to slip the whole lever arm assembly to the side (shown in Fig. 6 to Fig. 9), the brakes system can be changed and adjusted in a very short amount of time.
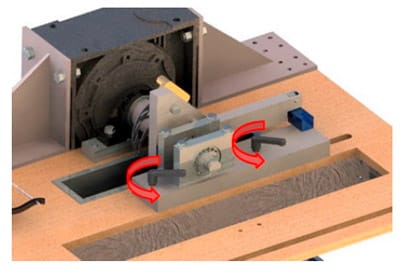
Fig. 6 – opening the clamps to push the assembly to the side
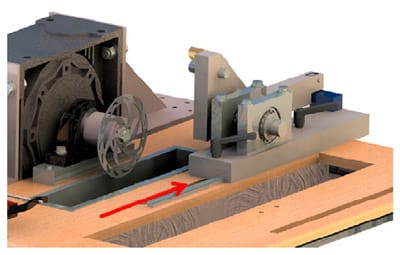
Fig. 7 – pushing the assembly to the side for changing disc and brake caliper

Fig. 8 – changing of the hub adapter with the mounted brake disc and the round steel profiles with the brake caliper
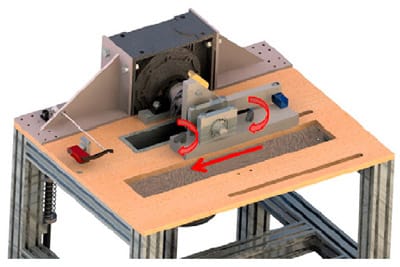
Fig. 9 – back pulling of the lever assembly and fixing the clamps again
4. Discussion and Conclusion
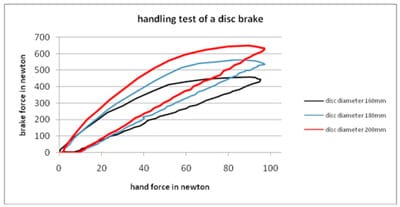
Fig. 10 – results of the same disc brake model with different disc diameter 160/180/200mm; moving average of 3 values was used
After evaluating and calibrating, the first test series took place. In Fig. 10 the results of one disc brake model of the year 2010 are shown. The model was tested with three different types of brake discs, varying in diameter and geometry of the friction ring. The characteristics of the brake cycles are nearly identical, the only significant differences between the three functions are as expected the rise of the function and the maximum reached brake force. The reached maximum forces are matching the expected behaviour of the interpreted effects of the different disc designs.
References
- Speedkiller. Ottmar, Dipl.-Ing. S. 12/08, München : Delius Klasing Verlag GmbH, Bielefeld, Germany, 2008, p. 35.
- Hayes Disc Brakes. Hayes Disc Brakes – Support & Downloads. [Online] [Cited: 25 01 2010.] https://www.hayesdiscbrake.com/support_downloads.shtml.
- Peter Barzel, et al. Die neue Fahrradtechnik: Material, Konstruktion, Fertigung. Bielefeld, Germany : BVA Bielefelder Verlag, 2008. ISBN: 978-3-87073-322-3.