Christopher P. Menchini, Douglas Dierdorf, Ph.D., Jennifer L. Kalberer, Michael J. McDonald, P.E., Kristofor S. Cozart, Adriana Casarez
Applied Research Associates, P.O. Box 40128 Tyndall Air Force Base, Florida 32403
Virgil J. Carr, Jr.
Air Force Research Laboratory
Final Technical Report, February 2007
DISTRIBUTION STATEMENT A: Approved for public release; distribution unlimited.
Air Force Research Laboratory
Materials and Manufacturing Directorate
Airbase Technologies Division
139 Barnes Drive, Suite 2
Tyndall AFB, FL 32403-5323
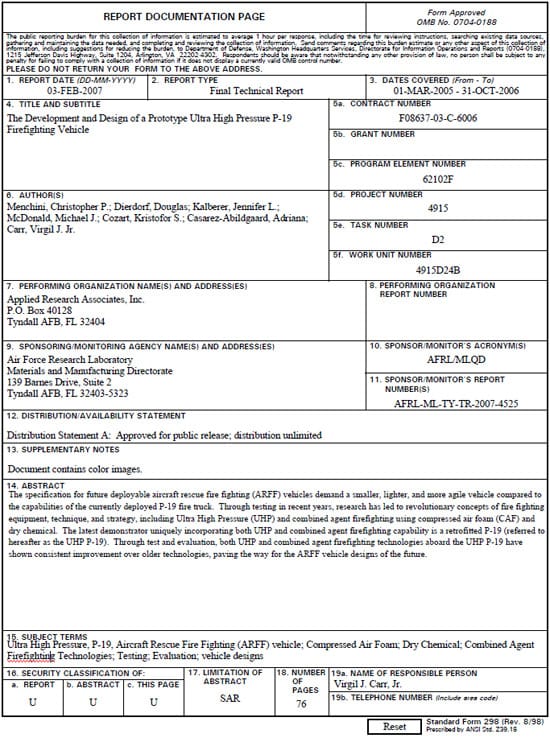
This report is published in the interest of scientific and technical information exchange, and its publication does not constitute the Government’s approval or disapproval of its ideas or findings.
Abstract
The specification for future deployable aircraft rescue firefighting (ARFF) vehicles demands a smaller, lighter, and more agile vehicle compared to the capabilities of the currently deployed P-19 fire truck. The long term goal of this effort is to reduce the vehicle footprint by incorporating state of the art technologies such that two vehicles can be transported on a single C-130J. Through testing in recent years, research has led to revolutionary concepts of firefighting equipment, technique, and strategy, including ultra high pressure (UHP) and combined agent firefighting using compressed air foam (CAF) and dry chemical. In general, developmental efforts have since delivered several prototypes for these individual concepts through multiple iterations and varying purpose. The latest demonstrator uniquely incorporating both UHP and combined agent firefighting capability is a retrofitted P-19 (referred to hereafter as the UHP P-19) which has also completed performance testing in support of a future ARFF vehicle specification. The UHP P-19 has also been evaluated by ARFF trainees of the 823rd Red Horse Squadron who gave the platform a “hands-on” excellent overall review. With successful conclusion of UHP P-19 testing, both UHP and combined agent firefighting technologies have been well characterized showing consistent improvement and potential over older systems. Due to this achievement, the UHP P-19 test bed can be used as a valid foundation for ARFF vehicle designs of the future. iii
Description | Abbreviation |
Two-Dimensional | 2-D |
Three-Dimensional | 3-D |
Air Force Base | AFB |
Air Force Civil Engineering Support Agency | AFCESA |
Air Force Research Laboratory | AFRL |
Aqueous Film-Forming Foam | AFFF |
Applied Research Associates, Inc. | ARA |
Aircraft Rescue Firefighting | ARFF |
Compressed Air Foam | CAF |
Carbon Dioxide | CO2 |
Electric Discharge Machining | EDM |
High Reach Extendable Turret | HRET |
Fire Research Group | MLQD |
Fire Extinguishing Effectiveness Test | FEET |
First Response Expeditionary | FRE |
High-Mobility Multipurpose Wheeled Vehicle | HMMWV |
Military Specification MIL | SPEC |
Potassium Bicarbonate (Dry Chemical) | PKP |
Ultra High Pressure | UHP |
United States Air Force | USAF |
Volume of Fluid | VOF |
Chapter 1: Introduction
1.1 Background
The Air Force Research Laboratories (AFRL) Fire Research Group (MLQD), in coordination with the Air Force Civil Engineering Support Agency (AFCESA), are working on the specifications for the next generation aircraft rescue firefighting (ARFF) vehicles for deployed locations. The P-19 has been a highly successful ARFF vehicle, becoming the backbone for US military operations both overseas and stateside. However, this aging fleet of vehicles built in the mid-1980’s will need replacement in the near future, creating the need for a new firefighting vehicle. Three major goals were identified for designing the next generation deployable ARFF vehicle including reducing the footprint and weight for easier transport, increasing the firefighting capability using innovative technologies with current firefighting agents, and improving the maneuverability of the vehicle for off-road applications. In recent years, AFRL has pioneered the development of revolutionary concepts in firefighting equipment, technique, and strategy that will provide the basis for new military ARFF vehicle designs.
1.2 Scope
The purpose of this report is to document the history, design, and testing to date of ultra high pressure technology, with special attention paid to the recently completed UHP P-19. The history of UHP technology will be discussed with regard to earlier platforms and how these concepts were scaled to a full size prototype. Afterwards, a design summary is presented discussing major components of the UHP P-19 and how these components contribute to both the totalized performance of the onboard UHP and combined agent firefighting technology. Quantitative flow characterization of both UHP and combined agent firefighting is then presented in order to derive performance specification requirements for the next generation ARFF vehicle. An UHP turret impact study is also presented to provide the information on personnel safety. Finally, a summary detailing current development work will be presented previewing ARFF vehicle platforms of the future.
1.3 Terminology
This report contains references to several different types of firefighting agents and technology which have been defined here for clarification. The following key descriptions, the majority of which are defined verbatim according to NFPA 412, will be consistently used throughout this report:
- Aqueous Film Forming Foam (AFFF) Concentrate – A concentrated aqueous solution of one or more hydrocarbon or fluorochemical surfactants that forms a foam capable of producing a vapor-suppressing aqueous film on the surface of hydrocarbon fuels (NFPA 412, Chapter 3).
- Foam – Firefighting foam is a stable aggregation of small bubbles of lower density than oil or water that exhibits tenacity for covering horizontal fires. Air foam is made by mixing air into a water solution, containing a foam concentrate, by means of suitably designed equipment. It flows fr
eely over a burning liquid surface and forms a tough, air-excluding, continuous blanket that seals volatile combustible vapors from access to air. It resists disruption from wind and draft over heat and flame attack and is capable of resealing in case of a mechanical rupture. Firefighting foam retains these properties for relatively long periods of time (NFPA 412, Chapter 3). - Foam Drainage Time (Quarter Life) – The time in minutes that it takes for 25 percent of the total liquid contained in the foam sample to drain from the foam (NFPA 412, Appendix A)
- Foam Expansion – The ratio between the volume of the foam produced and the volume of solution used in its production (NFPA 412, Chapter 3).
- Foam Pattern – The ground area over which foam is distributed during the discharge of a foam-making device (NFPA 412, Chapter 3).
- Heat Resistance – The property of a foam to withstand exposure to high heat fluxes without the loss of stability (NFPA 412, Chapter 3).
- Ultra High Pressure (UHP) – Water/AFFF applied at pressures between 900-1500 pounds per square inch (psi).
- Compressed Air Foam (CAF) – Water/AFFF foaming solution that has an expansion ratio 5:1 or greater using compressed air.
Chapter 2: Recent Advancements in Deployable Firefighting Technology
2.1 The Development of Ultra High Pressure Technology
In September of 2002, AFRL/MLQD began research on the use of UHP technology for extinguishing hydrocarbon fuel fires with respect to crash rescue events. Initial efforts were directed towards developing a single agent system that would address both two-dimensional (2-D) pool fuel fires traditionally fought with AFFF and three-dimensional (3-D) fires traditionally fought with Halon 1211. Figure 2.1.1 shows a mockup of an engine nacelle with a flowing fuel fire that might be experienced from a broken fuel or hydraulic fluid line. AFRL investigated UHP technology as a means to entrain liquefied gaseous agents in a water stream for extinguishment of 3-D fires. Keeping the gases under high pressure in the line would assure the gas would remain a liquid until it exited the nozzle. Initially, liquid carbon dioxide (CO2) was investigated as a Halon alternative because of its known fire extinguishing properties, low cost, and ozone-friendly properties. This liquid has a vapor pressure of 600 to 800 pounds per square inch (psi) at normal temperatures for firefighting application and becomes supercritical at approximately 85 degrees Fahrenheit (° F). To mix the water and CO2 in a liquid phase required raising the water pressure to greater than 800 psi. Early in 2000, Rosenbauer A.G. of Linz, a European fire equipment manufacturer from Austria, introduced an UHP system consisting of a skid mounted, 100 bar (≈ 1500 psi) pump and appropriate auxiliary systems to provide a foam-based firefighting capability. The UHP technology was successfully demonstrated for use on Class A structural and automotive fires; however, the effectiveness for Class B hydrocarbon fuel fires was never evaluated. AFRL/MLQD initiated contact with Rosenbauer US to obtain a system modified to use AFFF and liquid CO2. The system was delivered in the summer of 2002 and mated to a laboratory developed CO2 injection system (Figure 2.1.2).
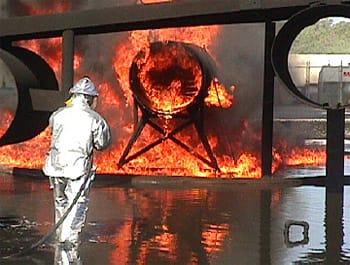
Figure 2.1.1: 3-D foam application to a 3-D flowing fuel fire.
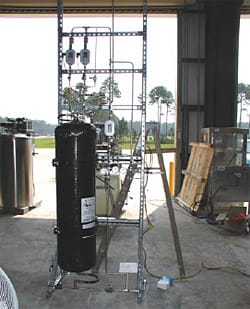
Figure 2.1.2: Liquid/supercritical CO2 injection system.
A series of initial experiments showed exceptional firefighting potential both with and without the addition of CO2. Figures 2.1.3 and 2.1.4 illustrate the level of performance. The 700 square foot (ft2) fire shown in Figure 2.1.3 was extinguished with a 22 second application of AFFF solution at a flow rate of 10 gallons per minute (gpm), or a total of about four gallons of solution. This result was startling because traditional application methods would require about 45 gallons of solution. The results demonstrated in Figure 2.1.4 were even more impressive because this fire typically cannot be extinguished with AFFF and usually requires the use of a gaseous agent, such as Halon, which only extinguishes the fire 75 percent (%) of the time (Dierdorf and Kiel). The UHP extinguished the fire in approximately 25 seconds and provided sufficient cooling after an additional 60 seconds of application to remove the potential of re-ignition.
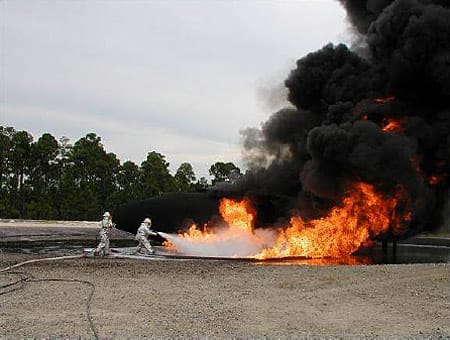
Figure 2.1.3: UHP mounted on the M-Gator extinguishing a 700 ft2 pool hydrocarbon fire.
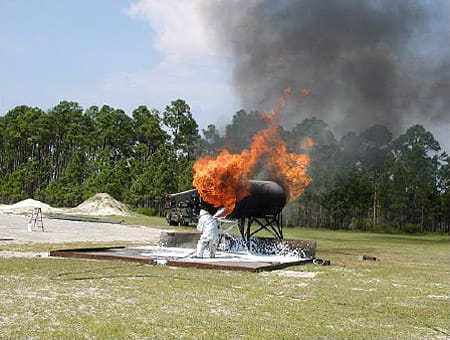
Figure 2.1.4: UHP attacking a 4 gpm continuously running fuel fire from an engine nacelle.
2.2 First Response Expeditionary (FRE) M-Gator Vehicle
The First Response Expeditionary (FRE) firefighting vehicle was the first UHP system developed by the AFRL/MLQD. The FRE consisted of a 22 horsepower (hp) Briggs and Stratton® engine with a 2 cylinder, 1500 psi plunger pump helping to produce a 14 gpm flow rate at the nozzle. The system accommodated 52 gallons of water and standard 5 gallon AFFF can. The unique nozzle design allows for either aspirated or non-aspirated foam in either a straight stream or fog pattern. Figure 2.2.1 shows the compact design of all the components located on a platform on the back of the John Deere Military Gator. Currently, the FRE is the only air droppable firefighting asset in the United States Air Force (USAF) inventory. The FRE was developed specifically at the request of a General for the Airborne Red Horse firefighters. The FRE proved that a 67% reduction in agent application was feasible without compromising extinguishment time.
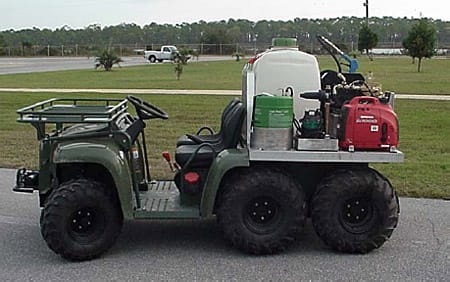
Figure 2.2.1: Side view of the 14 gpm FRE vehicle with optional equipment.
Figure 2.2.2 shows the general timeline outlining the milestones met during development and deployment of the FRE vehicle. In summary, the FRE was a fast-track research and development effort in which the design, prototype, air drop certification, and commercialization were completed in less than seven months.
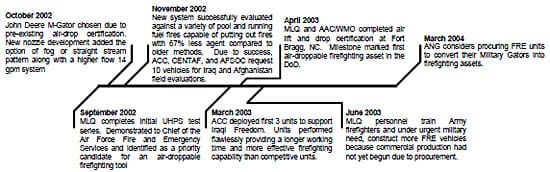
Figure 2.2.2: Timeline depicting landmark moments in the development and deployment of the FRE vehicle.
The FRE vehicle was evaluated on a variety of scenarios including pool fuel fires, running fuel fires, tent fires, and wild land forest fires (Table 2.2.1) indicating the versatility of UHP technology. Figures 2.2.3a and 2.2.3b show the FRE being used during wild land firefighting, including extinguishing brush fires and assisting with mop-up of deep seated fires. Currently, Rosenbauer has adapted the UHP skid technology for a variety of vehicle platforms including the Polaris, shown in Figure 2.2.4a, and military high-mobility multipurpose wheeled vehicles (HMMWV), as shown in Figure 2.2.4b.
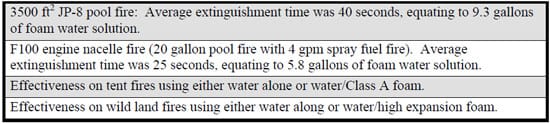
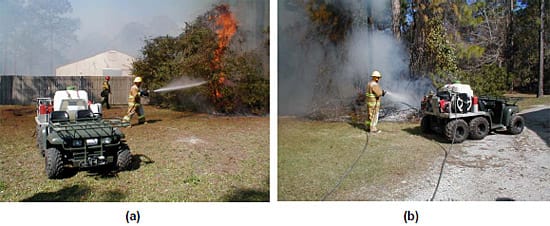
Figure 2.2.3: (a) The FRE providing rapid extinguishment of forest fires. (b) The FRE can also be used to reach deep-seated, smoldering fires shown here.
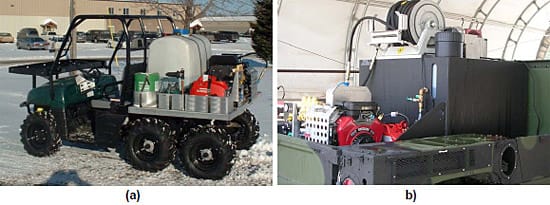
Figure 2.2.4: (a) A derivative of the UHP skid adapted for the Polaris. (b) The Rosenbauer UHPS fitted within the rear of a military HMMWV.
2.3 100 GPM UHP Skid
A 100 gpm, 1500 psi UHP skid system was designed and tested to demonstrate the scalability of the UHP technology. During this phase of research, nozzle and aspirator design were the primary focus. More than ten different nozzles with varying orifice diameters were designed and tested to determine the optimal geometry needed to maximize foam expansion ratios and throw distance. Figure 2.3.1a shows the 100 gpm UHP skid testing a new nozzle design while Figure 2.3.1b shows an image depicting velocity contours from a computational fluid dynamic (CFD) model designed using Fluent® (Fluent 6).
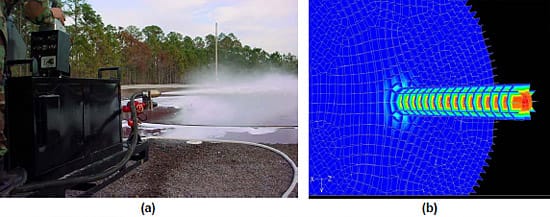
Figure 2.3.1: (a) The 100 gpm UHP skid delivering agent. (b) CFD velocity contours showing steep gradients within a UHP test nozzle using Fluent®.
Three different air aspirators were designed to increase the expansion ratio of the AFFF in order to enhance the foam blanket. The aspirators function by drawing air into the water foam solution through two diagonally aligned holes on the side of the nozzle, which mechanically mixes air with the agent just prior to discharge. Dr. David Summers, a professor of Mining Engineering at the University of Missouri-Rolla, was a key university consultant in providing excellent recommendations in designing the first generation experimental UHP nozzles. Figure 2.3.2 represents one of the first AFRL/MLQD designed UHP nozzles along with an accompanying aspirator. The nozzle walls were fabricated using an electrical discharge machining (EDM) finishing process to maximize laminar flow, which increased throw distance. The long gradual taper was a geometry that, through excessive design iteration, also helps to optimize stream reach for straightforward designs.
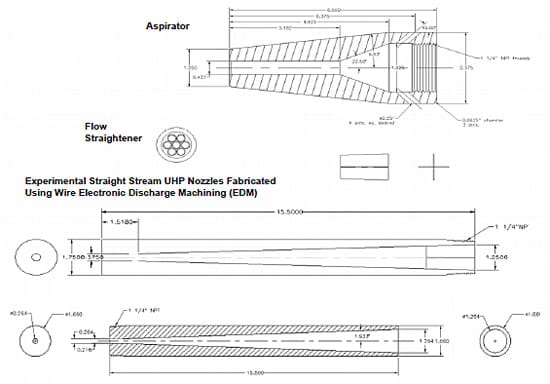
Figure 2.3.2: Schematic view of various AFRL/MLQD designed UHP nozzles with accompanying accessories.
The 100 gpm system was evaluated as part of the Fire Extinguishing Effectiveness Test (FEET) series to determine the gallons of water and foam required to extinguish a square foot of fire (McDonald et al.). FEET included over 400 fires using UHP, CAF, combined agent, and standard non-aspirated foam on water, gravel and soil surfaces common to airports. FEET results showed that UHP reduced agent application by more than 67%. Data collected from the FEET series was to support specification requirements for the next generation Air Force deployable ARFF vehicle.
2.4 200 GPM High Reach UHP Oshkosh T-1500
The next phase of UHP research involved scaling the technology to 200 gpm. The USAF was seeking a solution to extinguishing aircraft engine fires without the use of foam or dry chemical, leaving only water and gaseous agents as possible extinguishing media. The USAF request for clean agent firefighting for engine nacelles was in response to a cargo aircraft engine that caught fire at an air force base (AFB), causing extensive damage and the need for engine overhaul. In July of 2004, a 200 gpm UHP system was delivered to Tyndall AFB, FL. The system was designed by AFRL/MLQD and retrofitted onto an Oshkosh T-1500 capable of carrying 1500 gallons of water with high reach extendable turret (HRET) capability. Figures 2.4.1a and 2.4.1b show the range of spray patterns possible with the system, including fog and straight stream. Figure 2.4.2b also shows a side by side comparison of the agent streams from the 200 gpm UHP system and standard non-aspirated foam 500 gpm P-19 roof turret. Both vehicles were in the same position with each nozzle elevated at approximately 20° for maximum throw distance. Visual inspections showed no significant difference in the appearance or throw range of the UHP stream even though the flow was reduced by 60%.
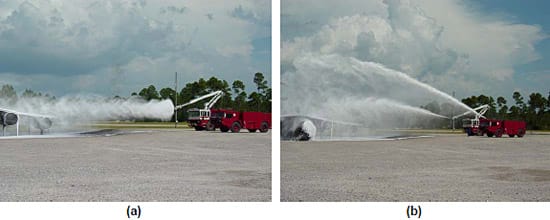
Figure 2.4.1: (a) The 200 gpm UHP Oshkosh T-1500 delivering agent. (b) Side by side comparison of agent streams (200 gpm UHP and standard 500 gpm P-19).
Figure 2.4.2 shows the HRET being used to extinguish a 7000 ft2 pool fire. The articulation of the HRET allows the vehicle to remain stationary while the operator focused on the fire without having to reposition the vehicle around the aircraft. This type of application increased efficiency and proved similar agent reductions demonstrated in the 100 gpm system.
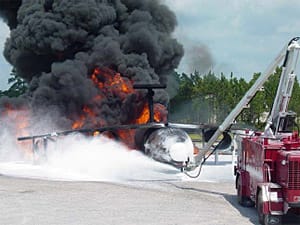
Figure 2.4.2: The 200 gpm UHP T-1500 Extinguishing a 7000 ft2 pool fire.
Chapter 3: UHP P-19 Design Summary
3.1 Standard P-19 Design Overview
The currently deployed P-19 employs two firefighting technologies: (1) standard non-aspirated foam and (2) dry chemical. The standard P-19’s primary firefighting agent delivery system is powered using a power take-off (PTO) shaft via a power divider driving a single-stage centrifugal pump capable of delivering 810 gpm of non-aspirated water or foam. The pump is capable of discharging agent at a flow rate of 500 gpm via a manually-operated roof turret with a range of approximately 200 feet, as well as from a pneumatically-assisted bumper turret at 250 gpm with a range of approximately 150 feet. The standard P-19 also comes with a 100 foot pistol grip-style hand line capable of delivering agent at 60 gpm located along the driver’s side of the truck. Dry chemical serves as a complimentary agent delivered at approximately 5 pounds per second (pps) via hand line from a 500 lb onboard reservoir tank positioned along the passenger’s side behind the cab. Non-aspirated foam is primarily used for large 2-D pool fires typical of large crash rescue events, whereas dry chemical is typically dispensed for suppressing localized 3-D fires such as burning engine nacelles. All nozzle exit pressures for the standard P-19 operate in a pressure regime between 200 and 350 psi, depending on what specific systems are active. The foam proportioning system is remotely located and manually set, with a water tank and foam tank capacity of 1000 and 130 gallons, respectively. A complete listing of standard P-19 specifications is provided in Appendix A (Crash Rescue Equipment Service, Inc). The standard P-19’s primary firefighting agent delivery system’s pumping diagram is provided in Appendix B. The standard P-19 technical manual, operation, and operator maintenance instructions can be found in the Air Force Technical Order 36A12-8-17-1 (Air Force).
3.2 UHP P-19 Design Overview</p >
Although UHP P-19 component installation was delegated to Crash Rescue Equipment Services, Inc., retrofit design was completed by the AFRL/MLQD. The prototype is a standard P-19 with the exception of the vehicle’s firefighting systems, which exhibit the latest in technology. To further the science, it is necessary that the vehicle be equipped with updated hardware control in order to optimize the performance of the UHP P-19. The demonstrator uses hydraulics to drive all of its firefighting systems, allowing precision speed control over each pump. Using digital instrumentation to relay agent pressure and flow rate at critical junctures throughout the entire system, open-loop feedback has proven critical during development in order to perfect agent delivery flow characteristics. This system is particularly versatile when testing different third party hardware such as nozzles and turrets, for example, which may require slight run modification from one another. Figure 3.2.1 depicts the retrofitted UHP P-19 ready for duty. All firefighting equipment including pumps, nozzles, agent tanks, plumbing hardware, and operational control are specific to the UHP P-19, unless otherwise specified.
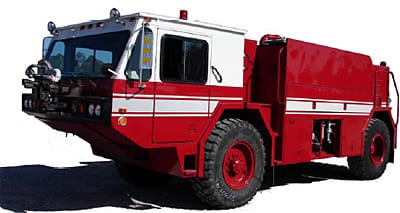
Figure 3.2.1: The retrofitted UHP P-19 ready for duty.
The demonstrator was re-designed to incorporate three different agent application technologies: (1) ultra high pressure system (UHP) (2) compressed air foam (CAF), and (3) dry chemical, with the option of combining CAF and dry chemical through a single nozzle. Figure 3.2.2 depicts the basic arrangement of main internal components. The major characteristics of the UHP P-19 involve a bumper turret capable of supporting both UHP and combined agent hand lines, along with separate UHP and combined agent hand lines located along the passenger’s side compartments. The roof turret has been removed because qualitative fire testing as well as quantitative flow characterization has shown that a 300 gpm UHP bumper turret has firefighting effectiveness equivalent to that of the standard 500 gallon roof turret. Also, practice has shown that UHP delivered near the base of 2-D hydrocarbon fuel fires has increased overall efficacy as opposed to being delivered at a higher elevation. Through operator feedback, it has also been shown more ergonomic for the firefighter because they can see both the agent stream as well as the target all from one vantage point. Simple combustion science supports the theory that the UHP stream breaks up the heated fuel vapor layer between the liquid fuel and the oxygen-rich air much more efficiently than standard methods, in large part by its shear penetrating force and displacement from the locally generated heat. Also, because the UHP jet moves so quickly downstream, droplet breakup occurs more rapidly than lower pressure methods due to increased turbulent intensity causing local oxygen content near the flame front to be dislocated by water mist, in essence suffocating the flame.
The UHP system is essentially the same technology as standard non-aspirated foam, with the energizing affects of a delivery pressure 4 times (approximately 1200 psi) the magnitude of the standard system at the bumper turret nozzle. Because of this increase in pressure, plumbing hardware as well as nozzle and turret design must be rated for high pressure (900 – 1500 psi). The UHP P-19 is intended for 300 gpm delivery of agent at approximately 1200 psi out of the UHP bumper nozzle, and 30 gpm at approximately 900 psi out of the UHP hand line nozzle from a 150 foot reel. With plunger pump exit pressures of approximately 1500 psi, frictional line loss over the entire system is the leading contributor to reduced nozzle exit pressures. Because testing has proven less overall agent is needed to fight the same scale fires in comparison to standard non-aspirated methods, AFFF concentration levels have been increased from the standard 3% to 6% for an increased factor of safety from burn back. It should be clarified here that 6% AFFF implies proportioning 3% AFFF concentrate at double the rate into the water to ultimately arrive at 6 parts 3% AFFF concentrate to 94 parts water. When stating 3% AFFF, it is assumed that 3% AFFF concentrate is being proportioned at 3 parts 3% AFFF concentrate and 97 parts water.
The CAF system uses the same extinguishing agent as the UHP system, except AFFF is proportioned in at 3%. Due to the injection of compressed air near the nozzle exit, foam expansion ratios normally twice the order of standard methods are created. By increasing the magnitude of the foam expansion through forced in-pipe aspiration, a significantly less amount of agent can be used to permanently extinguish a fire. The onboard CAF system is capable of 300 gpm delivery of foam at approximately 165 psi out of the bumper turret, and a hand line flowing 45 gpm at approximately 165 psi also. The dry chemical system is designed to flow approximately 7 pps from the bumper turret, and 5 pps from a hand line. Although the standard P-19 is equipped with a dry chemical hand line, The CAF and dry chemical system are capable of flowing concurrently through the use of a combined agent bumper turret nozzle and hand line through nozzles with concentric exit orifices to encourage CAF and dry chemical entrainment. Table 3.2.1 gives a brief comparison between the standard P-19 and UHP P-19, and Figure 3.2.2 depicts the basic arrangement of major components aboard the UHP P-19.
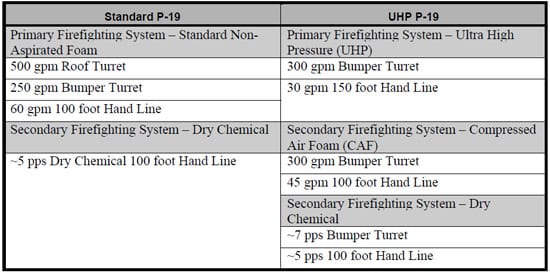
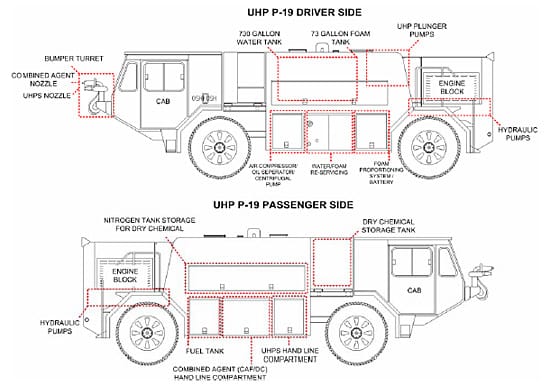
Figure 3.2.2: A UHP P-19 schematic depicting essential features.
3.3 UHP P-19 Ultra High Pressure System Design
UHP, the primary firefighting system, consists of an electrically-assisted bumper turret delivering water or foam solution at approximately 1200 psi via three 100 gpm reciprocating CAT plunger pumps running in parallel to supply a combined 300 gpm. Figure 3.3.1 depicts the system with currently attached Akron Brass prototype UHP nozzle and turret. The bumper turret is controlled electronically via joystick located on the center console of the cab, providing aspirating, variable stream nozzle control. An AFRL/MLQD designed turret attachment allows an auxiliary combined agent nozzle to be mounted using the same turret hardware and control.
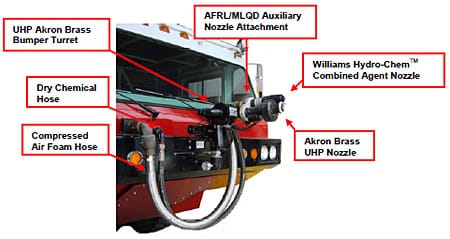
Figure 3.3.1: A typical UHP P-19 bumper turret configuration.
The plunger pumps are belt-driven by individual Linde piston rotary swash plate hydraulic motors which in turn are powered by the constant circulation of hydraulic fluid by Linde hydraulic pumps belt-driven off of the engine crank shaft pulley (Figures 3.3.2a and 3.3.2b for the photographs, and Figure 3.3.3 for the schematic). The plunger pumps in tandem with their respective hydraulic motors are located in a row along the top rear of the center compartment, while their associated hydraulic pumps are fastened to the truck frame on either side of the engine block (two coupled along with a charge pump on the passenger’s side and one on the driver’s side). An additional hydraulic pump is also employed to help drive the foam proportioning system on the driver’s side. See Figure 3.3.4a and 3.3.4b for the photographs and schematics, respectively. The charge pump is needed to supply cool, re-circulated hydraulic fluid to the system v
ia a 30 gallon hydraulic reservoir stationed in the rear area of the center compartment as the current fluid works, heats, and ultimately becomes displaced.
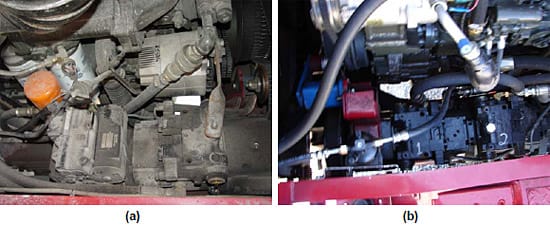
Figure 3.3.2: (a) Driver’s side hydraulic pumps and hoses. (b) Passenger’s side hydraulic pumps and hoses.
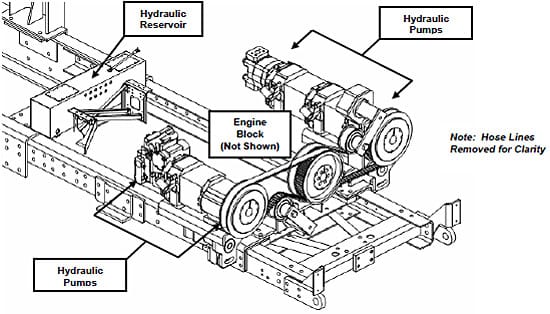
Figure 3.3.3: Hydraulic pumps and motors driven from the crank shaft pulley (Crash Rescue Equpiment Services, Inc.).
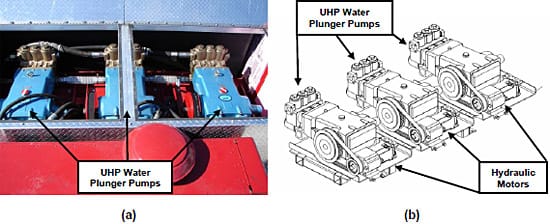
Figure 3.3.4: (a) Three 100 gpm UHP plunger pumps. (b) Schematic of 3 100 gpm UHP plunger pumps with their belt-driven hydraulic motors (Crash Rescue Equipment Services, Inc.).
While in UHP mode, the initial flow of water from a 730 gallon United Plastic Fabricating, Inc. polypropylene water tank (Figures 3.3.5a and 3.3.5b) is governed by a single-stage Waterous combination air compressor/centrifugal pump (Figures 3.3.6a and 3.3.6b) operating at approximately 300 gpm located below the center body compartment. The centrifugal pump and compressor is hydraulically driven by a hydraulic motor and pump in a manner similar to the plunger pumps, except the hydraulic pump is powered via a power take-off (PTO) drive shaft through a power divider. The PTO drive shaft and power divider employed on the UHP P-19 are original to the standard P-19, except for specific mating components needed to drive the centrifugal pump (Figure 3.3.7). An air compressor used primarily for CAF mode is mounted to the transmission of the centrifugal pump also, but will be discussed in more detail in Section 3.5 – CAF mode operation. Figure 3.3.8 depicts all internal components relative to the chassis.
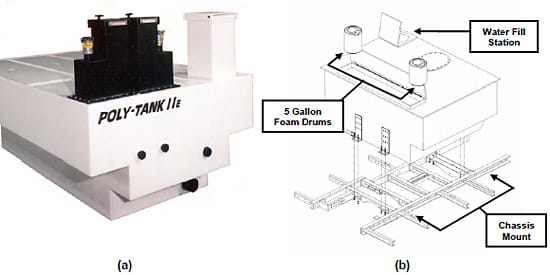
Figure 3.3.5: (a) The UHP P-19 combination 730 gallon water/73 gallon foam tank (United Plastic Fabricating, Inc). (b) The Water/foam tank schematic (Crash Rescue Equipment Services, Inc.).
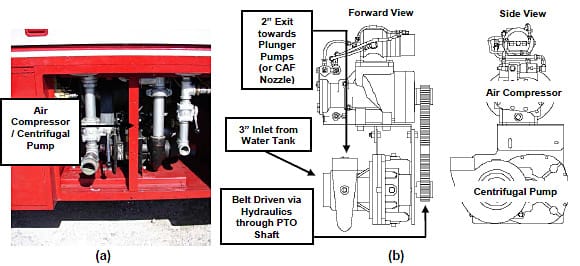
Figure 3.3.6: (a) Combination Centrifugal Pump/Air Compressor. (b) Combination Centrifugal Pump/Air Compressor schematic (Waterous Co.).
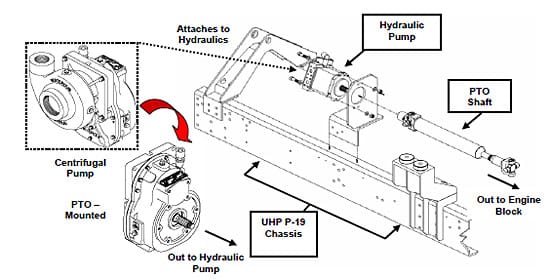
Figure 3.3.7: The UHP P-19 chassis with hydraulic components (Crash Rescue Equipment Service, Inc., Waterous Co.).
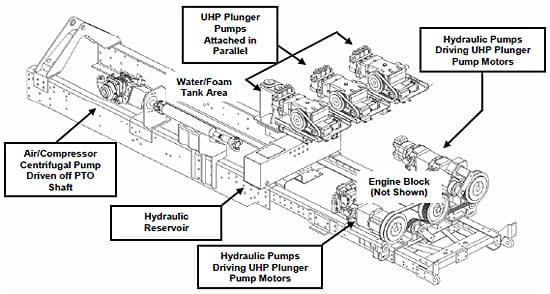
Figure 3.3.8: Schematic of rear UHP P-19 chassis with major internal firefighting components (Crash Rescue Equipment Service, Inc., Waterous Co.).
The centrifugal pump pressurizes the water to approximately 40 psi, which is within the required low inlet pressure regime for the plunger pumps to operate properly. Immediately before water enters the plunger pumps, an 80 mesh size high flow rate filter strains the water through openings equivalent to roughly 7/1000th of an inch (178 micron) (Figure 3.3.9). Water filtration is important when using plunger pumps because they are sensitive to excess particulate matter leading to premature eroding of the valves and seals, and ultimately pistons ceasing. When the main source of water is drafted from the ground, this became a serious issue. The centrifugal pump, on the other hand, does not have these issues due to its open channel impeller design capable of passing anything that can fit within its spiral shaped channels.
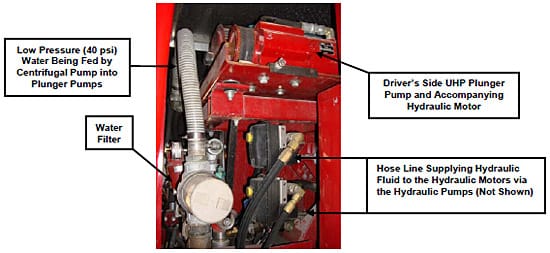
Figure 3.3.9: The UHP P-19 water filter inserted past the centrifugal pump to minimize particulate matter entering the high pressure plunger pumps.
The piping system has been situated in order to maximize accessibility, and all piping in contact with water or foam is made of stainless steel, bronze, brass, or flexible hose. Three inch diameter pipe was installed between the water tank and centrifugal pump, while 2 inch pipe was installed further downstream between the centrifugal pump and bumper turret plumbing (Figure 3.3.10). Piping was then reduced to a 1.5 inch diameter at the bumper where agent must navigate an exit path dependent upon manufacturer nozzle and turret design. Agent at approximately 1000 to 1200 psi ultimately discharges out of the nozzle where pressure and pattern characteristics are determined exclusively by nozzle exit geometry. Appendix C contains a UHP P-19 plumbing diagram showing the UHP system design along with the CAF flow logic.
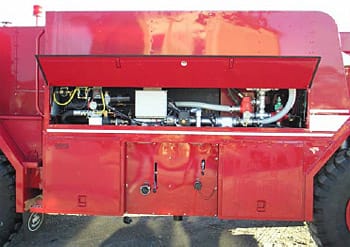
Figure 3.3.10: The UHP P-19’s driver’s side plumbing.
A 150 foot, 0.75 inch diameter UHP pistol grip-style hand line capable of delivering 30 gpm at approximately 1000 psi is located along the driver’s side of the truck in the compartment closest to the cab (See Figure 3.3.11). Nozzle pressure ranges, like that of the bumper turret nozzles, are dependent only on the nozzle geometry used due to various orifice exit area designs.
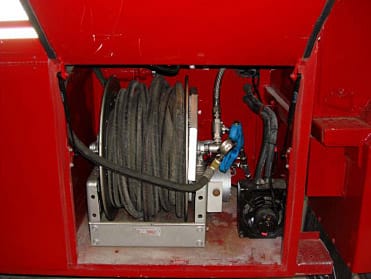
Figure 3.3.11: The UHP P-19’s UHP hand line reel.
3.4 UHP P-19 Foam Proportioning System Design
Foam induction is mechanically common for both UHP and CAF mode operation. A Foampro® foam proportioning system is used on the UHP P-19, which inducts foam from a 73 gallon foam tank packaged in a sub-compartment with the main water tank at a flow rate based upon the measured water flow rate just beyond the centrifugal pump (Figure 3.4.1). The proportioning system is installed on the driver’s side in the compartment closest to the engine block, and powered hydraulically in a similar manner to that of the UHP plunger pumps. In 300 gpm UHP mode, for example, the three plunger pumps supply approximately 282 gpm of high pressure water while the foam pump supplies 18 gpm to arrive at 300 gpm at 6% AFFF. In 300 gpm CAF mode, however, the centrifugal pump supplies approximately 291 gpm of low pressure water while the foam pump delivers 9 gpm to arrive at 300 gpm to arrive at 3% AFFF. The foam proportion can be user-defined through an in-cab digital interface for both UHP and CAF mode once the system is active, but returns
to the default values of 6% and 3% for UHP and CAF once the system is restarted.
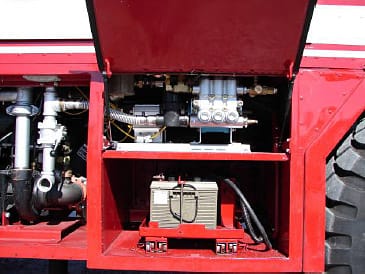
Figure 3.4.1: UHP P-19 Foam proportioning system (top) and battery (bottom).
3.5 UHP P-19 Compressed Air Foam System Design
The CAF system, one of the vehicle’s secondary firefighting systems, is driven exclusively by the centrifugal pump via its controlling hydraulic motor and pump assembly, except at a much higher speed compared to UHP mode to maintain approximately 300 gpm of agent flow at roughly 165 psi from pump to bumper turret nozzle exit. Foam is inducted downstream in the same fashion as in UHP mode, except this time only at 3% AFFF. Once foam has been proportioned into the water stream, the air compressor running in tandem with the centrifugal pump supplies dry, compressed air at a point near the exit point of the system at a pressure slightly higher than that of the foam solution in order to penetrate the stream. Because the air compressor and centrifugal pump are driven by the same belt, pump and compressor speed change proportionally with one another. Once the stream is penetrated, turbulent mixing causes millions of tiny air bubbles to expand inside the line. These tiny air bubbles, in turn, create a much heavier foam blanket (nearly double) to form compared to standard non-aspirated methods. CAF is ultimately delivered to a combination nozzle mounted on the UHP bumper turret from exit passages just above the left side of the bumper via 2 inch flexible hose. In its current configuration, CAF exits the system through the outer ring of a concentric combined agent nozzle manufactured by Williams Hydro-ChemTM with the ability to entrain CAF with dry chemical emanating from the center (Figure 3.5.1). Appendix C shows a complete UHP P-19 CAF system plumbing schematic.

Figure 3.5.1: A 300 gpm combined agent Williams Hydro-ChemTM nozzle mounted alongside the Elkhart Brass UHP bumper turret.
A 100 foot, 1.5 inch diameter combined agent hand-lever hand line capable of delivering 45 gpm at approximately 165 psi is located along the driver’s side of the truck in the center compartment just beyond the UHP hand line (Figure 3.5.1). The combined agent nozzle installed was also manufactured by Williams Hydro-ChemTM, and is identical in function to the bumper turret nozzle, just at a lower flow rate.
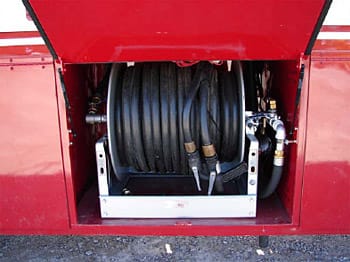
Figure 3.5.2: The UHP P-19 combined agent hand line reel.
3.6 UHP P-19 Dry Chemical System Design
The dry chemical delivery system was designed in a standard configuration. A tank residing behind the passenger’s side cab filled to capacity holds 500 lbs of dry chemical. For these evaluations, the dry chemical used was potassium bicarbonate, or PKP (Figure 3.6.1). When the system arms, a high pressure (approximately 2400 psi) nitrogen gas cylinder housed on the passenger’s side behind the cab (Figure 3.6.2) charges the dry chemical tank at approximately 185 psi through a regulator to fluidize the PKP. Dry nitrogen gas is used because it is chemically inert, non-flammable, and readily available. Once the system is charged, the agent can be delivered either independently, or in conjunction with CAF at approximately 7 pps through the bumper turret combined agent nozzle. As the dry chemical is expelled, the mass flow rate exiting the nozzle begins to decay non-linearly with respect to time due to the loss of dry chemical powder. Dry chemical flow rates start at approximately 5 pps through the combined agent hand line due to decreased nozzle exit areas.
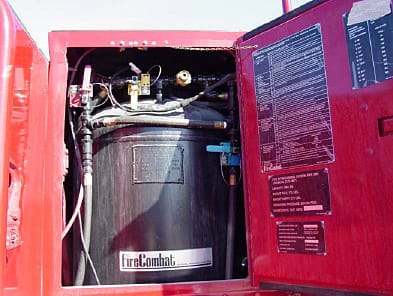
Figure 3.6.1: The 500 lb dry chemical storage tank located behind the passenger’s side cab.
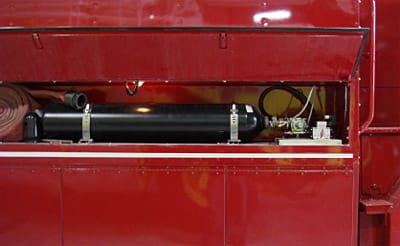
Figure 3.6.2: The high pressure nitrogen tank used to pressurize the dry chemical storage tank.
3.7 UHP P-19 Combined Agent System
The combined agent firefighting system consisted of operating the CAF and dry chemical system simultaneously. Either system can be operated independently or in tandem, depending on operational requirements. The Williams Hydro-chemTM dual agent nozzle offered the unique capability to entrain dry chemical within a ring of foam, which increased the throw distance of the dry chemical even in windy conditions. Figure 3.7.1 depicts the dry chemical and CAF flow pattern through a Williams Hydro-ChemTM combined agent nozzle.
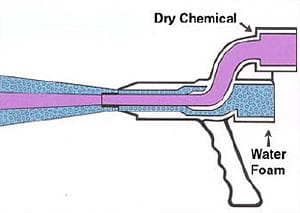
Figure 3.7.1: A schematic showing how the Williams Hydro-ChemTM combined agent hand line shrouds the dry chemical in a high energy, dense foam (Crash Rescue Equipment Service, Inc.).
3.8 UHP P-19 Cab Design and Operator Control
Several standard P-19 dashboard components were replaced with new components for the UHP P-19 for use for monitoring and operation. Component changes included the replacement of standard water and foam level gauges with digital readout displays, along with a single joystick capable of controlling all three firefighting agent delivery technologies via the bumper turret. A few specific features include a discharge time left readout relaying how much time is left dispensing the agent at its designed flow rate, along with UHP and CAF pressure indicators ensuring the system is operating at the correct pressure. Figures 3.8.1 and 3.8.2 show the general overview and layout of the modified UHP P-19 dashboard.
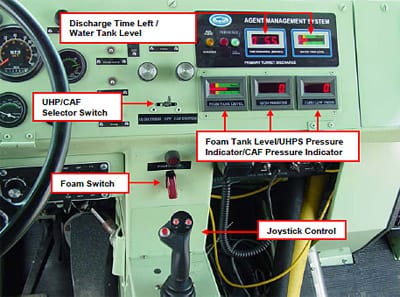
Figure 3.8.1: UHP P-19 operator cab control.
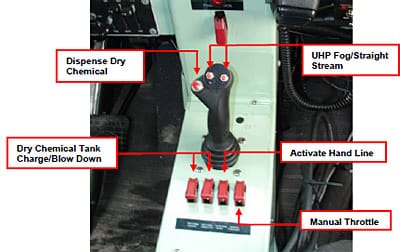
Figure 3.8.2: UHP P-19 joystick control along with auxiliary functions.
Design of the UHP P-19 firefighting system allows agent to be discharged, without interruption, while the truck is in motion in either direction, standing still, or maneuvering over rugged terrain. A brief summary of each agent delivery system’s operational procedure is given as follows:
Ultra High Pressure (UHP) Mode
- Engage the UHP system by moving the system selector switch to the High Press position.
- Place the foam toggle switch to the ON position. Note: If foam switch is not activated, only water will be discharged.
- For turret operation, press the joystick trigger momentarily to begin dispensing UHP agent, and rotate the joystick accordingly to direct the stream. When done dispensing agent, press the trigger again to shut the stream down. Press the fog or straight stream button to vary the stream pattern accordingly.
- For hand line operation, place the hand line toggle switch to the ON position. Note: One of the
three high pressure plunger pumps will engage and the centrifugal pump will engage in low speed mode, and the engine RPM’s will increase immediately. - For hand line operation, open hose reel ball valve (right side of hose reel) to the ON position. Last, open the hand line nozzle.
- When completed, turn the foam toggle switch to the OFF position, and expel water only out of all nozzles in order to prevent possible plumbing erosion due to residual foam.
- Close all nozzles, and close the UHP hose reel ball valve. Place hand line toggle switch to the OFF position and return the selector switch to the center position.
- Return foam switch to the OFF position.
Compressed Air Foam (CAF) Mode
- Engage the CAF system by moving the system selector switch to the CAF System position.
- Place the foam toggle switch to the ON position. Note: If foam switch is not activated, only water will be discharged.
- For turret operation, press the joystick trigger momentarily to begin dispensing CAF, and rotate the joystick accordingly to direct the stream. When done dispensing agent, press the trigger again to shut the stream down.
- For hand line operation, Place the hand line toggle switch to the ON position. Note: the centrifugal pumps will engage in high speed mode and the engine RPM’s will increase immediately. Turn the CAF hose reel ball valve (right side of combined agent hose reel) to the OPEN position. Last, open hand line nozzle.
- When completed, turn the foam toggle switch to the OFF position, and expel water only out of all nozzles used to prevent plumbing erosion due to residue foam.
- Close all nozzles, and close the CAF hose reel ball valve if opened. Place hand line toggle switch to OFF position, and return the selector switch to the center position.
- Return foam switch to the OFF position.
Dry Chemical Mode
- Turn UHP/CAF selector switch to either system other than the OFF position (Original designs intended for experimental dry chemical usage with both UHP and CAF operation).
- Initialize the dry chemical system by charging the dry chemical tank by switching the CHARGE DRY CHEMICAL switch to the ON position. Allow approximately 5 seconds for the tank to pressurize.
- For turret operation, press the dry chemical discharge button located on the outside left of the joystick control. Release when finished.
- For hand line operation, Place the hand line toggle switch to the ON position. Turn the dry chemical hose reel ball valve (left side of combined agent hose reel) to the OPEN position. Last, open nozzle.
- When completed, turn the BLOW DOWN DRY CHEMICAL switch to the ON position to remove corrosive dry chemical residue from the system. Allow approximately 5 to 10 seconds, and then turn the toggle OFF.
- Close all nozzles, and close the dry chemical hose reel ball valve if opened. Return the hand line toggle switch to the OFF position.
- Return UHP/CAF selector switch to the OFF position.
For combined agent firefighting, follow the operating procedures provided in both CAF and dry chemical mode.
Advanced control used in the developmental stages of defining agent flow characteristics is supported via a system developed by Parker known as IQAN. The system controls all hydraulic hardware onboard the UHP P-19, where personnel can monitor pump pressures from within the cab. The IQAN controller is not intended for user input along with every day use of the demonstrator, but only for testing and trouble shooting purposes. From this system, pressures at all intervals of the UHP and CAF mode operation can be monitored, as well as pump speeds increased or decreased with precision. Figure 3.8.2 shows the IQAN controller located to the right of the basic operator displays along with the Foampro® proportioning controller, which monitors agent flow and controls AFFF proportioning.
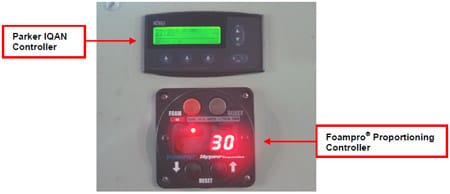
Figure 3.8.3: UHP P-19 IQAN control monitor along with the foam proportioning controller.
Air Force Technical Order 36A12-8-17-1 (Air Force) provides information on preventative maintenance, safety instruction and standard P-19 operational hardware not affected by the retrofit
Chapter 4: UHP P-19 Performance Evaluation
4.1 UHP P-19 Test Overview
The firefighting agent delivery systems aboard the UHP P-19 underwent several tests to quantify flow characterization in part using methods outlined in the NFPA 412 Standard for Evaluating Aircraft Rescue and Firefighting Operations (2003 Edition), military specification, or other standardized test procedure. From these testing standards, stream pattern and foam characteristics were recorded for a variety of nozzles associated with the major systems; namely, UHP, CAF, and combined agent for both the bumper turret and hand lines. Data with regard to UHP firefighting effectiveness and burn back resistance was compiled as well. Because UHP applies greater impact force compared to standard non-aspirated systems, jet impact pressure measurements from the UHP bumper turret nozzle were recorded to support personnel health and safety recommendations while working with this technology. Further information on UHP P-19 agent delivery test data not compiled here can be obtained from AFRL/MLQD.
4.2 UHP P-19 Test Objectives
The following objectives were defined to quantify UHP P-19 agent delivery flow characteristics. A minimum 5:1 expansion ratio goal for UHP and CAF mode was set to meet the foam quality requirements defined in NFPA 412 for air-aspirated AFFF (NFPA 412, Chapter 5). A minimum main turret throw distance of 190 feet was also set to meet minimum NFPA 414 requirements for an ARFF vehicle capable of holding between 528 and 1585 gallons of water. A 65 foot straight stream pattern hand line throw distance goal was derived likewise from the same set of requirements (NFPA 414, Chapter 4).
- Ultra High Pressure (UHP)
- 30 gpm UHP Hand line
- Foam Pattern Length
- Foam Pattern Width
- Foam Concentration (AFFF) for Minimum 5:1 Expansion Ratio
- 300 gpm UHP Bumper Turret
- Foam Pattern Length
- Foam Pattern Width
- Foam Concentration (AFFF) for Minimum 5:1 Expansion Ratio
- Foam Drainage Time
- Foam Burn back Resistance
- Pressure Impact at Various Standoff Distances
- 30 gpm UHP Hand line
- Combined Agent System
- 300 gpm Compressed Air Foam (CAF) Bumper Turret (Foam Only)
- Foam Pattern Length
- Foam Pattern Width
- Foam Concentration (AFFF) for Minimum 5:1 Expansion Ratio
- 300 gpm Combined Agent Bumper Turret (Foam + Dry Chemical)
- Foam Pattern Length
- Foam Pattern Width
- Foam Concentration (AFFF) for Minimum 5:1 Expansion Ratio
- 300 gpm Compressed Air Foam (CAF) Bumper Turret (Foam Only)
4.3 UHP P-19 Test Equipment
The following UHP P-19 test equipment was supplied either by the AFRL/MLQD or by private manufacturer. Where applicable, in the interest of competing technology, nozzle and turret nomenclature is denoted simply by position and the order in which testing occurred (e.g., UHP Bumper Turret Nozzle #1, etc). Because of this, the following equipment is in no particular test order. UHP turret nozzle impact materials were listed as well.
Major Firefighting Equipment
- Ultra High Pressure (UHP)
- 30 gpm UHP Hand line Nozzle
- Black Combination (Akron Brass)
- Stainless Steel Naturally Aspirated (AFRL/MLQD)
- 300 gpm UHP Bumper Turret Nozzle
- Stem-Centered (Elkhart Brass)
- Straight Bore (A
kron Brass)
- 30 gpm UHP Hand line Nozzle
- Combined Agent System
- 300 gpm Combined Agent Bumper Turret Nozzle
- Black Combined Agent (Williams-HydrochemTM)
- 300 gpm Combined Agent Bumper Turret Nozzle

Figure 4.3.1: UHP P-19 tested UHP hand line nozzles: (a) Akron Brass black combination fog/straight stream pistol-grip (b) AFRL/MLQD stainless steel naturally aspirated design.
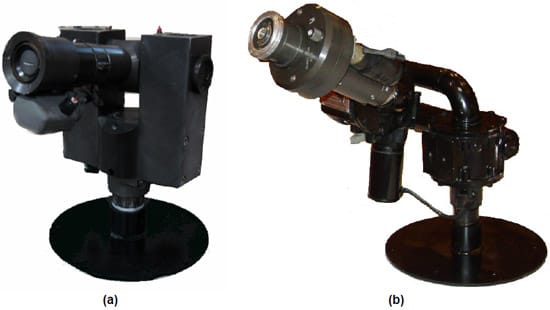
Figure 4.3.2: UHP P-19 tested 300 gpm UHP bumper turret nozzles: (a) Elkhart Brass stem-centered (b) Akron Brass straight bore.
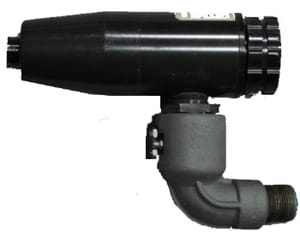
Figure 4.3.3: UHP P-19 tested 300 gpm combined agent Williams Hydro-ChemTM bumper turret nozzle.
Major Auxiliary Test Equipment
- Test Equipment as Required in NFPA 412
- Test Equipment as Required in MIL SPEC for Burn Back Resistance
- Sensor Products, Inc. Pressurex® Film with Various Pressure Reaction Ranges
4.4 UHP P-19 Flow Characterization Test Method
Tests were performed in accordance with NFPA 412 Test Method A (Chapter 6) with the UHP P-19 to quantify ultra high pressure foam pattern, expansion ration and drainage time. Minimum requirements for this test series were based on NFPA 412 test methodology, even though the application technology differed from traditional low pressure air-aspirated foam.
Foam Throw Pattern
The foam throw pattern was defined by dispensing agent for 30 seconds to provide a definitive foam blanket to obtain throw length and width. Foam less than 0.5 inches in depth was disregarded when measuring the longitudinal and lateral boundaries of the foam pattern using a 300 foot measuring tape reel. Testing was conducted with an average tail wind velocity of 3 to 5 mph measured using a hand held electronic wind meter. Optimum angles of 20° were found for both bumper and hand line orientations for maximum reach.
Foam Expansion Ratio
The UHP P-19 turret was directed at the foam collection backboard and discharged until both cylinders were filled. The outside of each cylinder was cleaned of any residual foam and then weighed. The weight of the cylinder with foam was subtracted from the weight of the cylinder empty, which calculated the weight of the foam. Because foam solution has nearly the same density as water, 1 gram of solution takes up approximately 1 milliliter of volume, making the quantity of volume and weight interchangeable when calculating the expansion ratio. The weight of the foam was then divided into the volume of the foam container, calculating the expansion ratio using Equation 4.4.1:

25% Foam Drainage Time
Drainage time was determined by measuring the amount of solution collected at the bottom of the cylinder at 30 second intervals until 25% of the volume (as recorded from the foam expansion measurement) had been exceeded. Drainage time was calculated only for 6% AFF foam. The 25% drain time was interpolated from the data, and calculated using Equation 4.4.2:

4.5 UHP P-19 Flow Characterization Test Results
The following results tabulated in Table 4.5.1 summarize the averaged data gathered over several repeated trials for each flow characterization test, with statistical outliers discarded. AFFF concentrations were tried at both 6% (6 parts 3% AFFF concentrate and 94 parts water) and 3% (3 parts 3% AFFF concentrate and 97 parts water) for certain configurations of interest. Foam pattern testing was conducted with an average tail wind velocity of 3 to 5 miles per hour (mph). As expected, expansion ratios increased with increased percentages of AFFF. For a fixed outlet area, nozzle pressures stay constant given a fixed flow rate. Although both the Elkhart Brass combination stem and straight bore Akron Brass UHP bumper turret nozzle are capable of varying their exit areas by manually adding or subtracting shims, neither prototype has the capability to vary pressure on-the-fly. Figures 4.5.1 and 4.5.2 show the Elkhart Brass UHP turret nozzle and Akron Brass UHP hand line nozzle, respectively undergoing throw evaluation, which compare well with goals defined in NFPA 412. Minimum 25% drainage time for both UHP turret nozzles exceed the NFPA regulation target for air-aspirated as well, taking an excess of 5 minutes longer to drain.
The UHP hand line results describe two different nozzle performances, one made by the AFRL/MLQD, and the other by Akron Brass. The pressure for UHP hand line Nozzle #2 was not measured at the nozzle, but a value of approximately 450 psi was calculated based upon pump pressure and known line loss. Here, all nozzles were tested at 6% because proportioning foam significantly below that percentage resulted in an expansion ratio much lower than the minimum standard of 5:1.
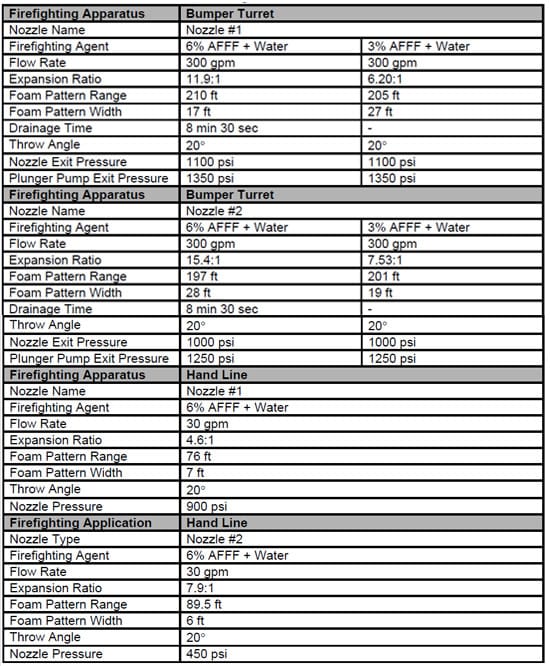
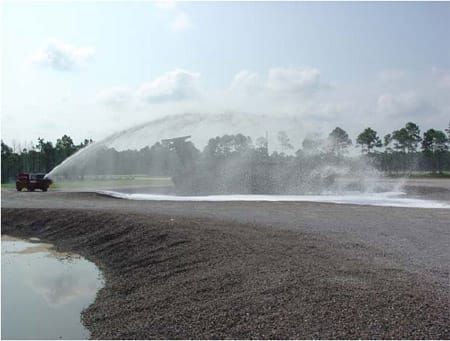
Figure 4.5.1: The Elkhart Brass UHP turret nozzle undergoing a throw test.
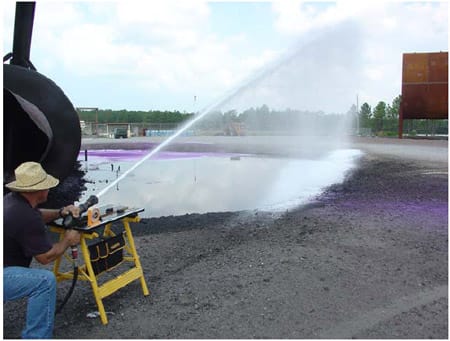
Figure 4.5.2: The Akron Brass UHP hand line undergoing a throw test.
The CAF and Hydro-ChemTM bumper turret nozzle flow characterization results using 3% AFFF at 150 psi are denoted below in Table 4.5.2. Although agent pressure after foam was injected reached approximately 165 psi, internal CAF pressures dropped by at least 15 psi in order for the injection air to penetrate the line further downstream. Due to substantial pressure loss with original smaller hosing attached at the nozzle, a temporary steel pipe was cut and swiveled for various attack angles. The nozzle was then attached and tested with the various pipes ultimately leading to an optimized throw angle with minimal performance loss. When dry chemical was injected, the ejected foam turned into a purple slurry that added more momentum to the spray stream, slightly increasing throw distance. Expansion ratio of foam and dry chemical combination cannot be measured due to the interference of the silicon used to fluidize the dry chemical, which inhibits foam expansion. This characteristic is common to all combined agent systems in use and procedures should dictate the application of a separate foam blanket to the extinguishment area following the application of combined agent to ensure burn back protection. Figure 4.5.3 depicts a throw test being conducted injecting compressed air foam and Figure 4.5.4 depicts both CAF and dry chemical from the combined agent turret nozzle.
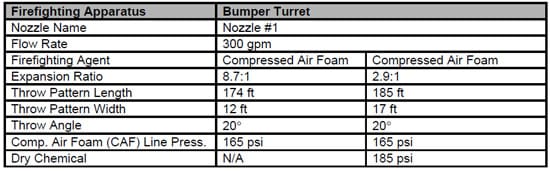
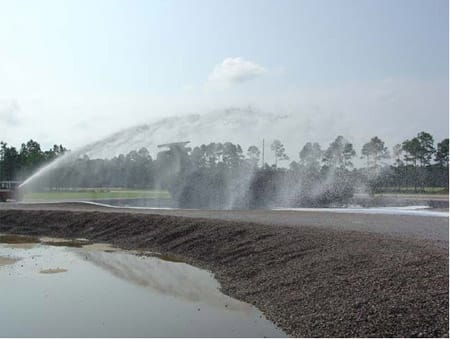
Figure 4.5.3: 300 gpm combined agent Williams Hydro-ChemTM bumper turret nozzle being used for a compressed air foam throw test.
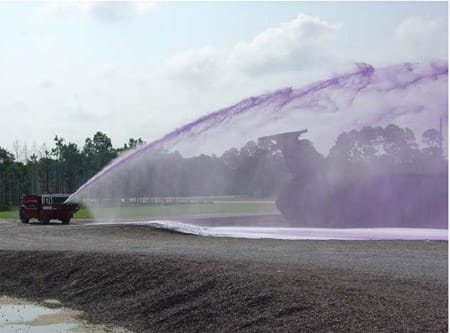
Figure 4.5.4: 300 gpm combined agent Williams Hydro-ChemTM bumper turret nozzle being used to conduct a combined agent throw test.
4.6 UHP P-19 Fire Extinguishing Effectiveness
The UHP P-19 has displayed great success in increasing fire extinguishing effectiveness using UHP technology compared to standard non-aspirated methods. Through repeated demonstration, the prototype has effectively fought large-scale hydrocarbon fuel fires using its UHP 300 gpm bumper turret nozzle with much greater efficiency than the standard P-19 500 gpm roof turret. Figure 4.6.1a and 4.6.1b shows the UHP P-19 extinguishing a full pit fire, shearing the flame front away from the fuel source. From numerous trials, data were derived to help define UHP extinguishing effectiveness as well as burn back resistance for both prototype turret nozzles.
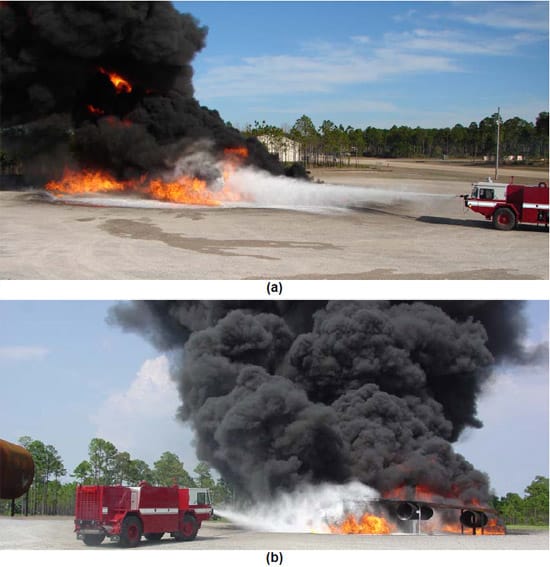
Figure 4.6.1: Different viewpoints of the UHP P-19 demonstrating UHP by extinguishing a 7000 ft2 fuel fire.
Pool fires ranging from 350 gallons of JP-8 jet fuel covering a 3500 ft2 (half pit), to approximately 500 gallons of jet fuel covering a 7000 ft2 area (full pit) have been extinguished as quickly as possible using the UHP P-19 300 gpm bumper turret. Extinguishment times took approximately 30 to 35 seconds at flow rates between 250 and 300 gpm, delivering water and foam proportioned in at 6% in the range of 150 to 175 gallons. Comparatively, the standard P-19 extinguished similarly sized fires in roughly 40 to 45 seconds at roof turret flow rates ranging from 500 and 675 gpm. From these exhibitions, an average firefighting effectiveness based upon volume of agent per unit area is estimated for both vehicles. From the observed results shown in Figure 4.6.2, the UHP P-19 demonstrates over a 300% increase in efficacy, while Figure 4.6.3 depicts a roughly 25% reduction in time until extinguishment. Figures 4.6.4 and 4.6.5 show the prototype fighting fire with both UHP nozzles, respectively, in preparing for burn back resistance evaluation.
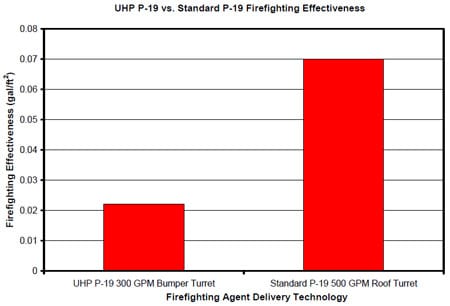
Figure 4.6.2: Estimated firefighting effectiveness comparison between the UHP P-19 300 gpm bumper turret and the Standard P-19 500 gpm roof turret.
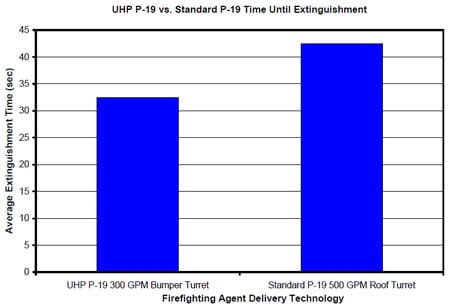
Figure 4.6.3: Estimated average extinguishment time comparison between the UHP P-19 300 gpm bumper turret and the Standard P-19 500 gpm roof turret.
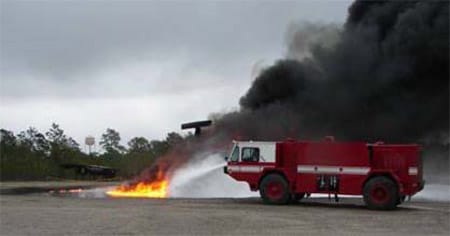
Figure 4.6.4: The UHP P-19 extinguishing a 3500 foot JP-8 fuel fire using UHP bumper turret nozzle #1.
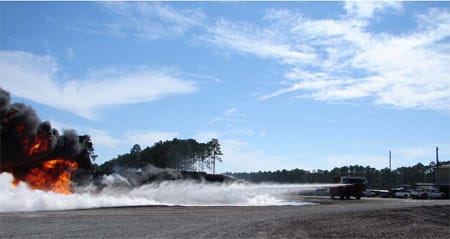
Figure 4.6.5: The UHP P-19 extinguishing a 3500 foot JP-8 fuel fire using UHP bumper turret nozzle #2.
Firefighting foam blankets must exhibit good burn back resistance to minimize the likelihood of reignition. To examine this attribute of agent delivered using the UHP bumper turret, burn back was tested with the UHP P-19 on fires containing 500 gallons of JP-8 jet fuel covering a 3500 ft2 area (Figure 4.6.6). Extinguishment took approximately 35 seconds at a flow rate of 300 gallons per minute, delivering 175 gallons of foam and water. Two 12 inch stovepipes were placed in the burn area and the foam inside the stovepipes was removed. At three (T3) and eight (T8) minutes after fire extinguishment, the residual fuel within the each stovepipe was ignited and allowed to burn for 60 seconds. Allowing the foam to partially drain provided the worst case scenario for burn back resistance. After the initial burn period, the stovepipes were removed and the fire was allowed to propagate to the remaining area. Burn back resistance was measured as the time after the initial 60 second burn, to self-extinguishment of the fire.
NFPA does not specify a minimum performance standard for burn back resistance so the criteria set by MIL SPEC F-24385F Fire Extinguishing Agent, Aqueous Film Forming Foam Concentrate, For Fresh and Sea Water was used (Naval Sea Systems Command). MIL SPEC burn back resistance for the 28 ft2 pan fire is 6 minutes. The fire was self-extinguished in both the T3 and T8 evaluations at 5:25 (minutes:seconds) and 3:36, respectively (Table 4.6.1). This result was important as the foam blanket resealed itself and completely extinguished the fire without the need for additional foam.
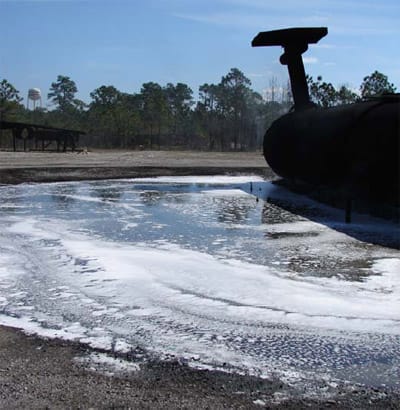
Figure 4.6.6: The foam blanket produced in preparation for burn back testing after extinguishment of a 3500 ft2 fire with the UHP P-19.

4.7 UHP P-19 Ultra High Pressure Jet Impact Test Method
Issues related to the safety were also addressed during this evaluation. With UHP nozzle exit pressures in excess of 1000 psi flowing at 300 gpm, injury to personnel within the agent stream was quantified. An extensive literature review was conducted by Summers and Viebrock on the impact of water jets on human flesh related to the inoculation of medical patients, industrial water jet cutting application and dental patients. Results using other fluids such as grease and oil were also highlighted and summarized. Their findings generally concluded that skin penetration pressures increase with increasing skin density, which was primarily driven by the subject’s age. For mature adults, average skin penetration pressure was approximately 25 MPa, or approximately 3,625 psi. Studies also cite that the majority of damage comes from particles within the fluid being injected and not from the increased fluid velocity created by the high pressure jet itself.
4.8 UHP P-19 Ultra High Pressure Jet Impact Results
By measuring jet impact pressures at incremental standoff distances from the nozzle exit, safety recommendations with regard to minimum distances personnel must maintain from the nozzle can be made. In order to make these measurements, UHP P-19 Nozzle #2 was arbitrarily selected, flowing agent at 1000 psi. It was assumed that impact forces would be greater using 100% water which is much denser than foam, helping to create a “worst case scenario” for human impact. To measure the impact pressure, Pressurex® pressure film
made by Sensor Products, Inc. was used. The film works such that once a certain magnitude of pressure is applied, a chemical reaction causes a microcapsule layer composed of a purple dye to burst at a particular intensity. The varying color intensity across the entire film correlates to a calculated pressure spectrum. Atmospheric conditions as well as impact duration are used to calibrate and post process the results. Figure 4.8.1 depicts an exposed pressure film sample along with a graphical explanation of how the process works.
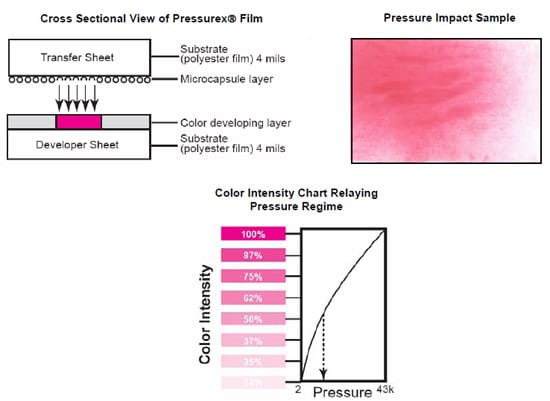
Figure 4.8.1: An exposed pressure film sample demonstrating the correlation between color dye intensity and quantitative pressure (Sensor Products, Inc.).
Pressure film was used to measure the turret nozzle impact pressure at distances of 5, 10, 15, 20, 30, 40 and 50 feet from the nozzle exit. The nozzle center was adjusted to be parallel with the center of the film, while keeping the film plane perpendicular to the jet core. Simplified analytical calculations showed that the 1000 psi jet exiting the nozzle exhibited a drop in pressure as the stream mixed with the atmosphere exponentially with respect to downstream distance. The preliminary sample test film stationed 5 and 10 feet from the nozzle with an average pressure impact range of 850 to 1000 psi verified these conclusions. Figure 4.8.2 shows the test set-up.
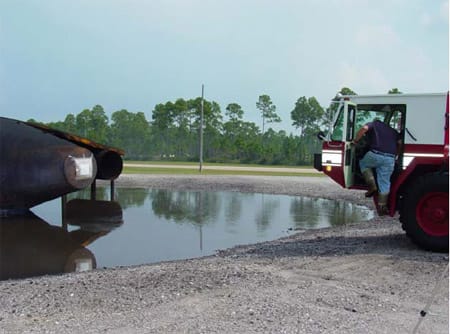
Figure 4.8.2: Preparation for a preliminary pressure impact measurement with a UHP bumper turret nozzle.
Because the pressure for the impact test ranges from approximately 15 psi (atmospheric pressure) to 1000 psi (nozzle exit pressure), two different types of pressure film were employed to cover the range: Super Low (70 – 350 psi) and Low (350 to 1,400 psi). Maximum impact pressures were calculated based upon data available from the film’s calibration curves in conjunction with the film’s pressure range and exposed intensities. Figure 4.8.3 depicts Low pressure film samples exposed (10 × 12 inches) from 5, 10, 15 and 20 feet away from the jet nozzle with a contour range of 0 to 1000 psi. Once the UHP jet reached a distance of approximately 25 feet from the nozzle exit, impact pressures decreased to the point where impact could only be detected on the Super Low Pressurex® film. Figure 4.8.4 depicts the Super Low film exposed samples with a pressure range of 0 to 350 psi.
To support the experimental Pressurex® film results, computational fluid dynamic (CFD) modeling of the multiphase UHP jet are presented as well. By imposing jet boundary conditions based upon the calculated exit velocity (387 feet per second) and exit area (0.249 square inches) of the real nozzle, a high speed turbulent water jet was modeled penetrating ambient air with 250 feet of physical domain using Fluent® CFD’s Volume of Fluid (VOF) model. For more information on Fluent’s® VOF model, the reader is referred to the Fluent® User’s Manual (Fluent® 6). Figure 4.8.5 depicts the total pressure versus standoff distance both experimentally, as well as computationally. As expected, total pressure decreases non-linearly within approximately the first 25 feet from the nozzle. As distances increased between the film and nozzle, the UHP jet impact pattern also became less definitive inferring jet break-up effects. Figure 4.8.6 reemphasized the jet core dissipation by depicting pressure magnitudes decreasing significantly both outward from the jet centerline as well as downstream of the nozzle. The physical shift in peak pressures from the horizontal jet centerline also became more pronounced at various standoff distances away as gravitational forces began to overtake longitudinal jet forces, ultimately causing the stream to collide with the ground at about 150 feet, which agreed qualitatively with experimental field testing of the actual UHP P-19. Figure 4.8.7 illustrates this concept with computational results reporting contours of velocity of the UHP jet stream, denoting the standoff distances relative to jet growth.
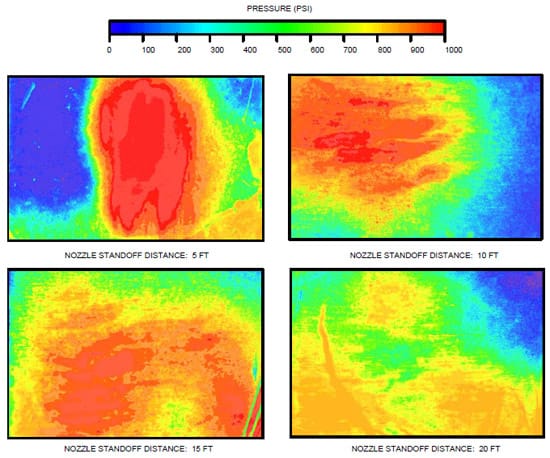
Figure 4.8.2: Preparation for a preliminary pressure impact measurement with a UHP bumper turret nozzle.
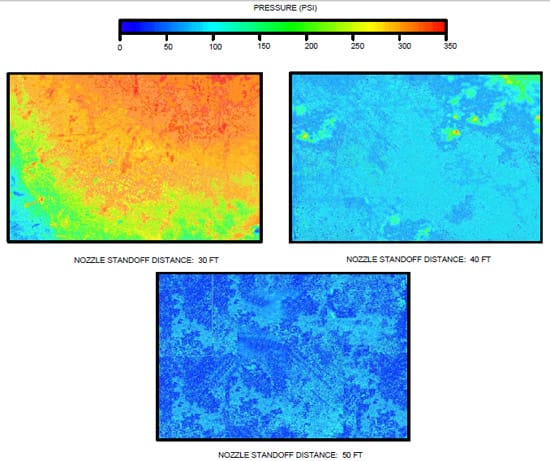
Figure 4.8.4: Exposed Super Low Pressurex® (0 – 350 psi) film contours of total impact pressure for 30, 40, and 50 foot standoff distances from the nozzle.
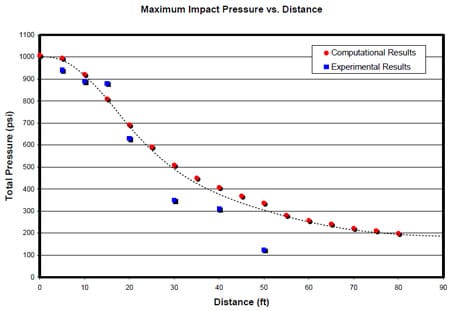
Figure 4.8.5: Total impact pressure vs. standoff distance comparison between experimental Pressurex® film and computational fluid dynamic results via Fluent®.
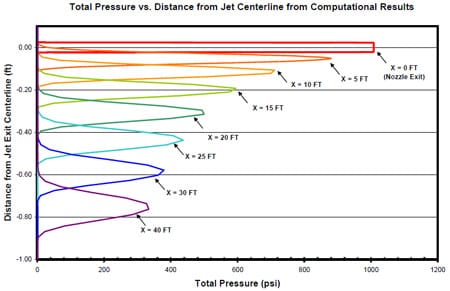
Figure 4.8.6: Computational results reporting the distance from jet exit centerline vs. total pressure comparison for each standoff distance from the nozzle.
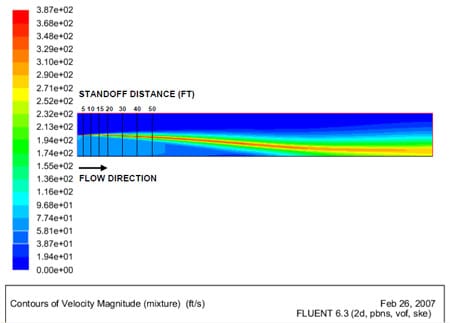
Figure 4.8.7: Computational results depicting contours of velocity magnitude for the UHP jet expanding over 250 feet of physical space.
4.9 UHP P-19 Test Conclusions
The UHP P-19 was designed and built to demonstrate the capability of the UHP, CAF, and combined agent firefighting systems in a deployable fire truck. Tests showed that these systems can be scaled to provide ARFF protection while reducing agent application quantities. The agent streams were evaluated for throw, pattern, expansion ratio, and impact pressure while operating in the UHP mode, the CAF mode, and the combined agent mode. Jet impact pressures were also measured while operating in UHP mode. Evaluations were conducted on the turret and UHP hand line. These evaluations showed that the UHP, CAF, and combined agent modes provided excellent performance for crash rescue firefighting.
Most major components used in this installation were from commercial products that are used in firefighting or other industries that use high pressure water. The notable exceptions are the nozzles, turrets, and the foam proportioning system. Nozzles and turrets were specially built by two manufacturers in the firefighting industry that normally make these components for lower pressure applications. All other components, such as pumps, valves, pipes and fittings, hoses, hose reels, hydraulic systems, control systems, gauges, the dry chemical system, and the CAF system were obtained from commercial products that did not require any special adaptations.
Nozzles, turrets, and the foam proportioning system were the only components needing special design consideration to contain high pressure. In addition to using stronger components, nozzle design had to consider the fluid dynamics of the discha
rged stream and the effect of the higher pressure and resultant higher discharge velocity. Several nozzle designs were evaluated in the development process to date, but this effort should continue to obtain greater improvement in throw distance and foam quality.
Flow tests conducted with the bumper turret showed acceptable performance for throw pattern and expansion ratio. The tests were conducted with nozzles and turrets from both suppliers, and at 3% and 6% foam concentration. All experiments exceeded the established minimum value of 5:1 and throw distances significantly exceeded the standard P-19’s value of 150 feet. Long throw distance was a particularly desirable result, significantly reducing the amount of maneuvering of the fire truck and significantly reducing extinguishment times. Foam Drainage tests also met minimum requirements, which was expected with excellent observed foam quality.
Two UHP 30 GPM hand line nozzles were evaluated. Both nozzles had good reach and one nozzle had desirable expansion ratio. Operation using the CAF system was evaluated using the Williams Hydro-ChemTM nozzle with and without the dry chemical system operating. The throw distance achieved for both configurations exceeded the established value, with greater throw distance achieved with the dry chemical. This was probably due to the additional energy supplied by the expanding compressed gas used in the dry chemical system. Hand line tests were not conducted on the dry chemical system.
Fire extinguishment effectiveness using The UHP bumper turret repeatedly demonstrated fire extinguishment effectiveness over three times greater than the standard P-19 roof turret. Fires were put out on average in one quarter less time with less than a third of the normal agent. The dispensed agent also provided excellent burn back resistance, easily exceeding MIL SPEC requirements.
Discharge total dynamic pressure was evaluated using pressure sensitive film to determine the effect of inadvertently hitting a firefighter with the high pressure stream. The test results showed an exponential decay in total pressure as a function of distance from the nozzle. Discharge total pressure significantly exceeded values observed from a conventional firefighting nozzle. This total pressure rapidly diminished as the distance from the nozzle increased. This effect was verified using simplified analytical methods as well as computational fluid dynamic models taking into account turbulent effects. Based on physiological testing on cadavers, the UHP jets will not penetrate unprotected skin even at the nozzle. UHP technology poses no greater threat to injury when compared to standard agent delivery systems when proper personal protective equipment and standard ARFF operational procedures are followed. Soft tissue, such as the eyes, should always be protected on any personnel working around low or high pressure water streams.
Discharge total dynamic pressure was evaluated using pressure sensitive film to determine the effect of inadvertently hitting a firefighter with the high pressure stream. The test results showed an exponential decay in total pressure as a function of distance from the nozzle. Discharge total pressure significantly exceeded values observed from a conventional firefighting nozzle. This total pressure rapidly diminished as the distance from the nozzle increased. This effect was verified using simplified analytical methods as well as computational fluid dynamic models taking into account turbulent effects. Based on physiological testing on cadavers, the UHP jets will not penetrate unprotected skin even at the nozzle. UHP technology poses no greater threat to injury when compared to standard agent delivery systems when proper personal protective equipment and standard ARFF operational procedures are followed. Soft tissue, such as the eyes, should always be protected on any personnel working around low or high pressure water streams.
In summary, these tests have shown that UHP and CAF systems, with and without dry chemical, provide significantly improved firefighting capability when compared with conventional non-air aspirated foam systems. Exceptional performance was achieved in throw distance and foam quality in almost all areas investigated.
4.10 Recommendations
Although the UHP and CAF systems have shown exceptional firefighting characteristics, several areas could benefit from further development and testing. These areas include continued nozzle development, evaluation of lower pressure UHP operation, evaluation of lower foam concentration, improved turret design, and use of high pressure centrifugal pumps.
Expansion ratio and throw distance are primarily controlled by the nozzle design. Considerable effort has been expended on nozzle design during the UHP development effort, however significant additional improvements may be possible. Smaller scale efforts have provided results that indicate significant improvements in throw distance might be obtained when applied to the larger scale. Since the primary turret UHP nozzle was the focus of design efforts, the UHP hand line nozzle still has room for improvement.
To date, experiments have focused on pressures between 1100 and 1500 psi, while normal firefighting uses pressures of 125 to 250 psi. Somewhere between these ranges, the effect of UHP becomes significant, and improved firefighting is achieved. The power required for the water pumps is directly proportional to the pump discharge pressure. Continued investigations into operating at intermediate pressures could result in reduced power requirements, reducing the size and weight of the firefighting vehicle while still maintaining UHP performance.
The foam concentration used with UHP has been held at 6%, or double the normal foam concentration. Adequate expansion ratios were obtained with 3% foam concentrations. Additional experiments should be conducted to evaluate expansion ratio, throw distance and burn back protection while using lower foam concentration. This may reduce logistics support requirements and improve environmental concerns about foam discharge while maintaining sufficient firefighting capability.
Studies into reduced pressure and reduced foam concentration should include additional fire testing to evaluate the effect of these changes on extinguishment time and application rate. These parameters are the best evaluators of firefighting effectiveness.
The current nozzle and turret configurations tested always featured the UHP nozzle normally installed on the turret, with the Williams Hydro-ChemTM nozzle installed in an offset auxiliary location. This causes increased load on the control motors while moving in one direction, and decreasing motor load while moving in the other. As a result, the controls were biased when operating in the CAF mode. Some method for balancing the load on the control motors should be developed.
All of the UHP work to date has used plunger pumps rather than centrifugal pumps that are normally found on firefighting equipment. There is no appropriate centrifugal pump currently available that meets the pressure and flow requirements of this system. There also isn’t a commercial plunger pump that meets the flow requirement, but this was satisfied using three pumps in parallel. Centrifugal pumps offer the desirable benefit of being able to pass contaminates that normally cause damage to the seals, pistons, and bores of the plunger pumps. They typically have lower efficiency. A single centrifugal pump that meets the pressure and flow requirements would provide a smaller, lighter pumping system that could drive off a single shaft in the power divider. Development of a UHP centrifugal pump should occur.
These recommendations provide the areas of future work needed to continue the advancement of the UHP firefighting system.
Chapter 5: UHP P-19 ARFF Trainee Field Evaluation
5.1 UHP P-19 Field Evaluation Purpose
As AFRL/MLQD UHP P-19 p
reliminary testing came to a close, real world feedback from the military firefighting community was requested in order to evaluate the demonstrator ranging from ergonomic design to overall firefighting capability. At first, consideration was made to deliver the demonstrator to fire departments at various Air Force bases to be individually tested and reviewed. However, this would become a very timely and costly endeavor. Since ARFF training for deployed firefighters and AFRL/MLQD share the same fire pit facilities at Tyndall AFB, it was arranged for ARFF trainees from Detachment 1, 823rd Red Horse Squadron would integrate the UHP P-19 into their normal training exercises. From these exercises, firefighting personnel from various bases gained experience using UHP technology that they may call upon in the field. The trainee evaluation also provided critical knowledge AFRL/MLQD can apply towards ARFF vehicle designs of the future.
5.2 UHP P-19 Field Evaluation Plan
The typical training program operates 42 weeks a year and is designed to provide military and civilian firefighters with the education, tactics, and operating procedures needed to accomplish a successful firefighting system. Class sizes range from 17 to 24 students with three trainees in each crew. In July of 2006, teams of ARFF trainees equipped in full gear participated in life fire demonstrations with the UHP P-19 for approximately four weeks. These exercises were expertly developed and delivered by experienced personnel, including Fire Cadre instructors, engineers, civilians, and contractors. Each team had the opportunity to learn basic firefighting techniques, maneuver control devices such as the bumper turret system, operate hose lines, observe the efficiency of water and foam, and much more. To determine the efficiencies and capabilities of UHP technology, performance surveys are provided to students to obtain data of fire extinguishment capabilities, as well as their overall experience. Appendix D depicts a sample performance survey filled out by the trainees.
5.3 UHP P-19 Field Evaluation Results
Four teams consisting of five firefighters evaluated the UHP technology aboard the UHP P-19 using a 1 to 5 rating scale, with 1 being poor and 5 being outstanding. Table 5.3.1 depicts the averaged results.
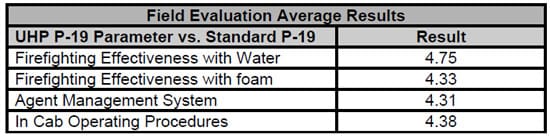
5.4 UHP P-19 Field Evaluation Conclusions and Recommendations
The cooperative effort between the AFRL/MLQD and the Red Horse Squadron ARFF trainees was an overall success. In general, student and instructor comments were extremely favorable in comparison with the standard P-19, with only minor recommendations with regard to ergonomic design such as joystick location. The following quotations were recorded from instructors and students after operating the UHP P-19:
A staff sergeant from Luke AFB who benefited tremendously from the training … “This is my first time working with this particular vehicle, and I felt it was very user friendly … distance is phenomenal … it engages [the fire] to distances where height is very important in order to reach the top of an aircraft. It is a definite need to today’s technology regarding aircraft and its personnel.”
A Senior Airmen from Eglin AFB, Florida was very impressed with the technology and effectiveness of the truck … “I felt it drove smoother and was easy to operate. I was impressed with various details, such as the conservation of the agent, the quickness of foam putting fires out quicker. I would drive this truck anytime.”
A staff sergeant from Offutt AFB, Nebraska had nothing but positive comments … “It’s great to be learning new technology because it opens the doors for fire protection. I felt it was a very smooth vehicle that creates a faster rescue path for personnel inside an aircraft. It’s user friendly, quicker, and easier to learn. You don’t have to spend too much time in the heat.”
A fire cadre instructor commented that “distance is much better because you don’t need to be parked next to the aircraft when putting a fire out. With the UHP P-19 you’re running time is good versus the [standard] P-19.”
References
Air Force Technical Order 36A12-8-17-1. “Aircraft Crash and Structural Firefighting Truck: Operation and Operator Maintenance Instructions.” USAF Type A/S32P-19 Technical Manual: 11 January 1988.
Crash Rescue Equipment Service, Inc. “Dry Chemical Agent – Williams’ “PKW” Dry Chemical.” www.crashrescue.com. Product Article: 26 February 2007.
Crash Rescue Equipment Service, Inc. “Typical Specifications – Oshkosh P-19.” Product Summary: 13 January 2007. www.crashrescue.com.
Crash Rescue Equipment Service, Inc. “Ultra High Pressure P-19 Technical Drawings.” October 2006.
Dierdorf, Douglas S. and Kiel, Jennifer C. “Halon Flight line Extinguisher Evaluation Data Supporting Standard Development.” Defense Technical Information Center. Final Technical Report: October 2005.
Fluent, Inc. “Fluent 6 User’s Manual.” 8 January 2007. https://www.fluentusers.com.
McDonald, Michael J. et al. “Fire Extinguishing Effectiveness Tests.” Defense Technical Information Center. AFRL-ML-TY-TR-2004-4554. Final Technical Report: October 2005.
Naval Sea Systems Command. Military Specification: “Fire Extinguishment Agent, Aqeous Film-Forming Foam (AFFF) Liquid Concentrate, for Fresh and Sea Water.” MIL-F-24385F: 7 January 1992.
NFPA 412: “Standard for Evaluating Aircraft Rescue and Firefighting Foam Equipment.” National Fire Protection Association (NFPA). 2003 Edition.
NFPA 414: “Standard for Aircraft Rescue and Firefighting Vehicles.” National Fire Protection Association (NFPA). 2007 Edition
Sensor Products, Inc. “Pressurex® Pre-Scale Pressure Indicating Film.” Product Article: 26 February 2007. www.sensorprod.com.
Summers, D.A. and Viebrock, J. “The Impact of Waterjets on Human Flesh.” 9th International Symposium on Jet Cutting Technology. paper H42. Sendai, Japan: 4-6 October 1988.
United Plastic Fabricating, Inc. “ARFF Tank Product Literature.” Product Specification: February 2007. www.unitedplastic.com.
Waterous Company. “CAF CP-2 Series Fire Pump Specifications.” Form No. F-1102. Product Specification: 21 February 2007. www.waterousco.com.
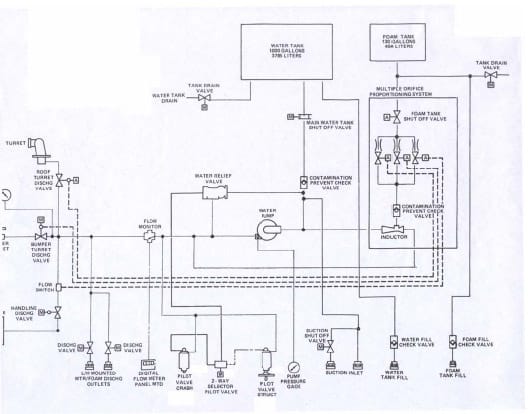
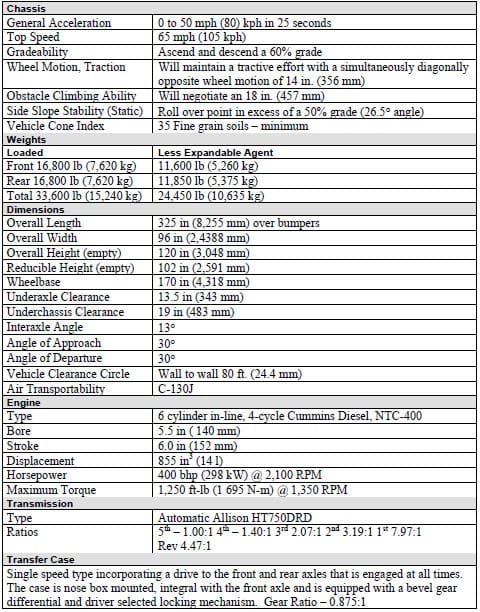
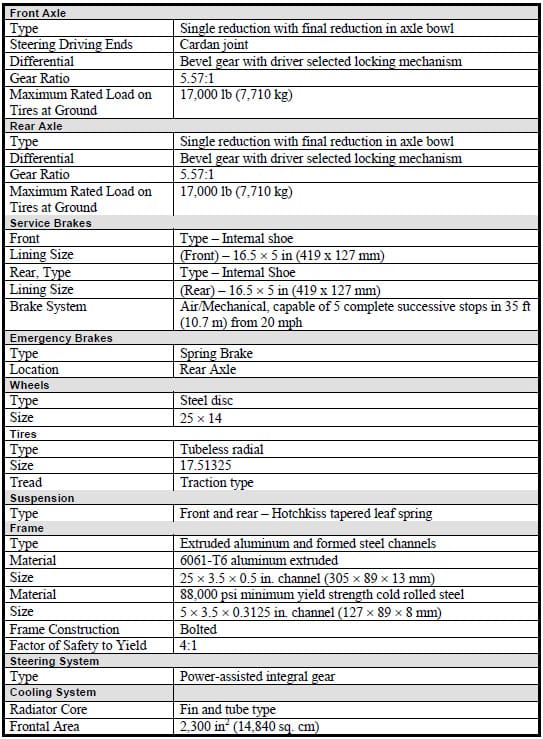
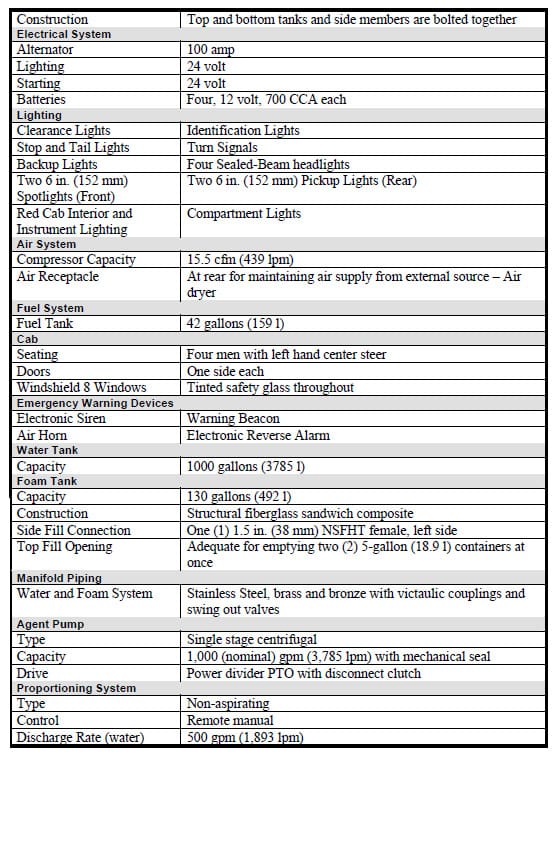
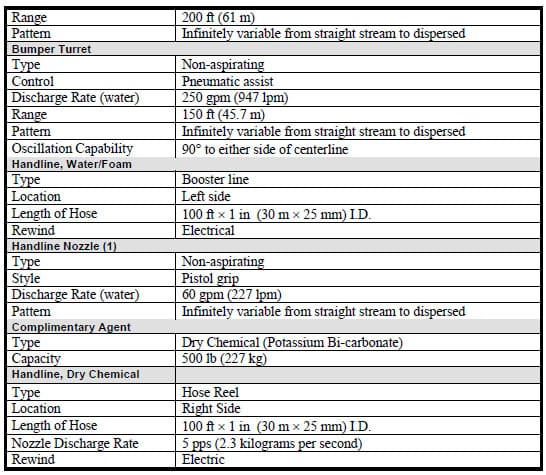
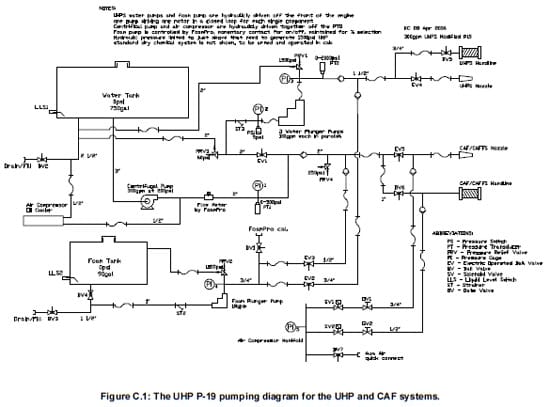
Appendix C: UHP P-19 Pumping Diagram for the Ultra High Pressure and Compressed Air Foam systems
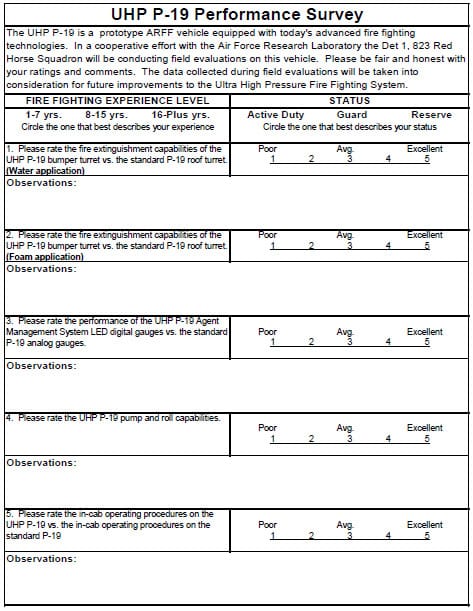
Appendix D: UHP P-19 ARFF Trainee Performance Survey