A. R. Abu Bakar and Huajiang Ouyang – Department of Engineering, University of Liverpool
Jennifer E. Siegel – Sensor Products LLC
ABSTRACT
Fugitive nature of disc brake squeal makes the problem even more difficult to tackle. The root cause of this nature is stili under investigation. There has been little quantitative research into this fugitive behaviour.
This paper stud’ies the effect of brake pad surface topographies on the fugitive nature of squeal. A finite element model of a disc brake is developed and validated through modal analysis and contact analysis. The complex eigenvalue analysis available in a commercial software package is pertormed. A comparison in squeal generation is made for different pad surface topographies.
The paper also simulates several structural modifications for squeal prevention. A plausible modification that results in reduced positive real parts of the eigenvalues is proposed. In the end, a root cause of fugitive nature of brake squeal is suggested.
INTRODUCTION
Since comfort issues become more prominent in the vehicle market competition, car manufacturers face challenging tasks to provide a better vehicle that satisfy customers’ requirements, Very often customers made a complaint that they were experienc’lng an annoying ‘squeal’ noise generated f-om a brake system. As a result, almost one billion dollar a year has been spent to warranty claims of which noise, vibration and harshness (NVH) issues are the cause [1].
Investigations into brakes squeal noise have been carried out over decades. The methods vary from purely theoretical or numerical to the experimental and quite sometimes combination of the two methods. In the brake research community, squeal noise is considered to be friction-induced vibration that generally occurs at frequency above 1 kHz [2] and at sound pressure level above 78 dB (A) [3]. Desp te being studied for a quite long time, comprehensive solutions to the squeal issue seem still far away to achieve. Furthermore, fugitive nature of squeal makes the problem even more difficult to tackle, Quite often squeal generated In one instance might disappear in another instance even though the same brake assembly is tested on apparently the same operating conditions.
The fugitive nature of brakes squeal issue has been raised in [4-8]. However, the reasons for this behaviour were not given. To date, there has been little quantitative research into this fugitive behaviour. Experimental observation made by Fosberry and Holubecki [9-10] revealed that all linings, which gave squeal. were glazed. Recent experimental invest gations by Sherif [11 J, Chen et al [12J and Eriksson et al [13J showed that surrace topography of sliding surfaces has a significant Influence on the generation and elimination of squeal.
Sherif [11] suggested that the ratio of the standard deviation of the height distribution of asperities to the mean radius of asperities of the d’lsc/pad interrace could describe triggering or ‘Janishing of squeal. He commented that if the ratio is above 1.0 squeal could not be established regardless of sliding speed and the applied load whilst if the ratio is lower than 0.1 squeal could be triggered, Earlier, Chen et al [12J suggested four conditions that distinguished whether squeal could occur or not. They repartee that the four conditions are found to be in correlation with the topography characteristics of the wear scars of the flat and ball specimens. In addition squeal tends to occur in the rough sliding surfaceS. Eriksson et al [13J studied the connection between brake pad surface topography and the occurrence of squeals. They tested two sets of brake padS, which have different material compositions They observed that generation of squeal depends on the size of brake pad contact plateaus. Pads with many small plateaus generated more squeal than did pads with few large plateaus.
Those observations in [9-13] imply that one of the reasons for fugitive behaviour in squeal is the changes in the sliding surfaces. Due to wear, the disc/pad interface changes with time and as a result pad/disc interface has different surface topographies generated under different braking applications. In this paper, the authors attempt to investigate the effect of brake pad surface topography on the fugitive nature of squeal. A detailed 3-dimensional finite element (FE) model is developed and validated through modal analysis and contact analysis. Brake pads surface profile is modelled based on the information obtained from the measurement made on the real brake pads interface. Different brake pad surface topographies are modelled in order to examine the fugitive behaviour of squeal. Prediction of squeal is made using a commercial software package, ABAQUS v6.4. Several structural modifications are Simulated in order to obtain a method of squeal suppression. In the end, suggestion of a good structural modification is also made.
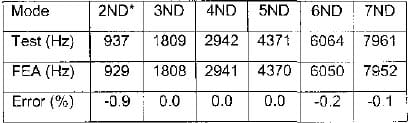
Table 1. Modal result of the disc at free-free condition
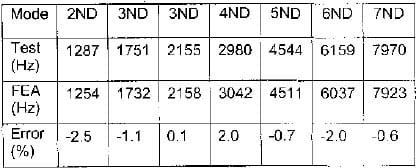
Table 2. Modal result of the assembly measured on the disc
FINITE ELEMENT MODEL
The finite element (FE) model, as shown in Fig. 6, consists of a disc (rotor), two pads, a caliper, a carrier, a piston and two guide pins. Damping shims are not included in the FE model. The model consists up to 8000 8-node solid elements and approximately 37,100 degrees of freedom. The disc is rigidly constrained but is allowed to rotate freely about its axial axis.
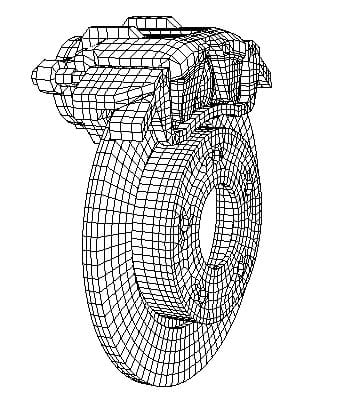
Figure 1. Finite element model of a disc brake.
Spring elements are used to represent contact interaction between brake components except for the disc/pads interface where element-based surfaces are employed. The FE model is validated using modal analysis at both components and assembly levels. Validation results of the FE model are shown in Table 1 and 2 respectively. From the tables, good correlations are achieved between the experimental and simulated results. The FE model is also correlated through contact analysis where static contact pressure ‘distributions are used to confirm between the experimental and simulated results. Correlation between predicted and experimental static contact pressure distributions is shown in Fig. 2. Details of the contact test and simulation are given in [14].
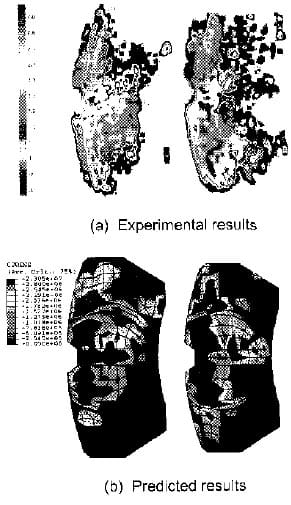
Figure 2. Static cont
act pressure distribution.
PREDICTION OF DISC BRAKE SQUEAL
Firstly, prediction of unstable frequencies using the complex eigenvalue analysis is made and compared with experimental results [15] for brake·line pressure between 0.1 – 0.9 MPa. A good correlation is obtained between the two results as shown in Fig. 3. It is shown that squeal mostly occurs at frequency of 4 kHz and above 7 kHz. The 4 kHz and above-7 kHz squeal are dominated by an out-of-plane mode with 5 and 7 nodal diameters of the disc respectively.
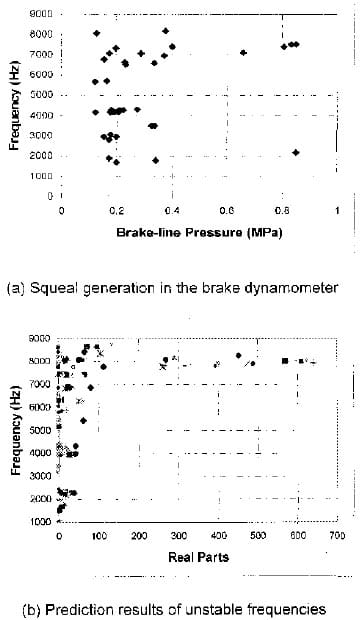
Figure 3. Comparison between predicted and experimental results.
WEAR EFFECT ON SQUEAL GENERATION
Bajer et al [16] incorporated wear lining effect in their model. This new capability is available in ABAQUS v6.5. Another way of incorporating wear into the FE model was done by Podra and Andersson [17] and Kim et al [18]. They manually adjusted contact interface nodes after simulating contact analysis in the first run. Using Archard wear formula, they calculated wear displacements and used the information to move the nodes of the contacted surfaces in the normal direction. A similar methodology to that of [17, 18] is adopted in this study and an Archard wear formula is employed which is then adjusted to the authors’ form as
h = kpΩrt
where h is the wear displacement, k is the specific wear rate coefficient, p is the contact pressure, Ω is the rotational speed, r is the pad mean radius and t is the disc sliding time. In order to simplify the simulation, constant specific wear rate is assumed to be k = 1.78×10-13m3/Nm3 [19].
For this investigation, brake-line pressure, sliding speed and kinetic friction coefficient are set to 0.4 MPa, 3 radls and 0.43 respectively. Disc sliding time is set to 600s and for each of wear simulation_ Contact analysis is firstly performed to obtain contact pressure_ Using the predicted contact pressure, wear displacement is calculated and FE nodes at the brake pad interface are adjusted in the normal direction for each Simulation The adjusted nodes are equivalent to removing some material on the contact surface of pads The new pad surface topography is then simulated to determine instability in the disc brake system This process is continued up to six simulations in order to observe significant changes in the unstable frequencies. Fig. 4 shows predicted unstable frequencies for a number of wear simulation.
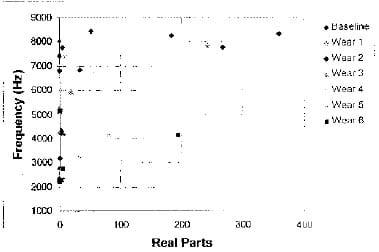
Figure 4. Predictions of unstable frequencies under wear simulation.
It can be seen that for a baseline model most unstable frequencies appear at above 7 kHz, which were also found in the experiment For the first two wear simulations it is found that these unstable frequencies remains. While for the third simulation there is no unstable frequency at all, In the forth simulation, although there emerges an unstable frequency It now drops to below 7 kHz, While in the fifth and sixth the unstable frequency changes to about 4 kHz.
From the above results it seems that at a particular brake surface topography with the presence of wear the brake system can evolve from an unstable state to a stable state even though the operating conditions are apparently the same. The above results may suggest that brake surface topography has a contribution towards the fugitive nature of squeal behaviour. However, its characteristics (topography) are rather difficult to quantify in order to explain this fugitive behaviour using the finite element method compared with the experimental method. Further investigation is required and will be the authors’ next task. Nevertheless, it shows the significance of wear effect on the squeal occurrence and consideration of surface topography may help engineers to obtain more realistic prediction particularly in appearance and disappearance of unstable frequencies within the same system and at the same operating conditions Figs. 5 and 6 show brake pad surface topographies and contact pressure distributions for the baseline model and wear simulation 3.
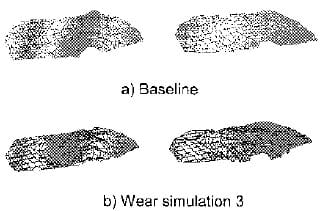
Figure 5. Brake pad surface topography: piston pad (left) and finger pad (right).
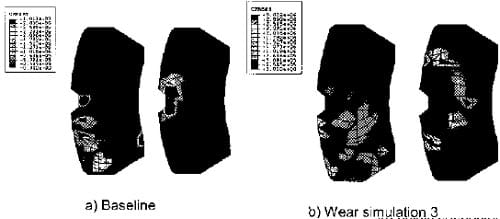
Figure 6. Dynamic contact pressure distribution at pressure of OAMPa and sliding speed of 3 rad/s. Top of the diagram is the leading edge.
STRUCTURAL MODIFICATIONS
Generally, structural (including material) modifications are a favourite means of improving squeal performance of the disc brake. In this work, several structural modifications are simulated and they are explained in Table 3. It is the authors’ intention to suppress squeal at frequencies of 4 kHz and above 7 kHz as these two frequencies dominate in the brake dynamometer tests. In doing so, a brake-line pressure of 0.8 MPa and a sliding speed of 6 rad/s are used.
From Fig. 7, it can be seen that using rigid connections at both pad abutments in the radial and circumferential direction (SM 8) and partial connection at the piston and finger pads (SM 2) [20J offers not much help to suppress unstable frequencies both at 4 kHz and above 7 kHz. Increasing Young’s modulus of the calliper (SM 1) and the disc (SM 6) can suppress the unstable frequency at 4 kHz but not the frequencies above 7 kHz. Applying rigid connection at the piston/back plate (SM 3) seems to change unstable frequencies to 5 kHz and 6.9 kHz. Similarly, increasing Young’s modulus of the back plate (SM 7) can only shift the unstable frequencies to 2.5 kHz and 6.9 kHz. Using rigid connection at the calliper finger/back plate (SM 4) will generate more unstable frequencies particularly at 3 kHz, 6.9 kHz and above 8 kHz. It seems that the only modification that can suppress those unstable frequencies is using combination of SM 3 and SM 4 (SM 5) in which rigid connections are applied to the piston/back plate and calliper finger/back plate. This means that those components (piston/piston pad and calliper/finger pad) are rigidly connected in all three directions and each pair would move together as one part.
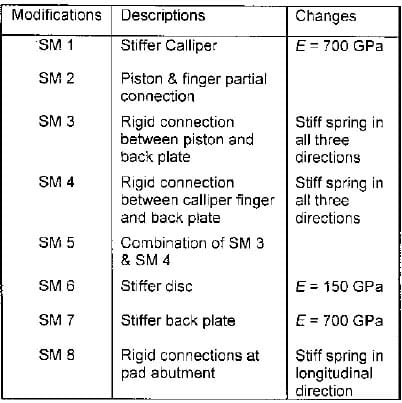
Table 3.Structural and material modifications
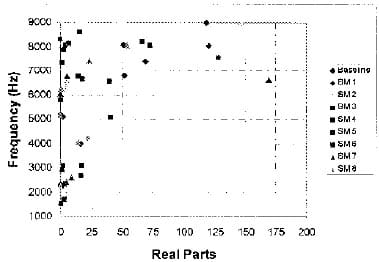
Figure 7. Prediction of unstable frequencies under structural modifications
In order to determine its effectiveness to eliminate or reduce instabilities in the disc brake system, this structural modification (SM 5) is simulated under different surface topographies that are investigated in the previous section.
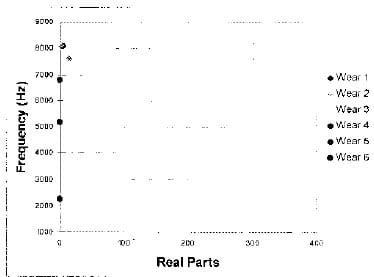
Figure 8. Predictions of unstable frequencies under wear effect against proposed structural modification
From Fig. 8, the results suggest that structural modification 5 (SM 5) is capable of reducing or eliminating unstable frequencies for different surface topographies. Comparing to Fig. 4 there is no unstable frequencies for wear simulation 1, 3, 4,5 and 6. Even though wear simulation 2 generates one unstable frequency at 7.5 kHz, the positive real parts are reduced significantly and the tendency to squeal is decreased If squea
l tends to occur at this frequency, this may suggest that squeal is difficult to suppress or eliminate in the presence of wear.
CONCLUSION
This paper investigates the effect of wear on the squeal generation using a commercial software package. Consideration of a real surface topography is seen to help to obtain realistic contact pressure distributions. Prior to the investigation, the FE model is validated through 3-validation stages, i.e., using modal analysis to correlate components and assembly model and using contact analysis to compare static contact pressure distribution over the experimental results. Using the validated model, predicted unstable frequencies are in good correlation with the squeal results found in the experiments.
With the Archard wear formula, the effect of material removal (wear) is simulated. The results show that the instability of disc brake system can vanish at particular wear condition or surface topography. This may suggest that surface topography has a significant influence on the fugitive nature of squeal behaviour. However, It requires further investigation to confirm thiS finding
Several modification ideas have been studied uSing the finite element method. It is found that by making rigid connections between the piston/back plate and calliper finger/back plate the disc brake system becomes stable in the sense that there are no positive real parts of their eigenvalues. Such modification is also proved to be effective even with the presence of wear or different surface topography.
ACKNOWLEDGMENTS
The first author wishes to thanks Dr Simon James of the University of Liverpool for providing the modal testing data, Dr Q. Cao of the University of Aberdeen for valuable help in tuning process, Sensor Product LLC for donating analysed images (Fig 2a) and Universiti Teknologi Malaysia for sponsoring the study.
REFERENCES
- Akay, A. ” Acoustics of friction”. J Acoust. Soc. Am., 111(4), pp 1525-1548, 2002.
- Samie, F, and Sheridan, D. C. “Contact analysis for a passenger cars disc brake”. SAE Paper 900005, 1990.
- Eriksson, M. ” Friction and contact phenomenon of disc brakes related to sq’Jeal”. PhD thesis, Faculty of Science and Technology, Uppsala University, 2000.
- Spurr, R.T. H Brake squeal”. IMechE, paper C95/71, pp 13-16, 1971.
- North, MR. ” Disc brake squeal”. lMechE, paper C38/76, pp 169-176, 1976.
- Crolla, D.A. and Lang, A. M. ” Brake noise and vibration – The state of the artn. In: Dawson, D., Taylor, C.M., and Godet, M. (Eds.), Vehicle Tribology, no. 18 in Tribology Series, pp 165-174, 1991.
- Ibrahim, RA ” Friction-induced vibration, chatter, squeal and chaos Part I’ Dynamics and modeling”. Appl. Mech. Rev., vol 47(7), pp 227-250,1994.
- Flint, J. and Hulten, J .• Lining-deformation-induced modal coupling as squeal generator in a distributed parameter disc brake model”. J. Sound Vib” 254(1), pp 1-21, 2002.
- Fosberry, RAC. and Holubecki, Z. ” Some experiments on the prevention of brake squeal”. MIRA report, No. 1957/1, 1957.
- Fosberry, RAC. and Holubecki, Z. An investigation of the cause and nature of the brake squeal”. MIRA report, No. 1957/2, 1957.
- Sherif, H.A. ” Investigation on effect of surface topography of pad/disc assembly on squeal generation”. Wear, 257 (7-8), pp 687-695,2004.
- Chen. G., Zhou, Z., Kapsa, P. and Vincent, L. “Effect of surface topography on formation of squeal under reciprocating sliding”. Wear, 253, pp 411-423, 2002.
- Eriksson, M., Bergman, F. and Jacobson, S. ” Surface characterization of brake pads after running under silent and squealing conditions” Wear, 232, pp 163-167,1999.
- Abu Bakar, A. R., Ouyang, H. and Siegel, J E. Brake pad surface topography Part I’ Contact Pressure Distribution”. SAE 05BC-4.
- James, S. ” An Experimental Study of Disc Brake Squeal”. PhD Thesis, Department of Engineering, University of Liverpool, 2003.
- Bajer, A” Belsky, V., and Kung, S.W. ” The influence of friction-induced damping and non-linear effects on brake squeal analysis”. SAE paper 2004-01-2794, 2004.
- Podra, P. and Andersson, S. ,. Simulating Sliding Wear with Finite Element Method” Tribology International, 32, pp 71-81, 1999.
- Kim, N.M. et al. ” Finite Element AnalYSiS and Experiment of Metal/Metal Wear in Oscillatory Contacts”. Wear, in press.
- Jang, H. et al. ” The effect of Metal Fibers on the Friction Performance of Automotive Brake Friction Materials” Wear, 256 (3-4), pp 406-414, 2004.
- Abu Bakar, A.R., Ouyang, H, and Cao, Q. ” Interface pressure distributions through structural modifications”. SAE paper 2003-01-3332,2003.