Attila Kis*, Nicholas Bottka+ , Ferenc Kovacs* and Peter Szolgayx
Abstract
Abstract – As the first step to build an adaptive tactile system on silicon, we have built up an experimental system with pressure sensory arrays Tactilus,® available on the market and an analogic CNN algorithm by using the Aladdin Pro cellular visual microproceuor development system. Using this system, we can measure and store some typical snapshots of topographic flows of pressure field in a tactile action and evaluate these field. by a set of analogic CNN algorithms.
1. INTRODUCTION
In the sensory revolution of information technology, we experience in our days, new sensing elements are used everywhere. The sensory outputs are continuous in value and may be discrete or continuous in time.
In living structures the sensing and “processing” parts are closely coupled providing “intelligent sensing”. We intend to build up a prototyping system where the sensory array output is processed by a CNN-UM (Cellular Neural Network – Universal Machine) processor [1 -2] . The CNN paradigm was successfully used in modeling the visual system of vertebrates, especially in the modeling of the retina (3-4]. So far, these types of sensor-processor structures have been studied in the case of optical sensors, but in this experiment we intend to use pressure sensors with CNN-UM. The most common approaches in pressure sensing are capacitance-based [5 -6], resistance-based [7] and piezoelectric [8] pressure sensors.
Though results in different implementations of pressure sensory arrays are already published, still very few of them are available as products. We have chosen Tactilus® [9] to build up a simple experimental system. The process of tactile perception is dynamical where the sensory array has to be moved in space to be sensed. Do to the dynamical perception, the processing system has to work with relatively big amount of data (tactile frames / sec.).
In this contribution we would like to record the snapshots on pressure field in some typical tactile actions and preprocess it by a CNN-UM.
The fIrst experiment is to determine an analogic algorithm for controlling a two-fingered robot hand holding a fragile object like a glass or a bottle. The target is to determine the minimal grasping force. The changes of the pressure fields are processed by the system and the moment when the object starts to slip out from the robot hand is sensed. Based on this information, we can provide a better feedback to the grasper.
The second experiment is to determine the properties, such as shape and size, of a given swface and to fInd bumps, holes and different textures on it.
In section 2 the experimental system is described. The analysis of some tactile process is given in section 3, and based on the experiments, some concluding remarks are given in section 4.
2. AN EXPERIMENTAL SYSTEM FOR TACTILE SENSING
This experimental system consists of three major parts, as it is shown in Figure 1.
The main-part of the signal processing system is Aladdin Pro [10]. This unit processes tactile image flow. In the process of detecting some movements across the sensor array, especially in detecting the phenomenon when an object is slipping out of fingers, we need a fast response from the processing unit that is well accomplished by the CNN·UM. Another need for analogic algorithms occurs when the requirement is to recognize the size, shape and texture of objects.
The sensory array is the Tactilus® tactile system, connected to a PC via a USB port.
The PC is used only to display the events and it makes the connection between th e sensor part and Aladdin Pro.
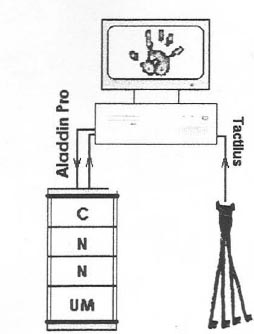
Figure 1: The experimental tactile system
Pressure sensing trough Tactilus
Tactilus® is an electronic tactile force and pressure indicating sensor. The reason why we use capacitor based sensors is that their pressure sensitivity is higher and they are more resistant to changes in operating temperature than the two other, most common approaches, resistor-based and piezoelectric pressure sensors. The sensors arc of linear responses, and low hysteresis. Performance is less likely to degrade over time.
Tactilus® allows monitoring precisely how force is dispersed between any two contacting or mating surfaces in real-time while the event occurs. The visualization of the pressure fields can be as follows: 20, 3D or histogram and the results can be rotated as well. The system includes a 50mm x 50mm palm sensor with 2.5 mm spatial resolution (21×21 tuxels) and five finger sensors, I3mm x 13mm each, 1.5 mm spatial resolution (9×9 tuxels). One luxel is one sensor point in a sensor array. The query ratc of this system is up to 60,000 sensors points/sec. The optimal range of pressure for sensor pads is 0-1 atm, accuracy ± 10% .
The spatial distribution of the arrays (e.g. Mounted on a glove) makes a configuration similar to that of a human hand possible, which lets us investigate the most important modality of somatic sensibility, the discriminative touch (required to recognize the size, shape, and the texture of objects and their movement on the skin surface) [II].
Aladdin Pro System provides a common framework for developing analogic CNN algorithms. The algorithms can be run on software simulators or a 64*64 CNN-UM analog VLSI chip [12]. The ACE4k is the platfonn containing a CNN-UM chip built in a board type PC I 04. The platfonn is connected to the host PC by a PCI bus interface providing the 64*64 CNN-UM a fast up -and ·down loading data capability.
3. ANALYSIS OF SOME TYPICAL TACTILE ACTIONS
Gentle Grasping
When grasping a fragile object such as a glass or a bottle, it is necessary to realize when the contact is made and to minimize the grasp force. Tactile sensors can provide better sensory information for this task than can be obtained by vision or force sensing. This algorithm is to detect the minimal force needed to hold an object with a two-fingered robot hand.
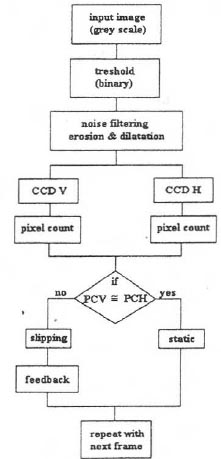
Figure 2: The flowchart of the algorithm for detecting the difference between pressure maps
The algorithm is continually tracking the pressuremap of the contact area, and detects when the object slips out of the fingers. The differences between thc shapes of the pressure-map when the object is well grasped and while it is slipping down, is recognized by algorithm in Question. This difference indicat
es the moment when the held object starts to slip. The orientation and speed of the event is calculated as well.
This information is used providing a proper feedback to the grasper. Conseguently the system can accomplish tasks which are very difficult to do with force and position sensors only.
Tbis task cannot be done only with one pressure sensor (sensing the normal pressure on each finger). But with the sensor array we can track the changes of the pressure field. which helps us to get better information about the actual condition of the grasped object.
In Figure 2 the flowchart of the algorithm is given. The first step is to get the shape of the pressure-map with a threshold template. The binary image is filtered from the noise by applying the erosion & dilatation morphologic operations. The width and the height of the map are measured by applying a horizontal CCO template by counting the pixels of the output image and in the same way for the vertical direction.
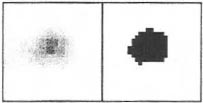
Figure 3: The pressure-maps: a) static pressure, b) with threshold
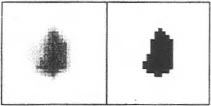
Figure 4: The pressure-maps: a) snapshot of the dynamical-slipping map, b) and its thresholded shape
All the templates are available from the CNN Software Library of Aladdin Pro System.
Surface reconstruction by using pressure maps
When we want to get some information about the texture and shape of an object, the importance of tactile information is obvious.
Texture sensing-recognition is an important need in telesurgery and minimal invasive surgery when surgeons cannot directly touch the diseased part but with a special device.
A different, but in the same way important task in robotics is the ability of recognizing the shapes of the objects in unstructured and changing environments, especially in cases when visual sensing is not enough (in the dark, smoke etc.).
Due to the neuro-physiology of tactile sensing, we can percept the textures better when we move our tip across the surface of an object, than in the case of static touch. The main reason of this is that the mechanoreceptors in our tips adapt to static stimuli.
This experiment is to determine the properties, such as the shape and size, of a given surface and to find bumps, holes and different textures on it.
The sensory array is mounted on an actuator moving in 20. For each tactile frame the system knows the X-Y coordinates of the sensory array. The images are interlaced, and after preprocessing they form the final image of the surface.

Figure 5: The pressure maps of the corners

Figure 6: The process of reconstruction
The algorithm joins the comers given by the pressure-maps. The surface of the object is obtained by filling the space between the corners and edges.
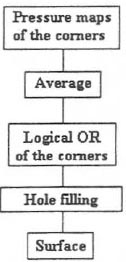
Figure 7: The surface reconstruction algorithm
This anaiogic CNN algorithm can help to understand how blind people can reconstruct the environment in their imagination.
4. CONCLUSION
An experimental system of an adaptive tactile sensing process was set up by using an Xsensor system and Aladdin Pro with 64×64 CNN-UM chip. Analogic CNN algorithms were developed and tested. The time requirement of pressure sensing process was higher than the total time requirement of the analogic CNN algorithm running on the chip. The sensor array is scanned with 16 frames/sec. The average running time of the analogic aJgoritm is about 21 ms. The actuators of the robot hand can be driven by the results of the analogic CNN algorithms.
Tactile sensing provides a rich set of information about the manipulation process, and the unexplored areas of tactile sensing research are numerous. In research regarding tactile sensing a next step is to demonstrate a closer coupling between vision and touch.
ACKNOWLEDGMENT
This project has been supported by the: “Hungarian National Research and Development Programme: TeleSense NKFP 2001/02/035”. Grant OTKATS40858 (National Research Fund, Hungary).
REFERENCES
- L. O. Chua, L. Yang, “Cellular Neural Networks: Theory”, in IEEE Transactions on Circuils and Systems, Vol. 35, pp. 1257-1272.,1988
- T. Roska, L. O. Chua, “The CNN Universal Machine – an Analogic AIr~ Computer”, in IEEE Trans. on Circuits and Systems II: Analog and Digital Signal Processing Vol. 40, No.3, pp. 163- 173, 1993
- D. Batya, B. Raska, T. Roska, F. Werblin, “A CNN Framework for . : Modeling Parallel Processing in a Mammalian Retina” International Journal of Ciroit Theory and Applications,Vol. 30, pp.363-393, 2002
- M. Brendel. T. Roska, “Adaptive Image Sensing and Enhancement Using the Adaptive Cellular Neural Network. Universal Machine”, International Journal of Cimit Theory and Applications. Vol. 30, pp.287-312, 2002
- Pressure Profile Systems. Capacitive SenSing, Los Angeles, 2002, www.pressure-profile.com
- Pressure Profile Systems, TactArray. Los Angeles, 2002, www.pressure-profile.com
- B. J. Kane, M. R. Cutkosky. G. T. A. Kovacs, “A Traction Stress Sensor Array for Use in HighResolution Robotic Tactile Imaging”, in Journal of Micro electromechanical Systems, Vol. 9, No.4, pp. 425-434.,2000
- PCB Piezotronics, General Piezoelectric Theory and Introduction to Piezoelectric Pressure Sensors, 1999
- Sensor Products, XSENSOR Real-Time Tactile Pressure Measurement, East Hanover, 2002, www.xsenSOLcom
- Aladdin Pro System, Analogic Computers, 2002, www.analogic-computers.com
- E. R. Kandel, J. H. Schwartz and T. M. Jessell: Principles of Neural Science. Publisher: McGrawHill/ Appleton & Lange; 4th edition (Jan. 5,2000)
- S. Espejo, R. Dominguez-Castro, G. Linan, A. Rodriguez-Vazquez, “A 64×64 CNN Universal Chip with Analog and Digital 110”, Proceedings of 5th IEEE Internalional Conference on Electronics, Circuits and Systems, (lCECS’98). pp. 203-206, Lisboa, 1998
- M-H. Bao, “Micro Mechanical Transducers, Pressure Sensors, Accelerometers and Gyroscopes”, in Handbook of Sensors and Actuators Vol. 8, Elsevier Science B.V., 2000
- K. Suzuki, K. Najafi, K. D. Wise, “A 1024- Element High-Performance Silicon Tactile Imager”, IEEE Transactions on Electron Devices, Vol. 37, No.8, pp. 1852-1860., 1990
- G. T. A. Kovacs: Micromachined Transducers Sourceboak, McGraw-Hill, 1998
- K. S. J. Pister, “Introduction to MEMS Design and Fabrication”, in Berkeley Sensor and Actuator Center, UC Berkeley, 2002
- W. P. Eaton, J. H. Smith, D. J. Monk, G. O’Brien, and T. F. Miller, “Comparison of Bulkand Surface- Micromachined Pressure Sensors”, Micromachined Devices and Components, Proc SPlE, Vo13514, p. 431, 1998