Article: Paper, Film & Foil Converter
During tough economic times, it may be tempting to reduce quality control to cut costs. However, Dolph Beyer, an engineer with Mohawk Fine Papers, asserts that doing this actually is counterproductive. He has determined that using Pressurex® pressure-indicating sensor film as a quality control tool actually decreases costs while significantly improving product quality.
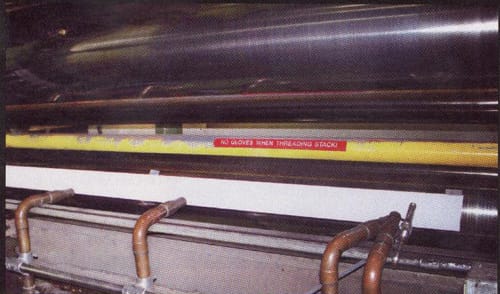
Pressurex® sensor film is placed on the roller at Mohawk Fine Papers before closing the nip.
Custom Converter
Perhaps best known as one of the largest premium paper manufacturers in North America, Mohawk Fine Papers also offers specialty converting services, including sheeting, slitting/rewinding, laminating, and embossing. Sheeting is accomplished on Bielomatik and E.C.H. Will equipment, among others. Jagenberg and Webco supply slitting/rewinding equipment.
Mohawk uses Pressurex® sensor film to take static nip impressions on its press section and dynamic nip impressions on its calenders. Dynamic nip impressions are inspected for uniformity and static nip impressions for uniformity and nip pressure. Image results of Pressurex® are archived and used as a control to compare tools and processes.
Beyer says pressure-indicating sensor film is especially helpful with calender rolls, which are swim rolls that have mechanisms to allow the center of the rollers to exert a different level of pressure. “Similar to crown rolls, swim rolls need to be carefully monitored to ensure even and exacting pressure is being applied to achieve optimum nip conditions,” he says. “We use the film to create just the right nip and improve the roll shape and crown to deliver better sheet uniformity.”
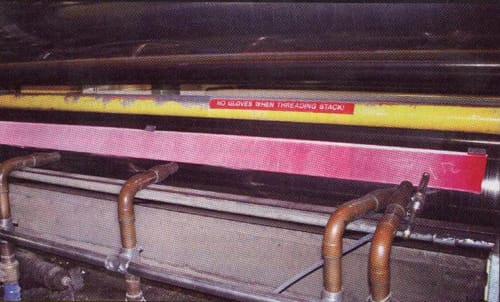
Pressurex® reveals variations in nip contact pressure that can be quantified easily.
How Sensor Film Works
Pressurex® reveals pressure from 2-43,200 psi (0.14-3,000 kg/cm²). When placed between contacting rollers, the sensor film instantaneously and permanently changes color directly proportional to the actual pressure applied (see Figure 1). Precise pressure magnitude then is determined easily by comparing color variation results to a color correlation chart (conceptually similar to interpreting Litmus paper).
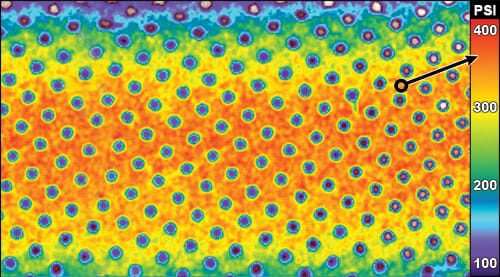
Figure 1. Nip impression image using Pressurex® film, which reveals nip pressure magnitude and distribution.
Variations in pressure that lead to defects in papermaking, converting, and printing can be quickly and accurately detected and corrected — improving yield, decreasing scrap, and increasing productivity.
By examining pressure variations in the nip, corrections in alignment and crown profiles can be made. The film is said to be effective on virtually all roller compositions and surfaces. A visual pressure mapping profile of an engraved pattern or drilled roll can be produced effortlessly to expose minute surface defects and other imperfections.
Pressurex® is extremely thin (4-8 mils) and flexible, which allows it to conform to curved surfaces. It is ideal for invasive, intolerant environments and tight spaces not accessible to conventional electronic transducers, according to the manufacturer. While recommended for tests in non-operating conditions, the sensor film can be used at temperatures exceeding 200 deg F (93 deg C) for brief intervals.
“By taking nip impressions with pressure-indicating film every couple of weeks, we have extended roll life by a few months in many cases,” Beyer says. “This quality control measure not only lowers costs for the replacement of these covers but also minimizes equipment downtime.”