Article: Armor & Mobility
As part of its new Future Soldier Initiative, the U.S. Army is collaborating with industry to develop the next generation in smarter tactical body armor.
In October 2009, the Office of the Assistant Secretary of the Army for Acquisition, Logistics & Technology (ASA/AL&T), in coordination with Natick Soldier Systems (NSS), Natick, Ma, began an initiative called the Future Soldier Initiative (FSI) directed at analyzing the Army’s long term strategy for balancing warfighter capabilities needs with science and technology trends through the use of hi-tech war gaming and simulation using actual input from ‘soldiers on the ground’.
In an effort to ‘tighten the loop’ in the area of capabilities testing, historically a task of U.S. Army Training and Doctrine Command (TRADOC), NSS is examining the performance of individual body armor equipment in trying to get a feel for what types of capabilities soldiers are likely to need to perform future missions at the platoon and company combat unit level.
Using real-time information gleaned from actual combat experiences today, NSS is providing the Army with actionable information on documented and potential future anomalies or “gaps” regarding specific systems used today so that DOD can direct science and industry in particular evolutionary directions that are most likely to eliminate these gaps.
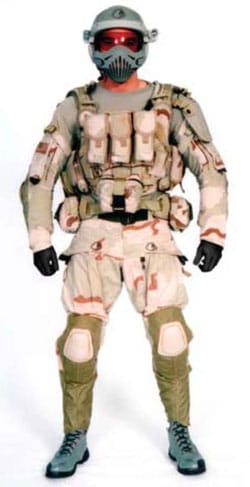
DoD’s Future Force Warrior design concept is one of a series of late
model body armor systems in line for fielding in 2010.
One of the areas FSI researchers have found to exhibit wide gaps in consistency is in the simulated testing and evaluation of body armor technology. Modern tactical body armor is heavy, hot, chafes the wearer, restricts movement and it smells after prolonged use. Soldiers typically dislike wearing it until they witness its effectiveness in preventing lethal injuries, and then it is worth its weight in gold.
“Using information that we gain from simulation and war game testing, we are able to predicate likely outcomes across particular systems in implementation and development in the face of environmental factors that already exist or are yet to exist,” said Dr. Jason Augustyn, Cell Lead for the Army’s Future Soldier Initiative. “The results we produce can be compared with work being done at Army TRADOC to help give the service a clearer indication as to how to invest in future capabilities such as body armor.”
Within a controlled test environment, NSS scientists and researchers conduct simulated war game scenarios for specific real world tactical situations. Particular scenarios involve conditional factors such as terrain, climate, urban vs rural, and demographic make-up. Actual warfighters are asked to be role players on a virtual battlefield comprising various color-coded cells representing combatant and non-combatant groups. The tactical scenario is at first broken down into a series of fragmentary orders, each informing the role players the conditions within a given situational scenario at a specific time.
“Through the interactions of each cell group, NSS researchers gather data from actual resultant actions to predict likely reactions from the command level down to the individual soldier system level,” said Augustyn. “The researchers work directly with the role players to determine where the capability gaps exist from the command level down to the individual soldier system level.”
To reduce the aforementioned failings, and also to increase performance, KDH Defense Systems, a Johnstown PA based company with a product line of tactical armor, was contracted by the U.S. Air Force to develop advances in all aspects of body armor application. KDH approached EDGE Product Development, a product development consultancy with offices in both PA and CA and asked EDGE to examine body armor vest design with a focus on human factors engineering. “Our goal was to develop a design based from the get gooutset on the needs of the wearer,” says Jeff Payne, who is responsible for managing the program for KDH, “so we pulled together a development team combining our personnel and HFE and engineering specialists”.
Challenges and Tradeoffs in Body Armor Design
According to Edge, Vest design requires a fine balancing act between several factors which are all related and often directly (see Fig 1). For example, ideal armor will feature improved ballistic performance but be of a lighter weight than current systems. Increased coverage for protection negatively affects heat dissipation properties, the wearers’ range of motion and overall system weight.
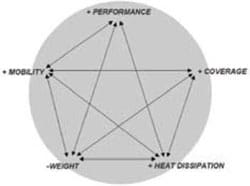
Figure 1 – Inherent tradeoffs in body armor design. Courtesy
of Edge Product Development Inc.
The program is focused on overcoming these tradeoffs as much as possible through good design and use of materials. Additionally, the decision was made by Edge to try to keep development focused on systems that were “offensively focused”. As Eric Kemner, a program manager at EDGE with 5 years of active duty service explains: “The value of an armor system is diminished the instant that it compromises the ability of a soldier to engage a threat. Body armor that negatively affects marksmanship is of no use – we don’t want to negate the soldier’s ability to react to enemy contact.”
“The Tactilus® pressure mapping system … shows us any pressure points that develop, not just when soldiers stand in place but also when they perform ballistic motions, such as jumping, running quickly, turning, crouching or crawling on their bellies,” said one of the project leaders, Dr. Evan Goldman, a professor of gross anatomy and physiology at Philadelphia University. “By viewing images and statistics from sensors located beneath their vests, we can see how these pressure points move with the body in real time as they perform their maneuvers.”
Weight Watching
The major complaint that users have about current systems is weight. A typical current issue large Improved Outer Tactical Vest (IOTV) weighs approximately 35 lbs, with the vast majority of that weight coming from the armor components.
Kemner says aAll effective vests rely on Small Arms Protective Insert (SAPI) hard ceramic plates for rifle round protection. While there have been advances in these plates over the years the weight of a large chest plate is still close to 5 lbs. Full coverage vests will carry two large plates and additionally two smaller side plates, with a plate weight of around 15 lbs.
In addition to the plates, vests feature soft armor made from dozens of layers of woven aramid fiber, such as Kevlar. Soft armor typically protects against handgun rounds and fragmentation, and weight of this component varies with the type of coverage offered by a specific vest. Full coverage vests, such as the IOTV, will offer much more protection than a lightweight plate carrier. The desired level of coverage varies for different groups and sometimes for different missions. Covert operatives tend to prefer a lightweight plate carrier to retain speed and mobility, whereas troops visibly patrolling a known hostile environment will be better served with a full coverage vest.
In addition to the weight of the armor, users attach a variety of pouches containing equipment such as ammunition and grenades, radios, flashlights, water and first aid kits to their vests (commonly referred to as “battle rattle”) with a typical combat load weighing around 30 lbs.
The team considered two options when looking to reduce the load on the wearer.
The first option examined was to reduce the weight of the carrier as much as possible, using lightweight webbing, minimizing double layers of Cordura wherever possible and examining every element of the carriage for weight reduction. Ultimately this focused approach began to create more problems than it solved as the vest was less resistant to wear and user comfort began to suffer. Shaving ounces from the vest carriage when it can be safely assumed that the wearer will strap over twenty five pounds of gear on top of it makes minute weight reductions imperceptible. In addition to this, armor will get lighter over time but it is unlikely that large gains will be made in the near future. The large amount of kinetic energy in a speeding rifle bullet that needs to be dissipated in a very small distance has to be accommodated through material that requires density and toughness, both to absorb the energy of the round and to keep backface deformation down to a minimum. The decision was made to design around the weight of today’s hard armor. While under KDH guidance another team at Nanomech Inc. in Springdale, Arkansas is working on developing lighter ballistic material with improved antimicrobial properties using a variety of nanotechnology based materials and manufacturing processes.
For the second approach, the EDGE team looked at mechanisms to effectively distribute the load away from “hotspots” on the wearer – typically the tops of the shoulders and around the neck. Existing vests accomplish this to some degree using internal and external cummerbunds, yet user injuries still prove that additional support and control is desirable. EDGE started out by developing dozens of prototypes incorporating diverse mechanisms including interior skeletons, elastic elements and webbing arrangements of original design and pulled from existing products such as hiking backpacks. Over time and through many reviews and refinements some approaches became front runners but the development team was still relying on personal experience and subjective perception to evaluate the system.
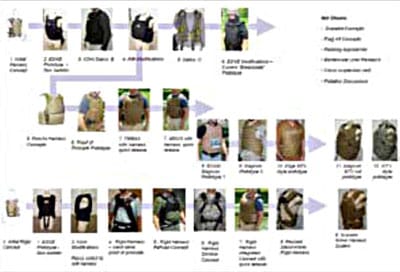
Figure 2 – Early development of prototype body armor systems
by KDH Defense and Edge Product Development
System Testing
It is easy to quantify the total load an armor system places on the soldier, it is simply weighed. It is not as easy to determine exactly what makes one armor system more balanced and comfortable than another. This information was vital to proving the worth of the experimental load management systems. While the team felt they had an improved armor system design, the only real number available at that time was total system weight.
Hard data was needed to prove the benefit of the systems. “We were getting a lot of positive feedback and we could feel the improvements in the systems when we put them on”, says Payne, “but we wanted to quantify the systems and when we looked around it became apparent that we would have to develop a test plan of our own to get data”. KDH Defense engaged Dr Evan Goldman, an Assistant Biology Professor at Philadelphia University. Dr Goldman developed a test plan and started evaluating the body armor prototypes for thermal resistance, pressure points, peak and overall forces, protective coverage, maneuverability, and range of motion, (additional info in sidebar).
Initial pressure and comfort testing relied on the opinion of test subjects. It rapidly became apparent that what was needed was hard data – load cells on the shoulders were considered but even the smallest cells would create pressure points of their own and would not provide adequate resolution. After some searching, KDH approached Sensor Products Inc., a New Jersey company that specializes in making surface pressure measurement equipment including the Tactilus Body Mapping system, a modular, scalable pressure sensing system with the ability to measure pressures from 0.1 PSI to 500 PSI.
Jason Blume, an engineer at Sensor Products Inc., discovered new uses for the Tactilus electronic sensor system specified for the project when he suggested the sensors could work in a new configuration to fit the size and shape of the vest and carriage.
Previously Sensor Product Inc.’s systems had supported square or rectangular designs, such as mattresses for ergonomic testing. While they were optimistic, there were questions about whether the sensors’ electronic lines could be cut and reconfigured to the vest. Three separate sensor pads needed to be used for the chest, back and waist, and clear color-coded body mapping images and precise statistics had to be produced without signal interference.
“The challenge for us in sensor technology was to modify our sensors and software to conform to the dimensions of a vest, while providing full three-dimensional pressure distribution visibility of the chest, back and neck,” notes Blume.
Sensor Products Inc. split up the sensing points; rows of sensors were distributed into two connecting L patterns, with one L inverted to face the other to provide coverage for the neck, shoulders and trunk. A third sensor pad was configured to wrap around the soldier’s waist. The software was broken up into multiple pieces for full system functionality. The sensors were then melded into the vest to serve as a guide for future prototypes.
Testing began in earnest. For true “apples to apples” comparison, prototype vests with the exact same amount of coverage as currently issued IOTV and MTV systems were built, using identical weight and shape armor components as those deployed.
From an Army perspective, the concept of body mapping in body armor development has clear potential from an immediate and long-term standpoint. “In the short term, the capability to measure improvement in performance as a function of individual warfighter needs through the use of condition-based data, specific to both wearer and wearer environment is a key part of FSI,” said Augustyn. “With this soldier-to-soldier information, we can better analyze how certain capabilities impact the greater combat unit as a whole, hence enabling the Army to make more educated technology investment decisions down the road.”
The body armor program is an ongoing effort and products are only now beginning to spin out of the research. Prototypes are being fielded with front line operatives and multiple patents have been filed as a result of the work.
Dr. Goldman attests that the armor being created has technological advantages. “While one of the armor prototypes excelled in some of our design goals, we could tell through the full-torso sensors that it limited the wearer’s range of motion. Thanks to the Tactilus sensor technology, the superb new armor we are creating has tremendous measurable enhancements compared to current military armors.”
Concepts Going Forward
From an Army perspective, the concept of body mapping in body armor development has clear potential from an immediate and long-term standpoint. “In the short term, the capability to measure improvement in performance as a function of individual warfighter needs through the use of condition-based data, specific o both wearer and wearer environment is a key part of FSI,” said Augustyn. “With this soldier-to-soldier information, we can better nalyze how certain capabilities impact the greater combat unit as a whole, hence enabling the Army to make more educated technology investment decisions down the road.”
The body armor program is an ongoing effort and products are only now beginning to spin out of the research. Prototypes are being fielded with front line operatives and multiple patents have been filed as a result of the work.
Human Factors Testing of Military Body Armor
Current body armor systems offer effective protection but the additional load from the armor and accessories have lead to a variety of reported injuries. Injuries include abrasions, muscle pain, heat injury, and significant nerve, vascular, and musculoskeletal injuries (1-4). The injuries caused by wearing armor in the short-term may result in reduced soldier effectiveness in the field. In the long term, the repetitive injury can be cumulative and result in mandatory recovery periods to prevent permanent disability.
Research is being done at Philadelphia University to evaluate human factors aspects of wearing body armor. The current Marine Tactical Vest (MVT), Improved Outer Tactical Vest (IOTV), and prototype armors by KHD Defense Systems Inc. are being evaluated. Research objectives include measurements of vest heat dissipation, protective coverage of the vests, and presence of regions of excess pressure (pressure points). Measurements are made during both static (sitting, standing, kneeling) and dynamic conditions (e.g. crawling, jumping, running).
Heat load:
One of the physiological measurements being evaluated is therefore the heat loading effects of the difference armors. Philadelphia University researchers are evaluating temperature by placing thermal-sensing electrodes directly on the skin or between the armor and the army combat uniform (ACU) while the subject stands or performs basic exercise (stair-stepping). The placement of skin electrodes provides a measure of heat generation by the subject. The measurements taken between the ACU and armor approximate the heat dissipation or conversely, how much heat is being trapped by the armor.
Static measurements:
To evaluate how the weight of the armor is distributed over the body, Philadelphia University researchers are using a custombuilt pressure-mapping system (Tactilus: Sensor Products Inc.). The sensor device consists of three pads, assembled in a vest shape and worn under the body armor. The pressure sensor system provides graphical and numerical displays of interactions between the body armor and the subject (Fig 1). The settings can be adjusted via a software interface so that all pressures are visible or only pressures reaching a pre-determined threshold value are visible. The latter is essential to determine the presence of pressure points and the former allows instant feedback that shows the weight distribution patterns over the entire trunk.
Dynamic measurements:
The Tactilus sensor pads are used in the dynamic tests to evaluate the weight distributions while subjects walk, crawl, reach (overhead, forward and to the sides), job in place, jog up stairs, and sprint. In many of these conditions, as with the static measurements, subjects carry a mock M-4 weapon to test whether the armor constrains necessary motions. All tests performed have shown that the armors have their own characteristic weight distributions. Typically, the pressure points are reproducible and have been noted in more than one of the dynamic tests. These data have been used to help customize and redesign the prototype armors.
Current findings:
The data collected thus far has shown clearly the deleterious effects of carrying heavy armor. Even before evaluating the data, petechiae (local trauma resulting in blood leakage from capillaries) were seen on the shoulders of subjects following the dynamic tests with both the MTV and IOTV. Subjective surveys taken throughout the testing procedures led the researchers to expect a finding of significant pressure points on shoulders but the visual effect of fresh bruising made evident the reality of the complaints we had noted. The sensor pad data provided quantifiable evidence of the burdensome shoulder pressures. Heat loading experiments also showed clear advantages of the internal frame/hip belt prototype. The sweating manikin data in particular showed decreased thermal resistance meaning the armor allowed for more heat dissipation. The presence of the semi-rigid internal frame likely provided pathways for heat to escape and in practice, would allow the wearer of the armor to stay cooler.