Article: U.S. Tech
When laminating a printed circuit board, we try to achieve good contact between the resist and the substrate surface by making the resist flow to conform to the surface topography. Flow is achieved by lowering the resist viscosity by heating it, and by applying a pressure differential for a certain time to cause the flow.
The pressure may be transmitted to the lamination rolls pneumatically, hydraulically, mechanically, or a combination of two or all three methods.
Insufficient pressure and/or non-uniform pressure can lead to lamination defects. These include: dry film resist wrinkles or defects in a print and etch process, in tent and etch, as well as in plating applications due to poor resist conformation caused by insufficient nip pressure. If the resist is not in good contact with the copper surface in a print and etch application, the etchant can penetrate the interface between the resist and the copper, attacking the copper line that should have been protected. If the etch damage is limited — not all of the copper is etched away, then the defect will be a so-called "dish down". If the copper is completely etched away at the location where the resist has conformed poorly, then the defect will be an "open".
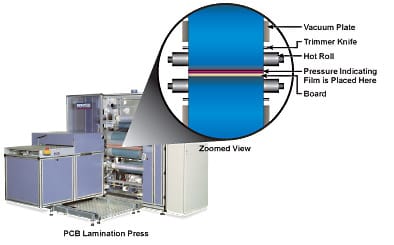
Figure 1: Properly aligned laminator.
Poor conformation of the photoresist in a tent and etch application can cause similar defects. In addition there is the danger that the through-hole metal is etched away if the poor conformation is at the annular ring around the through-hole.
Poor conformation in a plating application can allow copper and possibly metal etch resist, e.g. tin/lead solder or tin, plate to get under the resist line. When this happens, the copper that needs to be etched away after resist stripping is thicker and may be protected by metal etch resist so that it won’t etch, thereby causing a short.
Because of all of these potential problems, it is desirable to have a way of measuring nip pressure magnitude and uniformity. Pressurex® surface pressure indicating film measures the actual force profile at the interface of the roller set. The film is placed between the two rolls before closing the nip. After closing the nip, and applying the pressure, one can observe the image captured by the film revealing both the pressure distribution and magnitude by color in what is called its "footprint".
Measuring the Pressure
The force on the resist is not measured directly. A pressure gauge measures pressure applied to the pneumatic cylinders which close the lamination rolls. The actual force on the resist depends on the design of the roll loading system, taking into account the actual area of the cylinders and the mechanical leverage, if any, of the system. So it is desirable to have a direct nip pressure readout by testing with pressure-indicating film. This test gives insight into a potential problem with "bowing" of rolls, especially with thicker boards, and the test can measure the effectiveness of so called "crowned rolls" in counteracting bowing and in achieving a uniform pressure profile across the panel.
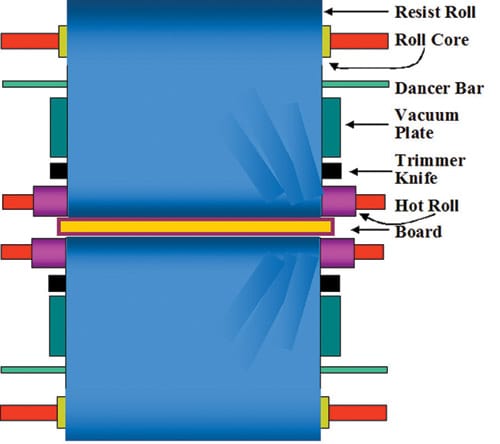
Figure 2: Lamination wrinkles, possibly caused by lamination rolls closing on right side before left side; closing force greater on the right side.
To measure improved resist conformation at higher pressures we used AOI to test for circuitry defects which are associated with poor resist conformation, such as "opens", nicks, dish-downs, and line thinning on a print and etch test pattern, at air pressures of 4 Bars and 7 Bars with an ASL-24 automatic sheet laminator. The two pressures correspond to forces of 36 lbs/in and 62 lbs/in, respectively. At the higher pressure, defects were reduced 79 percent from the lower pressure level. While this is a significant reduction, it is difficult to take advantage of the higher pressure because the lamination rolls bend under the increased pressure. This roll bending results in an uneven roll footprint on the resist. Roll bending can be compensated for with rolls which are "crowned".
A crowned roll has a rubber covering which is thicker in the center than at the edges and changes gradually from center to edge, resulting in a curved profile. We found that the correct amount of crown was in the range of 3-4 mils (75-100 microns).
Using Crowned Rolls
Crowning reduces the circuitry defect count both in the low and high pressure modes, the best case being high pressure and crowned rolls. Rubber suppliers are able to supply such crowned rolls.
Higher pressure was shown to be beneficial. Also, for straight rolls that are bending, there will be an abundance of opens in the center of the board in machine direction where the pressure is lowest due to roll bending.
It should be noted that a properly aligned and maintained laminator is the first step towards wrinkle-free lamination.
Problems with Wide Resist
A general rule is that wrinkles, on a reasonably maintained laminator, are a problem only when laminating wide resist or when laminating very thin laminate.
Laminator rolls bend when subjected to lamination loading. The bending causes higher driving speeds at the edges than in the center of the panel. While this usually does not affect the panels, except for very thin laminate, it can drive the resist film in a way that the film edges tend to move toward the middle, resulting in lamination wrinkles. If the loading is high enough to "iron out" the wrinkles during the time the film is being held by the vacuum bar, the wrinkles may not appear until the very end of the cut sheet when the film is dropped by the vacuum bar. Frequently, "comet tails" on tooling holes are caused by a combination of roll bending and poor control of the resist trailing edge.
The clamp pressures must be set at the same pressure for wrinkle-free lamination. This source may be one of the biggest causes of long wrinkles starting mostly at the middle of the panel and moving back at a small angle to the lamination direction.
Post-Lamination Wrinkles
The PL wrinkles can have a variety of causes one of which can be excessive lamination pressure. PL wrinkles are caused by heat and stress in the polyester base. While the need for good conformation requires as high a lamination pressure as possible, this pressure can add to the stress in the base.
In conclusion, maintaining the correct and uniform pressure across a hot roll laminator nip, e.g. through the use of pressure sensitive indicator film, is a useful process quality assurance technique for the detection and correction of roll misalignment, too low, or excessive or uneven pressure.