Article: JEC Composites
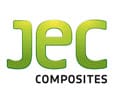
Resin Transfer Molded (RTM) composites are increasingly being produced with complex geometries that challenge the ability of engineers to maintain exacting tolerances. Preforms consisting of core materials such as honeycomb, foam and balsa must fill the complex mould uniformly to prevent defects that would otherwise occur during resin infiltration of the preform.
Pressure indicating sensor film is used as a quality control method to correct and prevent defects that result if the preform does not uniformly fill the mold. The film is used to test the preform before the resin is injected so that any needed modifications to the preform may be made to prevent a bad part from being produced. When uniform pressure in the mold is achieved during testing with the pressure indicating film, the result is uniform resin flow and a good composite part.
Pressurex® pressure indicating film from Sensor Products is an easy-to-use tool that reveals the distribution of surface contact pressures in cores, composite lay-ups and bonded surfaces; as announeced on July 17, 2009. After the fibrous preform is put into the mould, the film is placed on top of the preform and the mould is closed. Without injecting the resin, the mould is then opened and the pressure sensing film is inspected. Areas of high and low pressure are immediately revealed by the film which instantaneously and permanently changes colour directly proportional to the actual pressure. The precise pressure magnitude is easily determined by comparing colour variation results to a colour correlation chart (conceptually similar to interpreting Litmus paper).
RTM, Vacuum Assisted RTM (VARTM), and Lite RTM composite parts that require variable part thicknesses are particularly aided by the sensor film, since attaining uniformity of fiber volume fraction is very difficult. In regions of low pressure indication, the preform thickness can be enhanced, either with a thicker core material or inclusion of additional fiber. Conversely, in regions of high pressure indication, either the core material can be made thinner, or less fiber can be included.
Pressurex® has a wide variety of uses in manufacturing process control and machine/component inspection. Snapshot imaging results of the film can be used as a control to compare processes and tools, making it ideal for Six Sigma and other closely monitored high performance manufacturing operations. Additional statistical and imaging pressure analysis of the exposed film is available, if desired, from Sensor Products Inc.
Pressurex® measures from 2 – 43,500 PSI (0.14 – 300 kg/cm²) and is available in several different pressure ranges. The film is very thin (4 or 8 mils thick) and can be hand or laser-cut to any size or dimension. It is flexible and conforms to curved surfaces.
Coated on a Mylar sheet, the film is physically similar to a sheet of paper.