Article: PCB Magazine
Nella laminazione di un circuito stampato si sta tentando di arrivare a un contatto ottimale fra il resist e la superficie del substrato, facendo si che il flusso di resist sia il più conforme possibile alla topografia della superficie della scheda. Il flusso viene ottenuto abbassando la viscosità del resist mediante l’aumento della temperatura e applicando una pressione differenziale per un certo periodo di tempo, di modo da dare origine al flusso stesso. La pressione può essere trasmessa al rullo di laminazione in modo pneumatico, idraulico, meccanico o mediante una combinazione di questi.
Una pressione insufficiente e/o una pressione non uniforme possono portare a difetti di laminazione come le grinze nel dry film resist o a difetti evidenti nella stampa e nella fase di etching a causa di una deposizione del resist particolarmente povera a causa di un’insufficiente pressione del rullo pressore.1-9
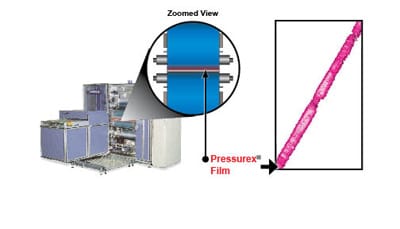
Un sistema per controllare visivamente i difetti successivi alla deposizione di resist garantisce di evitare perdite importanti e rallentamenti nelle fasi di produzione. Si tratta di un sistema innovativo che, per essere compreso nelle sue linee generali, necessita della conoscenza di problematiche meccaniche abbastanza complesse
UNA SOLUZIONE: PRESSUREX®
È desiderabile quindi disporre di un sistema che misuri la quantità di pressione e I’uniformità della stessa. Pressurex®9, indicatore di pressione superficiale del film, misura la forza dell’attuale profilo sull’interfaccia del rullo. L’indicatore di pressione del film viene piazzato fra i due rulli prima di chiudere il rullo pressore. Dopo la sua chiusura e a seguito dell’applicazione della pressione è possibile osservare l’immagine catturata dall’indicatore di pressione del film con la possibilità di evidenziarne la distribuzione della pressione cosi come la sua magnitudine (il termine comunemente utilizzato è "footprint").
Pressurex® (vedi Fig. 1) misura pressioni comprese fra 2 e 43.200 PSI (da 0,14 a 3000 kg/cm²). Quando viene piazzato fra le superfici a contatto fra loro, questo cambia colore in modo istantaneo e permanente e in modo direttamente proporzionale alla pressione al momento applicata. La magnitudine di pressione precisa viene facilmente determinata confrontando i risultati delle variazioni del colore e paragonandoli con una carta cromatica correlativa (processo questo concettualmente simile all’interpretazione di una cartina di tornasole).
Quando si compie il processo di laminazione di dry film su una struttura composita o su fotopolimero e di un film di poliestere su un rivestimento metallico dielettrico, la possibilità che il fotoresist subisca delle grinze o delle bolle è sempre presente. Controllando con attenzione la magnitudine della pressione e la distribuzione della stessa nei rulli di laminazione con film indicatori di pressione, i difetti provocati da grinze possono essere ridotti in modo sensibile.
Rulli pressori troppo tesi o eccessivamente laschi possono portare a rulli disallineati e rulli pressori imperfetti, motivi principali questi di corrugamenti intermittenti.
La forza impressa sul resist non viene misurata direttamente. Un sensore di pressione misura la pressione esercitata sui cilindri pneumatici che chiudono i rulli di laminatura. La forza esercitata sul resist dipende dal progetto del sistema di caricamento del rullo, tenendo in considerazione I’area dei cilindri e il leveraggio meccanico.
Dato che la forza viene esercitata sul resist mediante una copertura elastomerica del rullo, questa viene distribuita come pressione (forza per unità d’area) che dipende dalla larghezza, mentre la larghezza del rullo pressore è influenzata dalla forza complessiva applicata, dal diametro del rullo, dallo spessore e dalla durezza della copertura. La pressione sull’area varia da zero sui bordi a determinati picchi di pressione al centro del rullo pressore, là dove la copertura del rullo viene compressa con maggiore intensità.
Fig. 1 – Il film Pressurex® rivela la magnitudine di pressione del rullo pressore nella pressa di laminazione
La media di questo profilo di pressione (detta grossolanamente parabola) è di circa 2/3 del picco di pressione. Quando ci si riferisce alla pressione del rullo pressore si parla normalmente di "pressione media" invece che di "pressione di picco", ciò perché è più semplice determinarla.
Per semplificare le cose, comunque.si parlerà di forze sul rullo pressore in termini di forza per unità di lunghezza della larghezza della scheda (libbre per pollice o chilogrammi per centimetro), ignorando la reale larghezza del footprint. Questo test pud essere inoltre condotto quando sia presente fra i rulli un resist laminato con rivestimento in rame, specialmente con schede dotate di particolare spessore e il test può misurare gli effetti dei cosiddetti rulli a conformazione crown² per contrastare la flessione e che porti a un profilo di pressione uniforme lungo il pannello (si veda quanto segue). II problema della flessione del rullo viene illustrato in Fig. 2.
Fig. 2 – Illustrazione di flessione del rullo (visualizzazione esagerata)
FLESSIONE DEI RULLI IN FASE Dl LAMINAZIONE
La flessione del rullo può essere più o meno trascurabile e può condizionare la qualità della laminazione a causa di una notevole varietà di parametri. Laminatori a caldo che lavorano a pressioni relativamente modeste e che presentano rulli di grandi dimensioni sono meno soggetti al problema della flessione.
L’incurvatura dei rulli interessa più la laminazione degli strati esterni della scheda che di quelli interni, perché lo spessore di una scheda multistrato è grande abbastanza da determinare una flessione del rullo. Schede sottili o pannelli permettono al rullo di toccare entrambe le facce dell’elemento, riducendo cosi la tendenza alla flessione. II modello suggerisce che lo spessore complessivo del core dielettrico, più il rame, più lo spessore del resist debba essere maggiore di 22 mil (550 micron) prima che venga rilevata una flessione del rullo.
Quando questo avviene, il centro del pannello viene laminato a una pressione diversa rispetto ai bordi, il che determina una maggiore presenza di circuiti aperti e di difetti dish-down che sarà notata nelle operazioni di stampa e di etching lungo il centro del pannello e nella direzione di uscita della scheda dalla macchina. Per misurare il risultato della deposizione su una scheda di resist a una maggiore pressione viene usato un sistema AOI che testa i difetti del circuito che siano associati a un risultato insufficiente di deposizione del resist, quali "circuiti aperti", pizzicamenti (nick), dish-down e linee assottigliate su schede di test con pressioni di 4 e 7 Bar con un laminatore automatico di fogli ASL-24 (vedi Tab. 1).
Tabella 1 – Effetto della pressione e del profilo del rullo in relazione ai difetti presentati
I due valori di pressione corrispondono rispettivamente a forze di 36 e di 62 libbre per pollice. A una pressione maggiore i difetti sono ridotti del 79% rispetto a un livello di pressione più basso. Mentre questo porta a una riduzione importante dei difetti, è comunque difficile sfruttare una pressione maggiore perché la flessione dei dei rulli di laminazione viene indotta proprio da pressioni maggiori.
Questa flessione dei rulli ha luogo a causa di un irregolare footprint sul resist: il footprint è ridotto al centro del rullo e più largo sui bordi. Ciò significa che la pressione al centro del resist è inferiore rispetto a quella sui bordi. I produttori di sistemi di laminazione conoscono il fenomeno e provano a creare rulli che siano molto più robusti. Una flessione residua può essere compensata mediante I’utilizzo di rulli in configurazione "crown".²
Un rullo a effetto crown possiede un rivestimento di gomma che è più spesso al centro di quanto non lo sia ai bordi, con un cambiamento graduale dello spessore che lo porta a presentare un profilo curvato. In questo caso è possibile trovare un corretto valore di crown per l’ASL-24, cioè entro i 3-4 mil (75-100 micron).
Le Figg. 3 e 4 illustrano dei footprint causati da un rullo flesso e da un rullo a effetto crown.
Fig. 3 – Profilo di rullo pressore con rulli standar
Fig. 4 – Profilo di rullo pressore con rulli a effetto crown
La Tab. 1 mostra come I’effetto di crown riduca il conto del difetti del sistema circuitale sia in presenza di bassa pressione, sia in presenza di alta.
Il caso migliore è quello eseguito con alta pressione e con rulli dotati di un certo valore di crown. Fornitori di gomma come ad esempio la Robinson Rubber e I’Abba Rubber International inc. hanno nel loro catalogo rulli a effetto crown.
La Fig. 5 illustra la rappresentazione dei "circuiti aperti" a seconda dei diversi valori di pressione e dei diversi rulli utilizzati. L’effetto benefico delle più alte pressioni è evidente dalla figura. Inoltre, in caso di rulli flessi, è possibile vedere la grande abbondanza di "circuiti aperti" nel centra della scheda lungo la direzione di moto della macchina, là dove la pressione è più bassa a causa della flessione del rullo.
Fig. 5 – Difetti di "circuiti aperti" in funzione dei valori di pressione e dei profili dei rulli
In relazione alla massimizzazione del carico applicato sui rulli di pressione, la progettazione del sistema rappresenta un fattore limitante.
La robustezza dei rulli e il meccanismo di caricamento del rullo limitano generalmente il carico, sebbene la pressione pneumatica disponibile possa rappresentare un vincolo in certe aree.
La forza disponibile può essere concentrata su un footprint particolarmente ridotto, riducendo il diametro del rullo e lo spessore del rivestimento, anche se ciò esaspera i problemi di robustezza e di flessione.
GRINZE DI LAMINAZIONE COLLEGATE DIRETTAMENTE O INDIRETTAMENTE A PRESSIONI TROPPO ELEVATE O INSUFFICIENTI
Bisognerebbe tenere in considerazione che un laminatore oppurtunamente allineato e correttamente manutenuto rappresenta il primo passo per ottenere una laminazione priva di grinze (vedi Fig. 6).
Fig. 6 – Laminatore allineato correttamente
Molti dei motivi che contribuiscono alla creazione di grinze possono essere evitati se il laminatore viene adeguatamente allineato e manutenuto.
La Fig. 7 mostra che le grinze di laminazione puntano in una specifica direzione. Le cause principali possono essere imputate alla chiusura dei due rulli prima sul lato destro e, successivamente, su quello sinistro, oppure a causa di una forza che sia maggiore sulla parte destra rispetto alla sinistra.
Fig. 7 – Grinze di laminazione (Possibili cause:chiusura del rullo di laminazione sul lato destro primache sul sinistro; forza maggiore sul lato destro)
Una regola generale è che le grinze, prodotte con un laminatore manutenuto in modo regolare, sono un problema solo in caso di resist laminato di grandi dimensioni (>510 mm; >20") o nel caso in cui la lamina sia estremamente sottile (<0,2 mm; <0,008").
FLESSIONE DEL RULLO
I rulli di laminazione si flettono quando sono soggetti a carichi di laminazione. La flessione è causa di maggiore velocità di processo sui lati del pannello piuttosto che nel centro. Mentre normalmente ciò non determina effetti sui pannelli, a parte nel caso di laminazioni particolarmente sottili, ciò può portare in altri casi a un movimento del resist dai bordi verso il centro, provocando con ciò delle grinze in fase di laminazione. Se la compressione dei rulli è abbastanza alta da stirare le grinze nel periodo di tempo in cui il film viene trattenuto dalla barra di vuoto, le grinze non appariranno se non alla fine estrema del foglio, quando il film viene rilasciato dalla barra.
A questo punto non ci sono trattenimenti del bordo di trascinamento, pertanto gli ultimi centimetri si ammasseranno e quindi tenderanno a raggrinzirsi. Frequentemente ha luogo il cosiddetto effetto "code di cometa" sui fori di attrezzatura, causato da una combinazione di flessione del rullo e una forza di trazione insufficiente sul bordo terminale del resist.
PRESSIONI INADEGUATE DEL CILINDRO PNEUMATICO (PRESSIONI DI SERRAGGIO)
Le pressioni di serraggio (si tratta dei cilindri pneumatici che chiudono i rulli) devono essere regolate per una laminazione priva di grinze.
Queste possono essere una delle maggiori cause della presenza di estese grinze, soprattutto nel centro del pannello, e che si estendono secondo un andamento inverso rispetto a quello della direzione della laminatura e con un angolo contenuto.
Gli strumenti di misura disponibili sulla macchina non sono sempre gli indicatori più affidabili per valutare gli attuali valori di pressione. È sempre raccomandabile pertanto un controllo periodico di pressione indipendente.
GRINZE POST LAMINAZIONE
Questi tipi di grinze appaiono dopo la laminazione e honno una direzione coincidente con quella del movimento delta macchina (vedi Fig. 8).
Fig. 8 – Grinze post laminazione (rappresentazione esagerata)
Le grinze post laminazione possono essere determinate da una numerosa serie di cause, una delle quali può essere una pressione di laminazione eccessiva.
Le grinze post laminazione sono causate dal calore e dalle sollecitazioni a cui viene sottoposta la base di poliestere. Mentre la necessità di un buon risultato di deposizione del resist richiede una pressione di laminazione la più alta possibile, questo valore di pressione può andare ad assommarsi alle sollecitazioni esercitate sulla sua base.
Se ci si trova in presenza di un problema di grinze post laminazione, sarebbe meglio utilizzare due diversi rulli pressori a pressione e temperatura media, piuttosto che uno solo ad alta temperatura e ad alta pressione. Il secondo rullo pressore dovrebbe essere collocato immediatamente dopo il primo per minimizzare le perdite di calore fra i rulli stessi. Si noti che tale soluzione è più comoda in presenza di pannelli multistrato piuttosto che in caso di laminazione degli strati interni.
In conclusione, mantenere una corretta ed uniforme pressione lungo il rullo di laminazione a caldo, ad esempio mediante I’uso di un film sensibile indicatore di pressione, costituisce una vantaggiosa tecnica di garanzia di qualità per la localizzaizone e la correzione di disallineamenti del rullo, per un’insufficiente o troppo alta pressione che possa portare a un insufficiente risultato nella deposizione del resist e/o a grinze di laminazione del dry film che possano portare a loro volta a consistenti perdite produttive.
Autori:
Jeffrey G. Stark è presidente di Sensor Product Inc.,
Karl H. Dietz è autore di diversi saggi di tipo tecnico.
Titolo originale:Wrinkle Containment and Pressure Uniformity Control for Dry Film Resist Lamination
NOTE
- Edward Hagan,"The Role of Dry-Film Lamination in the Making of Ultra-Fine Pitch PC Boards",Technical Paper S12-4, Proceedings, Printed Circuits Expo ’98, Long Beach, CA, 26-30 aprile 1998;
- E. F. Hagan,"Using Crowned Rolls to Compensate for Roll Bending", in Technical Bulletin TB-9739 Rev. 1.0 (7/97), DuPont Photopolymer & Electronic Materials;
- Edward F. Hagan,"Effects of Lamination Parameters on Dry Film Photoresist Conformation", in Technical Paper F9, Proceedings, IPC Works ‘96, 19-25 ottobre 1996, Naples, FL;
- Karl H. Dietz,"Fine Lines in High Yields, (Part XXVIII): Advances in Hot Roll Lamination of Dry Film Photoresist (Part A)", in CircuiTree Magazine, dicembre 1997, p. 60;
- Karl H. Dietz, "Fine Lines in High Yields, (Part XXIX): Advances in Hot Roll Lamination of Dry Film Photoresist (Part B)", in CircuiTree Magazine, gennaio 1998, p. 18;
- E. Hagan e K. Dietz,"Dry Film Lamination Process Effects of Lamination Parameters on Wrinkling and Dimensional Properties of Dry Film and Copper-Clad Laminate", in Technical PaperFilm S05-2, Proceedings, IPC Printed Circuit Expo ’99, 14-18 marzo 1999, Long Beach, CA;
- Karl. H. Dietz e Edward F. Hagan,"The Process of Dry Film Lamination (Part I)", in PC Fab, settembre 1999, Vol. 22, No. 9, p. 42;
- Karl. H. Dietz e Edward F. Hagan,"The Process of Dry Film Lamination (Part II)", in PC Fab, ottobre 1999, Vol. 22, No. 10, p. 38;
- Karl H. Dietz, "Fine Lines in High Yields, (Part CXXXV): The Effects of Lamination Roll Mechanics on Conformation", in CircuiTree Magazine, dicembre 2006, p. 64;
- Pressurex® Measurement System, Sensor Products Inc., 300 Madison Avenue, Madison, NJ 07940, USA (https://www.sensorprod.com/pcb).