Article: European Tool & Mould Making
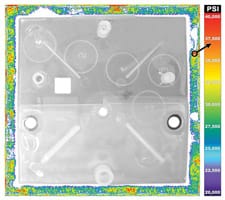
Pressure distribution along the parting line of a mould.
Thin, flexible Mylar-based Pressurex® sensor film from Sensor Products Inc. instantly captures and permanently records pressure distribution and magnitude between any two mating or contacting surfaces. Thus, it is ideal for ensuring proper parting line mating and alignment in injection moulding. After being clamped up and placed around he mould’s parting line, Pressurex reveals whether pressure is evenly distributed.
The film, which reveals pressure from 2 to 43,200 psi 0.14–3,000 kg/cm²), is designed to be a superior alternative to the use of bluing agents. It is available in eight different pressure ranges, with medium- and high-pressure ranges being those most commonly used for injection moulding applications.
When placed between two contacting surfaces, Pressurex® film instantaneously and permanently changes colour in direct proportion to the actual pressure applied. Precise pressure magnitude is easily determined through comparison of the resulting colour intensity with a colour correlation chart. No training or instrumentation is required; the only requirement is to take care in placing the Pressurex® properly in order to prevent parting line damage.
Physically similar to ordinary paper, Pressurex®, which is 4 or 8 mils thick, conforms to curved surfaces. It comes in sheets or rolls that can be cut to size. The film’s nominal operating temperature is 41°–95°F (5°–35°C), which is suitable for testing metal moulds, but it has been used at temperatures exceeding 300°F (149°C) for brief periods when paired with Sensor Products’ TemprX® insulating film.
Pressurex® film has application in injection, injectionblow, injection-compression, metal-injection, gas-assist, and water-assist moulding, as well as any other moulding process in which mating metal surfaces are an issue.