Article: Bodo’s Power Systems
Many of SB Electronics’ radial lead products are designed to take up the minimum amount of space on printed circuit boards. This is often down by flattening the round capacitor’s profile by pressing them between aluminum plates. By Arlene Gleicher, Sensor Products Inc. and David Bryan, SB Electronics
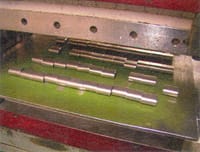
Figure 1: SB Electronics’ capacitors after being pressed
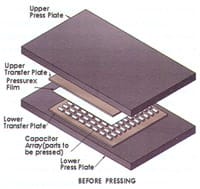
Figure 2: Before Pressing
As an innovator of film capacitor technology, SB Electronics designs and manufactures products that are on the cutting edge of today’s demanding electronics applications. To maintain continuous improvements of its manufacturing processes, David Bryan, Manufacturing Engineering Manager for SB Electronics, recently specified Pressurex®, a tactile surface pressure indicating sensor film from Sensor Products Inc. Many of SB Electronics‘ radial lead products are designed to take up the minimum amount of space on printed circuit boards. This is often done by flattening the round capacitor’s profile by pressing them between aluminum plates. A higher then expected scrap rate lad the quality department to contact engineering to troubleshoot and improve the process. Engineering, in turn, contacted Sensor Products Inc.
After histograms indicated that some of the tighter tolerance parts (± 1% capacitance) were going out of spec during out pressing operation, and making some initial dimensional measurements using conventional measuring equipment (calipers and micrometers), SB Electronics wanted a better was to determine exacty what was happening with the surface pressure during this process.
We ordered Pressurex®, a this sensor film that instantly captures and permanenty records pressure distribution and magnitude between contacting or mating surfaces. The film messures pressure from 2 – 43,000 PSI (o.14 – 3,000 kg/cm²). For his test, Bryan specified “super Low,” which measures pressure from 70 – 350 PSI ( 5 – 25kg/cm²).
We inserted a sheet of Pressurex® on top of the capacitors and between the press plates during a products run.
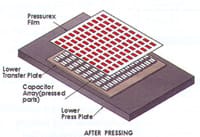
Figure 3: After Pressing
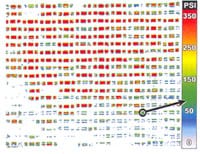
Figure 4: Pressurex® film revealed the uneven distribution of pressure across the press plates. (Image by Topaq® Analysis System.)
After the pressing operation, when we examined Pressurex®, the film had changed different intensities of color, with the color change directly proportional to the actual pressure applied. SB Electronics was able to determine the precise pressure magnitude by comparing the color intensity to a color correlation chart (conceptually similar to interpreting Litmus paper). We could visually inspect Pressurex and prove the press plates weren’t flat and were causing uneven pressure distribution.
Stimulated by this discovery, we wanted to statistically analyze the surface pressure further. We asked Sensor Products to use their Topaq® Image Analysis System, which consists of a Windows-based software and scanner, specifically calibrated to read and further interpret the film. Interpreted image are accompanied by a wealth or graphical and statistical data that are extremely valuable for contact pressure tests. With Topaq® small and problematic areas can be carefully scrutinized, as well as the entire interfacial surface.