Jiayu Wu, Hong Yuan, Xin Li
Abstract
Mechanical interaction behavior between human body and mattress is one of the crucial physical factors affecting the sleep comfort and quality. This paper proposes a novel method for sleep (dis)comfort level assessment in a supine posture without interfering with sleep in an attempt to improve mattress design. Three-dimensional (3D) back surface model is constructed by scanning human body in an upright standing position. Based on the mechanical property of mattress and body pressure distribution measured by Tactilus system, finite element (FE) models are established to numerically calculate mattress upper surface indentation. Finally, Pearson correlation coefficient similarity measure is used to evaluate sleep (dis)comfort by compared back surface with mattress upper surface indentation. The experimental process is validated with two distinct types of mattress, namely palm fiber mattress and latex foam/palm fiber mattress. Results show that all the participants feel more comfortable when lying on latex foam/palm fiber mattress, which are in excellent agreement with the results obtained by body pressure distribution and spinal alignment.
1. Introduction
Sleep, like nutrition and physical activity, is a crucial determinant of physiological needs (Dickerson et al., 2016; Duncan et al., 2016). Rechtschaffen et al. (1983) demonstrated that sleep is as necessary as food for bodily survival. However, the Institute of Medicine claimed that poor sleep has become a major public health issue (Colten and Altevogt, 2006). The Centers for Disease Control and Prevention (2014) reported that 7–19% of Americans never got sufficient sleep. Recent data indicated that 28% of Americans suffered from insufficient sleep on most nights, and only 31% of Americans consistently got sufficient sleep (McKnight-Eily et al., 2009). In mainland China, the survey showed that the residents with poor quality of sleep accounted for 22.4% (Chen et al., 2004), and poor sleep quality among college students reached up to 30% (Yang et al., 2011). In fact, the quality of sleep is affected by some ergonomic factors, including physical, physiological and psychological ergonomic parameters (Haex, 2004). Bed systems (i.e. mattress and supporting structure) are not only related to sleep quality, but also associated with the appearance of backache (Denninger et al., 2011; DeVocht et al., 2006; Kovacs et al., 2003; Verhaert et al., 2012) and pressure ulcer (Shelton et al., 1998). Epidemiological studies from all over the world reported that a lifetime prevalence rate of low back pain ranged from 49% to 80% (Verhaert et al., 2013). According to the literature (Bours et al., 2002; Lahmann et al., 2005), prevalence rates of pressure ulcer in Netherlands and Germany reached up to 23.1% and 7.3%–13.9%, respectively. Hence sleep comfort has become a primary factor in the purchase of mattress. From another perspective, mattress manufacturers have to innovate their mattress design to stay competitive.
There are many objective parameters relating to subjective parameter of sleep (dis)comfort. Among various objective parameters, body pressure distribution and spinal alignment are considered as the critical factors with a substantial impact on sleep comfort and quality. Parameters within the pressure distribution closely correlated to sleep comfort are the maximum pressure (DeVocht et al., 2006; Shelton et al., 1998; Zenk et al., 2008), the average pressure (Verver, 2004), the maximum pressure gradient (Zenk et al., 2008), the average pressure gradient, total pressure and total contact area (Verver, 2004) between human body and mattress. In addition, Shelton et al. (1998) defined a Pressure Index Pindex to evaluate the closeness of a surface to that of the simplistic ideal surface with a homogeneously distributed pressure of 10 mmHg across the entire interface area.
The main function of mattress is to provide proper support to the body, and allow the vertebral column recovering in its natural shape during sleep (LeBlanc et al., 1994; Nachemson and Elfstrom, 1970). In order to quantify the sleep comfort and set standards for mattress design, ergonomically focused definition is needed. Establishing quantifiable sleep comfort requires analysis of mechanical interaction behavior between human body and mattress in the process of sleeping. Several studies have proposed methods to evaluate sleep comfort, especially for lateral sleep position. Computed tomography (CT) scanning of volunteers were taken in a lateral sleep position on firm and soft mattresses in an attempt to record a training set of point distribution models on the back for evaluating the spinal alignment (Huysmans et al., 2006). Practically, spinal alignment can be observed clearly from X rays and CT scan, but they will be excluded by researchers for ethical reasons. Leilnahari et al. (2011) obtained the spinal alignment in a lateral sleep position on soft and firm mattress by using the optical tracking method. Denninger et al. (2011) compared the spine curvature in a lateral sleep posture with that in an upright standing posture, which is recorded by an infrared optical Optorak 3020 system. Verhaert et al. (2011, 2012) extracted medio-lateral body contours by using the Ik lo system, and modeled body shape with 28 degrees of freedom to evaluate spinal alignment in a variety of sleep posture. Obviously, optical methods are available for measuring the spinal alignment in a lateral sleep posture.
In order to overcome the shortage of the estimation of spinal alignment in a supine posture by optical methods, this study proposes a novel method to evaluate sleep comfort without interfering with sleep by using similarity measure theory. As spine is in its natural shape during upright standing, back surface configuration of this posture is considered as the most comfortable shape. Sleep (dis)comfort level can be derived in the comparison of back surface configuration and the mattress upper surface indentation, which is calculated from finite element model under body weight pressure. A validation research is performed to investigate the mechanical interaction between human body and mattress.
2. Materials and methods
2.1. Sleep comfort assessment process
Sleeping is a mechanical interaction process between human body and mattress. Mechanical property of mattress will crucially affect sleep quality and body comfort. If the mattress is too soft, the intervertebral discs will be compressed at the anterior side while soft tissues (e.g. muscle, ligaments) will be under tension at the posterior side. If the mattress is too firm, the lumbar part of the vertebral column will not smoothen immediately when lying down, and no contact will be made between the lumbar part of the back and the mattress (Haex, 2004). In order to design the mattress suitable for individual demand, human body (dis)comfort should be known clearly during lying on the mattress. Finally, an assessment method is put forward to evaluate the sleep (dis)comfort after comprehensive consideration of spinal alignment and body pressure, as shown in Fig. 1.
Fig. 1. Sleep (dis)comfort assessment process.
Back surface in an upright standing posture is referred to as the most comfortable position. Similarity measure is applied to evaluate sleep comfort level. This method can be employed to tune a mattress for a specific body shape by compared back surface model with mattress upper surface indentation calculated by using FE model.
2.2. Participants
A total of 17 people participated in the research, who were interviewed to determine if they were in good health with no backache in the last ten days, and didn’t suffer any spinal deformations, which ensured that every participant could maintain in an upright standing posture for 3D body scanner to get data of body size. Characteristics of the 17 participants included in the research were: Males, n=13; females, n=4; age 34.9 ± SD 9.7 years, weight 63.7 ± SD 13.9 kg, height 167.8 ± SD 8.8 cm, BMI 22.1 ± SD 2.8 kg/m2.
2.3. Mattress
2.3.1. Palm fiber mattress
In recent years, people have paid more attention to natural fiber composite materials for the sake of environment protection, energy saving and sustainable development. Palm fiber, with good elasticity, high toughness, anti-corrosion and anti-month characteristics, is raw materials for manufacture of natural fiber mattress. The mattress is mainly made of palm fiber, stuck together by rubber cement to form elastic structure as the mattress core that is wrapped by some fabric. Palm fiber plays the role of mechanical springs, but it is superior to the discrete spring for providing human body consecutive support. Palm fiber mattress is a porous structure that enables itself to breathe. This feature allows the release of body heat and moisture, keeping the sleep surface comfortable. The experimental mattress (Fig. 2) is provided by Guizhou Nature Technology Co., Ltd, Guiyang, China.
Fig. 2. Palm fiber mattress.
2.3.2. Latex foam mattress
Latex is also natural, biodegradable material, which is from rubber tree. In general, latex foam materials are used to manufacture highquality mattress. The soft latex foam can contour to body’s curves during sleep, and provide consecutive support. As latex foam contours to sleeper’s body, body weight pressure can be spread over the entire sleep surface. Sleeper’s body weight can be transferred over more of the sleeping surface areas and minimize pressure concentration due to the contouring effecting. Pressure concentration can result in uncomfortable feeling and cause sleeper to toss and turn more frequently.
2.3.3. Experiments of mattress test specimens
Three palm fiber test specimens are cubes with a rectangular cross section of 320mm by 160mm and a height of 120 mm, which were randomly taken from a palm fiber mattress. Three latex foam test specimens, with a circular cross section of diameter 100mm and a height of 100 mm, were cut from a latex foam mattress. The mechanical behavior of foam is greatly influenced by the temperature and humidity (Schrodt et al., 2005). Thus all tests specimens were kept at constant climatic conditions (24 °C temperature and 57% humidity) from 24 h before testing to the end of experiment. Mechanical interaction between mattress and body in a supine sleep position can be seen as a quasi-static loading process, so the loading speed was slow in the experiment. Palm fiber test specimens were compressed by MTS 831.10 Elastomer Test System (MTS Systems Corp., Eden Prairie, MN, USA). Loading rate remained 0.4 mm/s until the contact force reached 1 N. Latex foam test specimens were loaded in load-step mode with the constant rate of displacement 0.2 mm/s. Normal compressive stress and strain were recorded during the steady-state compression. The compressive stresses and strains of palm fiber and latex foam obtained from the experiments are shown in Fig. 3.
Fig. 3. Experimental data and fitting curve of stress-strain relation: (a) Palm fiber; (b) Latex
foam.
2.3.4. Mechanical behavior of mattresses
According to sleeping experiences, the strain in the thickness direction is normally less than 30%. Young’s modulus for each specimen in the thickness direction compression is derived from linear fitting of stress-strain data by linear regression method. Fig. 3a shows the regression curve of specimens and the corresponding regression parameters for each specimen are listed in Table 1.
Latex foam is considered as a compressible hyperelastic material, which can be characterized by strain energy function. Based on Ogden’s investigation, an isotropic form of strain energy function for the compressible materials is expressed as (Berezvai and Kossa, 2017; Storåkers, 1986):

(1)
where n denotes the order of the hyperelastic model, λ1, λ2 and λ3 are the three principle stretches, αi and βi are the constitutive parameters, μi are the stresses and J=λ1λ2λ3 is the relative volume.
The nominal stresses si yield from strain energy function Eq. (1), which can be expressed as follows,
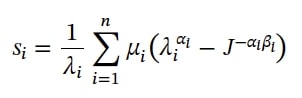
(2)
For uniaxial compression, n = 1 and λ2 = λ3 = λ1-β/(2β+1) The uniaxial normal compressive stress s can be calculated in terms of Eq. (2), as follows,
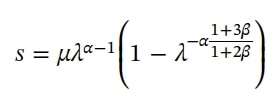
(3)
The constitutive relation of latex foam is modeled with Ogden strain energy function by using finite element software ANSYS (ANSYS Inc., Canonsburg, Pennsylvania, USA). Consequently, the parameters α, β, λ are approximately obtained by an iterative nonlinear regression on experimental data (see Table 1). The regression curve of specimens is shown in Fig. 3b.
It can be seen from Fig. 3 that, the fitted curves are rather good, particularly for the latex foam. This is demonstrated by the correlation coefficient Rcorr for the palm fiber and latex foam, respectively. Moreover, Fig. 3 indicates that latex foam specimen is softer than palm fiber specimen.
2.4. 3D body scanning
In recent years, 3D body scanning has been widely applied in industrial research. Some research achievements are made for practical project applications, such as costume designing (Lu et al., 2014; Park and Langseth-Schmidt, 2016), footwear design (Ma and Luximon, 2014), foot motion (Van den Herrewegen et al., 2014) and computation of breast ptosis (Li et al., 2016), etc. 3D body scanning, a technology for capture of spatial data in three dimensions, provides a novel way to construct three-dimensional entity with irregular shape by reverse modeling method. The 3D scanner has the capacity to digitize and characterize the surface of human body rapidly by collecting dense coordinate data points from the object surface as a point cloud, with high precision and no damage and without contact with body. With the resulting point cloud data, body surface can be reconstructed by using a specifically developed triangulated irregular network mesh (Jiang et al., 2016; Son and Kim, 2016; Wang and Feng, 2016).
3D body scanning system (Fig. 4a), adopted for this study, uses twelve scanning apparatuses to digitize of approximately 500,000 spatial data points in each scan. The participants, only dressed in their underwear, were asked to maintain for more than 7 s in an upright standing posture with the two upper limbs open slightly inside the scanner. Once the participant was ready, scanning began and the process lasted only 7 s for obtaining the point cloud of participants’ body surface.
The software package Geomagic Studio (Geomagic Corp., Morrisville, NC, USA) is available for reverse engineering and scanbased design. It can deliver robust 3D scan data into polygon and surface models for CAD-based design. After a scan has been taken, Geomagic Studio can be applied to construct triangular surface mesh from point cloud, and then established curved surface after complex processing, as shown in Fig. 4b–d. Back surface model is sliced from 3D body model in Subsection 3.3.
Fig. 4. (a) 3D body scanning system and 3D body model of (b) Point cloud, (c) Triangulated irregular network mesh, (d) Curved surface.
2.5. Body pressure measurements
Tactilus system (Sensor Products Inc. Madison, NJ, USA) allows the user to capture and record pressure conditions occurring in between any two contacting or impacting surfaces in real time. Piezoresistive fabric materials are used in Tactilus system. The resistance of these materials changes when pressure is applied on them. These fabric materials, with 16 Hz sample frequency, are very sensitive to a slight pressure change. In addition, these materials are elastic which can conform well with different curvatures of human body. 27 X 64 pieces of individual piezoresistive fabric sensor cell, whose size is 2.8148 cm X 2.8906 cm, constitute the Tactilus system with measuring areas of 76 cm by 185 cm. The 2.5mm thick Tactilus sensor is actually placed at the contact interface where it records and assimilates both pressure distribution and pressure magnitude on Windows® based computer. Body pressure map can be plotted from discrete data measured by each sensor by two-dimensional linear interpolation method.
Two distinct types of mattress are respectively carried out to measure body pressure. One is 16 cm thick mattress core simply made of palm fiber; the other has two-layer mattress cores: the upper-layer is 4 cm thick latex foam, and the lower layer is palm fiber with thickness 12 cm. The sensor pad (mat) was placed on the mattress flatly. Each participant lay on the mattress, and his/her head is raised by a soft latex pillow so that the coronal plane of the head is similar to upright standing position. Participant lay upper limbs on the sides of their body, and maintained in a supine posture with regular breath for 1 min until the body pressure displayed on the computer screen remained relative stable. The experimental data of body pressure start to record at this moment.
When lying in a supine posture, body pressure distribution for palm fiber (PF) and latex form/palm fiber (LF/PF) mattress is plotted by using MATLAB (MathWorks Inc., Natick, MA, USA), as shown in Fig. 5. Fig. 5 depicts that material properties of the mattress have a great influence on body pressure distribution. Generally, the maximum pressure appears in the buttocks area. The maximum body pressure of PF mattress is larger than that of LF/PF mattress. On the contrary, contact area of PF and LF/PF mattress has an opposite tendency. Furthermore, we can deduce from Fig. 5b–c that the average pressure gradient of PF mattress is larger than that of LF/PF mattress.
The maximum pressure, contact area and total pressure in thoracic, lumbar and buttock regions of PF (LF/PF) mattress are listed in Table 2. In accordance with Table 2, we can conclude that the maximum pressure in thoracic and buttock regions of PF mattress is larger than that of LF/PF mattress. In contrast, contact area in thoracic and buttock regions of PF mattress is small than that of LF/PF mattress. However, the maximum pressure and contact area of lumbar do not follow the above law, as lumbar vertebra can move freely, which is different from thoracic vertebra and sacrum structured by rib and pelvis, respectively. Additionally, the maximum pressure in lumbar region is much smaller than that in thoracic and buttock regions. Thus, parameters of the maximum pressure, contact area and total pressure can be applicable to assess the sleep comfort in thoracic and buttock regions rather than lumbar region, which is critically affected by spinal alignment.
Fig. 5. (a) A supine sleeping posture, and body pressure distribution of (b) PF mattress, (c) LF/PF mattress.
2.6. Mattress indentation calculated by FE model
Assessment of sleep comfort requires not only information on the participant’s anthropometrics, but also information on the indentation of the mattress resulting from the participant’s body pressure. Numerous researchers assessed human body comfort using FE method. Verver (2004) established a 3D FE model of the bony structures and the soft tissues to analyze automotive seating comfort. Denninger et al. (2011) used ANSYS to model human body as elliptical cylinders for custom mattress design. Vivid human body model in FE analysis is reasonable, whereas it is so tricky to identify mechanical properties of soft tissues, bony structures and connections between them. In the view of Kim et al. (2018), it is not necessary to establish three-dimensional body while analyzing car seat’s comfort functions. As the body pressure is measured by Tactilus system, FE model can be simplified as a mattress exposed to body pressure. Therefore, ANSYS FE simulations can be conducted to numerically calculate the mattress indentation in a supine sleep posture. PF mattress and LF/PF mattress are both modeled with the three-dimensional solid element SOLID185, which has hyperelasticity, large deflection, and large strain capabilities. Material parameters of mattresses are obtained from the mean value of Table 1. Displacement constraints are applied to the mattress lower surface. Body pressure measured by Tactilus system is applied to designated area of mattress upper surface. After FE calculation, indentation of mattress upper surface is shown in Fig. 6.
Fig. 6. Mattress upper surface indentation of (a) PF mattress, (b) LF/PF mattress.
Fig. 6 shows the mattress indentation, which has the largest value in the buttocks area, followed by the thoracic area. In general, the LF/PF mattress has larger indentation than the PF mattress for the same body parts. According to Figs. 5–6, mattress upper surface where body pressure is concentrated will sink deeply into the mattress.
3. Results and analysis
3.1. Similarity measure
The research of similarity has been overwhelmingly explored and widely used in various study fields, such as clustering criteria, classification statistics and retrieval problems, etc. Similarity measure is closely relevant to the distance measure, as the distance is defined as a quantitative degree of how far apart two objects are. There are many typical methods for similarity measure including Pearson correlation coefficient, cosine similarity measure, Euclidean distance, Tanimoto distance, and so on (Huang et al., 2016; Ray and Misra, 2016; Shin, 2016; Theodoridis and Koutroumbas, 2006). Pearson correlation coefficient measure can be expressed as

(4)
While analyzing gene expression data, Eisen et al. (1998) defined a related dissimilarity measure as
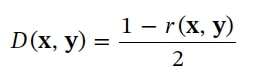
(5)
where D(x, y) ranges from 0 to 1.
3.2. Comfort assessment
The definition of comfort is so diverse in the literature (Vink and Hallbeck, 2012). It is very easy for a person to express whether the mattress is fine or not. However, it is hard to determine how or why the mattress is comfortable. To use objective parameters to describe subjective feeling of (dis)comfort is virtually impossible. That is just what researchers desire to achieve. In order to assess the sleep comfort, the most comfortable sleep position should be known clearly. Zenk et al. (2012) measured the pressure in the intervertebral disc L4-L5 and L5- S1, and demonstrated that the most comfortable position occurred while the pressure was minimum. According to the literature (Denninger et al., 2011; Haex, 2004; Verhaert et al., 2012), the spinal alignment in its natural shape during upright standing is considered as the most comfortable position. From the perspective of biomechanics, the stress between the intervertebral discs is mainly normal stress in an upright standing posture due to the gravity with respect to the craniocaudal direction. Assuming that the sleep posture is identical to an upright standing posture, the stress between the discs will approximate to zero. In addition, on account of the mechanical interaction between human body and mattress, the back and buttock suffer from large contact pressure, which will make sleeper feel uncomfortable. Taking into comprehensive consideration of various physical factors, spinal alignment and body pressure are the dominant factors affecting on the quality of sleep. Therefore, the sleep posture, the same as upright standing without contact pressure from mattress, can be defined as the most comfortable position. In other words, sleep comfort can be assessed by back surface deformation.
Human body comfort in a certain sleep posture can be evaluated by compared the back surface on a sleep system with the back surface during upright standing. The shape of back surface in an upright standing posture can be captured by 3D body scanner. However, it is difficult to measure the unobtrusive deformation of back surface in a supine sleep posture. Of course, back surface deformation can be calculated by constructing complicated human body FE model exposed to contact pressure, provided that the body structure of each sleeper and mechanical properties of human tissues are all known. In other words, sleep comfort can be evaluated by compared the indentation of the mattress with the back surface in an upright standing posture.
Measurement criterion of sleep comfort has been put forward above. Based on the theory of similarity measure, the shape of back surface from shoulders to buttocks and the deformation of mattress with the same zone are regarded as the vectors α and β, respectively. Compared α with β by Pearson correlation coefficient similarity measure, sleep comfort level (CL) can be expressed as
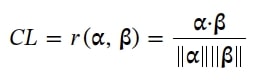
(6)
The value CL takes the range from −1 to 1. The larger the value CL is, the more comfortable the sleeper feels. The sleeper feels the most comfortable while CL = 1.
In the view of gene expression data analyzed by Eisen et al. (1998), sleep discomfort level (DL) can be expressed as
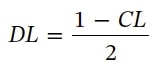
(7)
The bound of the value DL is from 0 to 1. It is clear that the discomfort feeling increases with the value DL. DL = 1 implies that the sleeper feels the most uncomfortable.
3.3. Experimental analysis
On the basis of Subsection 2.5, a generic model for evaluating sleep (dis)comfort has been developed, which should be constituted of four major regions: cervical, thoracic lumbar and buttock, as illustrated in Fig. 7a. Cervical region (dis)comfort during sleep is primarily associated with the configuration and mechanical properties of pillow. Hence sleep (dis)comfort, affected by the design of mattress, is basically related to thoracic, lumbar and buttock regions.
Fig. 7. (a) Vertebral column is divided into four regions; (b) Spinal alignment in natural standing posture and mattress upper surface indentation along the vertebral column direction; Extraction process of back surface, (c) 3D back model, (d) Back surface mesh, (e) Fitting back surface; (f) Indentation with the same zone of back surface.
According to skeletal anatomy of human body, sleep (dis)comfort of thoracic and buttock regions is mainly dependent on body pressure, yet spinal alignment may also cause sleep discomfort, especially in lumbar region. Spine shape is estimated by combining the measured mattress upper surface indentation and the anthropometric information incorporated in the modeled body shape. The distance between thoracic and lumbar, buttock and lumbar in sagittal axis direction are denoted by LT1, LB1, respectively; and the difference value of mattress upper surface indentation between thoracic and lumbar regions, buttock and lumbar regions are denoted by LT1, LB1, respectively; as shown in Fig. 7b. According to anthropometric information of 3D body model, we obtain that LT1 = 48.98 ± SD 19.34 mm, LB1 = 45.45 ± SD 3.33 mm. In addition, LB2 = 23.16 ± SD 2.25 mm, LT2 = 17.98 ± SD 1.75mm for PF mattress; and LB2 = 42.64 ± SD 2.12 mm, LT2 = 37.79 ± SD 1.89mm for LP/PF mattress, which are given by FE results. The difference between spinal alignment in a natural standing posture and mattress upper surface indentation (LT1 and LT2, LB1 and LB2) can be used to evaluate sleep comfort from spinal alignment, which can be expressed as

(8)
There is no doubt that larger values of LLT and LLB may lead to a higher level of sleep discomfort. Furthermore, the similarity between spinal alignment in a natural standing posture and mattress upper surface indentation is denoted by SA, which can be alternatively calculated by Pearson correlation coefficient.
3D back model is sliced from 3D human body model in an upright standing posture in the platform Workbench (ANSYS Inc., Canonsburg, Pennsylvania, USA) Geometry module (Fig. 7c). Mesh generation is implemented in Workbench Model module, from which 3D spatial data of back surface node are exported (Fig. 7d). The data are then used to construct the back surface configuration by using fitting in MATLAB, which is defined as the most comfortable position (Fig. 7e). For comparison with the most comfortable position conveniently, mattress upper surface indentation area is extracted as the same zone. Mattress upper surface indentation distribution from shoulder to buttock is depicted in Fig. 7f. Sleep (dis)comfort level can be easily obtained by compared Fig. 7e with Fig. 7f.
Assessment of sleep (dis)comfort level in a supine posture on PF and LF/PF mattresses are listed in Table 3. Based on the body pressure, the mean value of maximum pressure in thoracic and buttock regions of PF mattress is larger than that of LF/PF mattress. Conversely, contact area of PF mattress is smaller than that of LF/PF mattress. On the basis of spinal alignment, the values of LLT and LLB of PF mattress are larger than that of LF/PF mattress, which implies that LF/PF mattress can achieve higher comfort level. In contrast, the similarity of spinal alignment SA is larger for LF/PF mattress. After a comprehensive consideration, we propose a novel parameter to assess sleep comfort by compared back surface configuration in a natural standing posture with mattress upper surface indentation without interfering with sleep. Both body pressure distribution and spinal alignment (especially in the lumbar region) are considered in the study. Table 3 shows that the value CL of LF/PF mattress is a little bit larger than that of PF mattress, which indicates that the sleeper will feel more comfortable while sleeping on LF/PF mattress. Notably, the value of SA is generally larger than CL, as spinal alignment in thoracic and buttock regions remains almost unchanged for upright standing and supine posture. Hence CL value will be more reasonable. From the perspective of industrial design, a certain thickness of soft latex foam can help improve sleep comfort. Nevertheless, the values of SA and CL for both PF, LF/PF might not be statistically different at all, thus, we could conclude that PF mattress can meet the sleep comfort requirements.
4. Discussion
For the sake of better mattress design, the mechanical interaction behavior between human body and mattress should be known clearly, apart from the mechanical properties of mattress material. The purpose of this study is to put forward a measurement criterion of sleep comfort. Firstly, back surface in an upright standing posture is defined as the most comfortable mode, according to the literature (Denninger et al., 2011; Haex, 2004; Verhaert et al., 2012). Secondly, among various physical factors, spinal alignment and body pressure distribution are considered as the critical factors affecting on sleep comfort and sleep quality (Haex, 2004). The unobtrusive deformation of human body from shoulders to buttocks contains the fundamental information of spinal alignment and body pressure, which is difficult to measure during sleep. The aim of the present paper is not to accurately calculate the deformation of soft tissue (e.g. muscles, skin, ligaments and fat tissue) in a supine sleep postures, but to propose a straightforward model of mattress upper surface indentation to estimate back surface deformation without interfering with habitual sleep. Thirdly, comparing mattress upper surface indentation with back surface in an upright standing position, and introducing Pearson correlation coefficient, we can obtain sleep (dis)comfort level as a result of Eqs. (6) and (7).
Practically, some limitations exist in this study. First, mattress upper surface indentation can describe human body surface deformation under pressure to some extent, but differences exist between them, especially for firm mattress. A second limitation is that the experimental (dis)comfort level is the human feeling, which are now described by objective parameter. Actually, subjective assessment experiment should be made in an attempt to demonstrate experimental results. However, human feeling during sleep is affected by various factors, such as permeability of the mattress, the weather, the mood, etc. Additionally, comfortable feeling might be different for long-period sleep and short-period sleep on the same mattress. Therefore, future work will seek to improve the accuracy of the model by dealing with these limitations and considering more of the related physical factors.
This study, along with sleep posture and movement recognition (Liu et al., 2014), lays the foundation for intelligent mattress design, which can actively adjust mattress surface configuration according to the adopted sleep posture. With the development of 3D printing technology, intelligent algorithm and smart home, intelligent mattress will get thoroughly familiar with its master’s sleep habits through longperiod learning and training, and be designed and manufactured for private individuals in the coming future.
5. Conclusions
This study puts forward a novel method to evaluate sleep (dis) comfort, overcoming the shortage of optical measurement method in a supine posture. Back surface model in an upright standing posture, regarded as a vector α, is constructed with the help of 3D body scanning system. In accordance with the mechanical property of mattress material and body pressure distribution, mattress upper surface indentation from shoulder to buttock, regarded as a vector β, can be calculated by using FE model without interfering with sleep. Similarity of α and β by Pearson correlation coefficient method (Eq. (6)) is defined as comfort level (CL) for assessing sleep comfort.
Acknowledgments
The authors gratefully acknowledge the financial support provided by the National Natural Science Foundation of China (No. 11032005), the Major Project of Guizhou Province Department of Science and Technology (2014) 6024 and Academician Workstation of Guizhou Province Department of Science and Technology (2015) 4004.
References
- Berezvai, S., Kossa, A., 2017. Closed-form solution of the Ogden–Hill’s compressible hyperelastic model for ramp loading. Mech. Time-Dependent Mater. 21, 263–286.
- Bours, G.J., Halfens, R.J., Abu-Saad, H.H., Grol, R.T., 2002. Prevalence, prevention, and treatment of pressure ulcers: descriptive study in 89 institutions in The Netherlands. Res. Nurs. Health 25, 99–110.
- Chen, Y.L., Yang, X.J., Shi, C.F., 2004. Elementary study on sleep quality and influence factors for common population in xiamen, China. Strait Am. J. Prev. Med. 10, 4–6.
- Colten, H.R., Altevogt, B.M., 2006. Sleep Disorders and Sleep Deprivation: an Unmet Public Health Problem. National Academies Press, Washington, D.C.
- Denninger, M., Martel, F., Rancour, D., 2011. A single step process to design a custom mattress that relieves trunk shear forces. Int. J. Mech. Mater. Des. 7, 1–16.
- DeVocht, J.W., Wilder, D.G., Bandstra, E.R., Spratt, K.F., 2006. Biomechanical evaluation of four different mattresses. Appl. Ergon. 37, 297–304.
- Dickerson, S.S., Klingman, K.J., Jungquist, C.R., 2016. Common meanings of good and bad sleep in a healthy population sample. Sleep Health 2, 253–259.
- Duncan, D.T., Goedel, W.C., Mayer, K.H., Safren, S.A., Palamar, J.J., Hagen, D., Jean- Louis, G., 2016. Poor sleep health and its association with mental health, substance use, and condomless anal intercourse among gay, bisexual, and other men who have sex with men. Sleep Health 2 (4), 316–321.
- Eisen, M.B., Spellman, P.T., Brown, P.O., Botstein, D., 1998. Cluster analysis and display of genome-wide expression patterns. Proc. Natl. Acad. Sci. 95, 14863–14868.
- Haex, B., 2004. Back and Bed: Ergonomic Aspects of Sleeping. CRC Press, Boca Raton.
- Huang, X., Ghodsi, M., Hassani, H., 2016. A novel similarity measure based on eigenvalue distribution. Trans. A. Razmadze Math. Inst. 170 (3), 352–362.
- Huysmans, T., Haex, B., De Wilde, T., Van Audekercke, R., Vander Sloten, J., Van der Perre, G., 2006. A 3D active shape model for the evaluation of the alignment of the spine during sleeping. Gait Posture 24, 54–61.
- Jiang, Q., Feng, X., Gong, Y., Song, L., Ran, S., Cui, J., 2016. Reverse modelling of natural rock joints using 3D scanning and 3D printing. Comput. Geotech. 73, 210–220.
- Kim, D.Y., Bang, J.H., Lee, C.A., Kim, H.Y., Choi, K.Y., Lim, B.G., 2018. Numerical evaluation of time-dependent sagging for low density polyurethane foams to apply the long-term driving comfort on the seat cushion design. Int. J. Ind. Ergon. 64, 178–187.
- Kovacs, F.M., Abraira, V., Pena, A., Martin-Rodriguez, J.G., Sanchez-Vera, M., Ferrer, E., Ruano, D., Guillen, P., Gestoso, M., Muriel, A., 2003. Effect of firmness of mattress on chronic non-specific low-back pain: randomised, double-blind, controlled, multicentre trial. Lancet 362, 1599–1604.
- Lahmann, N.A., Halfens, R.J., Dassen, T., 2005. Prevalence of pressure ulcers in Germany. J. Clin. Nurs. 14, 165–172.
- LeBlanc, A.D., Evans, H.J., Schneider, V.S., Wendt III, R.E., Hedrick, T.D., 1994. Changes in intervertebral disc cross-sectional area with bed rest and space flight. Spine 19, 812–817.
- Leilnahari, K., Fatouraee, N., Khodalotfi, M., Sadeghein, M.A., Kashani, Y.A., 2011. Spine alignment in men during lateral sleep position: experimental study and modeling. Biomed. Eng. Online 10, 103.
- Li, D., Cheong, A., Reece, G.P., Crosby, M.A., Fingeret, M.C., Merchant, F.A., 2016. Computation of breast ptosis from 3D surface scans of the female torso. Comput. Biol. Med. 78, 18–28.
- Liu, J.J., Xu, W., Huang, M.C., Alshurafa, N., Sarrafzadeh, M., Raut, N., Yadegar, B., 2014. Sleep posture analysis using a dense pressure sensitive bedsheet. Pervasive Mob. Comput. 10, 34–50.
- Lu, Y., Song, G., Li, J., 2014. A novel approach for fit analysis of thermal protective clothing using three-dimensional body scanning. Appl. Ergon. 45, 1439–1446.
- Ma, X., Luximon, A., 2014. 3D foot prediction method for low cost scanning. Int. J. Ind. Ergon. 44, 866–873.
- McKnight-Eily, L., Liu, Y., Perry, G., Presley-Cantrell, L., Strine, T., Lu, H., Croft, J., 2009. Perceived insufficient rest or sleep among adults-United States, 2008 (Reprinted from MMWR, vol. 58, pg 1175–1179, 2009). JAMA, J. Am. Med. Assoc. 302 (23), 2532 (2009).
- Nachemson, A., Elfstrom, G., 1970. Intravital dynamic pressure measurements in lumbar discs. Scand. J. Rehabil. Med. 2, 1–40.
- Park, J., Langseth-Schmidt, K., 2016. Anthropometric fit evaluation of firefighters’ uniform pants: a sex comparison. Int. J. Ind. Ergon. 56, 1–8.
- Ray, S.S., Misra, S., 2016. A supervised weighted similarity measure for gene expressions using biological knowledge. Gene 595, 150–160.
- Rechtschaffen, A., Gilliland, M.A., Bergmann, B.M., Winter, J.B., 1983. Physiological correlates of prolonged sleep deprivation in rats. Science 221, 182–184.
- Schrodt, M., Benderoth, G., Kühhorn, A., Silber, G., 2005. Hyperelastic description of polymer soft foams at finite deformations. Tech. Mech. 25, 162–173.
- Shelton, F., Barnett, R., Meyer, E., 1998. Full-body interface pressure testing as a method for performance evaluation of clinical support surfaces. Appl. Ergon. 29, 491–497.
- Shin, K., 2016. An alternative approach to measure similarity between two deterministic transient signals. J. Sound Vib. 371, 434–445.
- Son, H., Kim, C., 2016. Automatic segmentation and 3D modeling of pipelines into constituent parts from laser-scan data of the built environment. Autom. ConStruct. 68, 203–211.
- Storåkers, B., 1986. On material representation and constitutive branching in finite compressible elasticity. J. Mech. Phys. Solid. 34, 125–145.
- The Centers for Disease Control and Prevention, 2014. Sleep and Sleep Disorders: Data and Statistics.
- Theodoridis, S., Koutroumbas, K., 2006. Pattern Pecognition, third ed. China Machine Press, Beijing.
- Van den Herrewegen, I., Cuppens, K., Broeckx, M., Barisch-Fritz, B., Vander Sloten, J., Leardini, A., Peeraer, L., 2014. Dynamic 3D scanning as a markerless method to calculate multi-segment foot kinematics during stance phase: methodology and first application. J. Biomech. 47, 2531–2539.
- Verhaert, V., Van Deun, D., Verbraecken, J., Vandekerckhove, M., Exadaktylos, V., Haex, B., Vander Sloten, J., 2013. Smart control of spinal alignment through active adjustment of mechanical bed properties during sleep. J. Ambient Intell. Smart Environ. 5, 369–380.
- Verhaert, V., Druyts, H., Deun, D.V., Exadaktylos, V., Verbraecken, J., Vandekerckhoved, M., Haex, B., Sloten, J.V., 2012. Estimating spine shape in lateral sleep positions using silhouette-derived body shape models. Int. J. Ind. Ergon. 42, 489–498.
- Verhaert, V., Haex, B., De Wilde, T., Berckmans, D., Verbraecken, J., De Valck, E., Vander Sloten, J., 2011. Ergonomics in bed design: the effect of spinal alignment on sleep parameters. Ergonomics 54, 169–178.
- Verver, M.M., 2004. Numerical Tools for Comfort Analyses of Automotive Seating. Technische Universiteit Eindhoven.
- Vink, P., Hallbeck, S., 2012. Editorial: comfort and discomfort studies demonstrate the need for a new model. Appl. Ergon. 43, 271–276.
- Wang, Y., Feng, H.Y., 2016. Effects of scanning orientation on outlier formation in 3D laser scanning of reflective surfaces. Optic Laser. Eng. 81, 35–45.
- Yang, Q., Wang, F., Hu, D., Xia, H., Zhang, J., Zhang, S., 2011. Sleep quality and its influencing factors in university students. J. Public Health Prev. Med. 22, 88–89 (In Chinese).
- Zenk, R., Franz, M., Bubb, H., 2008. Emocard–an approach to bring more emotion in the comfort concept. SAE Int. J. Passeng. Cars-Mech. Syst. 1, 775–782.
- Zenk, R., Franz, M., Bubb, H., Vink, P., 2012. Technical note: spine loading in automotive seating. Appl. Ergon. 43, 290–295.