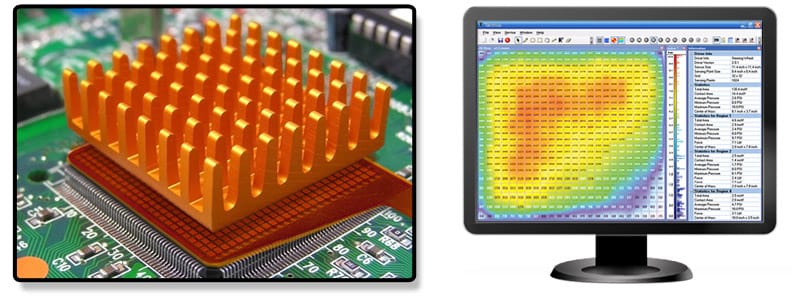
Tactilus® Heat sink sensor & electronic controller
The Tactilus® heat sink analysis system is designed to allow the engineer to measure actual contact forces and pressure distribution data between a heat sink and heat source. Unlike conventional transducers, Tactilus® is paper-thin with the intention of being non-intrusively placed between the two contacting surfaces. Now, for the first time, you can test, manipulate and reposition your heat sink interface in real-time without extensive computer simulation and prediction. Even a slight warping of the heat exchange structure or reduction in surface contact area can have profound implications for cooling efficiency. Tactilus® aids the engineer in validating and confirming what is predicated by FEA models.
Schedule a Live Product Web Demo
Download
Articles
- Mechanical Engineering
- Process Engineering Control & Maintenance
- Electronic Products
- ThomasNet News
- Design World
- Elektronik Industrie
- New Equipment Digest
- U.S. Tech
- Azosensors.com
- Desktopengineering.com
- DPAonthenet.net
- EETimes.com
- ElectronicDesign.com
- Electronic Specifier
- EngineeringTalk.com
- Sensor Tips
- ThermalNews.com
White Papers
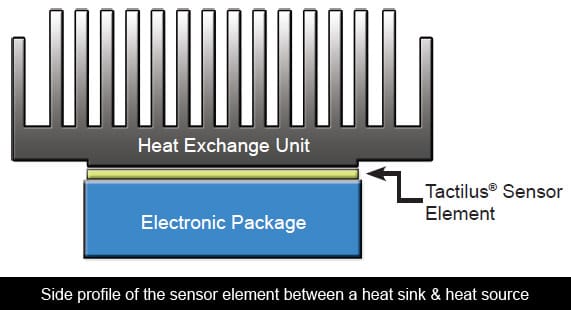
Tactilus® is a matrix-based tactile surface sensor. Essentially an “electronic skin” that records and interprets pressure distribution and magnitude between any two contacting or mating surfaces and assimilates that data collected into a powerful Windows® based tool kit. Each Tactilus® sensor is carefully assembled to exacting tolerances and individually calibrated and serialized. The architectural philosophy of Tactilus® is modular allowing for portability, easy expansion, and simultaneous data collection of up to 4 discrete sensor pads. Tactilus® employs sophisticated mathematical algorithms that intelligently separate signal from noise, and advanced electronic shielding techniques to maximize the sensor’s immunity to noise, temperature and humidity.
“Our primary proposition is to offer the client precisely what they require or need. To that end, everything we design with respect to the physical sensor element as well as our GUI and DLL’s can be completely tailored to your unique situation.” – Jeffrey G. Stark, CEO
Sensor Specifications | |
Technology | Resistive |
Pressure Range | 0 – 100 PSI (0 – 7 kg/cm²) |
Grid Size | 16 x 16 up to 32 x 32 |
Sensing Points | 256 up to 1,024 |
Total Sensing Area | Customizable to application |
Scan Speed | Up to 100 hertz |
Spatial Resolution | 62 mils (1.6 mm) or 125 mils (3.2mm) |
Thickness | 15 mils (0.7 mm) |
Accuracy | ± 10% |
Repeatability | ± 2% |
Hysteresis | ± 5% |
Non-linearity | ± 1.5% |